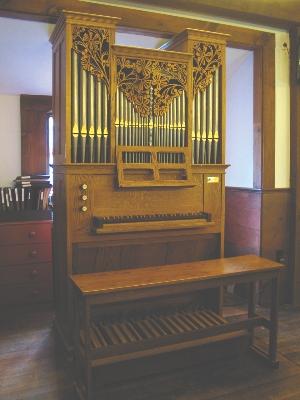
Out and about
After Christmas 2019 I retired from maintaining pipe organs. With some forty-five years of racing about twice a year to get to every client during “tuning season,” I was looking forward to sitting back, watching my friends and colleagues as they blasted about doing Easter and spring tunings, but as it turned out, no one was doing any tuning that spring. In March of 2020 the world as we knew it shut down, churches closed their doors, and organ tuners across the country stayed home.
My tuning and service career started when I was a student at Oberlin during the 1970s, as I was fortunate to work three days a week for John Leek. If you are a regular reader, you have read about John before. He was a first-generation Dutch immigrant who apprenticed in various workshops in the Netherlands starting when he was a child. He came to the United States in the early 1960s to work with Walter Holtkamp, Sr., whose reputation as an innovating organbuilder was widely known. While working on Holtkamp organs on the campus of Oberlin College, Leek saw that the school was advertising for a full-time organ curator. “That’s the job for me.”
He was still employed by Oberlin when I started working with him, but as he had developed a lively organ service trade outside of his work at the school, he soon left Oberlin and founded his eponymous company. I loved traveling around the area with him servicing organs from the start, going in and out of church and school buildings, working on a variety of instruments. Each client had distinct personalities, both personal and institutional. It was easy to tell if a place was well run or struggling, ambitious or complacent, progressive or conservative. There were people we looked forward to seeing and people we knew would be difficult. There were organs that were fun to work on, and a few that we dreaded. Some buildings were immaculately maintained, always neat and clean, and others were dirty, smelly, and cluttered.
I left John’s shop in 1984 with my wife and two toddlers to return to Boston where I grew up, joining the workshop of Daniel Angerstein & Associates in Stoughton, Massachusetts, and taking a position as music director at a lovely Congregational Church in Lynnfield, Massachusetts. In my first weeks with Angerstein, Dan and I went on service calls together so he could introduce me to the more complex and important instruments, and I was soon exploring my home territory with helpers from the workshop, learning the tricks and foibles of each instrument and client.
Dan closed his business in 1987 to become tonal director at M. P. Möller for what turned out to be Möller’s waning days—that venerable firm closed in 1993—and I took on Angerstein’s service clients as I formed the Bishop Organ Company. Over the years I think I serviced more than 300 different organs, some for short periods, some for well over thirty years, and I know there was a stretch in the 1990s when I had close to 100 clients at once. I had a group of wonderful helpers, three of whom I taught to tune and who were my pleasant travel companions as we rolled around New England.
§
We worked on a wide range of organs, from the mighty 240-stop Aeolian-Skinner at The First Church of Christ, Scientist (The Mother Church), in Boston where we tuned once a week, to a three-stop positive organ by Bedient Pipe Organ. That Bedient organ is in Saint Mary of the Harbor Episcopal Church in Provincetown, Massachusetts, at the tip of Cape Cod. Provincetown is more than seventy-five miles from the Sagamore Bridge connecting Cape Cod to the mainland. It was seventy-five miles from the workshop to the bridge, so we would schedule another service call on the Cape to make the trip worthwhile. After all that driving, tuning that tiny organ was something of a lark. Once as we started that long drive home, my helper Mark was half asleep in the passenger seat, looking dreamily out the window. As we passed a car, I overheard him whimper softly to himself, “They have ice cream.” I took the hint, and we stopped at the next opportunity.
After his retirement, my father was interim rector at Saint Mary, and I played a short evensong recital on the organ. It was like riding a tricycle. The organ had been a gift from an elderly gay couple who had lived in Provincetown for decades who collected $30,000 worth of recyclable bottles and cans by rooting through the dumpsters behind restaurants and bars—600,000 bottles and cans.
