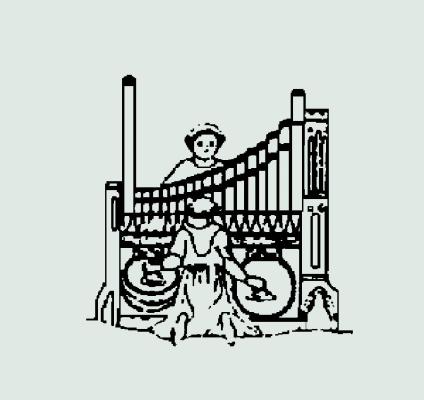
Parkey OrganBuilders,
Duluth, Georgia
Opus 11, First Presbyterian Church, Gainesville, Georgia
Our first conversations with Michael Henry, director of music for First Presbyterian Church, Gainesville, Georgia, took place in early 2007. At that time, the church had a two-manual, 23-rank Möller organ installed in 1975. Our discussions revolved around the mechanical condition of the Möller and the limitations of the tonal design. The church knew that work was imminent for the Möller in order to maintain reliability. As usual, funding remained an issue.
In mid-2008, Joseph S. Hatfield, a local business owner and church member, made provisions for a large bequest shortly before he passed away. This meant that the budget actually became larger than originally projected, and the discussions expanded to replacement of the Möller organ. The planning process broadened to include a consultant, James Mellichamp, Vice-President of Academic Affairs and organ professor of Piedmont College in Demorest, Georgia.
The original organ was a product of the neo-baroque influence and presented many challenges for use in church services. Our collaboration with Dr. Mellichamp produced a new three-manual and pedal specification of 40 ranks. The specification was designed to provide a more comprehensive instrument for choral accompaniment, congregational hymns, and an expansive list of organ literature.
The new organ incorporates two enclosed divisions—Swell and Choir. The Great and main Pedal stops remain unenclosed. Secondary Pedal stops are drawn from the Swell and Choir divisions, offering options for enclosed Pedal. The organ offers a tremendous level of independent stops, with very minimal unification. Three principal choruses are available. The primary principal chorus is located in the Great division, with a secondary principal chorus located in the Choir division. The Pedal division also features its own independent chorus from 16′ pitch to Mixture. The organ retains some of the flutes and strings from the previous Möller. These stops were rescaled and revoiced for new locations and pitches. We then completed the complement of flutes. Along with new strings in the Swell division, a secondary string and celeste stop were added to the Choir division.
The Great division is more eclectic than our previous designs. The principals are generously scaled, with the foundation pitch focused on the 8′ rather than the 4′ pitch as in the previous organ. The principals offer a warm body of sound, with a clear articulation and singing character to provide an excellent backbone for congregational singing. The 8′ and 4′ flutes offer a nice complement to the principals, while providing good color on their own. The 8′ and 4′ flutes also provide the foundation for a complete French flute Cornet décomposé. The Great Trompete is of German design, so while powerful it allows for a good blend with the principal chorus for ensemble use.
The Swell division is conceived as a French-based design, including the use of harmonic flutes at 4′ and 2′ pitches. The Trompette is fiery and is complemented by the 16′ Basson and 8′ Oboe. The commanding presence of the 8′ Trompette in the space did not require a 4′ reed. The foundations are drawn from the 8′ Viola and 8′ Chimney Flute, with the focus of the chorus from the 4′ Principal. Our use of violas helps to reinforce the 8′ foundation in a division that does not contain separate principal or diapason tone. Our violas provide a slightly more weighted sound, yet retain the sonority of string tone. The 4′ Harmonic Flute and 2′ Octavin (Harmonic Piccolo) provide a soaring intensity for the Swell division and tie in well to the Plein Jeu IV. The swell box construction features our own sound-insulated, double-wall design for excellent expression, providing a much greater effect than the previous Möller swell box.
