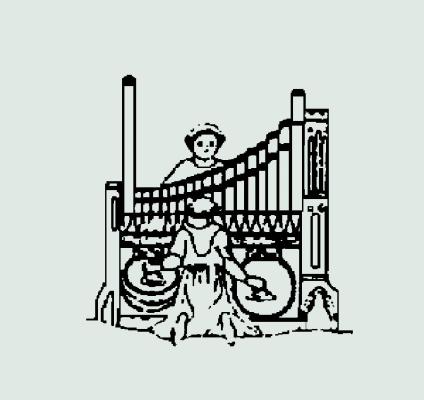
Grant Smalley Pipe Organs, Victoria, British Columbia (1984)
Born in Sidney, near Victoria B.C., Grant Smalley has worked as an organbuilder since 1966. He was associated with Gabriel Kney from 1968 to 1979, primarily building tracker-action organs and installing them throughout Canada and the U.S.A. During the last eight of those years he assumed Kney's tuning and maintenance business in addition to his organbuilding duties. He returned to Victoria in 1980 and established his own business four years later, buying out the organ maintenance service of Hugo Spilker, who had done restorations in the area. His associate, Douglas Adams, received formal training in instrumentation and systems technology, and manufacturing engineering technology; in addition to assisting in the construction of the new shop, he is responsible for electrical design, construction, and mechanical work. Beverly Smalley, the wife of Grant Smalley, handles the business and financial operations. All three are active participants in community choral groups.
Grant Smalley has built several small organs: a four-stop positiv organ, mechanical action (1985); a four-stop, portable, continuo organ with 56-note transposing keyboard, mechanical action (1989); and two continuo organs of 31/2 and 41/2 ranks, both with mechanical action (1995, 1997). The major activity, however, is organ restoration, along with regular tuning and routine maintenance work: about 50 organs throughout Vancouver Island and Greater Vancouver. A number of heritage organs in Victoria, including several instruments built by Casavant Frères in the early 1900s, and others by English and American makers, have received extensive overhauls in recent years.
Wooden pipes, most windchests, consoles, and casework are built in the shop; metal pipes are ordered to specifications and voiced there. Other components acquired from suppliers include keyboards, drawknobs, switching systems, and blowers.
Blair Batty & Associates, Simcoe, Ontario (1985)
Blair Batty was born in Simcoe, and as a teenage organ player he acquired an interest in the mechanical workings of organs. His organbuilding career began with the Keates Organ Company, Acton, Ontario, where he learned windchest construction, wiring, tuning, and installation procedures. In 1976 he moved to Europe, where he learned the craft of metal pipemaking with Jacques Stin-
kens, Zeist, Holland, and the art of reed manufacturing with Carl Giesecke & Sohn, Göttingen, West Germany. During that period he travelled extensively throughout Europe to study examples of French, German, and Dutch organbuilding. In 1977 he went to Gloucester, Massachusetts, to join C. B. Fisk as a pipemaker and draftsman, then in 1979 he was invited to head the pipe shop of the Noack Organ Company, Georgetown, Massachusetts. In 1981 he returned to Canada to work for Brunzema Organs, Fergus, Ontario, then returned to Simcoe in 1985 to establish his own firm. Since then he has visited England on several occasions to study the instruments of Willis and Hill.
The company has built three new organs. One is a two-manual, 27-stop instrument of eclectic design incorporating Schnitger-inspired choruses, a French-character trumpet, and Dutch/French-style Swell mutations, with console-equipped MIDI (1991). Another is a two-manual, 19-stop instrument of British-inspired design in which the basic choruses follow William Hill, but includes a Schnitger-style trumpet, a cornet and mutations of classical French design, and string stops scaled and voiced on Cavaillé-Coll principles (1993). A four-rank box organ was built for a private customer.
