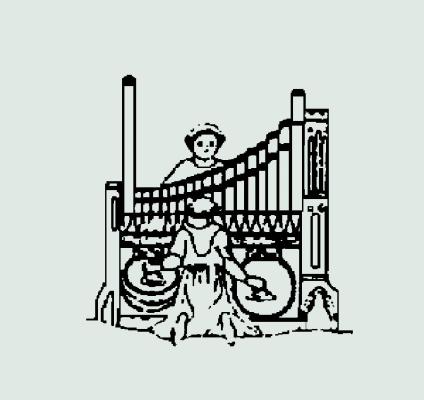
A. E. Schlueter Pipe Organ Company, Lithonia, Georgia
First Presbyterian Church, Savannah, Georgia
The new pipe organ for First Presbyterian Church, Savannah, Georgia is a custom-built instrument comprising 47 ranks of pipes with an eclectic specification paying homage to the American Classic school of organbuilding. A core concept of our company’s tonal ideal is “to design instruments that have warmth but not at the expense of clarity and clarity not at the expense of warmth.” We believe this to be one of the most important considerations in an instrument that draws its lineage from the organbuilding schools of Germany, France, and England. Of utmost concern was adequate support of the choir and congregation taking into account the acoustics of the church and the literature required of the organ in this worship setting.
The church musicians and organ committee had a clear vision for the type of organ they desired for worship when they contacted our firm three years ago. They listened to many instruments in order to define their ideals. Certain styles of organ design were clearly not suitable for First Presbyterian. Ultimately, they gravitated toward the collective work of Aeolian-Skinner circa 1940s–1950s as directed by G. Donald Harrison. As our firm worked with the church to develop a specification, it was decided that our work was to be in the spirit of this great builder but not a stop for stop copy. Key points of departure are found in the presence of an 8' Principal chorus in each manual division, a more dominant Choir division than would have been found in the period, and the choice of English reeds. Many of our decisions were guided by voicing sample pipes in the church prior to construction of the organ. While setting samples in the church it became evident that the French reeds often found on a Harrison-era organ would not be suitable in this acoustical environment.
During the planning and tonal finishing stages of the organ we worshipped with the choir and congregation in order to gauge critical balances and dynamic levels. We were also able to use the talents of the church musicians and other Savannah organists, each bringing their own playing and registration style to the instrument. This has been very important in the sound of the organ as it is heard in its final form.
A primary challenge was where the organ would be located. The church was built in the late 1940s and was designed to be enlarged by removing the front chancel wall. Until this came to pass, a temporary front chancel wall was built containing a large stained glass window depicting the Stations of the Cross. As the dream of a pipe organ lay dormant for many years, the congregation grew to accept the chancel design with its stained glass window and stone arch as key elements of the sanctuary. These elements were a cornerstone of the visual integrity and symmetry they wanted to maintain. Numerous design studies were undertaken with free-standing organ cases inside and outside the arch and its impact on the chancel stained glass window.
A visual design emerged from our engineering study that provided a focal point for the stained glass window with Christ as the center. The solution was to build a large chamber on the front of the sanctuary and to utilize a suspended light box for display of the window. In this manner we were able to speak around and under the window with a large degree of tonal freedom and minimal tonal occlusion. The organ chamber is built of solid concrete to concentrate the sound of the organ forward without a loss of energy. This allowed us to work with more modest scales and wind pressures than might have been required under other circumstances due to placement and chamber depth. During the installation and subsequent tonal finishing we were very pleased with the transfer of energy from this organ chamber design and construction.
The organ case was built of native white oak, finished to match other woods in the sanctuary. The lower case panels are designed as a reflective surface for the choir. The organ grille panels were designed to provide a decorative allure while acting tonally transparent. Our treatment of the organ grille panels allowed us to eliminate the use of grille cloth that is often tonally absorptive and does not allow a free exchange of air between the sanctuary and the organ chambers.
Ever mindful that an organ is musical only when it is in tune, we took great efforts in the design to provide a stable environment. A primary consideration was to place all of the manual and pedal pipework at one common level, thus avoiding differing thermo climes and the resulting tuning issues. The organ blower is located beneath the organ and draws its air from the bass of the Swell and Choir chambers. In this manner air is drawn from the same environment as the pipes to promote tuning stability. Metal windlines were used to dissipate heat buildup. The chambers were also designed with air returns in the ceiling to draw the ambient sanctuary air back into the chamber. This system is coupled to the sanctuary HVAC and runs whenever it is engaged. Thus no special controls are needed to set proper conditions in the church in respect to the organ. This careful attention to layout and other issues that affect the environmental conditions of the organ has enabled us to maintain a one-degree variance between all divisions, which promotes tuning stability.
