John M. Nolte has been in organ building for more than 40 years. In 1986 he founded his own company, which has grown to a staff of five, including his sons Benjamin and Jeremy. The firm has an international reputation for quality wood pipes. They have supplied voiced and unvoiced pipes to many of the best American organbuilders, and recently completed a commission for all of the wood pipes in the new Nicholson organ at Llandaff Cathedral. Nolte has been active in the American Institute of Organbuilders for the past ten years, and has shared technical information with that organization with a Journal of American Organbuilding article, convention lecture, and mid-year seminar on various aspects of wood pipe scaling, production, and voicing. The firm is currently focusing on a highly refined mechanical action.
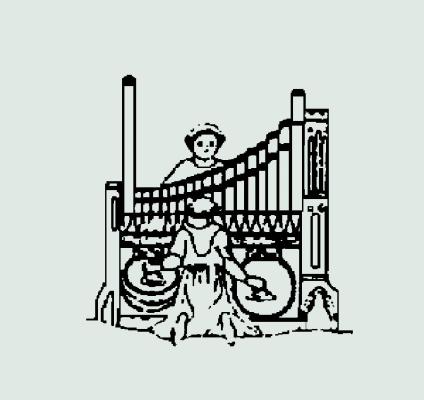
The January 2010 issue of The Diapason featured an article by Judit Angster and Francesco Ruffatti on organbuilders and research.1 This kind of work is very necessary and useful, and it can generate profitable discussion that leads to a better and broader understanding of the pipe organ. The research reported in January is far from complete, but it is a very good discussion starter. Several things in the article struck a chord with me, and I will elaborate on two of them. In this article I will discuss the open-toe versus closed-toe question on the basis of a little technical background that goes back to Daniel Bernoulli, an 18th-century Swiss scientist. This will be followed by a reprint of my article, “Scaling Pipes in Wood,” originally published in the Journal of American Organbuilding in March 2001.
The question of open-toe versus closed-toe requires an understanding of what organ wind pressure is with respect to voicing. There is a big difference between windchest pressure and voicing pressure. Windchest pressure is the pressure present at the toe of the pipe when the valve is opened. Voicing pressure is the pressure at the languid. In every case, voicing pressure is lower than windchest pressure. When we say an organ is on 5 inches wind pressure, measured in the chest, all we know about voicing pressure is that it is less than 5 inches—it could be 2 inches or less. What happens in the foot of the pipe is the key.
In the research article, one measurement that was taken was the wind pressure in the foot of the pipe. The author states, “To everyone’s surprise, it was noted that the wind pressure inside the pipe foot in open-toe pipes showed an average pressure drop of 10% or less from the original pressure inside the windchest, while in the closed-toe pipes, even though these were still fairly open, the pressure drop was about 40 to 50%.”2 I was surprised that a group of voicers and physicists was surprised. This is exactly what one should expect. Let’s look at what happens in the foot of the pipe. See Figure 1.
When the organist plays the note, air enters the foot of the pipe through the toe, and it exits the foot of the pipe through the flue. If the pipe is well made, and the toe is seated properly in the chest, all of the air that enters the toe leaves through the flue. When the chest pressure is higher, the air coming out of the pipe hole travels faster. When the pressure is lower, the air travels slower. The size of the hole does not affect the speed of the air—it just controls the volume of air that comes out of the chest. If the flue is completely closed so the air has nowhere to go, when the valve is open the pressure in the foot will rise until it is equal to the pressure in the chest. If we open the flue, air will escape from the foot, and the toe hole will replace it as fast as it can. In every case the pressure in the foot will be lower than the pressure in the chest. Because the volume of air leaving the pipe at the flue is the same as the volume of air entering at the toe, we can use variations of Bernoulli’s equation to predict what the difference in chest pressure and foot pressure will be. The rule is that the pressure drops at the toe and the flue vary inversely with the squares of their areas. Here is the formula:
(Atoe)2 = ΔPflue
(Aflue)2 ΔPtoe
where A is the area of the toe or flue, and ΔP is the pressure drop at the toe or flue.
Let’s illustrate this with a chart. If the original chest pressure is 100mm, then the area of the toe compared to the area of the flue will give these results for the pressure in the foot:
Atoe Aflue Foot Pressure
1 2 20mm
1 1 50mm
2 1 80mm
9.95 1 99mm
Notice that when the area of the toe opening and the area of the flue are the same, half of the chest pressure is lost in the toe, and half is lost when the air exits the flue to the atmosphere. When the toe opening is smaller than the flue, the pressure in the foot is even less than half of chest pressure. We have seen examples of pipes voiced on 10″ wind pressure that were actually speaking on 2″ wind pressure. For flue pipes, wind pressures of 8–10″ are found at the languid of fairground organs designed to be played outdoors and heard up to a quarter mile away. Rarely do indoor pipes receive pressures over 4″ at the languid. When the toe is larger than the flue, more than half of the chest pressure is present in the foot of the pipe. When the ratio is about 10:1, the toe is fully open and 99% of chest pressure is present in the toe.
For many years the American Institute of Organbuilders has recommended that in good flue voicing we aim for a toe that is twice the area of the flue. Notice from the chart that this yields 80% of chest pressure in the toe. This allows the voicer a little latitude to make the pipe louder or quieter by regulating the toe more or less open.
Why the emphasis on the pressure in the foot? Air passes through the flue to the upper lip where an oscillation develops that creates the standing wave in the body of the pipe. What matters for pipe speech is the velocity of the air at the flue, and that velocity is determined by the pressure in the foot of the pipe just below the languid. The blower pressure, the pressure in the chest, and the pressure at the bottom of the ocean are all irrelevant.
