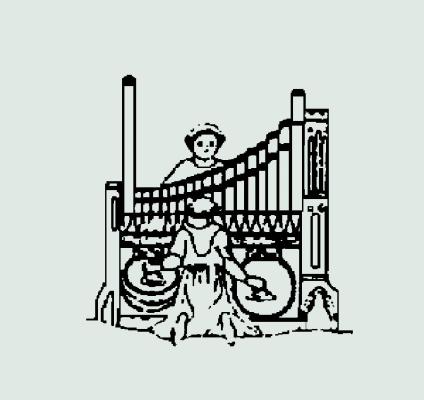
Andover Organ Company, Methuen, Massachusetts, Opus 115
Church of the Nativity,
Raleigh, North Carolina
It was a bright Sunday morning in Raleigh, North Carolina, when a North American moving van pulled into the parking lot of Church of the Nativity. Soon parishioners began to arrive to attend the morning service. Shortly after the service ended, a potluck lunch was served—a sumptuous feast that was to repeat itself in the days to come. Once the lunch dishes were cleaned up and the food put away, Mother Diane Corlett, Rector of Nativity, approached the moving van and with much fanfare received the first piece of Nativity’s new Andover organ. She processed into the sanctuary. Parishioners of all ages followed, each taking parts of the organ and depositing them in the sanctuary under the supervision of the Andover crew. After only an hour, the van was completely unloaded and the sanctuary was filled with hundreds of organ parts. The organ had arrived.
The following week and a half saw the organ being assembled in the front of the sanctuary. Team leader Matthew Bellocchio and his crew, consisting of David Zarges, Tony Miscio and Craig Seaman, completed the mechanical installation and traveled back to Lawrence. Two weeks later, tonal director John Morlock and voicer Don Glover arrived to begin the tonal finishing, which was completed in two weeks.
This instrument has tracker key and stop action. The case is made from solid red oak and is stained to match the woodwork of the church. The case pipes are made of 70% polished tin. The keyboards are covered with cow bone naturals and ebony sharps, and the drawknobs are made of pau ferro with faux ivory labels. The solid walnut pipe shades were designed and carved by Tony Miscio of the Andover staff. The organ has a Zimbelstern and a revolving star. It is a fitting addition for Church of the Nativity.
The dedication of the organ was on Friday, November 16, 2007, with Brian Jones, organist, playing works by Lefébure-Wély, Bach, Reinken, Sweelinck, Arne, White, Schumann, Rawsthorne and Saint-Saëns. Jones was joined by the Nativity Choir directed by Waltye Rasulala in When in Our Music God Is Glorified and the Nativity Bell Choir directed by Ruth Brown in Beethoven’s Hymn to Joy. The audience joined in singing hymns “Come, Ye Thankful People Come” and “Ye Watchers and Ye Holy One” with descants by the choir.
Church of the Nativity is a small, but very active and growing congregation and is known locally as Church of the Activity.
—Donald Olson
Andover Organ Company
Photo credit: Matthew Bellocchio
GREAT
8' Open Diapason 58 pipes
8' Chimney Flute 58 pipes
4' Principal 58 pipes
4' Flute prepared
2' Fifteenth 58 pipes
III Mixture 174 pipes
8' Trumpet prepared
Zimbelstern
SWELL
8' Stopped Diapason 58 pipes
8' Viola 46 pipes
8' Celeste prepared
4' Silver Flute 58 pipes
2-2/3' Nazard 58 pipes
2' Principal 58 pipes
1-3/5' Tierce prepared
8' Hautboy 58 pipes
Tremolo
PEDAL
16' Bourdon 32 pipes
8' Flutebass (ext) prepared
4' Chorale (ext) prepared
16' Trombone prepared
8' Tromba (ext) prepared
Couplers (by hitchdown pedals)
Swell to Great
Great to Pedal
Swell to Pedal
Milnar Organ Company
Eagleville, Tennessee
James Dorroh residence
When James Dorroh called and asked us to look into a two-manual, six-rank Wicks tracker organ, I knew we had an interesting experience ahead of us. Built in 1972 as a practice organ for Ohio Wesleyan University, the organ was in a private residence in the Minneapolis-St. Paul, Minnesota area. I asked our colleagues from the Obermeyer Organ Company to examine the organ and give us a report. By their assessment it was obvious the instrument had to come to our shop for repairs and modifications.
We were unaware that the Wicks Company even made tracker organs. A call to the company enlightened us that three tracker organs were built as practice organs for universities. They were gracious enough to supply us with a full set of blue prints for the entire organ. We agreed to take the project on.
There was an unusually warm spell in that part of the country in mid-December, which prompted us to send Kevin McGrath and my grandson, Christopher Brent, with our vans and trailers on the long journey from Middle Tennessee to Minneapolis. The trip was successful and we started setting up the organ in our shop on arrival. We mitered some pipes, rearranged some off chests, adjusted the actions, and rebuilt the casework to fit in Dr. Dorroh’s space. We adjusted the voicing once the organ was in its new home. Working with Dr. Dorroh was a pleasure, and made the project very successful.
—Dennis P. Milnar
Milnar Organ Company, LLC
Eagleville, TN 37060
<www.milnarorgan.com>
Manual I
8' Gedackt 56 pipes
2' Principal 56 pipes
Manual II
8' Quintadena 56 pipes
4' Rohrfloete 56 pipes
1-1/3' Gemshorn 56 pipes
Pedal
16' Subbass 32 pipes
Couplers
I/II
I/Pedal
II/Pedal