Three Decades of Building Organs in Lake City, Iowa
John A. Panning is tonal director of Dobson Pipe Organ Builders. A native of Wisconsin, he worked for two years with Hammes-Foxe Organs, Inc. in the Milwaukee area prior to joining Dobson in 1984. In these twenty years, he has been involved in every facet of pipe organ design, construction and maintenance. Mr. Panning has served two terms as Secretary of the American Institute of Organbuilders, and is currently a member of the AIO Journal committee. He was a member of the National Council of the Organ Historical Society from 1985–1991, and has served on two OHS convention committees. He has been North American Editor of Publications for the International Society of Organbuilders since 1991.
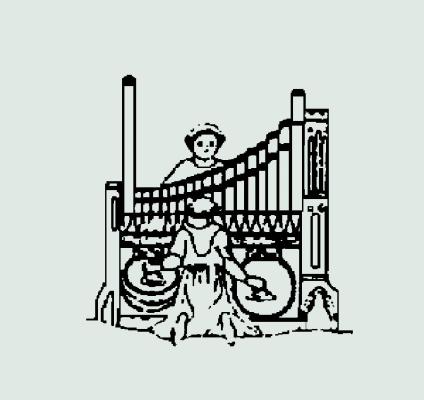
Thirty years ago this month, Lynn Dobson opened an organ building workshop in Lake City. Three decades later, clients from near and far have made the journey to this small western Iowa town.
Lynn A. Dobson, founder of the Dobson Pipe Organ Builders, was born in Carroll, Iowa, in 1949, and grew up on a farm in nearby Lanesboro. In 1966, he received a scholarship from the Hill Foundation to attend the Minneapolis School of Art summer session for gifted students. He graduated from Wayne State College in Wayne, Nebraska, in 1971 with majors in art and industrial education. During his college years, he built a twelve-stop mechanical-action organ in a shed on the family farm; this organ, Op. 1 (II/15), was eventually sold to Our Savior’s Lutheran Church in Sioux City, Iowa, where it still serves today. Upon graduation, Dobson taught high school art in Plattsmouth, Nebraska. However, the desire to be involved with organ building persisted, and in 1974 he left teaching to work for the Hendrickson Organ Company of St. Peter, Minnesota. In November 1974, he established his own firm, opening a small shop at 120 West Main Street in Lake City, Iowa.
What follows is a chronicle of the more important dates in the company’s history, a big-picture overview of three decades of art and craft as practiced by an increasingly prominent Midwestern American organ builder.
1975 ~ The young company’s first contract comes from one of Dobson’s former teachers, Antony Garlick, a music professor and composer at Wayne State College. The ten-stop residence organ incorporates both new and revoiced pipework. When Garlick moved in 1986, he sold the organ to Mary Brooks of Doylestown, Pennsylvania. In 1998, she in turn sold it to The Church of the Holy Spirit in Harleysville, Pennsylvania, and Dobson was once again called upon to move the organ, making several additions to suit its new, larger home. In his first year of business, Dobson is accepted as a member of the American Institute of Organbuilders (AIO).
1976 ~ Olivet Congregational Church, St. Paul, Minnesota, signs a contract for Op. 4 (II/33). The organ’s donor gave his gift to the church on the condition that it help launch the business of a promising young organ builder. At this time Lynn Dobson was assisted by his father Elmer Dobson, Jon Thieszen, who first began as summer help during college and would later become the company’s technical designer, and voicer Robert Sperling, a former co-worker at Hendrickson. The resulting instrument is a monumental achievement for so young a firm.
1979 ~ The company moves to its current location at 200 North Illinois Street, completely renovating the historic building and adding an erecting room with a 30¢ ceiling. In addition to instruments built for area churches, Dobson receives commissions from two Minnesota colleges as the decade closes. The first is a small studio organ for St. Olaf College (Op. 8, II/7; 1978). The second Minnesota institution, Bethany Lutheran College in Mankato, commissions an organ for its chapel (Op. 10, II/21; 1979), located in the school’s historic Old Main building. Op. 10 enjoys wide attention in organ journals. In 1996 it undergoes some tonal additions (increasing its size to 24 ranks) and receives a dramatic revision to its case to better suit its second home, Bethany’s new Trinity Chapel.
1980 ~ The decade opens with larger and more diverse projects, including one less than a block from the original Main Street shop: Lake City Union Church purchases a two-manual instrument (Op. 13, II/29; 1980). Dobson is engaged by Westminster Presbyterian Church of Des Moines, Iowa, to complete the organ (Op. 14, II/38; 1981) left unfinished by Lawrence Phelps Associates after that firm’s insolvency. Nearby Iowa State University in Ames, Iowa, contracts for a practice organ (Op. 16, II/3; 1981) and a teaching studio organ (Op. 21, II/18; 1982). The capabilities of the shop were enlarged during this period by several new employees, among them Tom Kult, a skilled cabinetmaker who later becomes shop foreman; David Storey, an organ builder who had previously worked for Jim McFarland in Pennsylvania; and Lake City native Sally Winter, secretary. Robert Sperling becomes full-time voicer. The firm is accepted for membership in the International Society of Organbuilders and is invited to join the Associated Pipe Organ Builders of America (APOBA); Lynn Dobson is elected to the AIO Board of Directors.