I once got fired by a client after a long day of travel. When I was working with Angerstein, we did a renovation and expansion project on a small Hook & Hastings tracker organ on Martha’s Vineyard, a quaint but exclusive touristy island about forty-five minutes by ferry from Cape Cod in Massachusetts. Later, when I was working on my own, the organ ciphered on Good Friday, and I received a call from the organist informing me that Easter was the day-after-tomorrow. His panicky and self-centered demeanor was well remembered from the time of the renovation project. I was finished with my hundred-or-so tunings, and the program of Easter music at my church was ready to go, so on Holy Saturday I made the two-hour drive from home in North Reading, Massachusetts, to Woods Hole where you catch the ferry to the Vineyard. It takes most of an hour to get your car in line for the ferry, and it is a forty-five-minute trip across the water.
I got to the church around noon, opened the windchest bung board, found a pallet caught between two guide pins, pushed the pins apart with my fingers, closed the bung, checked the tuning of the Oboe, and drove back to the ferry terminal. The invoice I sent the next week reflected four hours of driving, four hours dealing with the ferry, the cost of mileage and ferry tickets, and my minimum hour-and-a-half service call. The organist was furious. “You were in the church for fifteen minutes and you’re charging me a thousand dollars? You’re never coming back here.” I would not have expected “I’m so grateful you could get here in time for Easter” from that guy.
I had another panicky call from an organist on a Saturday morning. A wedding was starting in an hour, and the organ would not play. When he turned on the switch, lights glowed, and he heard the blower, but no sound. The church was a half hour from home. By the time I arrived, there were limousines parked in front of the church, a bagpipe howling in front, and people pouring into the church. I raced up the stairs to the organ loft, verified that the organ was running, and the electric stop action was working. I went to the basement and found a card table sucked up against the blower intake. Easy fix. Here comes the bride.
John Leek and I worked for a Polish Catholic Church on the west side of Cleveland. At the end of each tuning day, we presented ourselves at the rectory where the pastor would ask what we like to drink, duck back inside, and return with bottles of booze and cash to pay for the tuning. It seemed like kind of a loose way to run a ship.
Gustatory tuning
When scheduling a slate of tunings, I kept two criteria in mind, geographic proximity and what would be for lunch. Some organs would command a full day a few times a year. On other days we might visit two, three, or even four organs. Wendy and I lived in the Charlestown Navy Yard for ten years, a neighborhood of Boston across the harbor from the city where our neighbor was the USS Constitution, the oldest commissioned warship in the United States Navy. The Episcopal church in Charlestown was a service client with a neat little two-manual tracker organ. The organist there was a pal who was happy to hold notes, so that church was often an easy fourth stop of the day, getting me home in time for cocktails.
We had pairs of churches close to each other, each pair associated with a nice place for lunch, and I scheduled things so we had a variety of lunches. You would not want to have Mexican food two days in a row. We had a nice range of cuisines including Vietnamese (Harvard Square), Chinese (Boston University), Mexican (Worcester and Quincy, Massachusetts), Thai (Back Bay, Boston), Italian (Newton, Massachusetts), fried seafood and clam chowder (Cape Cod)—you get the idea.
Several of the organists of churches where we tuned often joined us for lunch, allowing fun conversations about what was going on in each church. I paid attention to what music was out in the choir rooms, what music was piled around the organ console, and what notices were posted on bulletin boards, so I had a comprehensive working knowledge of dozens of church music programs, all of which informed my work at the church where I was music director (as well as organ tuner).
Watch your step.
If you are paying attention, maintaining a lot of instruments is an education in organ building. It is a delight to work on a well-designed, well-engineered, well-built, and well-voiced organ. How easy it is to move around inside an organ and how easy it is to reach things that will always need attention is an important reflection on the quality of an instrument. No church wants to hear that an ordinarily simple repair would involve a week of dismantling other parts of the organ to gain access to the offender.
I maintain an organ in a large, central building in New York, built by a widely known and respected builder, that includes a common brand of solid-state controls for switching and combination actions. I was dumbfounded when I realized that the “brain” of the system was installed inside the console in a way that the interchangeable circuit boards could not be removed, making normal maintenance impossible without removing the entire unit from the console and stressing the immense jumble of ribbon cables that connect it to the organ. That Medusa-like tangle made my blood run cold.
