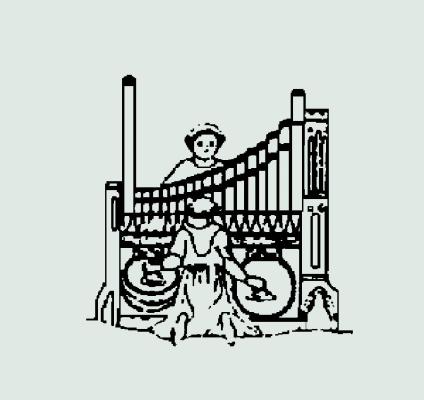
A. E. Schlueter Pipe Organ
Company, Lithonia, Georgia
Immaculate Heart of Mary Catholic Church, Atlanta, Georgia
The O’Neil-Foster Memorial Pipe Organ
Immaculate Heart of Mary Catholic Church is located in my hometown of Atlanta, Georgia, just a short drive from my office. Our involvement in the project began with an invitation to consult with this church from director of liturgy and music William Jefferson (Jeff) Bush. The church was planning a new sanctuary and wanted to study the possibility of building a pipe organ for this space.
During my first visit I had the opportunity to meet many of the church leadership, including Rev. James A. Schillinger, S.T.L., pastor; Michael D. Mullink, associate director of music; and Paul Tooher, director of business. The organ committee at this church included Jeff Bush as committee chair, Michael Mullink, Phil Jardina, Leann Logsdon, and Mark Galvin. Dr. John Romeri was invited by Jeff to serve as an informal consultant to him personally on this project.
As this distinguished group talked about plans for the new sanctuary, there was an excitement and zeal for their mission, which personally enveloped me. Beyond a simple cerebral response, I found a lasting emotional attachment to this church and its membership. I left this church posed with the question, “How could the members of the Schlueter family and our staff not be a part of this grand commission?”
To design the new sanctuary, the church engaged the services of the architectural firm CDH Partners with project architect Michael Boland. This firm’s work was interlaced with that of the liturgical consultant Brother Martin Erspamer, OSB. His contribution to this project was invaluable. Over a period that spanned years, he provided a distinct vision for the finished church building and its furnishings. He also worked as an able arbiter to diligently channel and focus the ideas, concerns, and aspirations of all the design parties and committees.
The organ, later to be named the O’Neil-Foster Memorial Pipe Organ, was made possible through the generous donations of Walter & Mary Alice Foster and Jim & Pat Sedlack.
When I was brought into the project, the basic layout of the sanctuary had already been formed and we lacked a space that allowed consideration for an organ chamber location. The only possibility was to incorporate a free-standing organ case design. The challenge was to find sufficient space that would work physically and tonally for the organ. As we studied the building plans to find a location, the sole workable area was on the central axis of the church, just behind the altar. The members of the church were willing to consider this space, but we all knew that the path to a final design would be an arduous choice, given the prominent chancel location. We considered over a dozen different organ case iterations, before settling on a final rendering.
To minimize the visual impact of the organ case, we held the center of the organ case to 10 feet of width on its forward exposure. The largest pipes of the 16′ Principal are positioned to the sides of the case and arrayed in an inverted ellipse that arcs away from the case center, which de-emphasizes the overall case width and accentuates its verticality. This greatly reduced the visual weight of the organ case.
What has pleased us most with the completed design is that it “feels right.” The casement is built of red oak with ebonized walnut accents. Taking the form of a reredos, it provides a visual backdrop that anchors the cross and the corpus. When viewed from an off-center location, the largest pipes vertically ascend toward the center to provide a central focus on Christ.
Taking advantage of the organ’s position in the church, we used the mass of the instrument casework to separate the main sanctuary from the chapel behind it. The rear of the organ case was built as a paneled oak wall with ebony dividers. The center panels form an arch to mirror and highlight the baldacchino. The stained glass in the cupola that forms the rear chapel wall provides a coalesced mixture of light and shadow, which plays off the organ’s oak panels to make this area a quiet, contemplative space for prayer. Here one senses the cloistered feeling of a space that is at once part of, and separate from, the main sanctuary. The emotional response experienced in the chapel leaves no doubt that this is Holy Space.
As the outer shell of the casework was brought to a point of design conclusion, we began to develop a stoplist that would be capable of the varied uses required of this instrument. From the beginning, the charge we were given was to design an instrument that would support worship, with a specificity of a literature bias to be a secondary concern. From shared listening experiences with the church, we developed an eclectic specification with roots in American Classicism. To support the choir and congregation, all divisions of the organ were planned to be weighted around an 8′ chorus structure with multiple weights of this tonic pitch register.
As we labored on the final stoplist, there were budgetary considerations that could not be ignored. With the free-standing case, console, and three-manual specification, this would not be an inexpensive organ to build. We faced a crossroad where the design for an instrument included most but not all of the elements we wanted in a stoplist, but a budget that had already been reached. To free ourselves from this stricture we looked inward. Those who have followed our work know it has not been uncommon for our firm to gift some additional items to our clients. We have always looked at this as our tithe to the communities of faith where we build organs. In the end, the 8′ Viole Dolce, 8′ Viole Dolce Celeste, 4⁄5′ Terz, and the 16′/8′ Trombone unit became gifts from the Schlueter family. As artists, it can be liberating to add stops into the organ on the basis of “it should be there” without sole regard to budget. Hearing the organ in the church we know that we made the right decision by our gifts.