1983 ~ The completion of large two-manual organs for the Church of St. Michael in Stillwater, Minnesota (Op. 23, II/34; 1983) and First Presbyterian Church in Manhattan, Kansas (Op. 24, II/43; 1983) are harbingers of Dobson’s expansion into the rest of the country. Op. 24 is the largest organ built by the firm to date, and is the first organ in the United States to employ a “dual” stop action, one that can be operated mechanically by the organist as well as electrically through a solid-state combination action.
1984 ~ John Panning, an organ builder from Wisconsin, joins the crew this year; he is later appointed the firm’s tonal director. The shop is remodeled and enlarged at this time to accommodate the fabrication of mechanical key action parts and console chassis. In November, the firm celebrates its 10th anniversary with an open house and a recital by Guy Bovet on Op. 13 at Lake City Union Church; hundreds of clients and friends of the company attend.
1985 ~ Op. 28 (II/30; 1985), for The Church of the Holy Comforter in Burlington, North Carolina, is the first of many Dobson instruments to be located outside of the Midwest. From 1985 to 1990, the firm builds twenty new organs in Pennsylvania, New York, North Carolina and Virginia, in addition to five Midwestern states. Eight are for universities and colleges, of which five are institutions affiliated with church bodies: Bethel College, North Newton, Kansas (Op. 27, II/19; 1985), St. Olaf College, Northfield, Minnesota (Op. 29, II/30; 1985), Augsburg College, Minneapolis, Minnesota (Op. 42, III/44; 1988), Calvin College, Grand Rapids, Michigan (Op. 44, III/49; 1989), and Wartburg Theological Seminary, Dubuque, Iowa (Op. 46, II/15; 1989). Op. 42 and 44 are both for new college chapels designed in cooperation with Dobson. New shop personnel by the end of this decade include Meridith Sperling (pipe racking, general organ building), Lyndon Evans and Randy Hausman (cabinetmakers), Dean Heim (general organ building, and later shop foreman), Art Middleton (key action and consoles) and Bob Savage (leatherwork and electrical). Dobson hosts the annual spring meeting of APOBA, during which the firm is elected president.
1989 ~ The first AIO Midyear Seminar is held at the Dobson shop. Twenty organ builders from across the country participate in lectures on case design and construction, cost accounting, shop administration and equipment. By this time the firm is well known for its artistic and innovative organ case design.
1990 ~ Gradual evolution of the firm’s tonal style continues. Although specialized instruments such as the organ in Italian style for Indiana University (Op. 35, II/26; 1987) have been built, most are of eclectic design. Earlier instruments explored the neo-classic aesthetic; new projects blend both classical and romantic influences. Op. 44 (1989) at Calvin College includes a 16¢ Open Wood in the Pedal, two enclosed divisions and a rich, smooth tonal palette. Joining the firm this year are Kirk Russell (business manager) and Dean Zenor, an organ builder from Connecticut.
1992 ~ Two instruments built this year demonstrate the firm’s range. Op. 55 (II/32) for St. John Lutheran Church in Storm Lake, Iowa, features Kirnberger III tuning, dual wind systems (a wedge bellows for flexible wind, a parallel-rise bellows and wind stabilizers for steady wind) and a freestanding case with attached console at the rear of the church. The chancel location and Anglican church music emphasis of St. Luke’s Episcopal Church, Kalamazoo, Michigan, result in Op. 57’s (II/42) more romantic tonal design. Op. 56 (II/17), for Trinity Lutheran Church, Manhattan Beach, California, is the first Dobson installation on the West Coast. The firm is incorporated as Dobson Pipe Organ Builders, Ltd., a new 4,500 sq. ft. wood shop is built, and a pipe shop is set up. The company becomes a prize sponsor for the National Improvisation Competition of the American Guild of Organists.
1993 ~ Op. 60 (III/49) for First United Methodist Church, Mesa, Arizona, the firm’s seventh three-manual instrument, features a Solo as the third manual rather than a more customary Positive or Choir. Voiced on 6≤ wind pressure with mechanical action, this division includes an 8¢ Harmonic Flute, 4¢ Flute Octaviante, Cornet V, and 8¢ Bombarde, all under expression except for the Cornet, which is mounted outside the Solo enclosure.
