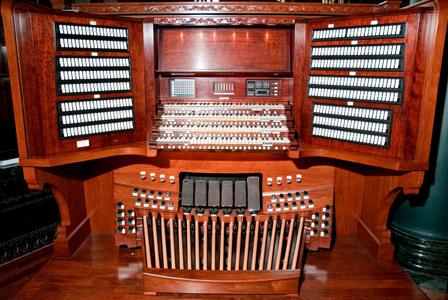
Solid State Organ Systems installed a new Capture for MultiSystem II in January at Longwood Gardens, Kennett Square, Pennsylvania. The CFM-II controls 353 stop-tablets, 70 pistons, and a custom Expression Matrix of 72 luminous stops. The CFM-II works with Organist Palette, where organists can access their own private library of memory and customize features such as Pedal Divide and the Advanced Sequencer. The project was managed by Richard Houghten, Inc., and specifications were made in conjunction with principal organist Peter Richard Conte. Also added during this update were the Organist Palette and Tuning for MultiSystem. This update comes as a successor to the SSOS Video MIDI Player installed in 2008.
SSOS has installed control systems around the world for over fifty years. MultiSystem II is the centerpiece of Solid State Organ Systems product line. A complete relay and switching system, MSII also provides the opportunity for their Capture for MultiSystem, Organist Palette, Record for MultiSystem, Tuning for MultiSystem, and the newly released Voicing for MultiSystem. The company has drawings, spares, upgrades, manuals, and backup for every system they have made. For information: 703/933-0024,
[email protected], or http://www.ssosystems.com/.