To provide control over the volume of the organ’s resources, the organ contains two expressive boxes, one for the Swell division and one for the Choir division. Built with extra-thick shades that overlap and interlock, the expressive boxes provide wide dynamic control with electro-pneumatic servo-motors faithfully duplicating the performer’s movement of the expression shoes at the organ console. This degree of expression finds additional favor with control of the high-pressure hooded Tromba Heroique in the Choir division. Constructed with small Willis tuba shallots on 16? wind pressure, this dynamic reed is duplexed to the Great division and can be tamed for use as a chorus reed by its enclosure. Indeed, the degree of control allowed by truly effective expression allows the use of a variety of stops for choral and congregational accompaniment and tonal layering that is not often possible in other instruments.
Our firm built electro-pneumatic slider chest actions of the Blackinton variety with our electro-pneumatic primary design. This type of chest action has the ability to operate over a wide pressure range without the repetition problems and pressure limitations often associated with electric pull-down slider chests. Electro-pneumatic unit chests are provided for all large bass pipes, offset chests, and reeds.
One fabled and often debated element in organ mechanical design is the winding system of the modern organ. Often in art one can consider that anything that draws attention to itself is probably too much. This maxim is used as an internal compass in our decision-making processes. Our concern is a winding system that provides a solid wind supply without being sterile. The winding on the Savannah organ is accomplished through the use of ribbed and floating lid regulators fitted with weights and springs. The organ reeds are placed on independent wind regulators to allow a pressure differential from the flue stops and to permit independent tremulant control. All of the windchests are individually fitted with tunable concussion bellows to allow fine regulation. In this manner, we achieved stable winding that still maintains a presence of life.
The resources of the organ are controlled by a three-manual drawknob console. Built in the English style, the console sits on a rolling platform to allow mobility. The console exterior is built of white oak with an interior of mahogany and ebony. The console features modern conveniences for the organ performer such as multiple memory levels, programmable crescendo and sforzando, transposer, MIDI, and the ability to record and play back organ performances.
As the music ministry continues to grow, the organ is prepared for additional stops in the Great, Swell, and Choir divisions. There is also preparation for an Antiphonal division with a horizontal Trompette en Chamade in the rear of the sanctuary. These design considerations allow the organ to grow with the needs of the congregation.
The organ chassis, inclusive of the organ case, console, windchests, winding system and wood pipes were built entirely by the Schlueter craftsmen. Delivery and installation of the organ took five weeks with the tonal finishing lasting six weeks beyond the installation. Tonal finishing was completed under the direction of Arthur Schlueter III and Daniel Angerstein with the assistance of Lee Hendricks, John Tanner, Marc Conley, and Al Schroer. As is the practice of our firm, the tonal finishing of the organ has occurred with several repeat trips to work with the pipes and evaluate the results. We find that this method of tonal finishing results in a finer degree of voicing than is possible from one concentrated trip. It is expected that over the course of the year we will continue to make small changes and refinements.
Quality organ building is never the result of one individual but is the result of the synergy of a team. In this respect our firm was ably assisted by the clergy, music staff, church staff, organ committee chairman and the members of the organ committee. These individuals readily gave of their time and talents and provided invaluable assistance from the inception of the organ project to its installation and tonal finishing. Their effort, coupled with that of the craftsmen of our firm, has resulted in the creation of this unique instrument. We would like to take this opportunity to thank each of the individuals involved with this project. We would also like to publicly thank the members of the First Presbyterian Church in Savannah, the organ committee, and individual members including but certainly not limited to minister Stephen Williams, parish associate Nelle McC. Bordeaux, Ray McClain, organist, Jim Adams, music director, and organ committee chairman Bill Ricks.
