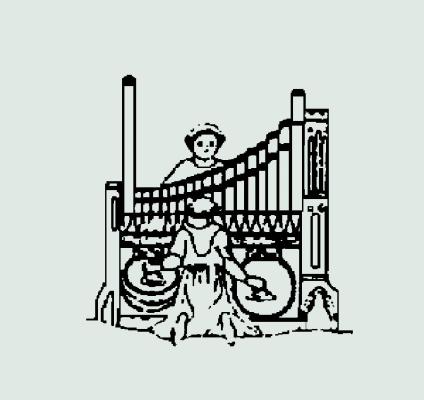
Anabel Taylor Chapel
Cornell University Baroque Organ
Ithaca, New York
GOArt / Parsons / Lowe
Selection
In 2003 Cornell University began planning for a new Baroque organ that would complement the existing Aeolian-Skinner organ in Sage Chapel (Opus 1009 III/68, 1940), as well as other smaller instruments located on campus. The decision was made to place the new instrument in an enlarged rear gallery, constructed with heavy timbers, in the intimate acoustic of Anabel Taylor Chapel. The new Baroque organ would be built by the Gothenburg Organ Art Center (GOArt), part of Gothenburg University in Gothenburg, Sweden, under the primary leadership of researcher and organbuilder Munetaka Yokota. This would not merely be an organ in “Baroque style,” but as much as possible, a reconstruction of an organ that could have been built in the late 17th or early 18th centuries by the German builder Arp Schnitger. The organ that Schnitger built in 1706 for the Charlottenburg Schlosskapelle (Palace Chapel) in Berlin was used as the primary model. This instrument is unique in that it blends the usual characteristics of Schnitger’s instruments built for the area around Hamburg (northwest Germany and the Netherlands), and characteristics of instruments in eastern and central Germany similar to what Johann Sebastian Bach would have known. It was also a sizable instrument for the Palace Chapel in which it stood.
The Charlottenburg organ was unfortunately destroyed during World War II, but there are recordings of the organ in addition to several photographs and documentation data, which allowed GOArt to use the original organ as a model. Because the Charlottenburg organ was confined in an unusual space, it was decided to follow a different model for the case design. The organ built by Schnitger in 1702 for the church of St. Salvator in Clausthal-Zellerfeld was chosen as a model for the case. Although its mechanism has been replaced several times since, the original Schnitger case is still in existence.
During the planning for this project, it was also decided to research how Schnitger built instruments in a city that was some distance from his home in Hamburg. This prompted GOArt and Cornell to enlist cabinetmaker Christopher Lowe of Freeville, New York, and Parsons Pipe Organ Builders of Canandaigua, New York, as local collaborators on the project. GOArt would design the organ, make the pipes, and build the keyboards, pedalboard, music rack, and bench, and provide all of the blacksmith work. Chris Lowe would construct the case, moldings, and balcony structure, and Parsons would build all of the internal mechanism: bellows, foot pumping mechanism, wind trunks, sperrventile, tremulant, key action, stop action, and windchests. The Parsons firm, Chris Lowe, and Munetaka Yokota would all work together to install the completed organ once the organ was set up and tested at Parsons’ Canandaigua workshop.
Parsons’ participation
Each new project brings its own set of challenges, and when a project involves three primary collaborators working for a university that demands perfection, those challenges could become overwhelming. However, working carefully through each new challenge, the final result speaks for itself as to the dedication to quality brought by each party.
One of the first challenges that we were presented with was the process of communicating design drawings. The design team in Gothenburg created a 3D CAD model of the organ. This model could be imported to our own 3D software, enabling us to measure components and create our own supplemental technical drawings. Three-dimensional computer modeling provides us with a greater sense of how all of the components relate to each other, allowing us to look at any combination of components and to rotate the computer model, and examine it from many angles. This was especially useful during this project, as this construction style was new to our staff and different from that to which we were accustomed.
Although the communication of CAD files across platforms provided challenges, other modern forms of communication were invaluable to this project, and are something that we guess Schnitger might have appreciated if it had been available to him. The use of Internet video conferencing allowed us to demonstrate and ask questions about specific shop techniques while allowing us to watch as Munetaka addressed these questions through demonstration, sketches, and gestures. These calls became daily occurrences during the latter part of the project and were crucial to its success.
This project was to be a “Process Reconstruction”—a term coined by the GOArt research team to describe the method used to discover unknown construction techniques, through the process of actually building the organ, rather than just through scholarly discussion. In other words, sometimes we cannot know the specific process or the correct way of building a component until we have experimented. In the end, this required us to learn many new skills and gave us an appreciation for the process that we may not have otherwise known.
