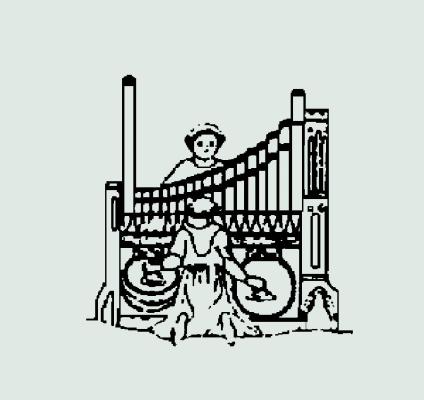
Foley-Baker, Inc.,
Tolland, Connecticut
Duke University Chapel,
Durham, North Carolina
The 1932 Aeolian at Duke University Chapel has as colorful a history as any American organ. In 1930, at a time when contracts had grown scarce, Aeolian wrested the job from Skinner, only to plagiarize the stoplist and layout of Skinner’s 1928 organ for Princeton University Chapel. By the time Aeolian installed the job, their brazen move had evolved into the bittersweet reality of a merger with Skinner. Thus, the Duke organ became Aeolian’s last statement of what a grand organ should be. After World War II, the instrument developed particular appeal through the tenure of Chapel organist Mildred Hendrix, with later chapters of near-replacement in the late 1980s, a seminal bequest toward restoration by Director of Chapel Music Benjamin Smith, renewed respect in the 1990s, and a complete renovation finished in 2009 by Foley-Baker, Inc. More than history, the tale of the Duke Aeolian reads like a screenplay.
Mike Foley recently wrote up the project in The American Organist from his company’s point of view; a forthcoming article in The Tracker will examine the organ’s historical and contemporary importance in greater detail. This piece focuses on technical and musical issues raised in the renovation, since the Duke project lies in that area between restoration (in which nothing is changed) and rebuilding (in which new and old material are given equal status toward an updated musical goal). How this project balanced respect for the original material with modern and practical concerns is important to review, and can be examined in three primary areas: musical, console, and interior.
Background
From 1929 to 1932, its final years of production, Aeolian’s organ department produced three heroic organs: Longwood Gardens (Op. 1726, 146 ranks, five 32′s), completed in June 1930; Westchester County Center, an auditorium in White Plains, New York (Op. 1747, 69 ranks, 32′ Bombarde), completed in late 1930; and Duke Chapel (Op. 1785, 120 ranks, three 32′s), signed in October 1930, installed in early 1932 and dedicated that June. (In 1931, Aeolian signed a fourth in this mode for the Hershey Community Theatre in Pennsylvania. The contract went to Aeolian-Skinner in the merger, and the resulting instrument, completed in 1933 under Ernest Skinner’s personal direction, was a Skinner through and through.)
High pressures, large scales, multiple reed batteries, and identical primary scaling link these Aeolians as sister efforts. The recent renovations at Duke and Longwood reveal that while Aeolian’s intentions were suitably heroic in each case, the company was still feeling its way along the finer points of how to build mechanisms and pipes to cope with the demands of high wind pressures. In turn, those details affect how these organs are renewed for their second life cycle.
Musical issues
At 120 ranks, the tonal disposition at Duke represented an apotheosis of the Symphonic organ, from a period in which a semblance of traditional chorus building was beginning to return to American organbuilding. The comprehensive chancel scheme was supported by an encased two-manual section in the nave, having an unenclosed chorus, Pedal 16′ Principal in the façade, and a group of enclosed softer voices.
The instrument remained in this original state only 16 years, however. Certain mechanical and musical issues brought about a campaign of work by Aeolian-Skinner in 1948, including a new remote-control combination action and crescendo pedal. Ten new string ranks were installed, probably not to provide a different type of tone as much as to correct speech deficiencies common to ranks built from Hoyt metal, as the originals were. Some sounds were changed. New Choir mutations did not precisely replicate the Aeolian originals, and the Antiphonal chorus was remodeled, using new 8′ and 4′ ranks, a revoiced chorus reed, and a de-tierced and brightened mixture. Finally, the chancel Great chorus underwent a bit of reshuffling: the 51⁄3′ Quinte became a third 4′ Principal, the III–VI Plein Jeu was returned to the factory to be loudened, and the chorus was rebalanced somewhat on site.
