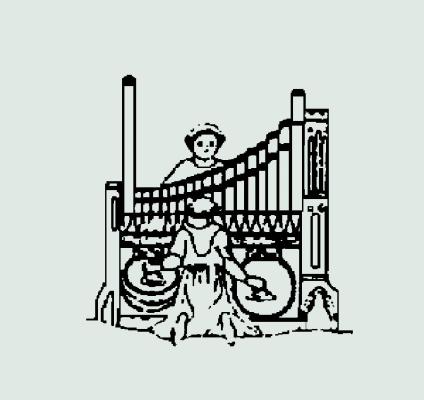
Organbuilding in the United States and Canada is a thriving art practiced in hundreds of shops throughout the continent. Emerging from decades of stylistic extremes, organbuilders are combining a wealth of knowledge from the past with new technologies to meet contemporary design challenges. North American builders, compelled by a unique spirit of cooperation and openness, are successfully raising the artistic standards of this time-honored craft. (American Institute of Organbuilders, descriptive statement.)
The organ has occupied a prominent place in the musical culture of Canada since the days of the first European settlement, chiefly because of its close connection with church music and the ambitions of many congregations. The first organs, brought from France, were installed in Québec City around 1660. An anecdotal report mentions the acquisition by a Halifax church of a Spanish instrument that had been seized on board a ship in 1765.1 Following a period in which organs continued to be imported from England and France, organbuilding began as early as 1723 and flourished mainly in Québec and Ontario from the mid-19th century onward.2 By the second half of the 19th century, organ building had become a relatively important industry in Eastern Canada, where companies had acquired sufficient expertise to compete in the international market, including the United States.3
The development of organbuilding in Canada proceeded through several phases, beginning with early builders.4 The first known organbuilder was Richard Coates, who arrived in Canada from England in 1817; he supplied mainly barrel organs to several small churches in Ontario. Joseph Casavant, the first Canadian-born builder, installed his first instrument in the Montréal region in 1840; he transmitted his skills to his sons, who later established the company that achieved world-wide recognition. The arrival from the United States of Samuel Russell Warren in 1836 marked the introduction of professional-calibre organbuilding into the country. His family firm had produced about 350 pipe organs by 1869; it was sold in 1896 to D. W. Karn (see below). Other prominent organ builders included Napoléon Déry (active 1874-1889), Eusèbe Brodeur (a successor to Joseph Casavant in 1866), and Louis Mitchell (active 1861-1893) in Québec, and Edward Lye (active 1864-1919) in Ontario.
The years 1880-1950 were marked by unprecedented growth in organbuilding, beginning with the establishment of Casavant Frères in 1879 in Saint-Hyacinthe, Québec. The Canadian Pipe Organ Company/Compagnie d'orgues canadiennes was established in 1910 by some former Casavant staff, also in Saint-Hyacinthe (when the firm closed in 1931 its equipment was acquired by Casavant). Prominent Ontario builders included the firms of Richard S. Williams (founded 1854 in Toronto), Denis W. Karn (commenced 1897 in Woodstock), C. Franklin Legge (founded 1915 in Toronto, joined by William F. Legge 1919, who later established his own company in Woodstock around 1948), and the Woodstock Pipe Organ Builders (an organization of skilled craftsmen in that Ontario town, 1922-1948). Several smaller, independent builders were active for a time in Ontario, the Maritime provinces, and Manitoba (late 1880s). British Columbia, on the other hand, seems to have had no indigenous organbuilders, for instruments were imported from the United States or from England on ships that sailed around Cape Horn; one of the earliest arrived in Victoria from England by this route in 1861.