We like to see neat wiring on junction boards in an organ, every wire in its proper place, soldered evenly, tied and dressed so it will be easy to troubleshoot in the future. Sometimes we are confronted by tangled messes of wires that show no order or logic. The weight of cables is hanging directly from delicate contacts, odd wires are laced about, and there is no logic from one row of pins to another. You just know by taking a glance that the mess will be unreliable, and it is difficult, sometimes hopeless to dig down to find the wire in question.
§
Organs enclosed in free-standing cases are often among the best built, but they can be difficult to service because one must reach everything from walkboards outside the back of the case. If there are seven or eight stops on the Great, that tin façade seems a mile away, and the treble pipes of the Principal down at rackboard level are often out of reach, especially if they are cone-tuned so you cannot use a long tuning iron. Staying with the Great as example, you might find three or even four reeds at the back of the windchest (16′ Trompette, 8′ Trompette, 8′ Vox Humana, 4′ Clarion), and two or three compound stops buried behind them (Mixture VI, Scharff IV, Sesquialter II). It is a stretch to reach over those hulking reeds to get to those tiny mixture trebles. As you get used to such an organ over the years, you realize which big reed pipes you can remove to gain the angles needed.
The lowest notes of the 8′ Gedeckt are probably tubed off the main chest and mounted on the case wall, but they are far away, and they can be especially tough to handle because if the pipe is sharp you must reach the pipe with two hands, one to hold the pipe and the other to move the cap higher on the pipe. Sometimes I asked a helper to hang on to my belt to keep me from falling into the pipes.
Ernest Skinner cared a lot about the serviceability of his organs. Stable ladders, ample walkboards between windchests, and sturdy tuning benches above the pipes make tuning comfortable and safe for both the tuner and the instrument. There are no surprises like treacherous spongy boards underfoot as you pass through the organ. We hope for this quality in any organ, but some are spooky. You must figure out what can bear your weight. A good rule for when you are walking somewhere in an organ where you have not walked before is do not put all your weight on anything without trying it gently first.
Over the years
Over years I learned the priorities and interests of the many organists I worked for. For one, I would always double check all the expression boxes, shutters, motors, and mechanisms, knowing that he used them constantly and considered them an important part of his playing. For another, it might be the trebles of the flutes, making sure that solo stops like orchestral reeds or harmonic flutes were in tune with each other, especially if there were antiphonal pairs of similar stops.
I learned the strengths and weaknesses of each organ, which reeds would need attention, the trebles of stopped wood flutes, keyboard contacts, and recalcitrant tremulants. I also learned which firms build organs that are reliable, easy to maintain, and, most important, beautiful. In my conversations with many organists, I learned what features of an organ made it most useful to the working musician, and how effectively it led the church’s music, especially congregational singing.
It is fun to reflect on how much easier that work is in the age of the mobile phone. Thirty years ago, while on the road doing service calls, I had to find pay phones to let people know if I was running late and to maintain my schedule. I had a memorized list of gas stations that had phone booths that were likely to be available. If I had to call a vendor with questions about the systems of an organ, I would ask in the church office if I could use the phone and sit facing away from the secretary so I could not see her angry glare when I had tied up the church’s only phone line for too long. Today you have your phone with you all the time (and it has a flashlight). If you are explaining something to a technician at Peterson Electro-Musical Products, Organ Supply Industries, or one of our other valued suppliers, you can snap a photo and send it instantly. What could be easier?
In several churches where I tuned for decades, I outlived generations of staff members and could be relied on to find a stepladder, to know where the controls for HVAC equipment were located, and how to program the electronic tower chimes. (I like to call them Bongatrons.) It is fun to think back on tens of thousands of miles driven, thousands of satisfying repairs—it is fun when you solve a knotty problem and get an organ back on its feet—endless conversations with musicians, clergy, and staff members. I had running jokes and teases with people I saw twice a year.
What an adventure, what a privilege, and what an education. Thanks for the great ride.