The Choir division offers the versatility of an English Choir, while blending some of the options for sounds of a Positiv. The Choir features the same style of expression box construction as the Swell division. An 8′ Violin Diapason is our starting point for the Choir division. The 8′ Violin Diapason and 4′ Violin Principal were conceived to provide some of the missing sounds from the old organ. First Presbyterian has long enjoyed the presence of a strong choral ministry, with an expansive repertoire of anthems and oratorios from the Baroque period to the contemporary era. The shortcomings in choral support and expressiveness of the Möller organ were the main considerations and concerns of the organ committee. The principals and the inclusion of an 8′ Dulciana and 8′ Unda Maris add a new dimension of options and sound that the organist never had in the old organ. The 2′ Principal and 11⁄3′ Quint add the final clarity to the Choir division with sparkling elegance. The 8′ Schalmei provides a pleasant crossover between a small ensemble reed and a light solo reed.
The Pedal division provides more than ample undergirding for the entire organ. A new polished façade comprises the Pedal 16′ Principal and 8′ Octave as well as the bass of the Great 8′ Principal. The division hosts an independent 16′ Subbass, 4′ Choral Bass, 4′ Nachthorn, Mixture III, and 16′ Posaune. After our discussions with the consultant, we provided both a 32′ Resultant and a derived 32′ Cornet from the tonal resources. Both offer that extra level of depth in the pedal line between soft and full registrations.
During the construction of an organ at Parkey OrganBuilders, it is our goal to provide a cohesive musical instrument. While adopting influences and ideas from many of the schools of organ construction, the specification nomenclature and the tonal finishing reflect the solidity of American organbuilding. One of the best compliments we receive regularly is that “stops blend beautifully and do what they are supposed to do.” Much care is given to the scaling of each stop as it relates to its solo and ensemble needs. All of our instruments are carefully finished in their space at completion of the installation.
When tracker action is not an option, our firm elects to use electro-pneumatic action in slider, unit, and pitman variations. Winding systems are always regulated via wedge or box reservoirs for optimal control, yet allowing for a gentle wind flex to prevent a sterile sound. Our operation in Duluth, Georgia is one of the largest facilities in the southeastern United States dedicated solely to the construction of pipe organs. Our use of modern-day technology—including CAD (computer-aided design), Photoshop, and CNC (computer numerically controlled) machinery—allows us to create organs with artistic flair, established mechanical designs, and high levels of accuracy. Our staff is involved with the creation of the organ from paper to final installation. Custom consoles, casework, windchests, wooden pipework, and winding systems are all constructed in our Duluth location.
The console for Opus 11 is constructed in a solid walnut case with burled walnut veneers as well as maple, mahogany, and ebony. The console features turned wooden drawknobs in ebony with maple faces. Engravings provided throughout are laser-engraved in our shop. Custom English keyboards feature bleached bone naturals with ebony sharps. Our ergonomic designs for console construction are based on AGO standards to provide a comfortable familiarity for the organist. Solid State Organ Systems are used for capture, relay, and MIDI and are known the world over for their reliability and intuitive designs for the organist.
We appreciate the cooperation of Michael Henry and the staff and members of First Presbyterian Church, Gainesville, Georgia. The church has made a conscious effort already on three occasions to involve children and youth in the organ project through the removal of the original pipework, an excursion to our shop to view the new organ through assembly, and a hands-on “bringing in the pipes” event for celebratory installation of the first pipes on Epiphany. We also thank James Mellichamp for his direction and cooperative collaboration in this instrument. The end results have provided a substantial experience in both sight and sound. Instruments of this caliber continue to provide enthusiasm and excitement for our staff. The dedicatory recital is scheduled for April 18, 2010, and will be performed by Dr. Mellichamp. First Presbyterian Church appreciates the generosity of Mr. and Mrs. Joseph S. Hatfield, who made this project a reality.