The company specializes in restoring and rebuilding older organs, employing the techniques and materials of the original builder as far as possible, and provides tuning and maintenance service to about 100 churches annually throughout southwestern Ontario. Most of the components of organs are produced in the factory: Pitman and slider windchests, bellows, rollerboards, tremulants, keyboards and pedalboards, and consoles. Pipes, both wooden and metal (including reeds), are generally made on the premises; the metal pipeshop and foundry section has a 12-foot, polished granite casting table, one of the few in Canada. Blowers and electrical combination and switching actions are acquired from external suppliers. The firm also provides services, parts, and pipes to other builders and tuners. A large reference library of historical and current organ design data, including pipe scalings of hundreds of historic organs, is maintained. A computer-assisted design (CAD) system is used. The firm had three full-time employees and several part-time helpers in 1998.
Gober Organs, Toronto, Ontario (1985)
Halbert Gober was born in Austin, Texas, and began his organbuilding career with Otto Hofmann (1969-1972), an organbuilder in Austin known as an early proponent of the tracker revival. Following university studies in liberal arts and architecture, he lived in Germany from 1972 to 1980. During the first four years he studied music, architecture, and organbuilding; in the remaining years he was employed with various organbuilders, including Rensch in Lauffen-am-Neckar (1972); Jann (1977-1980), where he completed his formal apprenticeship in 1979; and Felsberg in Chur, Switzerland. Following his move to Canada in 1981 he was employed as a voicer with Karl Wilhelm until 1985, before opening his own shop in the Montréal area in that year. From there he served as a freelance voicer and pipemaker for several organbuilders in North America and Europe.
He established his own shop in Toronto in 1991, where he commenced building tracker-action organs. Output to date amounts to six two-manual instruments of medium or small size; the most recent of these is a five-stop studio organ for the University of Notre Dame, South Bend, Indiana. Rebuilds and tonal revision projects are also undertaken. His philosophy is to draw on the full heritage of historical organbuilding in the construction of cohesive and logical instruments, with equal priority to dependability and musicality.
Wooden pipes, along with metal pipes made of cast and hammered lead, are manufactured on the premises. Reed pipes, including shallots, are also made in the shop. Action parts are from Germany. There were three employees in 1998.
Pole & Kingham, Chatham, Ontario (1985)
Donald Pole and Ron Kingham founded their company in 1979 and then incorporated in 1985, when the construction of complete new organs commenced. Earlier, between 1966 and 1968, Ron Kingham had been an employee of John Bright, a co-founder with Gabriel Kney of the Kney & Bright Organ Company in 1955; he built a house organ under John Bright's supervision. In the first five years of their association, the partners' work was limited to tuning, repairs, cleaning, and general maintenance.
Since 1985 they have built and installed seven new electrical-action instruments (two incorporating some older parts), mostly of medium-size, all in Ontario churches; two other instruments were provided to churches in Michigan, U.S.A. While their instruments are designed to meet both liturgical and performance needs, recent organs have a Romantic bias, and the Symphonic era is recalled in a new, three-manual, 36-stop instrument (the largest to date), with its six-rank String Organ division, installed in Holy Trinity Anglican Church, in Chatham, Ontario, in 1997. Other services include restoration of both tracker- and pneumatic-action organs, rebuilding with solid-state switching, enlargement, and tonal additions, along with general maintenance and tuning.
Wooden pipes (Bourdon, Chimney Flute, Gedeckt, and Doppelflute--the latter scaled after a fine Karn stop), windchests and reservoirs, and consoles are made in the shop; metal pipes are obtained from suppliers in Canada, U.S.A., Germany, and Holland. Five employees worked with the partners in 1998.
