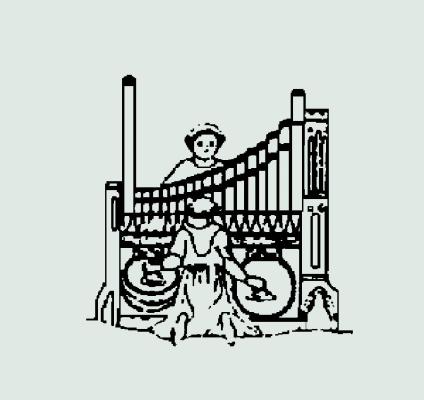
Andover Organ Company,
Methuen, Massachusetts,
Opus 117, 2009
Peter Griffin residence,
Harpswell, Maine
In February 2009, Andover Organ Company completed Opus 117, a residence organ for Peter Griffin of Harpswell, Maine. The organ is an expanded version of our ELM model practice/teaching instrument. It features our three-stop mechanical unit Pedal that begins with stopped wood pipes and changes to open metal, with the voicing gradually ranging from a flute in the bass to a principal sound in the 4′ range.
The casework is solid cherry, with case pipes of polished tin. The keyboards have bone naturals and ebony sharps. The drawknobs are pau ferro, with engraved inserts. The key action and stop action are mechanical. The visual design is by Don Olson, the mechanical design by Michael Eaton, and the tonal design and finishing by John Morlock. Ben Mague was the team leader, with Al Hosman, David Zarges, and David Michaud responsible for casework, windchests, and wind system. The tonal crew consisted of Don Glover, Jonathan Ross, and Fay Morlock. Mr. Griffin is a retired businessman and organ aficionado. He studies organ with Ray Cornils, Portland’s municipal organist.
—Don Olson
photo credit: Ben Mague
2 manuals, 13 stops, 12 ranks
MANUAL I
8′ Chimney Flute 58 pipes
4′ Principal 58 pipes
2′ Fifteenth 58 pipes
II Mixture 116 pipes
MANUAL II
8′ St. Diapason 58 pipes
4′ Flute 58 pipes
22⁄3′ Nazard 58 pipes
2′ Principal 58 pipes
13⁄5′ Tierce 58 pipes
8′ Hautboy 58 pipes
PEDAL
16′ Subbass 30 pipes
8′ Flutebass 12 pipes
4′ Chorale 12 pipes
Couplers
Manual II to Manual I
Manual I to Pedal
Manual II to Pedal