David Fienen is Emeritus Professor of Music at Gustavus Adolphus College, St. Peter, Minnesota. At Gustavus, he was Cantor at Christ Chapel, taught organ, music theory, chaired the music department, and served as provost and dean of the college his last two years before retirement.
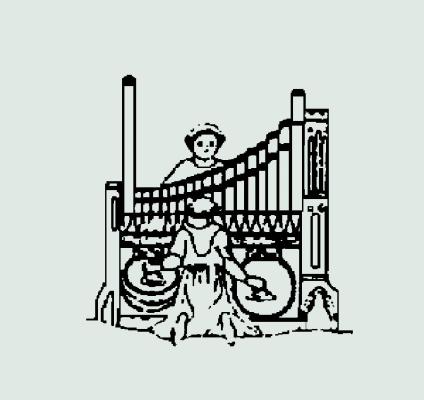
Sitting under a shade tree in his backyard last summer, sipping iced tea with Charles and Birgitta Hendrickson, I asked him about his philosophy of organ building. His immediate answer was, “If I can make them [the congregation] sing, I have succeeded.” To make them sing—what a fine goal!
First a physicist
Minnesota native Charles Hendrickson grew up in Willmar, Minnesota, where his father had a law practice. During Charles’s young years, his father, Roy, was also chair of the board of trustees at Gustavus Adolphus College (Roy’s alma mater) in St. Peter, Minnesota, from 1945–53. After Roy passed away in 1954, Charles’s mother, Frances, was hired as secretary to President Edgar Carlson at Gustavus from 1955–ca. 1967. Charles had already started his college career at Gustavus, and now the rest of his family moved to St. Peter. In 1957, Charles graduated from Gustavus with a Bachelor of Arts degree in physics and mathematics. It is interesting that he is not the only organbuilder with a physics background—Charles Fisk worked for Robert Oppenheimer on the Manhattan Project before he began building organs.
After college, Hendrickson started graduate studies at the University of Minnesota for one year, then taught physics at Superior State Teachers College (now University of Wisconsin-Superior, Superior, Wisconsin) for a year. He earned his Master of Science degree in physics at the University of Arkansas while also teaching for a year at Union University in Jackson, Tennessee (and serving as head of the department!). He also taught at Northeast State University in Oklahoma before returning to Minnesota to teach physics at Mankato State College (now Minnesota State University Mankato) for a couple of years.
In 1964, Charles married Birgitta Gillberg at Gamla Uppsala Church in Sweden. Birgitta, a native of Sweden, was teaching Swedish at Gustavus at that time. She continued teaching at Gustavus until Eric was born in 1967. She then returned to her academic career in 1975, teaching Swedish and German at Minnesota State University Mankato for 30 years until her retirement.
Hendrickson Organ Company: Beginnings
Hendrickson’s interest in the pipe organ began early in his young life, in 1953, when he watched with fascination as the Möller organ was rebuilt and reinstalled at Bethel Lutheran Church in Willmar. Harry Iverson, who was the Möller representative, supervised the regulation and work at the church, and Hendrickson got involved as a “gopher.” Iverson had previously been the Kimball representative and had designed the Minneapolis Auditorium Kimball organ. During graduate school, Hendrickson followed up on this early interest by working on organs (servicing, repairing, moving, tuning) on a part-time basis.
In 1964, Charles Hendrickson was asked to rebuild and significantly enlarge the 1910 Hillgreen-Lane organ in First Lutheran Church in Winthrop, Minnesota, by the pastor of the church, who was a family friend. Pastor Lambert Engwall had talked his congregation into undertaking the project to enlarge the organ in the church, had raised the money for the project, and convinced Hendrickson to tackle this project. As it was already part way through spring semester, Hendrickson resigned his teaching position at Mankato State and thus committed himself to being an organbuilder.
Several interesting things about this instrument, Opus 1, produced by the nascent Hendrickson Organ Company, are worth noting:
• The Swell division consists of pipes from the previous instrument, with new Hauptwerk, Positief, and Pedal divisions. The casework was mostly new to house the new organ.
• The Positief division was housed in its own case cantilevered on the balcony rail—in Rückpositiv position. This was the first Rückpositiv built in Minnesota.