In 1975 the Echo-Antiphonal was removed to make way for the present Flentrop, deleting a section of the Aeolian many had found particularly effective. But much more noteworthy was the Chapel’s acoustical transformation in 1974, from one of stereotypical Akoustolith deadness to epic acoustical grandeur. This one event changed all music in Duke Chapel; certainly no one active at Aeolian or Aeolian-Skinner ever experienced Op. 1785 as we do today.
Given this history of change, it was clear that any serious renovation of the Aeolian needed to develop an ethic around the organ’s tonal content. Duke organists Robert Parkins and David Arcus spent years considering the matter, working through the issues as they considered various restorers. By the time Foley-Baker was signed on in 2007, the plan had solidified around restoration of the 1932 tonal scheme: retaining the 1948 Aeolian-Skinner replacement ranks, reversing the 1948 changes and shifts, and regulating the pipes as closely as could be reasoned to where Aeolian left them in 1932. The adoption of such a plan was not a foregone conclusion, for the Aeolian is not without its anomalies. Unison flute tone outside the Solo is atypically gentle (the Great Principal Flute, for example, is softer than the Gemshorn), and some layout details that actually aid tonal projection do not initially appear to. After careful study and consideration, however, the conclusion among organists and rebuilders was that the most musical result would be attained with a return to the 1932 scheme.
While Aeolian’s scaling and voicing was heroic in these jobs, the metal pipework and some of the heftier chorus reeds are perhaps one degree less substantial than what is asked of them. As a result, it becomes especially incumbent to examine pipes thoroughly during rehabilitation to ensure their readiness for another life-cycle. In addition to normal tub washing, numerous seams and loose languids were repaired. Pipes were re-rounded on mandrels to assure good speaking conditions, tops trimmed, and new tuning collars fit throughout. Some of the largest wood pipes had developed cracks, which were routed out, splined and repaired. Finally, Foley-Baker tonal director Milovan Popovic reviewed all flue pipes on the voicing machine. The goal here was to do anything and everything that would promote stability of speech and tone for the next several generations.
For Duke, two aspects made the flue reconditioning process more complex. Unlike working on a Skinner, where many examples exist for study, the scarcity of this breed of Aeolian can involve more interpretation than can be comfortable during a restorative process. Also, Aeolian employed Hoyt metal for many flue ranks, evidently unaware of the material’s tendency to creep over time. The syndrome mostly affects flue pipe windways, as lower lips bow out, making the tone less efficient and duller while vaguely staying on speech. Re-setting the windways is straightforward enough, but it involves a careful ear and a degree of conjecture to divine what the original voicers were after.
Broome & Co. LLC undertook reconditioning of all reed stops, having performed a similar task with the Longwood reeds, each job informing the other. That process is intensive. The pipes are fully documented before disassembly and rigorous cleaning; wood wedges are replaced with brass; every scrolled slot is cut out and replaced; and finally, the pipes are re-assembled and checked through on the voicing machine.
The final element in the organ’s musical rehabilitation was the many weeks of tonal finishing, again led by Milovan Popovic. Tremolo regulation received perhaps as much attention as tone, an area to which Mike Foley is personally devoted. Aeolian used small tremolos to wobble large reservoirs, resulting in a light, fast and almost reiterative effect that many would find unpalatable today. To produce, from these elements, an effect that organists will actually use is no small feat. Finally, after years of silence, the Chimes and Harp are heard again, the latter particularly fine in Aeolian organs, long on tone and short on action noise.
In the end, there was one stoplist change and one addition. The 15-inch wind pressure Pedal reed unit was made available in the manuals as an additional unison Trombone. And a new 25-inch-wind Festival Trumpet was added, modeled on the louder of the two fanfare Tubas on the Skinner at Yale University (the Aeolian-Skinner at Girard College in Philadelphia has a stop of similar construction). All members of the design team reflected upon a group of samples; the preferred stop was built by A.R. Schopp’s Sons and voiced by Christopher Broome. These unenclosed pipes are nestled into the right transept opening, speaking directly into the crossing as a heraldic voice.
Console
While the company’s earliest consoles followed the terrace-jamb form typical of the late 19th century, Aeolian evolved a trademark style in the ’teens, using horizontally tilting tablets in angled side jambs. The resulting low profile, even for large consoles, suited the residential setting (the person on the bench, operating a roll, could still engage socially). Organists often derided these consoles, since at a glance it wasn’t clear which stops were drawn. Branching out to church organs in the 1920s, Aeolian first rotated the tablets to the more usual vertical arrangement, then developed a distinctive type of drawknob console, with natty celluloid moldings around departments and large ivory stopknobs on thick ivory shanks rather than the usual ebony. Some peculiarities migrated from the residence consoles: expression shoes with little excursion, spongy key action without tracker touch, non-AGO pedalboard and clavier relationships, and placement of the Sforzando piston directly next to Great to Pedal (surprise!).
