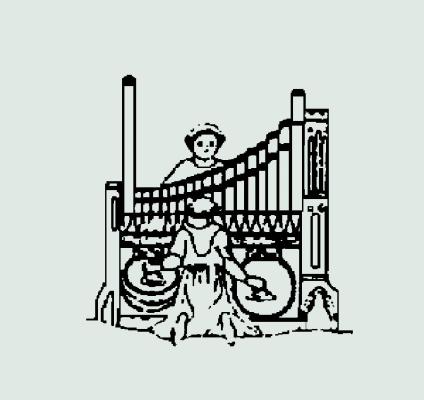
Milnar Organ Company,
Eagleville, Tennessee
Cal Turner, Jr. Residence,
Franklin, Tennessee
I recall the winter morning in January 2006 when I received a call that would begin one of the most noteworthy experiences in my career. At the time, we were giving some assistance to the Schoenstein Organ Company with their installation of a new organ in the Laura Turner Concert Hall in the new Schermerhorn Symphony Center in Nashville. The caller that January day three years ago was Cal Turner, Jr., whose support of the fine arts was well known, including his contributions to the Schermerhorn concert hall named in his mother’s honor.
Mr. Turner asked if we could build a pipe organ for his new home that was well under construction. The home site is on the tallest hill in Franklin, Tennessee, about one half hour from our shop. Soon after that call, my eldest son Derek and I met with Mr. Turner and the architect, Brad Norris, to explore the possibility of building a new organ for the multi-leveled great room.
Our most limiting factor was space. The super-structure of this room was made up of very large wooden beams. Two of these beams supported the staircase landing on the second floor. They were about eight feet apart, and projected about four feet into the room, a perfect spot for the main Great division. We wanted to keep the profile of the Great windchest and case as low as possible. Using a schwimmer helped, but there was no room for a blower of adequate size. The .75hp Ventus blower located in the Swell was more than adequate for the entire organ. We had the contractor cut a trough in one of the support beams for our air line and cables. The wood and cast iron railing behind the main Great organ, in the walkway, was made removable for tuning and servicing.
To the left of where the main Great division would be was a room that was planned as a large closet. With some redesigning and a little give and take, it became our tight Swell chamber. Between the two main chests we built our walkboard in three removable sections. This gave us access to all the windchests for service. Special low-heat lighting in the ceiling keeps the temperature down while tuning. Temperature and humidity control is exceptional in the home, and it keeps the organ in very good tune.
The inside walls were well insulated, which kept the Swell sound egress confined to the shades. We constructed the Swell shades of oak and stained them to match the beams in the room. To keep the shades from being so noticeable, we placed the Great 8′ Erzähler and 4′ Koppel Flute in front. Because of the space restriction, it was necessary to place the low pipes of the 16′ Bourdon on the outside of the Swell chamber in an open hallway over the sitting room. There were no wall obstructions, so with a little higher wind pressure, the bass pipes fill their need. Above the great room is a small observation room that looks over the county; it is accessible by a staircase or elevator. During the installation of the organ, some of our men witnessed a large crane lifting the roof off the observation tower, place one of the home’s three Bösendorfer grand pianos in the room, and replace the roof.
Below the great room is a large, ornately decorated oriental-styled theater modeled after a traditional Chinese Siheyuan or courtyard. The lowest level has parking for many cars and an interior full-sized car wash. The walls are painted with characters from Mrs. Margaret Turner’s book I the Fly, by Denas Davis, the original illustrator of her children’s book. The area is so well appointed, it serves as a banquet room as well.
From the console on the main floor, while you are surrounded by the majestic hand-hewn timber structure of the living room, you can look through one of the numerous kitchens and see the indoor water park equipped with waterfalls and several water slides. Working in this unique 23,600 sq. ft. home was almost surreal.
For a modest-sized organ, as one can see by the stoplist, it can successfully play a variety of organ literature. The organ was built primarily for entertainment, but quite a bit of classical music has been recorded on the instrument. With the use of the chimes and a MIDI module, a lot of interesting and amusing music is heard, especially when Cal Turner is performing for his grandchildren. We all enjoyed building this instrument for this very fine, generous, good man.
Cal Turner, Jr. received his B.A., cum laude, from Vanderbilt University in 1962. Following his graduation from Vanderbilt, Mr. Turner served for more than three years as an officer in the United States Navy. In December 1965, he began his career at Dollar General, the company founded by his father and grandfather in 1939. He succeeded his father as president in 1977 and as chairman in 1988. At the time of his retirement in 2003, Dollar General had grown into a New York Stock Exchange retailer with more than 6,000 stores in 27 states and annual sales in excess of $6 billion.
Cal Turner, Jr. has served on the board of numerous civic and charitable organizations throughout Tennessee and Kentucky. He personally received the Presidential Award for Private Sector Initiatives from Ronald Reagan at a White House ceremony. I believe one of his greatest achievements was to learn to play the pipe organ from his mother, Laura Turner. Cal served many years as organist at the Methodist Church in Scottsville, Kentucky. Mr. Turner has joined the Nashville AGO and is planning a Christmas program for the chapter this year.