In the early 1950s some organbuilders, encouraged by younger organists who had played European instruments, as well as the increasing availability of sound recordings of these organs, turned to classical principles of organbuilding to counter what they perceived as the colorless sound palettes of Canadian organs of the 1930s. The return to earlier tonal aesthetics, inspired by the so-called 17th-century "Baroque organ," found expression in the construction of bright-toned, tracker-action instruments. The "new orthodoxy" was enthusiastically assimilated by Casavant Frères and by a number of independent builders in the same region, some of whom had received their training in Europe. Karl Wilhelm, Hellmuth Wolff, André Guilbault and Guy Thérien, Fernand Létourneau, Gabriel Kney, and Gerhard Brunzema were prominent in this movement, and many of them are still in business. Their accomplishments, along with the activities of other known organbuilders of the 1990s, will be described in chronological order, according to their founding dates, in the remainder of this article.5
Casavant Frères, Saint-Hyacinthe, Québec (1879)
Casavant is the oldest continuing name in organbuilding in North America. Joseph Casavant (1807-1874), the father of the founders of the company, began his organbuilding career while still a Latin student at a Québec religious college, where he completed an unfinished organ from France with the help of a classic treatise on organbuilding. By the time he retired in 1866, after 26 years in business in Saint-Hyacinthe, Québec, he had installed organs in 17 churches in Québec and Ontario, but none of them survive. His sons, Joseph-Claver Casavant (1855-1933) and Samuel-Marie Casavant (1850-1929), worked for Eusèbe Brodeur, their father's successor, for a few years. They opened their own factory in Saint-Hyacinthe, Québec, in 1879, following an extended tour of western Europe inspecting organs and visiting workshops; Claver had apprenticed briefly with a Versailles builder before the tour. In the early years the Casavant brothers were conservative in their tonal design, emulating the ensemble sound of the kind they had heard in old-world instruments that they had examined during their European tour. But from the outset the brothers were innovators, beginning with improvements in the electric operation of their organs in the 1890s. As their reputation spread beyond the cities and towns of their province, production increased steadily.
The company experienced difficult times in the 1930s due to economic conditions, much standardization, and repetitive tonal design. Production was curtailed during the years of World War II due to a shortage of materials, and the company manufactured many unit organs during this period. Later, new initiatives were undertaken by several imaginative artistic directors who served with the firm between 1958 and 1965: Lawrence Phelps from Aeolian-Skinner in the U.S.A.; and European-trained Gerhard Brunzema, Karl Wilhelm, and Hellmuth Wolff.
Most present-day Casavant organs exhibit a conventional design that retains both symphonic and modern elements in subtle synthesis. Casavant organs are recognized for their special tonal qualities and the way the individual stops are blended together into a chorus at all dynamic levels. Time-tested actions include tracker, electrically operated slider windchests, and electro-pneumatic (since 1892; tubular-pneumatic was last used in the mid-1940s). The company workshop has eight departments: metalworking, woodworking, mechanism, consoles, painting, racking, voicing, and assembly. Virtually all components are made in the workshop, including all flue and reed pipes (to 32-foot-length), reed shallots, windchests, consoles, keyboards and pedalboards, and casework, although specialized wood carving and gilding are done by outside artisans. A few electrical components, such as blowers, power-supply units, electromagnets, solid-state combination and coupling systems, and hardware, are purchased from world-wide suppliers. All visual designs are coordinated with their intended surroundings; there are no stock designs. Organs are completely assembled for rigorous testing and playing in preparation for on-time delivery.
The company resumed the construction of tracker-action instruments in 1961 after a lapse of about 55 years, producing 216 such organs since that date. By the end of 1998 the total output amounted to 3,775 organs of all sizes, and many of these have received enthusiastic testimonials from renowned recitalists over the years. Although sales were limited mainly to North America until World War II, Casavant organs now have been installed in churches, concert halls, and teaching institutions on five continents. The firm's largest instrument is a five-manual, 129-stop organ with two consoles installed in Broadway Baptist Church, Fort Worth, Texas, in 1996. The great majority of the very large instruments have been installed in locations in the United States; the exception is the four-manual, 75-stop organ in Jack Singer Concert Hall, Calgary Centre for the Performing Arts, in 1987. The company also engages in renovation projects and additions to existing organs.
