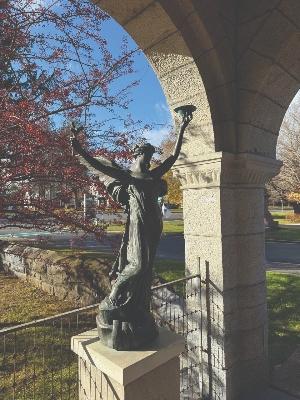
Where it all begins
When I was growing up, my family had a summer home on Cape Cod where we grew enamored by a brilliant potter about five miles away. Scargo Hill Pottery was founded by Harry Holl, and over fifty years later his daughters still make the characteristic shaped dishes, mugs, and vases we grew to love. Harry worked with white porcelain that he accented with dark spots made by mixing the black sand from a specific nearby beach into his clay. He accented them with vibrant glazes. Our household and those of my siblings are rich with Harry Holl pieces; it is lovely to eat daily meals off such beautiful art and to have such ornaments on our walls and shelves.
From its beginning Scargo Hill Pottery has had a wonderful, almost spiritual side. There is a row of potter’s wheels in a sunlit spot with a translucent fiberglass roof and no walls, where you can stand and watch the artists create their products. I still think it is magical to watch a turned shape emerge from a lump of clay and become a useful vessel. From my earliest teenage years I have been in love with places where beautiful things were made. On many a summer evening, we piled into the car after supper to visit Harry and his troupe. The lovely outings were capped by a stop at Sea Breeze soft-serve ice cream conveniently located along the route.
§
The 150-acre summer estate of sculptor Daniel Chester French (1850–1931) is a couple miles from where we live in Stockbridge, Massachusetts. French is perhaps best known for two iconic public sculptures, The Minute Man statue in Concord, Massachusetts, near “the rude bridge that arched the flood,” and the monumental statue of a seated Abraham Lincoln in the Lincoln Memorial in Washington, D.C. He bought the property in 1896 and immediately commissioned the construction of a studio that became his principal workspace for the rest of his life. At that time there was train service from New York to Stockbridge; the Stockbridge station, long out of use, still stands just a couple miles from Chesterwood.
The studio is situated close to the house and has large glass windows providing plenty of natural light inside that feature broad views of Monument Mountain and the rest of the southern Berkshires. The principal work room is twenty-nine feet by thirty feet with twenty-six-foot-high walls allowing enough space for monumental equestrian statues. Since most of French’s work was to be installed outdoors, the design of the building included a working platform on railroad tracks with large doors that allowed him to move a massive work in progress outside so he could view it in natural light. He was so eager to work in the beautiful new space that he moved in two weeks before it was complete. The building included a reception room where he could receive potential clients and where his family had afternoon tea when the weather would not permit using the house’s grand south-facing porch.
The Minute Man was completed in 1875 for the centennial of the start of the Revolutionary War, before French acquired Chesterwood, but the Lincoln Memorial was completed in 1920. French designed Lincoln’s statue at Chesterwood, and a six-foot model is on display there. The full-scale statue was carved by the Piccirilli Brothers whose studio was on 142nd Street in the Bronx, New York. A four-foot bronze statue of a winged angel by Daniel Chester French, The Spirit of Life, stands in a portico at Saint Paul’s Episcopal Church in Stockbridge.
A visit to Chesterwood is an inspiration. It is thrilling to think of the wealthy and powerful people who traveled there to commission public art, and wonderful to imagine the brilliant and prolific artist toiling in the lovely studio in that bucolic setting, surrounded by family and friends.
§
Another iconic artist’s studio is within walking distance of our house in Stockbridge. Norman Rockwell had been living in Vermont when his wife began treatment at a prominent psychiatric hospital in Stockbridge, and Rockwell moved his family there in 1953. His first studio in this town was behind a large plate-glass window in the central storefront of Stockbridge’s Main Street, directly above the Back Room Rest, familiarly known as Alice’s Restaurant of Arlo Guthrie fame. He later built a free-standing studio with plenty of natural light on South Street. When the present building of the Norman Rockwell Museum was opened in 1993, the studio was moved to the new site where museum visitors can go inside to see Rockwell’s easels, paints, brushes, props, and tools.
