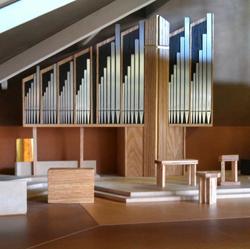
The J.F. Nordlie Company, pipe organ builders of Sioux Falls, South Dakota, announce that Mt. Calvary Lutheran Church in Eagan, Minnesota, has signed an agreement for design and construction of a new 29-rank, two-manual electro-pneumatic action organ.
The organ will be housed in a case of rift-sawn red oak located on the chancel platform. Completion of the instrument is scheduled for late summer of 2015.
For information: www.jfnordlie.com.