The key personnel include Pierre Dionne, President and Chief Operating Officer (from 1978), formerly Dean of Administration at the Business School of the University of Montréal; Stanley Scheer, Vice-President (1984), formerly Professor of Music and Head of the Department of Fine Arts at Pfeiffer University, Misenheimer, North Carolina, holds a Master of Music degree in organ performance from Westminster Choir College, Princeton, New Jersey; Jean-Louis Coignet, Tonal Director (1981), a professionally trained physiologist with a doctorate from the Sorbonne, contributor to music journals, the most knowledgeable authority on the work of Cavaillé-Coll today, was formerly organ expert for the City of Paris; Jacquelin Rochette, Associate Tonal Director (1984), formerly Music Director of Chalmers-Wesley United Church, Québec City, holds a Master's degree in organ performance from Laval University, performs regularly on CBC radio, and has recorded works by several French composers for organ; Denis Blain, Technical Director (1986), with many years of practical experience in virtually all aspects of organbuilding, is in charge of research and development; Pierre Drouin, Chief Engineer, holds a Bachelor of Architecture degree from Laval University, introduced computer-assisted drafting, and supervises the design and layout of each organ. In 1998 the company had 85 full-time employees, many with more than 30 years of service with the company. All levels of management and production personnel function as a team.
Keates-Geissler Pipe Organs, Guelph, Ontario (1945)
The company was established in 1945 in London, Ontario, by Bert Keates (he came from England in his infancy) and relocated to Lucan, Ontario, in 1950. When it was incorporated in 1951 the assets of the Woodstock Pipe Organ Builders (formerly Karn-Warren) were purchased. The company moved to Acton, Ontario, in 1961, a more central location in the province. In 1969 the growing firm took over the business of the J. C. Hallman Company, a manufacturer of electronic instruments and pipe organs, when it discontinued making pipe organs (but not parts for them). For several years some organs were manufactured under the name of Keates-Hallman Pipe Organs.6 The company moved to Guelph, Ontario, in 1994.
Dieter Geissler was born in Dittelsdorf, Saxony, Germany, where he began his trade as a cabinetmaker. At the age of 14 he commenced his apprenticeship with Schuster & Sohn, Zitau, where he remained from 1946 to 1950. In 1951 he moved to Lübeck, West Germany, where he worked as a voicer with E. Kemper & Sohn for five years. In 1956 he moved to Canada to join Keates's staff. When Keates retired at the end of 1971 Dieter Geissler became president of the firm, which he purchased in 1972, and adopted the present company name in 1982. His son, Jens Geissler, joined the company in 1978.
Keates-Geissler organs are offered in all types of action and are custom built to any required size. Altogether, 147 new organs7 have been installed at locations in Canada, the United States (about 15), and Barbados, West Indies. The output includes a number of four- and five-manual instruments; the largest is a five-manual, 231-stop organ, installed in the First Baptist Church, Jackson, Mississippi, in 1992 (a compilation of its original 1939 E. M. Skinner instrument, a 1929 five-manual Casavant organ removed by Keates-Geissler in 1986 from the Royal York Hotel, Toronto, and some additional structures by the company). The firm has undertaken a substantial number of renovation, rebuilding, and reinstallation projects over the years, about 1,500 altogether, about 75 of these in the United States.
All wooden pipes are made in the factory, but metal pipes are made by Giesecke or Laukhuff in Germany to the company's scaling specifications; preliminary voicing is done in the factory before final voicing on-site. The windchests of electro-pneumatic instruments feature Pitman-chest action that includes some unique features to overcome the effects of extremes in temperature and humidity; the company is the only such manufacturer in Ontario and one of a few in Canada. Expandable electronic switching systems are designed and made in the factory from readily available components to facilitate replacement. Solid-state switching and multiple-memory combination actions are also manufactured. Console shells are handcrafted from solid wood in the factory; tracker touch is an available option. Keyboards are custom made to the company's specifications by Laukhuff, Germany, and blowers are acquired mainly from the same company. The company had four full-time employees in 1998; other part-time workers are hired as needed.
Guilbault-Thérien, Saint-Hyacinthe, Québec (1946)
This company originated with the Providence Organ Company, established in Saint-Hyacinthe in 1946. The partners, André Guilbault, whose father Maurice Guilbault had worked for Casavant, and Guy Thérien, a voicer from Casavant, joined forces in 1968 when the elder Guilbault retired. The present company name was adopted in 1979. When André Guilbault retired in 1992, Alain Guilbault (no relation) acquired an interest in the company.