Many hundreds of Norman Rockwell’s large-scale paintings were featured on the covers of The Saturday Evening Post and are inscribed in the artistic minds of millions of people around the world. I have been moved many times by sitting on the bench and playing the keys upon which the giants of organ music sat and played—Widor, Dupré, Saint-Saëns, Fauré, and so many others. It is equally moving to see the stool on which Rockwell sat while painting his beloved three-dimensional self-portrait, his iconic Rosie the Riveter, and The Runaway.
Our place in Stockbridge backs up to the cemetery where every morning I walk Farley the Goldendoodle through the cemetery, past Norman Rockwell’s grave to the adjoining Naumkeag estate, a great place for him (Farley) to be off leash for his morning constitutional. Norman is there with two of his wives, his gravestone festooned with tubes of paint, paintbrushes, and little trinkets left in tribute to his marvelous career and influence on our cultural life. Our granddaughter has been swept up by Norman-mania, being sure to visit him each time she visits us.
That Ingenious Business
In 1990 the Pennsylvania German Society published a book by our late colleague, friend, and organ builder, Raymond Brunner about the Pennsylvania German organbuilders Philip Bachman and David Tannenberg, among many others. These were some of the first organbuilders active in the United States, and a few authentic examples of their eighteenth-century American-built organs are still extant. As the organ was the most complex device built by humans at that time, the phrase “that ingenious business” evolved around that local industry. Now we are surrounded by technological marvels—no eighteenth-century organbuilder could have imagined mobile phones, flat-screen televisions, or nuclear submarines, but the pipe organ remains one of our fascinating achievements.
Among my many pleasures of working with the Organ Clearing House is visiting the workshops where pipe organs are built. We have working relationships with many of the country’s fine organbuilders as we help them with their projects, providing truck transportation, rigging and hoisting, assembly and disassembly. I have been in dozens of organ shops both here and abroad, and I always marvel at the creativity and dedication of the people in them. My first shop visits were open houses at Fisk and Noack in the 1970s when I was in high school. Organbuilder George Bozeman was an early mentor. I sang with his wife, Pat, in the choir at my home parish, and they were generous, taking me to those magical places to see organs nearing completion and ready to be dismantled and shipped. My high school organ teacher John Skelton also shared those wonders with me.
My first experience working in an organ shop was the summer of 1975, between my freshman and sophomore years at Oberlin, when I spent those months in the workshop of Bozeman-Gibson & Company. The shop was in Lowell, Massachusetts, in a building previously occupied by organbuilder Rostron Kershaw, and I spent my first day as a nascent organbuilder in the parking lot with sawhorses, façade pipes, Zip-Strip, hose, bucket, and rubber gloves. Oh, the glory of it. The parking lot was shared with a guy who transported chickens on a flatbed truck stacked high with wooden coops. I do not think he raised the chickens. I guess you would say he was trafficking in chickens, but the truck clattered in and out, and he was always happy to take the sawdust from the dust collection system to line his coops. Once when the bin was empty, he asked if we would plane some wood.
That summer, the company was working on the restoration of the wonderful 1848 George Stevens organ in the First Church of Belfast, Maine, and the installation of a new organ in the Federated Church of Castleton, Vermont. What an adventure it was for a nineteen-year-old enthusiast to spend the summer driving around New England, staying in motels, eating with a meal allowance ($1.50, $2.50, $3.50 for breakfast, lunch, dinner), and having my first hands-on experiences with organs. I returned the following summer and helped install the Bozeman-Gibson organ on Squirrel Island, an exclusive summer community off the Maine coast near Boothbay Harbor, six miles as the crow flies from our house in Newcastle.
Nearly fifty years later, I still marvel at the magic. I have a sense that it is improbable that we would be allowed, even encouraged to make something as otherworldly as a pipe organ. The variety of skills involved seems endless. An organbuilder is an architect, carpenter, woodworker, steel worker, electrician, leather worker, metallurgist, sculptor, acoustician, and musician. A comprehensive workshop houses familiar machinery like saws, drill presses, and planers, milling machines, and welders, and equipment you are not likely to see elsewhere like the cauldrons for melting soft metals, and especially the tables for casting the long sheets of metal used to make organ pipes.
François-Lamathe Dom Bédos de Celles de Salelles (1709–1779, we know him familiarly as Dom Bédos) was a Benedictine monk and organbuilder who published a monumental treatise, L’art du facteur d’orgues (The Art of Organbuilding) in 1778. Its volumes are packed with elegant engravings showing all facets of the trade including tools, workbenches, mechanical actions, wind systems, windchest layout, and clever exploded views of the interior of a complete organ. The cauldron and casting table are clearly illustrated, just like those found in modern workshops. I imagine that Dom Bédos built lovely big bellows to help tend the fires under his melting pot. Of course, today’s organbuilders do not have to stoke wood fires to melt their metal; a gas burner does the trick in a trice. Flipping through the pages of the good monk’s treatise shows how little has changed in the craft in nearly 250 years.