—Phillip K. Parkey
President and Tonal Director
Parkey OrganBuilders
Parkey OrganBuilders
Staff listing, Opus 11
Tonal design and finishing: Phillip Parkey
Mechanical engineering and visual design, installation: Michael Morris
CNC operations for console, structure, windchest construction winding systems and installation: Philip Read, Josh Okeson
Console and relay wiring, installation: Doug Rogers
Chest actions, wiring, winding, assembly, installation: Otilia Gamboa
Office manager and installation: Josh Duncan
Voicing and tonal finishing, installation: Kenny Lewis
Parkey OrganBuilders, Opus 11
First Presbyterian Church,
Gainesville, Georgia
GREAT (Unenclosed)
16′ Bourdon Swell
8′ Principal 61 pipes
8′ Metal Gedackt 61 pipes
4′ Octave 61 pipes
4′ Spitz Flute 61 pipes
22⁄3′ Nazard 61 pipes
2′ Tapered Flute 61 pipes
13⁄5′ Tierce 61 pipes
11⁄3′ Mixture IV 244 pipes
8′ Trompete 61 pipes
8′ Fanfare Trumpet Prepared for
Tremolo
Zimbelstern
SWELL (Enclosed)
16′ Bourdon 12 pipes
8′ Chimney Flute 61 pipes
8′ Viola 61 pipes
8′ Viola Celeste GG 54 pipes
4′ Principal 61 pipes
4′ Harmonic Flute 61 pipes
2′ Octavin 61 pipes
1′ Plein Jeu IV 244 pipes
16′ Bassoon 12 pipes
8′ Trompette 61 pipes
8′ Oboe 61 pipes
Tremolo
Swell 16
Swell Unison Off
Swell 4
CHOIR (Enclosed)
8′ Violin Diapason 61 pipes
8′ Gedeckt 61 pipes
8′ Dulciana 61 pipes
8′ Unda Maris TC 49 pipes
4′ Violin Principal 61 pipes
2′ Principal 61 pipes
11⁄3′ Quint 61 pipes
8′ Schalmei 61 pipes
8′ Fanfare Trumpet Great
(Uncoupled)
Tremolo
Choir 16
Choir Unison Off
Choir 4
PEDAL
32′ Resultant 32 notes
16′ Principal 32 pipes
16′ Subbass 32 pipes
16′ Bourdon Swell
8′ Octave 12 pipes
8′ Bass Flute 12 pipes
4′ Choral Bass 32 pipes
4′ Nachthorn 32 pipes
2′ Mixture III 96 pipes
32′ Cornet V 32 notes
16′ Posaune 32 pipes
16′ Bassoon Swell
8′ Trompete 12 pipes
4′ Schalmei Choir
8′ Fanfare Trumpet Great
Couplers
Great to Pedal 8
Great to Pedal 4
Swell to Pedal 8
Swell to Pedal 4
Choir to Pedal 8
Choir to Pedal 4
Swell to Great 16
Swell to Great 8
Swell to Great 4
Choir to Great 16
Choir to Great 8
Choir to Great 4
Swell to Choir 16
Swell to Choir 8
Swell to Choir 4
MIDI on Swell
MIDI on Great
MIDI on Choir
MIDI on Pedal
Great/Choir transfer
Capture System
(100 levels of memory)
10 general pistons, thumb and toe
6 divisional pistons, thumb/manual
6 divisional toe studs for Pedal
Swell to Pedal reversible, thumb and toe
Great to Pedal reversible, thumb and toe
Choir to Pedal reversible, thumb and toe
Swell to Great reversible, thumb only
32′ Resultant reversible, toe only
32′ Cornet reversible, toe only
Zimbelstern reversible, thumb and toe
Full Organ reversible, thumb and toe
General Cancel, thumb only
Set piston, thumb only
“Any Piston Next” sequencer
Full MIDI interface and record/playback is included
Cover photo by Travis Massey, Magic Craft Studio