At the outset the company manufactured electro-pneumatic instruments, but built its first mechanical-action instrument (Opus #1 in a new series), a two-manual, 7-stop organ, in 1970, immediately followed by several small one- and two-manual instruments. From 1974 onward the typical instruments were medium-size, two-manual organs. Larger instruments of three or four manuals began to appear with greater frequency after 1983, the largest being a four-manual, 45-stop organ installed in Grace Church, White Plains, New York, in 1989, the only installation in the United States to that time. While the tonal layout of the organs is mainly inspired by European sources, mainly French, the swell divisions of the larger instruments are sufficiently versatile to handle symphonic literature.
The output of new organs was about 55 to 1998, mainly in Québec and Ontario. The company's work has also involved the restoration and reconstruction of a similar number of Québec organs, mainly by Casavant, but including some of historical significance that are over a hundred years old by such early builders as Napoléon Déry and Louis Mitchell.
Several compact discs featuring performances by Québec organists on instruments manufactured by the company, or on reconstructed historical Casavant instruments, have been released in the past decade.8
Principal Pipe Organ Company, Woodstock, Ontario (1961)
The company was established by Chris Houthuyzen in Woodstock, Ontario, a town with a continuing tradition of organbuilding. The founder served his apprenticeship and received further training in The Netherlands before coming to Canada. Small to medium-sized instruments, employing electro-pneumatic action, are the company's specialty, with a contemporary emphasis on the guiding principles of Dutch organbuilding. A total of 119 installations have been completed over the years; the largest was a four-manual, 58-rank instrument. Wooden pipes are made in the shop, but most metal pipes come from suppliers in the United States; their scaling is dictated by the acoustics and intended use of the organ. Chests, reservoirs, ducting, consoles, and casework are manufactured on the premises. Much of the company's work involves rebuilding and maintaining organs, as well as the installation and servicing of church bells, including cast and electronic carillons on behalf of the Verdin Company, Cincinnati, Ohio. The company had three employees in 1998.
Gabriel Kney, London, Ontario (1962-1996)
Gabriel Kney was born in Speyer, Germany; his father was a master cabinetmaker and amateur bassoonist, and his mother was a singer. He served his apprenticeship in organbuilding with Paul Sattel in Speyer (1945-1951), where he assisted in the restoration of historic, sometimes war-damaged, instruments, along with new organ construction. Since the era was a time of transition from the "Romantic" style of organbuilding to the concepts of Orgelbewegung, this trend provided him with the opportunity to learn about and participate in the building of organs of both concepts. Concurrently he was a student of organ literature, liturgical music, harmony, and improvisation at The Institute of Church Music in the same city.
He emigrated to Canada in 1951 and joined the Keates Organ Company in Lucan, Ontario, as an organbuilder and voicer. In 1955 he was co-founder, with John Bright, of the Kney and Bright Organ Company in London, Ontario, with the intention of specializing in tracker instruments. The timing was premature, for only a few musicians and teaching institutions found such instruments of interest; with the exception of two teaching organs of tracker design supplied to a college in the United States, most of the early organs were requested to have electric key action. In 1962 Gabriel Kney established his own company in London, Ontario, where, with enlarged facilities and a staff of six to eight, he specialized in mechanical-action instruments. Organs from the period between 1962 and 1966 were designed in the historic manner of Werkprinzip, with organ pipes enclosed in a free-standing casework and separated into tonal sections. The tonal design of smaller instruments followed 18th-century North European practices, with some tuned in unequal temperaments of the period.
Altogether, his shops produced 128 organs since 1955; the largest in Canada being the four-manual, 71-stop, tracker-action instrument with two consoles in Roy Thomson Hall, Toronto. Since the early 1970s almost three-quarters of the installations were in locations in the United States, several of these in large universities. Occasionally maintenance and historic instrument restoration projects were undertaken.