Juget-Sinclair, Montréal, Québec (1994)
Denis Juget, a native of the Savoy region of France, received his diploma in fine cabinetmaking in Annency, Haute-Savoy, France, in 1979, then worked as an apprentice with leading organbuilders on both sides of the Atlantic, with whom he acquired skills in all phases of organbuilding: Lucien Simon, Lyon, France (1979-1983); Robert Chauvin, Dax, France (1983-
1985); Wolff & Associés, Laval, Québec, upon his arrival in Canada (1985-1991); Orgelbau Goll, Lucerne, Switzerland (1990-1991); Orgelbau Rohlf, Seitzental, Germany (1992-1994); and Karl Wilhelm, Mont Saint-Hilaire, Québec (1992-1994). Special assignments be-tween 1988 and 1990 involved the restoration, renovation, and voicing of several organs in Austria, Italy, and Spain. His organbuilding enterprise began in 1994 in Saint-Basile-le-Grand, Québec, in a backyard, two-story, former chicken coop, which was converted into a workshop. In the following year he completed a two-manual, 3-stop house organ for a private client.
Following studies in science at McGill University in Montréal, Stephen Sinclair worked first as an apprentice cabinetmaker, then as an apprentice organbuilder with Wolff & Associés (1989-1991). He received practical working experience in general organbuilding and reed-stop restoration with Manufacture d'orgues Franc-comptoise, Courtefontaine, France (1995, 1997); pipemaking with Georges Blaison, France (1996) and N. P. Mander, London, England (1997); and general organbuilding, design, voicing, maintenance, and tuning with Wolff & Associés (1992-1998). He joined Denis Juget as an equal associate in 1998.
The company divides its time between the restoration of historic instruments and the construction of small mechanical-action organs. Since 1995 five two-manual, 3-stop, house organs and one continuo organ have been manufactured; three of the house organs for clients in the United States. Works in progress include two similar house organs for destinations in Québec and Germany, and a two-manual, 10-stop practice organ for the University of Cincinnati, ready in 1999. The house organs incorporate a design by Denis Juget that enables them to be moved relatively easily without breaking down the action.
All parts are made in-house, including wooden and metal pipes, wind chests, bellows, rollerboards, keyboards and pedalboards, drawknobs, and casework (hand-planed in solid wood, using mortise-and-tenon construction). Blowers are purchased from Laukhuff, Germany. Several part-time workers assist in various stages of production and installation. Following relocation in late 1998 to an industrial space with 30-foot cathedral ceilings in Montréal, the associates intend to make the leap from building practice instruments to full-fledged church organs in the near future.
D. Leslie Smith, Fergus, Ontario (1996)
Leslie Smith grew up in southern Alberta, and acquired his interest in music at an early age through involvement in church choirs and piano lessons. He developed an early fascination with organ building and enrolled in organ performance studies at the University of Calgary after completing high school. Using practical skills acquired from his father, who was a carpenter and mechanic, he completed several kits for harpsichords and clavichords, and established an association with a local organ serviceman who introduced him to the techniques of maintaining and tuning electro-pneumatic instruments. In 1973 he moved to London, Ontario, to continue his organ studies at the University of Western Ontario. While in that city, he became acquainted with Gabriel Kney, in whose organbuilding shop he worked on a part-time basis for several years. In 1982 he joined Brunzema Organs in Fergus, Ontario, where he remained for 10 years as a journeyman organbuilder. After the death of Gerhard Brunzema in 1992 and the closing of his organbuilding operation, Leslie Smith worked as an independent contractor in pipemaking and voicing on a number of projects in Canada and the United States. His first organ, a two-manual, 11-stop studio organ was undertaken in 1982 as a part-time project while working with Gerhard Brunzema; it was completed in 1992.
In 1996 he established his new workshop on part of the former Brunzema premises. In the same year he produced his first commission, a one-manual, 6-stop, mechanical-action organ, for a cemetery chapel in Montréal. A similar organ, but without pedals, was supplied to a church in Kansas City, Missouri. Although eclectic and innovative in terms of tonal and visual design, Leslie Smith's approach is inspired by the work of mid-19th-century Canadian and American firms such as S. R. Warren of Montréal and Hook & Hastings of Boston, favoring generous scaling and higher pressures.