The use of woodworking techniques consistent with the period was essential for the project’s success. We were permitted to use power equipment to mill lumber and cut it to size, but the final surface needed to show the traces of hand planing and scraping. As modern woodworkers, we are more likely to reach for our router or palm sander than for our hand plane. The necessity of using hand planes and scrapers in this project has re-trained us to reach for those tools and complete the task at hand before we could have gotten the router set up. The organ is made entirely of quarter-sawn white oak. This construction style relies heavily on joinery, some nails, and some glue. Long nails, ranging in length from 4 to 5 inches, were hand-forged by a blacksmith in Sweden, along with all the other ironwork required for the key and stop action, the bellows pumping mechanism, and the casework hinges and locks. Leather was provided by a German supplier, using period tanning techniques.
The key and stop actions are made in a manner consistent with Arp Schnitger’s practice. The key action rollers are made of white oak. Key action squares are made of iron and were supplied by GOArt. Most trackers and stickers are made of white oak, and the ends are hand wrapped with twine for strength. All metal trackers are of brass wire, and all trackers and stickers have hand-bent brass wire ends inserted. The key action is suspended, which means that the keys pivot at the tail and hang from the trackers or rest on the stickers from the chest. The Manual key action travels up from the key to the rollerboard, which is nailed to the back frame of the organ. The Rucwerk keyboard pushes stickers that carry the action to a rollerboard, which is located under the organist. The Pedal key action also relies on stickers that transfer motion to a rollerbox, which carries the motion, via trackers rather than rollers, to the Pedal chests on either side of the organ.
The stop knobs are made of pear that has been dyed black, with a bone button in the center. The stop action traces and trundles are made of white oak, with iron arms and levers. The iron arms are heated red-hot and then pounded into the oak trundles and are secured by quickly peening the iron.
The organ is winded from four large wedge bellows located in an isolated room in the tower of Anabel Taylor Chapel, approximately 30 feet above and behind the organ. The bellows can be foot pumped, or an electric blower can be used for practice without an assistant. Solid oak windlines connect these bellows to the organ. Windlines are joined with splines or inserted with tenons, and all joints are sealed with leather. A single Schnitger-style tremulant affects the entire organ.
Five windchests are located throughout the organ. The Manual and Pedal each have two chests, and the Rucwerk has one. All of the chests are built of solid quarter-sawn white oak. Given the wide humidity swings common to New York State, leather slider seals are used to eliminate runs and provide consistent wind to the pipes through changing climatic conditions. This required that each individual toeboard be carefully shimmed to allow the sliders to move with the correct freedom.
Casework
The casework was made by Christopher Lowe and Peter DeBoer in Chris’s workshop outside of Ithaca, New York. As the parts were made over an eleven-month period, they were assembled in a nearby barn. The case is made almost entirely of quarter-sawn white oak, mostly domestic. The oak in the long pedal tower frames and the thick posts at the console sides was imported from Germany. The rear panels are made of unfinished pine. Traditional joints hold the frame together: dovetails, splines, and pegged mortise and tenon. The panels are held together with clenched wrought-iron nails and have hand-forged iron hinges where access is needed for tuning. The molding profiles taken from the Schnitger organ in Clausthal-Zellerfeld were smoothed with an array of old wooden molding planes and custom-made planes and scrapers.
When Chris asked for guidance on what the finished surface of the moldings should be like, Munetaka responded, “We want to see the tool marks . . .
but they have to be nice tool marks.” The insides of the panels are finished with an extra deeply scooped texture for its acoustic property. All the oak has been fumed with ammonia to darken it, and the exterior surfaces were rubbed with linseed oil with iron-oxide pigment. The pipe shades are of basswood scroll-sawn to leafy shapes, and were painted by Joel Speerstra and his mother, Karen, with shadows and details to appear three-dimensional.
The casework was dismantled from the barn and moved to our Canandaigua workshop in November 2008. The interior components were installed over the next year, and the entire organ was enclosed in a tent and fumed with ammonia. Following this process, three wooden stops were installed for testing, and the organ was featured in an open house event at our facility on January 10, 2010.
Installation
Installation of the organ began in February 2010. This process required more on-site construction than to what we are accustomed. Because the pipes were shipped directly to Cornell University, the racking process had to be completed on-site. This required burning the rack holes to the correct size, for each pipe, in a tent outside the chapel in the frigid February air. The various tapered irons were carefully heated in a hand-crank coal forge; monitoring the exact temperature of the irons was critical to the process. Once ready, the irons were used to enlarge the holes by burning the wood until the pipes fit correctly. All of the upper racking was performed on-site, with the façade pipes being carefully carried up the scaffold to be marked for the precise location of the hook. Once soldered, a pin was located and driven into the oak rack.
All of the pipes that are offset from the main chests are conducted with lead tubes that were individually mitered, soldered, and fit on-site, and forced into leathered holes in the toeboards.