Wooden pipes were made in the shop, with the exception of very large pipes made to specifications by suppliers in the United States, England, or Germany. Metal pipes also were made to order by independent pipemakers in Germany or Holland. Some console components, such as keyboards, were obtained from suppliers in the United States, England, or Germany. Electric switching devices came from the United States in earlier years, later from England. Blowers were imported from Laukhuff in Germany, Meidinger in Switzerland, or White in the United States. All casework and chest construction was done in the shop.
In 1996 Gabriel Kney retired from active organbuilding and closed his company. Since then he has acted as a consultant to churches seeking advice on organ purchase, restoration, and tonal redesign, and sometimes to other organbuilders.
Karl Wilhelm, Mont Saint-Hilaire, Québec (1966)
Karl Wilhelm was born in Lichtenthal, Rumania, and grew up in Weikersheim, Germany. At the age of 16 he entered apprenticeship with A. Laukhuff, Weikersheim (1952-1956), followed by working experience with W. E. Renkewitz, Nehren/Tübingen (1956-1957), and Metzler & Söhne, Dietikon, Switzerland (1957-1960). After moving to Canada, in 1960 he joined Casavant Frères, where he established the department and trained several employees for the production of modern mechanical organs; while there he was responsible for the design and manufacture of 26 organs. In 1966 he established his own firm, first in Saint-Hyacinthe, then moved to new facilities in Mont Saint-Hilaire, near Montréal, Québec, in 1974. For a while he was assisted by Hellmuth Wolff, now an independent builder (see below).
Karl Wilhelm specializes in building mechanical organs of all sizes, 147 to date, of which 69 are located in the United States and two in Seoul, Korea. Of the total output, 43 are one-manual instruments, 93 are two-manual instruments of medium size, and 11 are three-manual instruments--the largest is a 50-stop instrument in St. Andrew's Presbyterian Church, Toronto, installed in 1983. Two have detached consoles, and four have combination actions with electric stop-action; all instruments have mechanical key action. The design and layout of instruments adhere to the principles of the classical tradition of German and French organbuilding. Three-manual instruments feature a large swell division, suitable for the performance of Anglican Church music and the Romantic repertoire.
All wooden pipes are made on the premises, along with almost one-half of the metal pipes that are handmade of a tin-lead alloy; other metal pipes are imported from Germany. Scaling and voicing are done in the classical open-toe manner for natural speech and mellow blend. Windchests and bellows, consoles and action, and cases are manufactured in a 9,000 sq. ft. workshop. Organs may have cases of contemporary design, or perhaps are more ornate with moldings and hand-carved pipe shades that are compatible with the architecture of the location. Blowers are acquired from Laukhuff, Germany; miscellaneous parts come from other suppliers. The firm does not engage in rebuilding or renovation but services and tunes its own instruments throughout North America. In 1998 the firm had five employees, all trained by Karl Wilhelm.
Wolff & Associés, Laval, Québec (1968)
Hellmuth Wolff was born in Zurich, Switzerland. While a teenager he apprenticed with Metzler & Söhne, Dietikon, Switzerland (1953-1957); in his spare time he built his first organ, a four-stop positiv instrument. He received additional training with G. A. C. de Graff, Amsterdam (1958-1960) and with Rieger Orgelbau, Schwarzach, Austria (1960-1962). In the United States (1962-1963) he worked with Otto Hofmann, in Austin, Texas, and Charles Fisk, in Gloucester, Massachusetts. After moving to Canada he worked with Casavant Frères (1963-1965) in its newly established tracker-action department, and then with Karl Wilhelm (1966-1968), with whom he had worked at Casavant. In the interval 1965-1966 he returned briefly to Europe to work as a designer and voicer with Manufacture d'orgues Genève, in Geneva. Besides playing the piano and singing in choirs wherever he went, he completed his musical training by taking organ lessons with Win Dalm in Amsterdam and later with Bernard Lagacé in Montréal.