• Hendrickson rented space in the empty Green Giant canning plant in Winthrop to build the organ with three helpers. (This is reminiscent of how older organ builders like Schnitger operated—building on site or at least in the vicinity of the church.)
• The new pipes added to this organ came from Organ Supply.
• Composer David N. Johnson, then on the faculty of St. Olaf College, played the dedication recital in September 1965.
• In 1982, Hendrickson added two mutations and swapped out two flute ranks, bringing the instrument to 36 ranks.
At about the same time, Hendrickson was asked by his home congregation, First Lutheran Church in St. Peter, Minnesota, to build a “temporary” organ for their new sanctuary then under construction to replace the church that had been destroyed by lightning on Mother’s Day in 1962. He readily complied by assembling a two-manual, eight-rank instrument, partly from salvaged materials. The outstanding acoustics of the building helped this small instrument to be amazingly successful, and it also included a horizontal trumpet! This temporary instrument, Opus 2, installed in 1965, remained in the church longer than expected. It was not replaced until his Opus 45 was completed in 1979, a two-manual, 44-rank instrument with a third coupler keyboard.
Opus 3 was another enlargement project, this time resulting in a two-manual, 30-rank instrument at Grace Lutheran Church, Mankato, Minnesota, using some ranks, offset chests, blower, and console from the previous two-manual, nine-rank M. P. Möller organ built for Grace Lutheran’s previous building. This instrument was also subsequently expanded in 1992 by adding a new Great division, horizontal trumpet, new three-manual console, and other tonal and mechanical revisions (Opus 86, three manuals, 41 ranks).
From these beginnings of the Hendrickson Organ Company in 1964, there followed several new instruments, including Opus 6, of two manuals, eight ranks, at St. John Lutheran Church in Yankton, South Dakota, and Opus 9, of two manuals, 24 ranks, at Blessed Sacrament Catholic Church in La Crosse, Wisconsin, plus more revisions, enlargements, and rebuilds, leading up to Opus 10 in 1970. Interestingly, the Yankton instrument, a larger version of Opus 2, came about because Harold Spitznagel was the architect of both First Lutheran Church in St. Peter (which housed Hendrickson Opus 2) and of St. John Lutheran Church in Yankton (Opus 6). The Yankton instrument originally contained only eight ranks, later enlarged to 12 after a fire in the church in 2009.
It is worthwhile to look further at the early influences on Hendrickson. He is largely a self-taught organbuilder, learning by experience, by voracious reading, and from the influences of Russ Johnson (an acoustician) and Robert Noehren (an organbuilder, performer, and teacher himself). Around the time Hendrickson was starting to build his Opus 1 and Opus 2, he met Robert Noehren at the Central Lutheran Organ Symposium in Minneapolis. From Noehren he became convinced to use primarily all-electric action when building electric-action instruments. And from Noehren, he learned the concepts of judicious borrowing and duplexing to retain clarity in the resulting organ while realizing some economies of budget and space. His Opus 1 at Winthrop used electro-pneumatic chests for the Great and Swell, but all-electric for the Positief. Subsequently, he primarily (though not exclusively) used all-electric chests when building non-mechanical-action instruments.
The Hendrickson factory
The year 1970 saw a new chapter unfold. Hendrickson was contacted by William Kuhlman, professor of organ, to build a new organ for Luther College in Decorah, Iowa. Most of his work prior to this time had been accomplished in his basement, garage, rented facilities, or on site. Now, in order to have a tall erecting room, he took the plunge, purchased land in the industrial park in St. Peter, and built the first part of his organ factory, including in the center a tall room where he could set up this two-story instrument. The organ for Luther College, Opus 10, of two manuals, 35 ranks, was his first mechanical-action instrument.
This organ was intended as a teaching, practice, and performance instrument, and was built on a movable platform like a hovercraft so it could move to a neighboring room. Subsequently, it was relocated to a permanent teaching studio on the campus, the floating mechanism disabled, and an electric-action, unified trumpet rank on the Great was reinstalled as an 8′ horizontal reed, playable from the mechanical action. Due to heavy use, the keyboards have been replaced twice on this instrument.