With this technical information in mind, I really must question the experiments that were supposed to determine whether or not there is a difference between closed-toe and open-toe voicing. The experiments referred to in the article state that windchest pressure was constant, and that pressure in the foot was twice as much for the open-toe compared to the closed-toe. Then both pipes were voiced to match loudness. This proves nothing about the difference between open-toe and closed-toe voicing.
If I voice a pipe with an open toe on 70mm wind pressure, and then voice a pipe with an open toe on 35mm wind pressure, and I make the two pipes equally loud, will there be a difference in tonality? Of course there will be. The pipe voiced on the higher pressure will drive the upper harmonics more in relation to the fundamental, and the tone will be brighter. That is exactly what the chart in Figure 5 in the article illustrates. The only difference is that the researchers achieved a pressure in the foot of about 35mm by closing the toe, instead of opening the toe and setting windchest pressure at 35mm.
If I want to compare open-toe voicing to closed-toe voicing, the pressure in the foot must be the same, not the pressure in the windchest. If we use the toe-to-flue ratio of 2:1, that means that to achieve the same tonality between the two voicing methods, the chest pressure for the closed toe must be 25% higher. If I voice an open-toe pipe on 80mm windchest pressure, I must voice the comparable closed-toe pipe on 100mm windchest pressure. The cut-up, the size of the flue, and the treatment of the languid should be the same.
When organs started to use tubular pneumatic and electro-pneumatic actions, these early actions required windchest pressures of 4″ to 6″ to operate properly. When these new chests were used to rebuild older organs that were voiced on lower pressures with open or nearly open toes, the old pipes had to be revoiced to the higher windchest pressures. Frequently, all the voicers did with the old pipes was to close the toes until the pressure in the foot was lowered to where it had been originally. This method is fast, and if the pipes were going back into the same room, the original voicing and regulation was already correct.
In the last few years we happened upon a large supply of treble pipes that were well made and voiced with open toes on low pressure, around 65mm (21⁄2″). We have used them to replace inferior trebles in a number of sets of pipes on several different, but higher, pressures. Closing the toes was all that was necessary, unless the pipes needed to be made significantly louder.
To do a meaningful comparison between open-toe voicing and closed-toe voicing, several identical pipes should be voiced to match as perfectly as possible with open toes. Then raise the windchest pressure for one of them and see if closing the toes will bring back the match. It will.
The researchers also noted another difference:
Under equal conditions, the ‘wind noise,’ a natural component of the pipe sound that the voicer normally tends to reduce or eliminate, was by far more noticeable in closed toe pipes. This is not at all an irrelevant difference: in practical terms, it means that pipes voiced with closed or partially opened toes will require a heavier presence of ‘nicks’ at the languids in order to control wind noise, and this in turn will determine significant modifications to the structure of their sound.3
There are several distinct ways wind noise can be generated in a pipe with closed toes, and the treatment must address the problem. Nicking is seldom the only solution, and rarely is it the best solution for eliminating wind noise.
At the toe, if chest pressure is quite high, the velocity of the air through the toe can create turbulence and, consequently, noise. Turbulence is exacerbated when friction in the toe opening slows down the air at the boundary of the hole, while the air towards the middle of the hole is unimpeded. The solution is to carefully countersink the toe hole so that the smallest part of the hole comes to a point in the cross-section. See the photos for examples of a noisy and a quiet toe. The closed toe pictured in the research article has not been properly treated to keep it as quiet as possible.
At the flue, noise is generated when the flue is overly large. This happens for different reasons. When the chest pressure or foot pressure is too low, the flue must be opened more to get enough volume of air to produce a loud enough sound. This can happen with either open or closed toes. When the pressure in the foot is too high, opening the flue will lower the foot pressure, but it also creates a wider air stream than necessary to create the musical note, so some of the air generates noise, not tone. Large flues are also sometimes used to compensate for upper lips that are too thick. Once again, excessive amounts of air traveling through the flue create unwanted and unnecessary noise. A thinner lip and smaller flue will eliminate the problem.
When the area of the toe is relatively small compared to the flue, the velocity of the air entering the toe is substantially higher than the velocity of the air exiting the flue. As the air in the foot slows down, the degree to which it has to slow down will create turbulent conditions in the foot of the pipe, which generate noise both in the foot and at the flue. Some voicers use steel wool or other devices in the foot itself to overcome this.
Nicking can be used to control wind noise in all of these circumstances, and if the tonal quality resulting from the nicking is what one wants, so be it. If, instead, we want a tone more like what is achieved without nicking in open-toe voicing, attention to detail can achieve this quite easily.
The 2:1 relationship of toe area to flue area, along with the correct windchest pressure, will overcome these problems. A ratio of 1:1 can be used with good results if the voicer is very attentive to detail. When the toe becomes smaller than the flue, trouble is not far behind. The use of partially closed toes to regulate pipe speech can provide results equal in virtually every respect to what can be achieved with open toes. In order to accomplish this, it is necessary for the windchest pressure to be higher than it would be for open-toe voicing so that the pressure in the pipe foot is ideal. Raising the chest pressure too high can cause wind noise problems, but these can be controlled by keeping the windchest pressures from being excessive. So much for my contribution to this part of the discussion.
The researchers also mentioned investigations into transitions between stopped and open pipes, or between wood and metal pipes within the same rank. My research on wood pipes will be presented in the reprint of my March 2001 article, “Scaling Pipes in Wood.” The research for this article was based on years of making reproductions of wood pipes for antique orchestrions, and a study of historic wood pipe scaling, notably the Compenius organ of 1610. On the practical side, this led to a commission for an all-wood practice organ, which also had strict action requirements. This organ will be featured in a future article.