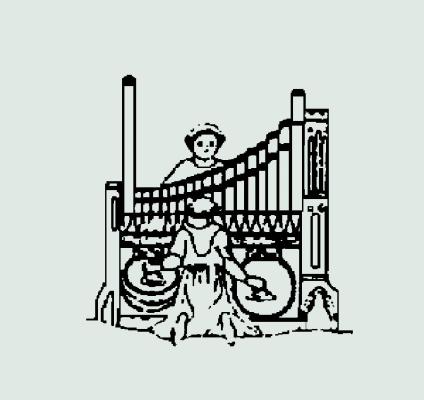
Parkey OrganBuilders, Duluth, Georgia
Cathedral of St. John Berchmans, Shreveport, Louisiana
October 2011 marked the completion of the new pipe organ by Parkey OrganBuilders for the Cathedral of St. John Berchmans, Shreveport, Louisiana. St. John Berchmans had embarked on a major building restoration in 1992, just a few years after becoming the cathedral for the newly created Diocese of Shreveport. The 1992 restoration included plans to build a new organ for the church, but for various reasons, though the pipe organ was signed for and partially built, the instrument was never completed.
More than 15 years later, after the renovation was completed, the cathedral, under the direction of the rector, Father Peter Mangum, and the newly appointed director of sacred music and organist, Justin Ward, set itself a goal of expanding the cathedral music program, to include evaluating and completing the organ project. The cathedral secured the services of James Dorroh of Birmingham, Alabama, as an organ consultant to help achieve the goal of creating an organ that would visually complement the architecture of the building and tonally support both choral and congregational singing. The organ committee recognized the need for such an organ to provide sacred music in a way that would augment the worship experience for parishioners in addition to providing a cornerstone instrument for the community.
The organ committee quickly narrowed the list to three very capable firms, and in the summer of 2010, the committee chose our firm to complete the organ project. We worked directly with Mr. Ward and Dr. Dorroh to refine the initial specification drawn up by Dr. Dorroh to create a sound that would fit the needs of the cathedral. Because the choral program remains the center of music for the cathedral, we had to tailor our design for the most efficient utilization of space possible in the gallery. The new organ stands in two matching cases within the same footprint allocated for the organ in 1992.
To accommodate any number of singers and additional musicians, the organ was designed with a movable console, which of course dictated the need for some sort of electric action. Our firm is comfortable in working with both electric and mechanical actions. When tracker action is not possible, we recommend the use of electro-pneumatic slider chests. Our windchests and winding systems are designed and built completely in-house. Using computer-aided design (CAD) software systems and computer numerically controlled (CNC) router machinery, we have developed an efficient and effective slider chest design for a clean and responsive action. The winding system is engineered based on single-rise reservoirs for a steady, fluid wind supply but with a gentle flex to provide life to the singing line of the organ.
In addition to the mechanical design of the organ, our CAD systems have been instrumental in providing extensively scaled rendering work, so that the client can see and experience the visual design of an organ before anything is ever committed to materials.
As the organ is a musical instrument capable of a strong visual and aural statement, we work to combine the art of sight and sound together. Michael Morris of our staff provided the visual design, which included retaining materials from the previous organ and expanding the case to house the new organ. In his design, one notes the core of the previous case combined with the essence of visual design seen in organbuilding of the early 1900s. Case details were shifted from the contemporary look to a much more traditional gothic format consistent with the architecture of the cathedral. A majority of material was retained from the previous case, though some parts are easily recognizable and some vastly changed. The side façades provide a magnitude of scale for the space: where the previous organ case was based on the use of 8′ pipes, the new cases are based on the 16′ Principal and Violone. The use of polychrome details combines with the colors of the nave for a more complete marriage of organ case and room architecture. Careful attention to detail was provided throughout the project. Details range from the turned wooden drawknobs to the 18k gold leaf accents in the case.
Since part of an earlier organ existed, the organ committee challenged us to retain parts of the existing instrument. In reviewing the uncompleted organ, we found that there were mechanical supply parts that could be retained without sacrificing the integrity of the instrument. Unfortunately, the pipework did not offer such an extensive array of options. While we did retain some pipework, it was limited to four ranks that were
rescaled and revoiced to be compatible with the new tonal design of the organ. The remaining organ is completely new, with custom scaling for the space.
In addition to the challenge of working with an existing organ, the cathedral realized the needs of working within an existing space. Though the organ enjoys an excellent position for tonal egress in the room, the nave presented some obstacles in terms of sonic reflections. After consultation with Dennis Fleisher of MuSonics, the cathedral underwent an extensive renovation of the ceiling in the main portion of the nave, in order to install hard surfaces over the previous acoustically absorbent ceiling. The acoustical response in the room was greatly improved. The room now readily supports the organ’s warmth and clarity equally throughout the nave.
Our conversations with Justin Ward and James Dorroh focused on the need for the organ to lead choirs and congregations in music for the worship service. In recent years the Catholic Church has further recognized the contribution of the pipe organ as the main instrument for the Catholic Mass. Dr. Dorroh and I discussed the role and influence of the Baroque revival in America, and the influence of leading clarity common to the German Baroque organ. Those traits were combined with aspects of the weight and presence of the French Grand Orgue of the late 1800s. The result is an organ that can skillfully handle the full range of organ literature, from soft and subtle to large and fiery. However, the use of moderate pressures and large scales keeps a refined and unforced sound.
Mixtures are carefully terraced and balanced to define the chorus with a silvery clarity without becoming abrasive. Power and brilliance are also supported by the use of French reeds in the Swell division. The Cavaillé-Coll-scaled 8′ Voix Humaine was featured in the Franck Choral in proper context during the dedication recital. The Pontifical Trumpet is of ample scale to carry in the room over full organ, yet it manages chords easily with a majestic elegance. The 8′ flutes possess individual color and personality and are also enhanced with carefully balanced 4′ flutes in each division. Two independent manual Principal choruses are provided in addition to full mutations in the Choir. The 8′ Viola Pomposa and 8′ Flute a
Cheminee provide the foundation support for the Swell division. The dynamic terracing allows for a smooth buildup of sound from the 8′ Spitzflöte in the Choir to full organ.
In the end, the organ makes a strong but elegant statement consistent with the quality of worship services at the cathedral. Justin Ward and James Dorroh were a tremendous pleasure to work with during the project, providing clear and concise direction while yet allowing us room for artful design and finishing. We appreciate the confidence placed in us by the parishioners, clergy, and staff of the cathedral. I also extend my personal thanks to our own staff and suppliers who have made this an overwhelming success.
Please feel free to contact us at www.parkeyorgans.com, or contact the cathedral for further information. Visits can be arranged with Justin Ward at the cathedral.
—Phillip K. Parkey
President and Tonal Director
Parkey OrganBuilders
Staff
Phillip K. Parkey—President and tonal director, voicing and tonal finishing
Michael Morris—Visual and structural design and installation
Josh Okeson—Shop foreman, cabinet maker, wiring and installation
Otilia Gamboa—Chestwork, wiring and small parts
Philip Read—CNC operator, cabinet maker and installation
Jim Allen—Cabinet maker and installation
Kenny Lewis—Voicing, wiring, installation and tonal finishing.