The original factory consisted of a tall central erecting room, with the office in the back as an upstairs room, and two flanking rooms for wood work, pipe set up, and voicing. The equipment included the voicing machine originally built by Vogelpohl & Spaeth in New Ulm, Minnesota, in the late 19th century. Over the years, a sizeable building was added behind the original shop, including an assembly room and new voicing room, with the earlier flanking rooms repurposed. Later still, another former business building was moved to adjoin the addition, becoming the office, drafting studio, and library storage for the extensive collection of books and organ journals kept close at hand. (Hendrickson has every issue of The Diapason since 1913, and of The American Organist since 1929!) A large warehouse was added next door for much-needed storage and to house the spray booth. Interestingly, after a tornado struck in 1998, both this author and the Gustavus chaplain rented space in the warehouse to store all of our furniture while our houses were being rebuilt. More recently, a disastrous fire in November 2013 engulfed the original shop building. (Andreas Hendrickson, Charles’s younger son, designed a replacement shop building, which has been recently completed.) Fortunately, the added buildings were separated enough that they were not damaged, and no organs were destroyed except for some wood pipes, machinery, and some supplies.
With Opus 10 for Luther College, Hendrickson began building mechanical-action instruments, either with mechanical stop action or electric stop action. A significant portion of the organs built by the firm feature mechanical action. When asked, Hendrickson expressed his preference for this type of action “just because I like it.” He also indicated he felt such instruments are “very satisfying” and provide the “best possible solution.” But Hendrickson indicated that throughout his career, he particularly wanted to “satisfy a need.” This is a most salient point—he set out to provide a good musical instrument for a wide variety of situations, large and small, and while his preference would be a tracker organ, sometimes placement, finances, or other considerations necessitated using electric action. If that were the case, he set out to make it the best it could be. Not infrequently, his project working with a church to improve their musical resources would also involve redesigning either the chancel or the balcony to facilitate placement of the new instrument and the location of the choir and/or the liturgical appointments.
During the half-century so far of the Hendrickson Organ Company, the firm has been involved in a wide variety of organ projects, building large and very small instruments, restoring, rebuilding, and expanding both historic instruments and some of their own, adding single divisions and/or replacing consoles—a variety of, as Charles said, “solving problems” for particular situations and congregations. To comment on each of the many projects (opus numbers) undertaken by the Hendrickson Organ Company would occupy far more space than is possible here; instead, a summary is presented, featuring a few interesting examples.
Mechanical-action instruments
There are 27 mechanical-action organs on the Hendrickson opus list, ranging from a practice instrument with one 8′ flute for each of two manuals and pedal (Opus 33) to his largest instrument at Wayzata Community Church in Wayzata, Minnesota (Opus 92, four manuals, 70 ranks). The Wayzata instrument is unusual in that it incorporates a large Paul Granlund bronze sculpture in the middle of the façade.
Other sizable mechanical-action organs include Opus 47, a three-manual, 43-rank organ in St. Wenceslaus Catholic Church, New Prague, Minnesota, and Opus 35, a three-manual, 59-rank instrument at Sts. Peter and Paul Catholic Church, Mankato, Minnesota. These large instruments have mechanical key and stop action. The New Prague instrument leans toward a French Classic style, though not exclusively. The later Opus 78, of three manuals, 62 ranks, at St. Joseph Cathedral in Sioux Falls, South Dakota, utilizes a multi-channel electric stop action. It was also an instrument of a more complex design because of its size and the necessity for a detached keydesk. Hendrickson also had to redesign the gallery choir risers to accommodate the new organ. All three of these instruments were placed in rear balconies, and the Mankato and New Prague installations feature Rückpositiv divisions.
While most of Hendrickson’s two-manual mechanical-action instruments contain between 12 and 29 ranks, the largest is Opus 45, a two-manual, 44-rank instrument completed in 1979 at Hendrickson’s own church, First Lutheran Church, St. Peter, Minnesota. This instrument finally replaced the “temporary” Opus 2 that he had built nearly 15 years earlier. The organ features a horizontal trumpet on the Great (as had Opus 2) but also includes a trumpet within the case for that division. For this instrument, Hendrickson used a chassis from Laukhuff, Pedal division façade pipes made of aluminum, and a third manual as a coupler manual. This instrument is housed in an excellent acoustical environment and is a particularly successful installation. Marie-Claire Alain examined the organ upon completion and played the dedication recital.