The Great division of this instrument was built with a Principal chorus of 8′, 4′, 2′, and IV-rank Mixture that is grounded with a 16′ Bourdon. Due to a room acoustic that promotes the propagation of bass frequencies, the pipe scales of the 16′ and 8′ registers were pulled in, and made slightly smaller to support clarity of speech and phrasing. We chose to use a large-scale metal open 8′ Hohl Flute because of its ability to be used as a blending and thickening agent to the Great chorus. When used as an independent solo voice it has a clarity and focus that are often lost in large-scale open flutes of different construction. It is paired with a lyrical 4′ Rohr Flute that is a playful muse in this acoustic. The 8′ Trumpet on the Great has English shallots and is thinner in scale and texture than its compatriot in the Swell division. As a chorus reed with a subtle edge-tone, it provides a blaze of color under the Great chorus. The Swell Basson-Hautbois and Positiv Krummhorn are duplexed to this division to allow differing weight and color possibilities to the ensemble or allow their use as solo voices.
While everyone recognizes the utilitarian function of the Swell division as a foil to the Great for congregational accompaniment, we realized early on the importance of careful stop choice for the single enclosed division on this instrument. It would need to have a wide dynamic range and timbre to be effective in undergirding the choir and soloist. The Swell division was designed with a rich palette, replete with various weights of color and texture.
With the choir on the side apse, there was a concern about the organ being heard evenly. The expression box opens on three sides to provide an evenly diffused cone of sound in the church and also to provide tonal focus for support of the choir.
The third manual on this instrument is an unenclosed Positiv division. With its rearward position in the upper portion of the chapel cupola, we were able to take advantage of the tangential incidence of the wall surfaces. This reflects and refracts the Positiv division to a position of forward presence in the organ.
The Erzahlers proved to be the perfect string stops in this unenclosed division. With their position at the capstone in this space, the sound filters throughout the church in an even, gentle manner. These stops, when drawn and coupled with the Viole de Gambe, Viole Dolce, and their companion Celestes, mass in a bloom of sound that buoys the spirit and lifts the soul.
An unusual stop in this Positiv is the 4⁄5′ Terz. Constructed as small principal pipes, it breaks back one octave at G3. It can be effective as a coloring agent to 8′ and 4′ stops in the organ, added to the 11⁄3′ to build a bell-like Glockenspiel mixture, or used with the 16′ and unison couplers to build a secondary Cornet. With its middle compass octave shift, the 4⁄5′ has enough tonal weight to combine with the mixture to supply a French accent to larger registrations.
To provide sufficient undergirding for this instrument, we started with a case design that allowed an exposed 16′ Principal in the Pedal. With its forward position in the case, this stop is voiced in an unforced manner that provided the fundamental we desired allied with harmonic definition. The 16′ Bourdon and balance of the Pedal resources are positioned at the upper rear of the organ case to take advantage of the acoustical reflection of the cupola in the same manner as the resources of the Positiv division. With this spatial treatment, these stops project forward to tonally sit beside the 16′ Principal. Softer underlayment of the Pedal foundation is provided by the 16′/8′
Lieblich Gedeckt in the Swell division.
The 16′ Trombone and 16′ Basson-Hautbois provide the reed foundation for this instrument. The 16′ Trombone in the Pedal division is available as a manual extension to provide a dynamic solo reed. This stop is eight inches in scale at CCC and is on a moderately high wind pressure. It provides a rich, vibrant voice in the favorable acoustics of the room and can work equally well as a solo voice or logical conclusion to the ensemble in large registrations.
Mechanically, this organ follows our normal practice with its use of electro-pneumatic slider windchests of the Blackinton style, electro-pneumatic unit action for reeds and large flue stops, and a winding system with dual curtain valve reservoirs. The resources of the organ are controlled by a three-manual drawknob console that is built of red oak and includes ebonized accents commensurate with the organ case. The console features such modern conveniences as multiple memory levels, programmable crescendo and sforzando, transposer, piston sequencer, MIDI, and the ability to record and play back organ performances.
With any organ project it is possible to be so close to your own work that you cannot judge it on its own merits. It becomes important to step back from your work before you can say it is time to “put down the brush.” This is particularly true of tonal finishing. The surety of vision and purpose that guides one’s work can also result in blinders preventing your best work from coming forward. To mitigate this, our firm completes tonal finishing over a period of time. Not only does it allow the ears to relax, but it also allows you to come back to a project more objective and able to assess your work dispassionately. The tonal finishing occurred throughout the first year, with multiple visits to the church as we traveled through the liturgical year and made different demands of the organ’s resources.
I want to extend a sincere “thank you” to our team of tonal finishers on this project, which included Dan Angerstein, Anthony Nichols, John Tanner, Bud Taylor, Dave Koscis, and Fred Oyster. I also want to thank the dedicated members of my staff, led by Marc Conley, who selflessly provided their hands and hearts to the building and installation of this instrument. The construction of an instrument of this scale is a monumental task with thousands of man hours that are visible and many thousands more that are unseen. The aforementioned are the people who helped sculpt the wood, zinc, lead, copper, and brass into poetry.
In the end, as a principal of the firm whose name is on the organ, what do I think about the organ we built? Early on I knew how special this project could be. As a builder I have been privileged to attend many concerts at this church and to attend Mass on multiple occasions. I must confess that as much as I have enjoyed the organ in recital, I have taken far great pleasure hearing the organ in a worship setting. This is not said to diminish the music brought forth by those who have played the organ in concert; rather, hearing the organ taking its part in worship is a validation of the years of planning and work that go into such an instrument. Having been part of building an instrument that serves in worship every day is the greatest gift an organ builder can have. It is a culmination of pride, passion, and a legacy that we are leaving to future generations.
We are very pleased to offer selections from recordings made on this organ by Herbert Buffington, available at pipe-organ.com/listen.shtm.
A. E. Schlueter Pipe Organ Company can be reached at P. O. Box 838, Lithonia, GA 30058; 770/482-4845 or via our website: www.pipe-organ.com.
—Arthur E. Schlueter III