Jim Toevs has a doctorate in nuclear astrophysics. While a professor at Hope College, he taught and consulted in acoustics. A musician, for 20 years he was the principal trumpet in the Los Alamos (NM) Symphony Orchestra and has sung in and directed church choirs.
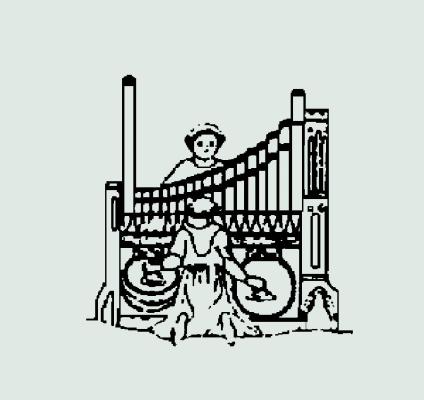
Introduction1
With the installation and voicing of the wonderful new Fisk Opus 133 tracker organ in the First Presbyterian Church of Santa Fe, New Mexico, a number of interesting effects and impacts of Santa Fe’s thin air became apparent. This article will note the major observations and describe the physical acoustics related to organ pipe function at high altitude.
Santa Fe is located at the foot of the southern Sangre de Cristo mountains at an altitude of about 7,000 feet above sea level. In fact, the altitude at the church is 2,127 meters or 6,978 feet. At this altitude, both the atmospheric pressure and density of air are reduced to about 77% of their values at sea level. This difference in pressure corresponds to about 92 inches of water. Considering that most organs operate with a wind pressure of 2 to 4 inches (water column), this difference is quite significant. It is not surprising that organ operation is impacted by this difference; perhaps what is surprising is that the impact is not greater. The fine people of C. B. Fisk dealt with these differences with little difficulty.
Parameters in which high altitude might impact pipe organ performance include:
• Pipe intonation—essentially no effect;
• Windchest blower requirements—observed significant effect;
• Tone production: pre-voicing and voicing—observed significant effect;
• Sensitivity to windchest pressure—observed significant effect;
• Sanctuary acoustics—small but real effect.
Pipe intonation
The impact of altitude on the basic intonation of the organ pipes themselves is minimal. The frequency at which a pipe sounds (fundamental) is based on the length of the pipe and the speed of sound. The length, of course, does not depend on altitude, and fortunately neither does the speed of sound because the ratio of the pressure to density remains the same so long as the temperature is fixed. Basic intonation is therefore not affected by altitude.
Windchest blower requirements
The relationship between blower output (cubic feet per minute, or CFM) and desired windchest pressure (usually measured in equivalent inches of water column supported above the ambient pressure) is given by Bernoulli’s equation. This is perhaps the most fundamental law of fluid flow and basically is just a statement of the conservation of energy. Because density also decreases with altitude, a higher blower capacity will be required in high altitude installations than at sea level in order to obtain the same windchest pressure used at sea level. Using a higher output blower has become standard practice for high altitude installations.
Tone production: pre-voicing and voicing
As Mitchell and Broome have pointed out,2 windchest pressure must compensate for altitude differences when pre-voicing will be performed in a shop that is at a different altitude than the location at which the organ will be installed and receive final voicing. In both flue and reed pipes, the velocity has a direct impact on tuning and sound quality, and it is clearly desirable to produce the same pipe velocities during both pre-voicing and voicing. Once again from Bernoulli’s equation, since the density of air is greater at sea level than at high altitude, a higher windchest pressure must be used at sea level to produce the same velocities in the shop as in the installation. The desired shop windchest pressure is found by multiplying the desired windchest pressure at altitude by the inverse ratio of the atmospheric pressures at the two locations. This is the formula described by Mitchell and Broome.
Pressures of 3 inches and 4 inches were required for Opus 133, and the inverse pressure ratio between Santa Fe and sea level is 1/0.77 = 1.3. Therefore, pre-voicing in the Fisk Gloucester shop used pressures of 3.9 inches and 5.2 inches (water column).