In addition to these full-size tracker organs, the company built five portative organs consisting of one manual (no pedal) with 8′ flute, 4′ flute, and 2′ principal stops. The first such instrument was built for the St. Olaf Choir (Opus 16) and was intended to be able to be transported in a regular coach bus (with a couple of seats removed). To fit that size, the instrument has a short octave in the bass (lacking C#, D#, F#, and G#) and the compass is an octave shorter in the treble than a normal 61-note compass. In addition, the keyboard folds down inside the case, thus fitting through a bus door (at least back in the early 1970s). The stops are divided between bass and treble. The blower is also enclosed in the case, which is mounted on casters and has handles for ease in lifting and moving it around. After a second version was ordered by the Rockford Kantorei in Rockford, Illinois (Opus 18), three more instruments were built—“for every board we cut, we cut three.” These instruments eventually found their way to the University of Wisconsin in River Falls, Wisconsin (Opus 30), Concordia College in Moorhead, Minnesota (Opus 81), and Gustavus Adolphus College in St. Peter, Minnesota (Opus 72a). The organs are principally used for continuo playing.
Electric-action instruments
The Hendrickson opus list includes nearly 60 electric-action instruments. Thirty of these projects involved organs with fewer than 20 ranks, most incorporating at least some borrowing or duplexing, using the ideas Hendrickson had acquired from Robert Noehren. Many of these instruments use all-electric chests, as mentioned above. However, for Opus 60, a two-manual, 19-rank organ built for First Lutheran Church in Glencoe, Minnesota, the builder used slider chests with electric pull-downs. The largest two-manual electric-action instrument is Opus 25, of two manuals, 38 ranks, installed in First Lutheran Church, St. James, Minnesota (another instrument with a horizontal trumpet).
A dozen three-manual instruments (and one four-manual) contain 30 to 54 ranks. Beginning with Opus 1 (three manuals, 34 ranks), the list includes many significant enlargements of instruments by Möller, Aeolian-Skinner, Austin, Hillgreen-Lane, and Schantz, the largest being the expansion of a 1961 Schlicker (three manuals, 32 ranks) as Hendrickson Opus 100 (three manuals, 54 ranks) for Our Savior’s Lutheran Church, Sioux Falls, South Dakota. Two notable large all-new instruments are Opus 51 (three manuals, 46 ranks) at St. Mark Catholic Church in St. Paul, Minnesota, and Opus 34 (three manuals, 51 ranks) at St. John’s Lutheran in Owatonna, Minnesota (yet another organ with a dramatic horizontal trumpet). The Owatonna instrument also uses pallet and slider chests with electric pulldowns.
What is clear from all these instruments is that Charles Hendrickson and the many workers over the years in the shop were interested in creating or improving musical instruments that would “make them sing,” whether in the big city or the small country church. Hendrickson always endeavored to learn from the past, from his own experience, and from the lessons the industry had learned, whether from books or from his colleagues in the business. He was not interested in modeling after a particular style or a particular period, nor was he dogmatic about actions or particular stops, but was focused on a clear, singing tone and satisfying the particular needs of a group of people assembled in a specific congregation.
