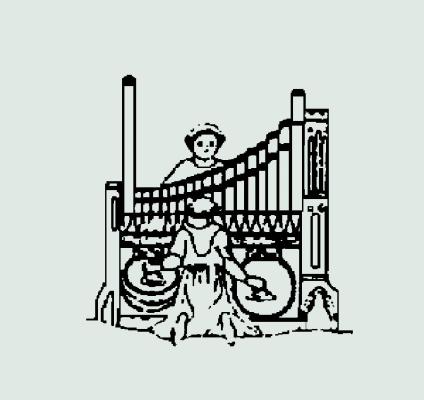
The Sweelinck Organ Project at St. Andrew’s Episcopal Church, Antelope, California
Named after the influential Netherlands composer, Jan Pieterszoon Sweelinck (1562–1621), this project centers on the creation of a pipe organ of a kind known in Northern Europe in the 17th century. Thus, it offers a glimpse into a musical world of the early Baroque period, with echoes of the Renaissance still clearly audible. Not a replica of any specific organ, the Sacramento Sweelinck Organ represents a synthesis of features common to many smaller instruments from this region and period.
Aside from its anticipated use as an instrument for performance practice study, the organ is played weekly in traditional church services at St. Andrew’s Episcopal Church in Antelope, California, in a deliberate attempt to test the feasibility of using such a highly focused instrument to support modern congregational worship, in this case using The Hymnal 1982 and Lift Every Voice and Sing II.
Research and design of the organ was carried out in 2004–2005 by Dr. Lee T. Lovallo, assistant professor at National University’s Sacramento campus and music director at St. Andrew’s. Construction was begun in late 2005 in collaboration with organbuilder Rick Simms and included help from a number of volunteers. Painting and gilding of the case doors in a traditional design was executed by Sacramento artist Theodore Sanders of National University. The calligraphy of the stop labels and the carving of the motto at the top of organ (“Singen wir aus Herzens Grunde”—“Let us sing from the depths of our hearts”) were executed by St. Andrew’s parishioner George Simpson.
The organ was dedicated on April 18, 2009 by Dr. David Rothe of California State University, Chico, in a recital that featured music from the Robertsbridge Codex through Sweelinck and early Bach. The organ features:
mechanical key and stop action;
hand-pumped, single-fold wedge-shaped bellows and low wind pressure (65 mm) without wind stabilizers;
visual design, including decorated case doors, typical of period instruments;
keyboards and pedalboard utilizing short octaves, period key dimensions and shapes, limited compasses (CDEF GA–c3), and an early-style shove coupler to connect the manuals;
tuning at high choir pitch (Chorton, A = 460) in ¼ comma meantone temperament;
construction materials chosen from locally available lumber, animal hides and glues, and recycled components from older instruments; and
construction techniques employing period joinery and period finishes.
—Lee T. Lovallo, Ph.D.
National University, Sacramento
HAUPTWERK
8′ Prinzipal
4′ Oktav
3′ Quint
2′ Oktav
Mixtur II
8′ Gedackt
8′ Spitzflöte
8′ Regal
8′ Schalmey
UNTERWERK
8′ Quintadena
4′ Prinzipal (TC)
2′ Blockflöte (TC)
8′ Krummhorn (TC)
PEDAL
16′ Subbaß
8′ Tromba
Accessories
Nachtigal, Zymbelstern, Tremulant, Calcant signal, Pedal pull-down to HW, intermanual shove coupler, hand-raised wind option
============================================================================
Parkey OrganBuilders,
Duluth, Georgia
St. Peter’s Episcopal Church,
Talladega, Alabama
In early 2008 we received a call from Jim Dorroh of Birmingham, Alabama, regarding the restoration of a 1904 Hook & Hastings tracker organ. Dr. Dorroh had been asked to serve as the consultant for the project. In our discussions, it was explained that the organ had suffered extensive water damage due to a storm-ravaged roof in the spring. We made the arrangements to meet with the committee from St. Peter’s, along with my shop supervisor, Michael Morris.
