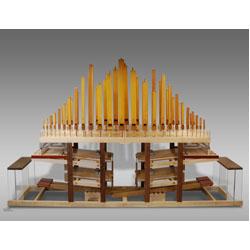
Parsons Pipe Organ Builders of Canandaigua, NY has recently completed construction of The AUERGLASS; a tracker action, foot pumped pipe organ. The musical vision for this project is that of artists Tauba Auerbach and Cameron Mesirow. Parsons was challenged to meld the physical constraints of traditional pipe organ building with this avant-garde concept.
The Auerglass is a two-person mechanical action organ. The instrument requires two people to create music and cannot be played alone. This marriage of interdependency and cooperation is achieved as one player pumps the bellows in order for the other to create music and vice versa.
The two keyboards cover a four-octave range and have been divided so that each of the two players has every other note at their disposal. Auerbach and Mesirow (of the band Glasser), will play a composition written specifically for the instrument. It combines music that Auerbach wrote as a child, songs from Glasser and new materials.
The Auerglass will be played at the opening on September 3rd, as a prelude to a Glasser performance at 8pm on September 11th, and daily at 5pm from Tuesday through Saturday during the exhibition.
For additional information visit www.Deitch.com
The Auerglass instrument
Summary of features:
• 49 notes, suspended key action, tone channel windchests, foot pumped
• Pipes - 8’ Clarabella of southern yellow pine
• Keys of eastern white pine with coverings of plum (naturals)and maple (sharps)
• Keycheeks, pumper pedals and other accents of blood wood and figured maple
• Four wedge bellows, wind conduits and pumper levers of quartersawn white oak.
• Structure and bench seat of walnut and maple; joinery is mortise and tenon
• Bench frame, pallet box and racks of ¾” clear acrylic
• Organ divides in the middle for transport
• Adjustable pumper lever ratios; Wind pressure 3.3” W.C. (84mm)
• Overall dimensions L = 15’-10 ½”; W = 2’-7” ½”; H = 9’-8”
Tauba Auerbach’s “HERE AND NOW/AND NOWHERE” exhibition at Deitch Projects,
September 3 – October 17, 2009,
18 Wooster Street, NYC