Rebuilds, restorations, and
renovations of 19th– and early 20th-century organs
The company website (www.hendricksonorgan.com) lists over 116 opus numbers. They include more than two dozen rebuilds, renovations, and restorations, notably:
• Rebuilding and enlarging the 1862 Marklove organ in the Cathedral of Our Merciful Savior in Faribault, Minnesota (Opus 70, two manuals, 34 ranks), using many of the original pipes—possibly the oldest pipes in Minnesota;
• Rebuilding two other late 19th-century organs, one by Hutchings, Plaisted & Co. (Opus 40, two manuals, 21 ranks), and the 1896 Kimball tubular pneumatic instrument located in the Union Sunday School in Clermont, Iowa (Opus 51a, two manuals, 27 ranks). The latter is the largest remaining tubular-pneumatic Kimball in original condition;
• Restoring, rebuilding, or revising several early 20th-century instruments by Hinners, Hillgreen-Lane, Kimball, Estey, and Vogelpohl & Spaeth (a late 19th/early 20th-century Minnesota builder);
• Maintaining, revising, and renovating the large four-manual, 52-rank Hillgreen-Lane organ in Christ Chapel at Gustavus Adolphus College in St. Peter, Minnesota, especially after the 1998 tornado severely damaged the entire campus and community. Organ repairs included cleaning all reeds, re-racking pipes, building a new Great chest, and replacing the keyboards;
• Rescuing Hendrickson Opus 53 (two manuals, 27 ranks) that was housed in St. Peter Catholic Church, which was destroyed by the same tornado. This mechanical-action organ was later used as part of the much larger instrument (Opus 99, three manuals, 40 ranks) designed by Andreas Hendrickson for the new church;
• Rebuilding and moving a much-altered 1931 Aeolian-Skinner (Opus 877) to a church in Arkansas in 1990 (Opus 88, three manuals, 30 ranks), then, after that church had closed, moving the instrument and reinstalling it at Celebration Lutheran Church in Sartell, Minnesota, in 2009 (Opus 115, three manuals, 35 ranks).
Hendrickson as author
From his beginnings in academe, Hendrickson never lost his inquisitive mind or his desire to share what he had learned. An active member of the Associated Pipe Organ Builders of America (APOBA) and the American Institute of Organbuilders, he served as president of APOBA for about 8 years. During that time, he arranged for the organization to commence sponsoring Pipedreams on American Public Media and oversaw the statement APOBA produced regarding “sampled voices” in pipe organs.
A large undertaking by Hendrickson was a long series of articles he wrote, mainly for The American Organist. These included articles on families of tone, divisions of the organ, tonal architecture, pipe materials, and a host of other relevant topics. The Hendrickson Organ Company website lists and links to 46 of these articles written between 1976 and 2003. [http://www.enchamade.com/hendricksonorgan/wb/pages/articles.php]
More recently, Hendrickson returned to his physics roots by collaborating on a research project with Dr. Tom Huber and some of his students at Gustavus Adolphus College. A summary of their study, “Vibrational Modes of an Organ Reed Pipe,” can be accessed at http://physics.gac.edu/~Huber/organs/vibrometer/ and an abstract of Huber’s Faculty Shop Talk about the project can be found at https://gustavus.edu/events/shoptalks/Shop0304.htm.
The future
Charles Hendrickson has retired from active involvement in the work of the Hendrickson Organ Company. The enterprise continues under the leadership of his two sons, Andreas and Eric. Andreas, who holds an architecture degree from the University of Minnesota, is in charge of design, while his older brother, Eric, is head of installations, tuning, and service. Andreas also called on his architecture background to design the rebuilding of the portion of the shop lost to the November 2013 fire. The company services many of their own instruments, plus numerous other instruments around Minnesota and neighboring states. The brothers grew up in the organ factory and learned many of their skills from their father. Thus a new generation is continuing the process of building, rebuilding, and repairing pipe organs in this small town in southern Minnesota. ν
References
Bies, Jessica. “PORTRAITS: Sons of St. Peter pipe organ maker continue Hendrickson legacy,” St. Peter Herald, March 27, 2014. www.southernminn.com/st_peter_herald/news/article_bb355bf8-3aea-55a2-b9…
Hendrickson Organ Company website: http://hendricksonorgan.com
Huber, Tom, Brian Collins, Charles Hendrickson, and Mario Pineda. “Vibrational Modes of an Organ Reed Pipe.” Presentation for Acoustical Society of America Meeting, November 2003. http://physics.gustavus.edu/~huber/organs/
Interviews with Charles Hendrickson in June and July, 2016, plus several phone conversations.
Organ Historical Society Pipe Organ Database: database.organsociety.org
TCAGO Pipe Organ List: http://www.pipeorganlist.com/OrganList/index.html
Vance, Daniel. “Hendrickson Organ Company.” Connect Business Magazine, July 1999, Mankato, Minnesota. http://connectbiz.com/1999/07/hendrickson-organ-company/