The Duke console was Aeolian’s tallest of this model: impressive as a forest of ivory, if tending to noisiness with its vacuum-action stopknob motors. As the size and fame of the Duke choir grew, the console height became a liability in the visual communication between organist and conductor. And, with the removal of the nave sections in 1975, the console contained many redundant controls.
For these and other reasons, the organists decided they would prefer to archive the original console and have a smaller one better suited to the instrument’s current configuration. Richard S. Houghten of Milan, Michigan was directly contracted for this work, along with the design and installation of solid-state control systems throughout. The new console blends dimensions and features more typical of Skinner (particularly key-touch and piston arrangement) with some of the visual design peculiar to the Aeolian original. Legally sourced ivory for keys, stopknobs, tablets, pistons, and indicator tags contribute to an ambience more of a modernized old console than a brand-new one.
Interior
Projects involving old organs are made easier when the instruments in question are entirely original. More challenging is an organ that has unquestionable musical merit but might not have a mechanical foundation of comparable quality. At Longwood, Aeolian’s first truly high-pressure effort (ranging from 8″ to 30″), Aeolian experienced some structural instability with their new style of pitman windchest. Unlike Skinner chests, which are formed with horizontal joist-like separators between every stop, the Aeolian pitman chest is a simple box with a solid table, four sides and an occasional vertical post. At Longwood, this proved insubstantial to the pressures employed (many were reinforced in the recent renovation); the White Plains organ shows further evidence of the same syndrome. By the time the Duke organ was built, Aeolian had already realized that stouter construction was necessary. While each chest was carefully checked for signs of stress or need for reinforcement, none was needed in the end.
Otherwise, restoring all mechanisms to a like-new standard comprises the bulk of any restorative effort. Each firm’s instruments bring particular challenges. Aeolian was atypical in being a two-finish wood shop: some things painted, others shellacked. This factor complicates renewal of the main windchests, whose solid tops are shellacked but whose sides and bottoms are painted. Most Aeolian organs have 6-stage accordion swell engines. For fancy jobs, a relay mixed and matched the six stages to produce 14 discrete increments of opening. A nice idea in theory, in practice the operation could lack smoothness, particularly in the first few stages. For Duke, Aeolian built 14-stage accordions, an elegant solution but a tougher restoration challenge. Finally, tremendous effort was put into renewing the Duke chambers and making all surfaces maximally reflective, together with a well-lit working environment for the technician. After decades of looking dank and worn, the chambers now gleam like a first-class hotel lobby.
Personnel
There had been talk of restoring the Duke Aeolian since 1990. Through the 1990s and 2000s, former curator Norman Ryan had rehabilitated much of the Swell, and portions of the Choir and Solo. In the push to undertake a comprehensive renovation, two gentlemen stood behind the project and saw that it got done. Duke University Organist Dr. Robert Parkins set aside earlier conceptions about style and saw that the instrument’s fabric and tone were respected. He also dealt with the many logistical issues such projects raise. Chapel Organist Dr. David Arcus, familiar with and fond of similar instruments built by Skinner (particularly that at Yale University, on which he studied with Dr. Charles Krigbaum) asked important questions, challenged assumptions, and kept music central to the discussion. His persuasive playing on the Aeolian invigorated established admirers and persuaded new ones. For Sunday worship, the two organists have developed creative means of employing both Flentrop and Aeolian in antiphonal hymn accompaniment, as well as showcasing Duke’s other organs: the meantone Brombaugh in the side Memorial Chapel, and the Richards, Fowkes in Goodson Chapel, next door at Duke Divinity School.
A project of this magnitude, accomplished on budget in 20 months, requires planning of the surest sort coupled to experience in managing complex projects. While Mike Foley plays an active role in that process, foreman Phil Carpenter’s long experience in the site management shows through every detail of the finished result. The Duke renovation takes its place in FBI’s impressive roster of high-profile work of late: Boston-area Aeolian-Skinners at Symphony Hall, The First Church of Christ, Scientist, and Trinity Church; Groton School; and in 2010, the relocated 1929 Skinner for The Memorial Church, Harvard University.
For those who admire all of Duke’s fine organs, in their excellence and variety, this renovation allows the Aeolian to shine forth with the elegance of its sisters. Better still, it is played often and well. For those who labor hard on such jobs, there is no finer outcome.