Pipework
The majority of the pipes in the organ are combinations of lead and tin. The wooden stops are made of pine. The pipe metal was cast on sand, as it would have been in Schnitger’s time. This technique was “rediscovered” by GOArt as part of their original research project in Gothenburg. In contrast, the modern method of casting thick metal sheets and then planing metal to the desired thickness by machine, produces a weaker material because it removes the hardest metal from the outer surface.
As Munetaka Yokota notes,
If the handcraft worker has to do everything by hand, then she or he will have the incentive of casting it as close as possible to the desired thickness and with the desired taper, and scraping it minimally, but very carefully, in the areas where it must be scraped well for acoustical reasons. This much more complex process works with the metal to create a sheet that gives a structural and acoustic result that, almost as a byproduct of the process, is as close as possible to the original Schnitger pipes. . . . Process reconstruction was developed with the goal of reproducing the acoustical quality of the 17th-century organ pipes, and this . . . philosophy is applied to the rest of the organ production as much as possible.
Final product
The organ was publicly presented during the Organ Inauguration and Dedication Festival and Conference, March 10–13, 2011 on the Cornell University campus. Many lectures were presented detailing the world that existed when the original organ at Berlin’s Schlosskapelle was introduced in 1706. There were demonstrations of the organ’s individual stops and a discussion about the construction process, and numerous concerts to demonstrate the organ as a solo instrument as well as how it worked together with other instruments. The inaugural concert by Harald Vogel was presented twice to allow more people to experience the new instrument in the intimate space of Anabel Taylor Chapel. The first inaugural concert also featured the new composition Anacrusis by Kevin Ernste. This piece featured the organ with electronic sounds as well as live organbuilding sounds made by numerous students and organbuilders who had worked on the instrument.
We would like to thank Professor Annette Richards, University Organist, who was the impetus behind this project and the glue that held it all together. Professor David Yearsley also provided welcome support and encouragement throughout the project. The support of Jacques van Oortmerssen, who served as inspector for Cornell during the project, was crucial to its success, and his performance during the festival was a tribute to his contributions.
The artistic endeavor of building the organ now gives way to the artistic endeavor of using it to teach and to enrich the lives of people for generations to come. For Parsons Pipe Organ Builders, there is a single underlying purpose to creating these beautiful instruments: that this organ will be used by Cornell students to glorify God through weekly services of worship.
—Parsons Pipe Organ Builders
4820 Bristol Valley Road
Canandaigua, NY 14424-8125
888/229-4820
www.parsonsorgans.com
To view a descriptive video produced by Cornell University, visit <http://www.cornell.edu/video/index.cfm?VideoID=1017>.
Parsons’ staff:
Richard Parsons
Calvin Parsons
Duane Prill
Peter Geise
Aaron Feidner
David Bellows
Glenn Feidner
Graham Sleeman
Jay Slover
Matthew Parsons
Steven Martindale
Tony Martino
Photo credit: Timothy Parsons, unless otherwise indicated
Anabel Taylor Chapel
Cornell University Baroque Organ
Ithaca, New York
GOArt / Parsons / Lowe
MANVAL (II)
1 PRINCIPAL 8 fus
2 QVINTADENA 16 fus
3 FLOITE DVES 8 fus
4 GEDACT 8 fus
5 OCTAV 4 fus
6 VIOL DE GAMB 4 fus
7 SPITZFLÖIT 4 fus
8 NASSAT 3 fus
9 SVPER OCTAV 2 fus
10 MIXTVR 4 fach
11 TROMMET 8 fus
12 VOX HVMANA 8 fus
RVCWERK (I)
1 PRINCIPAL 8 fus
2 GEDACT LIEBLICH 8 fus
3 OCTAV 4 fus
4 FLÖITE DVES 4 fus
5 OCTAV 2 fus
6 WALTFLÖIT 2 fus
7 SEPQVIALT 2 fach
8 SCHARF 3 fach
9 HOBOY 8 fus
PEDAL
1 PRINCIPAL 16 fus
2 OCTAV 8 fus
3 OCTAV 4 fus
4 NACHT HORN 2 fus
5 RAVSCHPFEIFE 2 fach
6 MIPTVR 4 fach
7 POSAVNEN 16 fus
8 TROMMET 8 fus
9 TROMMET 4 fus
10 CORNET 2 fus
(preparation)
TREMVLANT
VENTIEL MANVAL
VENTIEL RVCWERK
VENTIEL PEDAL
CALCANT
Four wedge bellows
Pitch: a1 = 415 Hz
Compass: Manuals C, D–d3
Pedal C, D–d1
Temperament: Werckmeister III
The stop names are presented as on the stop labels. Note that the “x” has been replaced by a “p” in both the Rucwerk Sepquialt and Pedal Miptur, possibly as a nod to the division names Rückpositiv and Pedal.
30 stops, 40 ranks, with one preparation.