1995 ~ The mid-’90s see an even wider variety of projects, ranging from Op. 62 (II/11; 1994), a residence organ for Rich Wanner in Berkeley, California, to the 1996 renovation of the important four-manual 1959 Schlicker organ at Valparaiso University, Valparaiso, Indiana, and its enlargement to 102 ranks. Other notable organs delivered are Op. 65 (II/36; 1995) for the University of South Carolina, Columbia, South Carolina, Op. 67 (II/32; 1996) for Wartburg College, Waverly, Iowa, and Op. 69 (II/31; 1997) for Pakachoag Church, Auburn, Massachusetts. Voicer and pipemaker William Ayers joins the firm during these years.
1998 ~ The organ for St. Paul’s Episcopal Church in Minneapolis, Minnesota, (Op. 70, II/45) unabashedly combines classical and romantic tonal elements in a fresh and original way. This same line is followed in the large three-manual instrument for West Market Street Methodist Church in Greensboro, North Carolina (Op. 71, III/58; 1999), voiced in collaboration with Los Angeles organ builder Manuel Rosales. A somewhat more classical course is taken with the instrument at St. Joseph Abbey in St. Benedict, Louisiana (Op. 73, III/38; 2000), which is greatly enhanced by the Abbey church’s five seconds of reverberation. Joining the firm by the end of the decade are Scott Hicks (general organ building), Gerrid Otto (windchests, general organ building), John Ourensma (voicing, pipemaking) and Randall Pepe (wood pipemaking and general organ building).
2000 ~ The firm’s work at the beginning of a new century includes the monumental instrument for the Cathedral of Our Lady of the Angels in Los Angeles, California (Op. 75, IV/105; 2003) and the company’s first contract for a major concert hall, Verizon Hall in Philadelphia’s Kimmel Center for the Performing Arts (Op. 76, IV/125; 2006), the new home of the Philadelphia Orchestra. These high-profile projects bring Dobson into collegial working relationships with world-famous architects: José Rafael Moneo for the cathedral project and Rafael Viñoly for the concert hall.
2003 ~ Not to be lost among the contracts for immense organs are instruments of more normal size delivered to churches and universities in Delaware, Illinois, and Minnesota. Op. 78 (III/42) for St. John’s Methodist Church in Augusta is Dobson’s first instrument in Georgia, housed in an elegant cherrywood case with carved pipeshades. Joining the firm during the first years of the century are Antal Kozma (technical design) and Donny Hobbs (general organ building, voicing, pipemaking).
2004 ~ Op. 80 (II/26), for St. Paul’s Church, Rock Creek Parish, Washington, D.C., was set up and played in Lake City during a 30th anniversary open house. To further celebrate, a festive reception for friends of the company was held during the Los Angeles AGO convention following Martin Jean’s recital on Op. 75 at the Cathedral of Our Lady of the Angels. The second phase of the installation of Op. 76 (IV/125) in Verizon Hall takes place during the summer, while Op. 79 (II/23), for Shepherd of the Bay Lutheran Church, Ellison Bay, Wisconsin, is installed in the fall. Ongoing design work includes a significant concert hall instrument for the new Atlanta Symphony Center, designed by famed architect Santiago Calatrava of Zürich. Instruments for the Chapel of the Cross in Chapel Hill, North Carolina, and the Lutheran Church of the Good Shepherd in Lancaster, Pennsylvania, give the shop a small respite between these large projects.
Since 1994, the daily operation of the shop has been under the direction of a management team consisting of Lynn Dobson (president and artistic director), John Panning (tonal director), Jon Thieszen (technical designer), Dean Heim (shop foreman), Dean Zenor (project manager) and Kirk Russell (business manager).
News, specifications of every organ, and many photographs can be found on Dobson’s website at
Dobson Pipe Organ Builders, Ltd.
William Ayers, 1994, voicer, pipemaker
Mitch Clark, 2004, technical designer
Lynn A. Dobson, 1974, president and artistic director
Lyndon Evans, 1988, cabinetmaker
Randy Hausman, 1988, cabinetmaker
Dean Heim, 1988, shop foreman, general organbuilding
Scott Hicks, 1997, general organbuilding
Donny Hobbs, 2003, general organbuilding, voicing
Antal Kozma, 2001, technical designer
Arthur Middleton, 1987, machinist, key action, wood pipes
Gerrid D. Otto, 1998, windchests, general organbuilding
John Ourensma, 1999, voicer, pipemaker
John A. Panning, 1984, tonal director, voicer
Kirk P. Russell, 1990, business manager
Robert Savage, 1989, leatherwork, electrical, general organbuilding
Meridith Sperling, 1985, windchests, general organbuilding
Jon H. Thieszen, 1975, technical designer
Sally J. Winter, 1983, accounting and secretarial
Dean C. Zenor, 1990, key action, administrative