Wooden pipes for these two instruments were made in-house, but metal pipes were supplied by F. J. Rogers, Leeds, England. Blowers came from Laukhuff, Germany. Keyboards, and key and stop action were fabricated in the shop. Stops are divided into bass and treble, using a special form of drawstop mechanism developed by the builder. Cases are made from common hardwoods, using traditional construction techniques.
Maintenance work to organs of all makes and construction in Ontario and Québec comprises a significant part of his activity; in 1996 he was appointed curator of the largest pipe organ in Montréal, a four-manual, 86-stop Casavant instrument (installed in 1932, rebuilt in 1992 by another firm) at the Church of St. Andrew and St. Paul, and will soon undertake complete rebuilding projects, as well.
The Future of Organbuilding
The status of organbuilding in the 21st century is not easy to predict, given the variety of factors involved. Generalizations about the number of future organ installations are risky; nevertheless, it is interesting to note that, within roughly the last three decades, while the annual production of instruments of all sizes peaked several times in the 1980s, the low periods of the 1970s were again matched in the years since 1994. Whether this recession will continue in the coming years is uncertain, but some recent trends provide clues to a possible future.13
The fact that few new organs have been installed in Canadian locations in recent years is not surprising, for the distinguishing characteristics of the "golden age" of the organ in the early years of the twentieth century--in terms of the erection of new church buildings, the proliferation of organbuilding firms that supplied both churches and motion picture theaters with instruments, and public enthusiasm for organ recitals played by local and touring recitalists--are not likely to be repeated, considering shifting cultural values along with the various musical and other forms of entertainment now available.
Although most organbuilders have confined their operations to meeting only local and regional needs, several Canadian firms have cultivated the international market with apparent success. The services of the Canadian Commercial Corporation, a crown corporation of the Government of Canada that assumes the role of prime contractor and subcontracts all of the contract back to the Canadian firm, are available for companies seeking worldwide clients.
As for the tonal design of new instruments, the uneasy hybrid designs of earlier years largely have been abandoned in preference to the rediscovered qualities of universally admired older instruments of the 17th and 18th centuries, without blindly copying them. Although instruments of neoclassical design, with their historically "authentic" stoplists, are not entirely suitable for the performance of all schools of organ music, they are probably more versatile than the earlier generation of organs for general liturgical and performance purposes. On the other hand, some organbuilders prefer an eclectic approach, a matter that is subject to ongoing debate.14 The recent strong demand for mechanical-action instruments may eventually stabilize, for reasons relating to architecture, economics, changing musical tastes, and a return to the Romantic idiom in repertoire. Purchasers may prefer some of the advantages of nonmechanical instruments, such as the consistent keyboard touch and flexible console location provided by electric action.15
Much of the earlier activity of new organ construction has been redirected to rebuilding and restoring older instruments, some of historical significance. Most Canadian organbuilders engage in this growing activity, which can provide churches with a cost-effective alternative to the purchase of a comparable new instrument. Routine maintenance work is also part of the service provided by many firms, large and small.
Pipe organs have always been expensive, so electronic instruments utilizing highly developed digital technology now provide an economic alternative for church congregations lacking the will or the means to acquire and maintain a pipe organ. The respective merits of pipe organs and electronic instruments have been debated since the latter were first introduced. Nevertheless, there is an obvious answer, based on musical criteria, to the question, Which is preferable: a poorly designed, badly maintained pipe organ, or a high quality electronic instrument? Electronic instruments have a place in locations where pipe organs are out of the question, whether for space or budgetary considerations. They have proved adequate for the liturgical requirements of many small or medium-size churches with limited budgets, and these instruments have provided competition for more costly pipe organs. The increasing acceptance of electronic instruments further diminishes the probability of a significant number of new pipe organ installations in the coming years. On the other hand, educational institutions (those that are not financially beleaguered, if any) and affluent congregations of some churches (not necessarily the largest) undoubtedly will continue to prefer pipe organs for musical, historical, or social reasons, and such instruments can be supplied only by the larger, well-established, organbuilding companies.