It’s not often an organ builder has the opportunity to build an organ for a modern mansion. Cal Turner, Jr. gave us a free hand in the visual and tonal design. His enthusiasm for the project was infectious to everyone in our shop. We will always be grateful to Mr. Turner for his faith in our firm and the great working relationship we shared.
The following people were involved in the building of this organ: Dennis Milnar, Derek Milnar, Jeffrey Milnar, Todd Milnar, Greg Milnar, Tim Murphy, Kevin McGrath, Chris Brent, Ryan Milnar, Chris Sias, and Melanie Duncan.
When the organ was completed I sent Mr. Turner the following letter and received his response, which follows my letter:
Dear Cal,
I was very pleased with the final results of the tonal finishing. By raising wind pressures and raising the volume of several sets of pipes we probably increased the volume of the organ by about 20 percent. The versatility was enhanced even more. The wind pressure in the Swell was increased from 3.5 to 4 inches w.c. The pipes reacted very well to the increase. The only stop that needed a little calming was the Harmonic Flute from middle C up. That’s where the stop goes harmonic and the attack was a little pronounced. Restricting the air at the toe slightly brought it back into good speech.
We further increased the volume of the 8′ Gedeckt by opening the toe hole, allowing more wind to enter the pipe. This gave a good foundation to the Swell, a better balance to the flute chorus, and added to the volume of the Pedal.
We also increased the volume of the 8′ Viola so it was dominant to the Great Erzähler with the shades open. We use this stop at 8′ and 4′pitches to tune the Swell division, and it works very well.
The last significant increase in volume in the Swell was to the 8′ Oboe. By raising the caps at the top of the resonator and raising the tuning wire on the reed tongue, it gave the Oboe much more tonal presence and volume. The increased fundamental sound gave the whole Swell division much more presence.
We raised the windchest in front of the swell shades to 3.6 inches w.c. This brought the Koppel Flute in good balance within the flute chorus, and an increased fullness to the Erzähler. We kept the main Great windchest at 3.0 inches w.c. because of its prominent location in the room; its volume is more than adequate. We actually brought about an octave of the 8′ Principal down a bit because it was overpowering. This balanced the principal chorus.
This is probably more information than you wanted to hear, but I am so pleased with the overall results of the instrument I wanted to share it with you.
Sincerely,
Dennis P. Milnar
GREAT
8′ Principal 61 pipes
8’ Rohr Flute 61 pipes
8′ Harmonic Flute (Sw)
1–12 from 8′ Gedeckt
8′ Erzähler 61 pipes
8′ Erzähler Celeste TC 49 pipes
4′ Octave 61 pipes
4′ Koppel Flute 61 pipes
2′ Principal (ext 8′ Princ) 24 pipes
11⁄3′ Mixture III 183 pipes
Chimes 21 bars
Swell to Great 16′
Swell to Great 8′
Swell to Great 4′
MIDI to Great
SWELL
8′ Gedeckt 61 pipes
8′ Viola 61 pipes
8′ Viola Celeste TC 49 pipes
4′ Harmonic Flute 61 pipes
4′ Violetta (ext) 12 pipes
22⁄3′ Nazard 61 pipes
2′ Piccolo (ext) 12 pipes
13⁄5′ Tierce TC 37 pipes
11⁄3′ Quint (ext)
8′ Oboe 61 pipes
Tremolo
Swell to Swell 4′
MIDI to Swell
PEDAL
16′ Gedeckt 12 pipes
8′ Principal (Gt)
8′ Rohr Flute (Gt)
8′ Gedeckt (Sw)
51⁄3′ Quint (Sw 8′ Gedeckt)
4′ Principal (Gt 8′ Principal)
4′ Chimney Flute (Gt 8′ Rohr Flute)
8′ Oboe (Sw)
4′ Oboe (Sw)
Great to Pedal
Swell to Pedal
MIDI to Pedal
The mahogany two-manual console includes:
mahogany pedalboard with rosewood sharps
keyboards with pearwood naturals and rosewood sharps
burlwood nameboard and drawknob jambs
mahogany adjustable bench
six rosewood coupler rockers
27 custom rosewood turned drawknob heads with engraved inserts
20 thumb pistons
six toe studs
adjustable fluorescent music rack and pedal light
General MIDI Module SD-20 with JBL Eon G2-15 self-powered speaker
ICS-4000 control system
Other features:
Peterson 16-stage shade machine
motor-driven tremolo
Great 8′ Principal and 4′ Octave of 75% polished tin
The center façade pipe is diamond faceted and signed by the pipe maker and dedicated to Mr. Turner.
Cover photo: Roger Wade Studio, Inc., Bigfork, Montana