—Jonathan Ambrosino
Photo credit: Mark Manring
The Duke Aeolian was rededicated in a gala concert February 8, 2009, jointly offered by Drs. Parkins and Arcus to a capacity audience, with works of Brahms, Karg-Elert, Reger, Pierné, Franck, Gigout, Locklair, Tournemire, and Jongen. The entire recital can be seen episodically on YouTube.
Chancel Organ, Duke University Chapel, Durham, North Carolina
Aeolian Organ Company, Opus 1785, 1931Р32
GREAT (wind pressures: 6″ for flues, 12″ for reeds)
32′ Quintaton (from tenor c) 61 pipes
16′ Diapason 73 pipes
partially in north façade
16′ Bourdon (Pedal, ext) 17 pipes
8′ First Diapason 73 pipes
swapped with Second in 1932
8′ Second Diapason 73 pipes
swapped with First in 1932
8′ Third Diapason 73 pipes
restored to original from Prestant 4′
8′ Gemshorn 73 pipes
8′ Principal Flute 73 pipes
8′ Doppel Flute 73 pipes
(in Choir chamber)
51⁄3′ Quint 73 pipes
restored to original from Third Diapason
4′ Octave 73 pipes
4′ Principal 73 pipes
4′ Flute 73 pipes
(in Choir chamber)
31⁄5′ Tenth 73 pipes
22⁄3′ Twelfth 61 pipes
2′ Fifteenth 61 pipes
Harmonics V 305 pipes
Plein Jeu III–VI 268 pipes
16′ Contra Tromba 73 pipes
(in Choir chamber)
8′ Trombone (Pedal)
8′ Tromba 73 pipes
(in Choir chamber)
4′ Octave Tromba 73 pipes
(in Choir chamber)
8′ Tuba Mirabilis (Solo)
8′ Festival Trumpet 61 pipes
(new, floating, 25″ wind pressure)
Great to Great 16
Great to Great 4
Great Unison Off
SWELL (wind pressures: 6″ for flues and orchestral reeds, 10″ for chorus reeds)
16′ Bourdon 73 pipes
8′ Diapason 73 pipes
8′ Geigen Diapason 73 pipes
8′ Gamba 73 pipes
8′ Gamba Celeste 73 pipes
8′ Salicional 73 pipes
8′ Voix Celeste 73 pipes
8′ Rohrflute 73 pipes
8′ Cor de nuit* 73 pipes
8′ Flauto dolce 73 pipes
8′ Flute Celeste 61 pipes
4′ Octave 73 pipes
4′ Fugara 73 pipes
4′ Flute Triangulaire* 73 pipes
22⁄3′ Nazard* 61 pipes
2′ Piccolo 61 pipes
2′ Flautino* 61 pipes
13⁄5′ Tierce* 61 pipes
Cornet V (composed of stops marked*)
Chorus Mixture V 305 pipes
16′ Posaune 73 pipes
8′ French Trumpet 73 pipes
8′ Cornopean 73 pipes
8′ Oboe 73 pipes
8′ Vox Humana 73 pipes
4′ Clarion 73 pipes
8′ Harp (in Choir box)
4′ Celesta (in Choir box)
Tremolo
Chimes
Swell to Swell 16
Swell to Swell 4
Swell Unison Off
CHOIR (wind pressure: 6″ throughout)
16′ Gamba 12 pipes
(ext Viole d’orchestre 8′)
8′ Diapason 73 pipes
8′ Viole d’orchestre 73 pipes
8′ Viole Celeste 73 pipes
8′ Concert Flute 73 pipes
8′ Quintadena (derived from stops marked*)
8′ Dulciana* 73 pipes
8′ Dulciana Celeste 73 pipes
4′ Violina 73 pipes
4′ Harmonic Flute 73 pipes
22⁄3′ Nazard* 61 pipes
2′ Piccolo 61 pipes
13⁄5′ Tierce 61 pipes
11⁄7′ Septieme 61 pipes
16′ Fagotto 73 pipes
8′ Trumpet 73 pipes
8′ Corno di bassetto 73 pipes
8′ Orchestral Oboe 73 pipes
8′ Tuba Mirabilis (Solo)
8′ Festival Trumpet
8′ Harp 49 bars
4′ Celesta (ext Harp) 12 bars
Tremolo
Chimes 25 tubes
Choir to Choir 16
Choir to Choir 4
Choir Unison Off