Established in 1973, the A. E. Schlueter Pipe Organ Company is located of 20 miles east of Atlanta in the town of Lithonia, Georgia. The facility contains over 22,000 square feet of space dedicated to building organs for worship and recital. Created as a family business, the company is operated under the guidance of Arthur Schlueter, Jr. and Arthur Schlueter III. Together they provide direction to over 25 artisans in the building and rebuilding of pipe organs. In a desire to be mindful of the reason for the instruments, the seal of the company incorporates “Soli Deo Gloria,” God alone the glory. Additional information on our firm and projects can be viewed at
—Arthur Schlueter III
A. E. Schlueter Pipe Organ Company wishes to thank its staff including:
Art Schlueter Jr.—president
Arthur Schlueter III—vice president/ tonal and artistic direction
John Tanner—vice president of production/tonal finisher
Howard Weaver—senior design engineer
Shan Dalton—office manager/ administrative assistant
Bob Parris—executive assistant
Marc Conley—shop foreman/tonal finisher
Randy Wilson—assistant shop foreman
Rob Black—master cabinetmaker/CAD organ design
Sam Polk—organ assembly, tuning assistant
Al Schroer—voicing, organ assembly & tuning
Dallas Wood—organ assembly, tuning assistant
Michael DeSimone—leather & small parts
Katrina Thornton—financial secretary
Barbra Sedlacek—office support
Joe Sedlacek, Sr.—console wiring
Joe Sedlacek, Jr.—organ assembly
Mark Montour—CNC operator/woodwright
Dustin Carlisle—organ assembly
Jeffery Chilcutt—organ assembly
Kelvin Cheatham—organ assembly
Kevin Cartwright—tuning & service
Bob Weaver—tuning & service
Othel Liles—electrical engineer
Patty Conley—organ assembly
Herb Ridgely, Jr.—sales and support staff
Don Land—sales and support staff
David Stills—sales and support staff
Noel Jones—sales and support staff
A. E. Schlueter: First Presbyterian Church, Savannah, Georgia,
III manuals, 47 ranks
GREAT (Unenclosed)
16' Sub Principal
8' Open Diapason
8' Principal
8' Harmonic Flute
8' Bourdon
8' Gemshorn (Choir)
8' Violone
4' Octave
4' Flute
2' Fifteenth
IV–V Fourniture 11?3'
8' Clarinet (Choir)
16' Tromba Heroique (non-coupling) (Choir)
8' Tromba Heroique (non-coupling)
(Choir)
4' Tromba Heroique (non-coupling) (Choir)
Zimbelstern
Chimes (Choir)
Tremulant
SWELL (Expressive)
16' Lieblich Gedeckt
8' Geigen Principal
8' Chimney Flute
8' Viole de Gambe
8' Viole Celeste
8' Flauto Dolce
8' Flute Celeste
4' Geigen Octave
4' Nachthorn
22/3' Nazard
2' Recorder
11/3' Tierce
IV Full Mixture 2'
16' Bassoon
8' Trumpet
8' Oboe
4' Clarion
Tremulant
Swell to Swell 16'
Swell Unison Off
Swell to Swell 4'
CHOIR (Expressive)
16' Gemshorn
8' Principal
8' Holzgedeckt
8' Gemshorn
8' Gemshorn Celeste
4' Principal
4' Spindle Flute
2' Fifteenth
11/3 ' Larigot
1' Sifflote
III Scharf 2/3'
8' Clarinet
16' Tromba Heroique (non-coupling)
8' Tromba Heroique (non-coupling, high-pressure, hooded)
4' Tromba Heroique (non-coupling, high-pressure)
Harp (digital)
Tremulant
Choir to Choir 16'
Choir Unison Off
Choir to Choir 4'
Antiphonal (prepared for)
PEDAL
32' Violone (digital)
32' Bourdon (digital)
16' Contra Bass (digital)
16' Sub Principal
16' Gemshorn (Choir)
16' Subbass
16' Lieblich Gedeckt (Swell)
8' Octave
8' Gemshorn (Choir)
8' Bourdon
8' Gedeckt (Swell)
4' Choral Bass
4' Cantus Flute (Great)
2' Flute (Swell)
III Mixture 22/3'
32' Contra Trombone (digital)
16' Trombone
16' Bassoon (Swell)
8' Tromba (Choir)
8' Trumpet (Swell)
4' Tromba (Choir)
4' Clarinet (Choir)
Inter-Manual Couplers
Great to Pedal 8', 4'
Swell to Pedal 8', 4'
Choir to Pedal 8', 4'
Antiphonal to Pedal 8'
Swell to Great 16', 8', 4'
Choir to Great 16', 8', 4'
Antiphonal to Great 8'
Swell to Choir 16', 8', 4'
Antiphonal to Choir 8'
Antiphonal to Swell 8'
Choir/Great Transfer (latching piston)
(divisional pistons transfer)
MIDI Controls (with record/playback)
MIDI to Great
MIDI to Swell
MIDI to Choir
MIDI to Pedal
Combination system with a minimum of 128 levels of memory
Six thumb pistons each division
12 General pistons—thumb and toe
Great to Pedal—thumb and toe
Swell to Pedal—thumb and toe
Choir to Pedal—thumb and toe
Swell to Great—thumb
Choir to Great—thumb and toe
Swell to Choir—thumb
32' Violone—reversible—thumb
32' Bourdon—thumb
32' Contra Trombone—reversible—thumb and toe
Sforzando—thumb and toe (programmable)
Crescendo Pedal (programmable)
Set Piston—thumb
General Cancel—thumb
Additional Features
Zimbelstern—9 bells
Chimes—32 notes
MIDI (programmable as preset stops)
Data File Sequencer provided for Playback/Record of organ performance
Transposer
Programmable Sforzando
Programmable Crescendo
Tracker touch keyboards