At our initial visit the organ was unplayable. The water had severely damaged both the Great and Swell chests, along with the felt and leather components in the action. Our firm and several other firms agreed that the only option was to completely remove the organ and restore the entire instrument. The organ was removed and shipped back to our location in Norcross, Georgia, in summer 2008. Once the organ was in our shop, we completely dismantled the rest of the windchests and components for further inspection. As originally suspected, the Great and Swell windchests were a total loss. The metal pipework survived well, though repairs to some of the wooden pipes were necessary.
The organ was originally installed in the First Baptist Church of Talladega in 1904, and subsequently was sold and moved to St. Peter’s in 1934. Though the church constructed a new building at that time, the provisions for space for the organ were not ideal. During reinstallation, part of the façade was installed in the chamber, and the organ sat recessed in its alcove. The organ had gone through some minor renovations in the 1980s. Sometime after that renovation, another builder removed the 8′ Salicional from the Swell and installed an 8′ Trumpet in its place. Due to the pitfalls of changes and “upgrades,” service and tuning was precarious at best.
Working with Dr. Dorroh, we discussed and agreed that new Great and Swell chests were in order. We also discussed the options of some minor relocation of the organ. This allowed most of the chambered façade pipes to be returned their original position in the façade and provided better access for service and tuning. The church also agreed to raise additional funds to allow for the reinstallation of the 8′ Salicional (while retaining the 8′ Trumpet) and to install a needed 2′ stop in the Great division. Since the church was agreeable to extending the organ out of the chamber and new chests were in order, the additional stops were easy to accommodate.
The work ensued and the organ began to take shape in our shop in early 2009. The keyboards were restored in ivory; new stopknobs and stop actions were provided in the historical fashion of the existing stop actions. Existing woodwork was repaired and refinished, and new casework was constructed as needed. The façade pipes were stripped and repainted.
The organ had a blower installed in 1934, which was later replaced. During its replacement, another reservoir was added atop the Swell box. This reservoir proved larger than necessary, and since the reservoir had water damage we opted to install a smaller reservoir. The church also provided a much better blower enclosure space. The original Hook & Hastings double-rise reservoir, though water-damaged and leaking, was intact and in position. Our revision to the winding system preserved the double-rise reservoir, as this is key to the gentle flex and stability of the wind. A new curtain valve box was provided.
As do most builders, we often build new organs; however, projects such as this are a great exercise and study for our staff to experience. As a tonal director, I find it is a good study in the format of building not a recital organ, but a church organ. Each stop in the instrument fills an appropriate position with respect to sound, color, and volume. The organ features a string in each division to balance two colorful flutes, a Stopped Diapason and a Melodia. The organ features Diapasons at 8′ and 4′ pitches on the Great. Our task for the 2′ was to achieve clarity without being strident. After all the pipework had undergone cleaning and regulation back to its original state, many were surprised at the return of color and speech intonations.
The organ was officially heard and rededicated to service on Easter Sunday, April 12, 2009. Dan Miller, choirmaster/organist, played the service, which was presided over by Father Ray Walden, Priest in Charge, and the Bishop of Alabama.
Our appreciation goes out to Dr. Jim Dorroh, Dan Miller, Father Walden, and the congregation of St. Peter’s. How delightful it was that a congregation took such interest in the return of their instrument in the weeks leading up to Easter. The return of the organ on Easter Sunday could not have been more fitting.
—Phil Parkey
GREAT (unenclosed)
8′ Open Diapason 61 pipes
8′ Melodia 61 pipes
8′ Dulciana 61 pipes
4′ Octave 61 pipes
2′ Super Octave 61 pipes
Swell to Great 8′
Swell to Great 4′
SWELL (enclosed)
8′ Salicional 61 pipes
(reinstalled)
8′ Stopped Diapason 61 pipes
4′ Harmonic Flute 61 pipes
8′ Oboe 61 pipes
8′ Trumpet 61 pipes
(by another builder)
Tremulant
PEDAL
16′ Bourdon 30 pipes
Great to Pedal
Swell to Pedal
Toe stud reversible for Open Diapason stop
Zimbelstern operated via toe stud reversible (later addition)