Sensitivity to windchest pressure
During the final stages of voicing in Santa Fe, Fisk Opus 133 was performing very well, but suddenly developed significant intonation and sound quality problems when the HVAC (heat, ventilation, and air conditioning) system for the sanctuary switched between its two modes of operation. The change resulted in an increase of windchest pressure from 3 inches to 3¼ inches (water column). At sea level a change of ¼ inch could be accommodated without greatly impacting organ tuning and voicing, but in Santa Fe such was not the case. This sensitivity was not anticipated, but can be understood through an examination of tone production in organ pipes. In both flue and reed pipes steady energy is supplied through air streams produced by the windchest pressure, and a complex mechanism converts this energy into oscillating energy (sound).
Flue Pipes
In both a tin whistle and in flue pipes, production of oscillation, that is, tone, is through “edge tone generation.” The edge tone frequency depends strongly on air velocity through the windway, and must resonate with one of the natural modes (frequencies) of the pipe; the fundamental mode is always chosen. However, a small change in frequency of the edge tone can pull the edge-tone-pipe system away from the desired intonation. A small change in windchest pressure at altitude will result in a larger change in velocity (and therefore in pitch) than at sea level, due to the reduced density of air at altitude.
Reed pipes
In a reed pipe, air is supplied to the boot from the windchest at a pressure greater than the pressure in the resonator. This causes air to flow under the reed (tongue) into the resonator. Oscillation and therefore tone generation occur when very specific relationships are met among the variables and the stiffness of the reed. Both the stiffness and the oscillating length of the reed are set by the tuning wire.
The effect of a small change in windchest pressure on the frequency of a reed pipe is also greater than it is at sea level. Furthermore, the operating point of the reed, that is, the zero point of its oscillation, moves closer to the shallot as windchest pressure is increased. This may sharpen the onset of each cycle of the oscillation, increasing high frequency content, and, if close enough to the shallot, cause the flow under the reed to become turbulent. Both effects can alter the sound quality of the reed pipe.
To summarize this discussion, for both reed and flue pipes the sensitivity to small changes in windchest pressure is greater at altitude than at sea level, as the Fisk personnel discovered. The solution to this problem for Opus 133 was to gain a better understanding of the Santa Fe FPC sanctuary HVAC system and take appropriate steps to minimize the windchest pressure difference between the two operating modes. Figure 1 is a schematic of the system. The two modes of operation are as follows:
• Recycle mode: Air flows from the blower room to the sanctuary and is returned through the bellows room to the blower room. Valve R is open and Valve FA is closed down to 15%.
• Outside air mode: Outside air is brought in to the blower room and distributed to the sanctuary, and exits through the roof when the sanctuary pressure rises above that of the outside. The recycle valve is closed and the fresh air valve is 70% open.
Cost and environment are the two reasons for two modes of HVAC operation. During winter when outside air is well below the desired ambient temperature in the sanctuary, the air exchange is limited to the 15% required by code for healthy fresh air in the sanctuary (corresponding to the 15% setting of the fresh air valve). A larger percentage of fresh air would require more preheating, increasing gas costs. During summer when outside air is warmer than that desired for the sanctuary, a larger fresh air fraction would increase electric costs for cooling. On the other hand, during spring and fall, when some cooling is needed and outside air is marginally cooler than the desired sanctuary temperature, an increased recycle fraction saves cooling costs. Of course, environmental concerns track with increased gas and electric costs.
Organ pressure is supplied by the small blower in the bellows room and regulated by the bellows. It was found with a simple manometer (U-shaped tube with water) that the organ pressure during the recycle mode was 3 inches of water (that is, water in the manometer rose 3 inches), and in the outside air mode, the organ pressure was 3¼ inches (water column). The ¼-inch change significantly impacted tuning and sound quality. The reason for the ¼-inch change was that the recycle mode involved a great amount of air flow in the return ducts through the bellows room to the blower room, creating a pressure drop of ¼ inch in the return ducts. In this mode, then, the bellows regulating system had to supply 3¼ inches of pressure in order to yield the desired 3 inches of windchest pressure.