The role of the organist is of considerable importance in ensuring a future for organbuilding. If a church considering the purchase of a new organ already has a fully trained organist, this person, working with a musically educated and supportive committee, can influence the decision in favor of a pipe organ in preference to an electronic instrument, providing that a realistic fund-raising objective can be achieved. A church with an adequate pipe organ will seek a highly trained individual to play it, and such organists ordinarily prefer appointments to churches with pipe organs; once hired, their presence encourages the continuation of the pipe organ tradition.
Changes in the liturgical practices of some religious denominations may have a subtle, long-term effect on the future of organbuilding. The emergence in some congregations of youth-segregated services, with their unique liturgical practices that employ guitars or other instruments associated with folk music or religious rock groups, may produce a generation of worshippers unfamiliar with the organ, its musical heritage, and its literature. A broader associated issue is the question of the future of institutionalized religion and its possible decline due to the growth of science, education, and secularization, or its theological transformation into various manifestations of individualistic spiritual development. These possibilities undoubtedly will take many years, perhaps centuries, to resolve.
Shifts in population characteristics introduce another factor into the question of the future of organbuilding. Some suburban churches located in stable neighborhoods now have congregations comprised largely of aging members living on limited incomes, not offset by significant numbers of younger, fully employed members. If the present job of organ maintenance is difficult for such congregations, even with skilled volunteer labor working under the supervision of a trained organ technician, the acquisition of a new instrument is beyond consideration; in fact, the amalgamation or dispersal of these congregations is the more likely scenario. The inevitable result would be the closing of some church buildings, along with the possible removal or relocation of existing pipe organs. The more affluent churches with a wider spread of ages among their members, and which encourage the full participation of younger members in their musical programs, are the only ones that will escape this fate, thus leaving open the possibility of the purchase of a new organ in the distant future. A related consideration, which provides a cause for optimism, is grounded in the speculation that recent declines in per capita real income may stimulate group activities at the expense of individual life styles, and that churches may again become a center of social as well as spiritual activities. In such contexts the pipe organ, as a cultural, religious, and artistic centerpiece, may serve as a source of pride and inspiration, and as a vehicle for the renewal of congregations.16
Over the longer term, increased public awareness, combined with both formal and informal educational opportunities, may contribute to the sustained vitality of the organ culture generally, including organbuilding. Radio broadcasts of organ recordings, instructive television programs, increased concert programming for organ and other instruments, and the development of audiences for subscription series of organ recitals, would increase knowledge of the organ among the general public. In the educational system, in-service sessions on the organ for school music teachers, the preparation of classroom learning materials for use in regular music instruction courses, and the participation of students in on-site inspection trips and demonstrations would provide practical contexts for raising awareness of the organ at a level that students can understand and enjoy.17 As for organists, competitions or commissions for hymn arrangements, sacred songs, or new compositions for the organ could be fostered on both the regional and national levels by the Royal Canadian College of Organists. These informational and educational programs would contribute to the development and maintenance of an appreciative audience for the organ throughout the coming decades. Such forms of revitalization would ensure the future of the King of Instruments well into the 21st century.
REFERENCES
13. Some of the following material is adapted from the chapter, "The Future of the Organ," in Hartman, The Organ in Manitoba (note 5 above).
14. See Quentin Regestein and Lois Regestein, "The 'Right' Organ," The Diapason, August 1998, 13-16; September 1998, 17-18. Radically opposing points of view debate the legitimacy of a "universal" hybrid organ, one that is perfect for everything.
15. R. E. Colberd, "Pipe Organ Building: the Nineties and Beyond," The Diapason, July 1994, 12.
16. Ibid., 14.
17. For a description of a recent educational event for school children, see Valerie L. Hall, "Meet the King of Instruments: A Successful Workshop Model for Kids," Organ Canada, July 1998, 9.