But how much has changed
Aristide Cavaillé-Coll (1811–1899) is revered for the tremendous legacy of pipe organs his company produced for such churches as Notre-Dame and Saint-Sulpice in Paris, but along with over 500 instruments he was honored for the invention of the circular saw blade. How we take them for granted now. I still have the table saw I bought in 1987 when I started the Bishop Organ Company, and I have ten or fifteen circular blades for it, some of which have specialty uses. Most of them have carbide steel tips on the teeth that stay sharp through miles of cuts. Think of spending a day making thousands of wood trackers, maybe ten feet long with a cross section of 1.5 by 8 millimeters. You stand at that saw all day making cut after cut. It is monotonous, but you cannot let your mind wander because you really want precise cuts, and you want to keep your fingers. (I still have all mine after forty-nine years behind the saw.)
As repetitive and precise as that task is, besides the circular saw blade we have the added luxury of a shop-wide dust collection system. The good monk had none of that. He cut those trackers by hand. My mentor John Leek taught me to make long, straight saw cuts and to plane a board flat and parallel by hand before I was free to use the machines. It was a great learning experience. I hardly ever did that again, but that helped me imagine the time, effort, and concentration it would take to make an organ full of trackers by hand. Or think of making a keyboard by hand with sixty long straight cuts. When I worked for Angerstein & Associates in Stoughton, Massachusetts, in the 1980s, I built the four keyboards for the new console of a large organ in Corpus Christi, Texas, and I remember that the lowest few naturals of the bottom keyboard were a little wider than the others. I have not noticed anything like that in any of the historic organs I have visited. I recently had a fun exchange about that with the good people of the Red River Organ Company who maintain that organ now.
I had a root canal a couple months ago—not my first choice of how to spend a morning, but I had a good laugh with the endodontist when I told her that the smell of grinding my teeth reminded me of standing at a table saw cutting ivory or cow bone for keyboards. I was impressed by the array of teeny cutting tools she used with a compressed-air motor to drill so delicately into the roots of my teeth. She spoke softly to her assisting technician, “A 14, please,” “A 12, please.” Between gulps, I asked if those were bit sizes. Yes, but of course the numbers refer to length in millimeters, not diameter.
Drill sergeant
The art of organbuilding can be defined as the art of knowing where to put the holes. Each pipe in an organ needs at least two holes, a toehole to stand in and a rackboard hole that stands it up straight. In a slider chest, there are two more holes for each pipe, one in the windchest table and one in the slider. A ten-stop, sixty-one-note slider chest has 2,440 holes. Those in the windchest, sliders, and toeboards range from about ½ inch to 1¼ inches with some larger oval holes because the holes cannot be larger than the travel distance of the slider. The rackboard holes range from about ½ inch to 3 inches or more, with the largest pipes supported by felted “scallop” racks higher up on the pipe. Dom Bédos’s windchests did not have sixty-one note compasses, but he still had to drill thousands of holes just to hold up and blow the pipes. There are usually at least two holes in each key of a keyboard, one for a balance pin, and one for a guide pin. He built an organ with five manuals, each with fifty-six notes—that is 560 holes. He used a “bit-and-brace” drill with handmade bits. What skill, precision, and plain hard work
was involved.
I have thousands of drill bits in my workshop—twist bits, multi-spur bits, Forstner bits (guided by the outside edge rather than a center pin), countersinks, and spade bits. To turn those bits, I have a little fleet of drill motors with rechargeable batteries and the drill press I bought with the table saw.
With your own eyes
If you have not already, I hope you all get to visit an organ shop sometime. Most companies that build new organs love to host open house events when an organ is ready to be shipped. Those events typically include food and drink, displays about how certain tasks and processes are accomplished, and the added excitement of visitors from the church where the organ is going. If you are planning a trip to an area that is home to an organ company, get in touch through their website or give them a call to ask if you might visit. At least they will put you on a mailing list for the next open house. There is an old gag about sausages—you might love to eat them, but you do not want to watch them being made. Watching the artisans at work in an organ shop will inspire your love of the instrument and will inspire your musicianship. It’s nothing like sausages.