In 1968 he opened his own business in Laval, Québec, with one employee; his present associate, James Louder, started his apprenticeship with Hellmuth Wolff in 1974, after training in classical guitar and English. The first large project undertaken in that year was the construction of a three-manual, 26-stop instrument at the Church of St. John the Evangelist, New York City; this was one of the city's first modern tracker-action organs and it incorporated features not yet seen in North America. In 1977 the company moved to a new shop; the firm became incorporated in 1981, and James Louder became a partner in 1988.
Hellmuth Wolff has been part of the Organ Reform in North America since the movement came to this continent in the early 1960s. He specializes in mechanical-action instruments, large and small, whose design is inspired by French or German classical traditions, although other styles are represented that are designed to accommodate a wide range of organ literature. A total of 42 organs have been manufactured; about one-half of these were installed in locations in the United States. While a few small residence or practice instruments have been built, the majority are two-manual organs, in addition to eight three-manual organs, and one four-manual, 50-stop/70-rank instrument installed in Christ Church Cathedral, Indianapolis, Indiana, in 1989.9 Other related activities include rebuilding, restoration, and maintenance work, chiefly in the Montréal area.
Wooden pipes are made on the premises, while metal pipes are acquired from several pipemakers in Canada, U.S.A., and Europe; some reeds are made there, also. Windchests, consoles, and cases are also manufactured on site. Blowers are acquired from Meidinger and Laukhuff in Germany. Several installations feature both mechanical stop-action and capture systems; the first was built in 1977 for the Eighth Church of Christ, Scientist, in New York City; it was probably the first such system in North America. Both sequencers and traditional multilevel capture systems are used. There were eight employees in 1998.
Hellmuth Wolff, along with his associate, James Louder, have contributed to symposiums and written publications on organs and organbuilding.10 Fourteen compact discs, featuring performances by Canadian and American artists on Wolff instruments, have been released, and three others are in preparation.11
Brunzema Organs, Fergus, Ontario (1979-1992)
Gerhard Brunzema was born in Emden, Germany, and grew up in Menden on the Ruhr river, a northern part of the country where there was an abundance of historic organs. After World War II he apprenticed with Paul Ott in Göttingen and worked with him as a journeyman organbuilder (1948-1952). He received extensive technical training, including acoustics, at the Brunswick State Institute for Physics and Technology (1953-1954), and received a Master's degree in organbuilding in 1955. In 1953 he joined the prominent European organbuilder Jürgen Ahrend in the construction and restoration of organs, some in Holland and Germany of great historical significance; this association continued for 18 years. After emigrating to Canada he joined Casavant Frères in 1972 and served as artistic director until 1979; during that time he was responsible for the design of several notable organs in Canada, the United States, Japan, and Australia, along with the restoration of a number of historic Casavant instruments in Ontario and Québec. His experience at Casavant gave him the opportunity to work with very large organs, an experience that was lacking in Germany.
In 1979 he established his own business in Fergus, Ontario. Throughout his career he specialized mainly in small, one-manual, four-stop, continuo organs (25 in all); most of his nine two-manual instruments--the largest was 25 stops--were made between 1985 and 1987. In 1990 he was joined by his son, Friedrich, who had completed his apprenticeship in Europe. Until the time of his death in 1992, Gerhard Brunzema's total output amounted to 41 instruments; of these, 20 were installed in Canadian locations (mainly in eastern provinces), 17 in the United States, one in the Philippines, one in South Korea, and two in European countries. The tonal design of his instruments was strongly influenced by Schnitger organs that he had studied and restored while in Europe. He believed that basic organ design cannot be learned through restoration work, because such instruments were conceived by others; nevertheless, in restorations the intentions of the original builders should be respected. As for new instruments, his philosophy was that "An organbuilder should choose a style and stay with it, so that he not only continues to develop his own skills, but also continues to help improve the skills of the people working for him. . . . Become a master of one thing, get over the initial difficulties very quickly, and then polish your knowledge, the details of which will finally add up to a very good result."12
Koppejan Pipe Organs, Chilliwack, British Columbia (1979)
Adrian Koppejan was born in Veenendaal, Holland, and apprenticed with his father, who was an organbuilder there. He worked with Friedrich Weigle in Echterdingen by Stuttgart, Germany (1963-1966), with Pels & Van Leeuwen in Alkmaar, Holland (1968-1972) as shop foreman of the mechanical organ department, and with his father's company, Koppejan Pipe Organs, in Ederveen, Holland (1968-1972). He moved to Canada in 1974 and established his own company five years later.