When the recycle valve closed to change to the fresh air mode of operation, the only flow in the return duct from the sanctuary to the bellows room was the much smaller flow used by the organ itself. Therefore, there was no loss in that section of duct, and the bellows room was essentially at the same pressure as the sanctuary. With the bellows regulation system still set at 3¼ inches, the windchest pressure became 3¼ inches.
During this time, the main HVAC blower was operating at 100% capacity (60 Hz) even though the blower system included a variable speed control. The following experiment was performed: the variable speed control was set to reduce the blower speed to 2/3 of full capacity (40 Hz), and the pressure differential between the sanctuary and the blower room was measured for both modes of operation—recycle with 15% air exchange and fresh air with 70% air exchange. The only change from the original HVAC settings is that the blower now operates at a lower speed. It was found that the pressure differential at 15% air exchange was 1⁄8 inch, and at 70% air exchange (recycle valve closed) was 1⁄16 inch. As expected, with the organ operating with the bellows regulating system set at 3¼ inches, the organ pressure was 33⁄8 inches at 15% air exchange (recycle mode) and 35⁄16 inches at 70% air exchange.
The bellows regulating system is now set at 31⁄16 inches, yielding an organ-to-sanctuary pressure of 3 or 31⁄16 inches in the two modes of operation—a difference of 1⁄16 inch, small enough that tuning is now not adversely affected. In addition, HVAC noise has been greatly reduced, and the air circulation in the sanctuary, while quite adequate, is less drafty for those sitting in the ends of pews near the walls, where the supply air vents are located.
Sanctuary acoustics
FPC Santa Fe underwent major renovation before Fisk Opus 133 was installed. This included considerable acoustic work in the sanctuary to prepare it for this fine instrument; much of the focus was on steps to increase the reverberation time. The chancel has diamond plaster side walls, which diverge slightly to help sound radiate into the sanctuary. The sanctuary has hardwood floors with minimal carpeting, hard plaster walls, and hardwood pews with reasonably reflective pew cushions. The ceiling was rebuilt with heavy plywood above latillas, and fine sand one foot deep was poured onto the plywood to help contain low frequencies from the organ. Although the reverberation time has not been measured, it is estimated to be about 1.5–2.2 seconds.
In addition to sound energy absorption each time a sound wave encounters a surface, sound energy can be lost through absorption in air. Absorption in air is a rather complex phenomenon involving molecular dynamics, and it varies with air density and relative humidity in a manner that is counterintuitive: thin, dry air attenuates sound more than thick, wet air. Furthermore, the attenuation varies with frequency. Table 1 provides values for attenuation at different frequencies for sea level and the Santa Fe altitude and for 10% and 50% relative humidity. Notice that absorption is greater at low humidity, high altitude, and higher frequency. At high altitude air is thinner and can hold less moisture; relative humidity of 12%–15% is not unusual on summer days in Santa Fe. To mitigate against the drying effects on organ components, a humidifying system is used to maintain relative humidity at around 40%; this also helps to reduce air absorption at higher frequencies.
In Table 1, the sound absorption is given in decibels per kilometer, which is just a little farther than sound travels during a reverberation time of 2.2 seconds. Figure 2 provides a plot of these attenuation data at sea level and in Santa Fe at 50% relative humidity.
Clearly, the attenuation is greater at high altitude and high frequency. However, to understand whether or not this will impact the sound of the organ in the sanctuary, the attenuation must be compared with reverberation decay, the decay in sound energy due to reflection off surfaces. This comparison showed that at 4 kHz, the air attenuation at sea level would be barely noticeable if at all, and would be completely negligible at lower frequencies. In Santa Fe a very astute listener might notice the lack of high frequency components after initial transients on a very dry day, but otherwise the sanctuary acoustics should be little affected by the high altitude.
Conclusion
The differences in organ acoustics and operation between sea level locations and Santa Fe are real and observable, but not severe. Judicious choices of windchest pressure for pre-voicing and voicing and better understanding of the HVAC system both have contributed to a very successful installation: Fisk Opus 133 is now performing regularly and brilliantly. It is hoped that these observations will serve others who choose to install a fine organ at similar altitudes.