SOLO (wind pressures: 10″ for flues and orchestral reeds, 15″ for chorus Tubas, 25″ for Tuba mirabilis)
8′ Stentorphone 73 pipes
8′ Gamba 73 pipes
8′ Gamba Celeste 73 pipes
8′ Flauto Mirabilis 73 pipes
4′ Octave 73 pipes
4′ Orchestral Flute 73 pipes
Mixture V 305 pipes
16′ Tuba 73 pipes
8′ Tuba Mirabilis 73 pipes
8′ Tuba 73 pipes
8′ French Horn 73 pipes
8′ English Horn 73 pipes
4′ Clarion 73 pipes
Tremolo
Chimes
Solo to Solo 16
Solo to Solo 4
Solo Unison Off
PEDAL (wind pressures: 6″ for flues, 15″ for reeds)
32′ Diapason (ext Ped Diap) 12 pipes
32′ Bourdon (from Bourdon 16′; 1–12 in
common with Diapason 32′)
16′ Diapason 32 pipes
16′ Contrabass 32 pipes
16′ Diapason (Great)
16′ Bourdon 68 pipes
16′ Gamba (Choir)
16′ Echo Lieblich (from Swell Bourdon)
102⁄3′ Quint (from Pedal Bourdon)
8′ Octave (ext Diapason) 12 pipes
8′ Principal 32 pipes
8′ Gedeckt (from Pedal Bourdon 16′)
8′ Stille Gedeckt (from Sw Bourdon 16′)
51⁄3′ Twelfth (from Pedal Bourdon 16′)
4′ Flute (from Pedal Bourdon 16′)
Harmonics V 160 pipes
32′ Bombarde (ext Ped Tbone) 12 pipes
32′ Fagotto (ext Choir) 12 pipes
16′ Trombone 32 pipes
16′ Tuba (Solo)
16′ Tromba (Great)
16′ Fagotto (Choir)
102⁄3′ Quint Trombone (from Great Contra
Tromba 16′)
8′ Trombone (ext) 12 pipes
8′ Tuba Mirabilis (Solo)
8′ Festival Trumpet
4′ Clarion (ext) 12 pipes
Chimes (Choir)
Couplers
Great to Pedal 8 Solo to Great 16
Swell to Pedal 8 Solo to Great 8
Choir to Pedal 8 Solo to Great 4
Solo to Pedal 8 Solo to Swell 16
Great to Pedal 4 Solo to Swell 8
Swell to Pedal 4 Solo to Swell 4
Choir to Pedal 4 Swell to Choir 16
Solo to Pedal 4 Swell to Choir 8
Pedal to Pedal 4 Swell to Choir 4
Pedal Divide Great to Choir 16
Swell to Great 16 Great to Choir 8
Swell to Great 8 Great to Choir 4
Swell to Great 4 Solo to Choir 16
Choir to Great 16 Solo to Choir 8
Choir to Great 8 Solo to Choir 4
Choir to Great 4 Pedal to Choir 8
Great and Choir Transfer
Balanced Expression Pedals
Choir Expression
Swell Expression
Solo Expression
Crescendo (programmable)
Combination Pre-sets
Standard Capture Combination System with 256 levels of memory
Manual Piston Combinations
Great: 1–8, 0 (Cancel)
Swell: 1–8, 0
Choir: 1–8, 0
Solo: 1–8, 0
Pedal: 4–8, 0
General: 1–20
General Cancel
Pedal Piston Combinations
Pedal: 1–5, 0
General: 1–16
Setter
Piston Sequencer
Memory Up and Down pistons
Reversibles
Manual and Pedal Pistons
Great to Pedal 8
Swell to Great 8
Choir to Pedal 8
Solo to Pedal 8
Diapason 32′
Bombarde 32′
Fagotto 32′
16′ Manual Stops Off
32′ Pedal Stops Off
All Swells to Solo Expression Pedal
Sfz mf
Sfz Tutti
Manual Pistons Only
Solo to Swell 8
Swell to Pedal 8
Choir to Great 8
Solo to Great 8
Swell to Choir 8
Solo to Choir 8
Great to Choir 8
All Pistons Next
Harp Sustain
Indicator Lights
Usher Signal
Telephone
Transposer
Pedal Divide
Sfz mf
Sfz Tutti
Crescendo
All Swells to Solo Expression Pedal
All Pistons Next
Pedal 32′ Off
Manual 16′ Off
Harp Sustain
Digital display for memory level, general piston number, and crescendo level