Adrian Koppejan strives for a clear, warm, but not loud sound in his instruments, a preference inspired by classical organs of North Germany. This sound palette is reflected in the instruments in which he specializes: small and medium-size tracker instruments; he has built five electromechanical organs, as well. His output to date consists of 19 organs; these have been installed in churches and private residences in British Columbia, Alberta, and Washington state. His largest organ is a three-manual, 31-stop, electromechanical instrument, with a MIDI system, installed in the Good Shepherd Church, White Rock, B.C., in 1995. An instrument of similar size was constructed in 1998. Rebuilding, restoration, maintenance, and tuning are also part of regular activities.
Wooden pipes are mostly acquired from Laukhuff, Germany; metal pipes come from Stinkens in Holland and Laukhuff in Germany. Keyboards are made in Germany by Laukhuff or Heuss. Winding mechanisms, consoles, solid oak cabinets, and casework are manufactured in the shop. Blowers are supplied by Laukhuff, and electrical control systems come from Peterson in the U.S.A. There were two part-time employees in 1998 as Adrian Koppejan reduced the scope of his operations in anticipation of retirement.
Orgues Létourneau, Saint-Hyacinthe, Québec (1979)
Fernand Létourneau was born in Saint-Hyacinthe, Québec, where he worked for while as a carpenter before entering employment with Casavant Frères in 1965; there he apprenticed with his uncle, Jean-Paul Létourneau, who was head reed voicer. He remained with the company for 14 years, where he was head voicer from 1975 to 1978, when he decided to set up his own independent company. First, with the help of a Canada Council grant, he embarked on an organ tour of Europe to study the voicing of old masters. Upon his return to Canada in 1978 he began building organs in Sainte-Rosalie, Québec, and became incorporated in 1979. His first organ, a two-manual, 6-stop instrument, was started in the basement of the family house and then displayed in the shop of a cabinetmaker; it was later acquired by the Conservatoire de Musique du Québec, Hull, where dozens of students have learned to play the organ on this small instrument. In 1984 he moved back to Saint-Hyacinthe, where three other organbuilders were already established. The factory's first building was formerly a municipal water-filter plant; the partially underground space provided a room 35 feet in height, ideal for erecting organs. A second industrial building was acquired recently to supplement the original premises.
A total of 55 organs of various sizes have been built to 1998; 13 others are in progress. The great majority have mechanical action, utilizing classical principles used in European instruments, and with the flexibility provided by ranks inspired by Dom Bédos, Schnitger, and Cavaillé-Coll. The largest will be a four-manual, 101-stop, mechanical-action instrument intended for the Francis Winspear Centre, Edmonton, Alberta. International distribution has been common from the outset, beginning with three early instruments that were installed in Australian locations in the early 1980s (the builder had become known on account of his activities as a voicer of Casavant instruments in that country). Others have been placed in New Zealand, Austria, England (Pembroke College, Oxford, 1995; an instrument is under construction for the Tower of London for completion in late 1999), the United States (over one-third of the total production), and Canada (chiefly eastern provinces, a few in the west). The company now has permanent representatives in the United States, England, and New Zealand. Fernand Létourneau prefers to build instruments of eclectic tonal design that are suitable for the performance of a wide range of organ literature. Historic restorations have also been undertaken.
All organ components, with the exception of electronics, are made in the factory, including wooden and metal pipes to 32-foot length, keyboards, consoles, and casework. Blowers are acquired from Laukhuff, Germany. Middle-size organs are equipped with electronic sequencers, card readers, and similar devices. The company is constantly engaged in rebuilding and restoring instruments of different vintages to original condition, about 50 to date, several of which have been designated as historical or heritage instruments. In 1998 there were 45 full-time staff in the Létourneau "family," of which a number are related to one another as father-son/daughter, uncle, brother, cousin, and husband-wife.