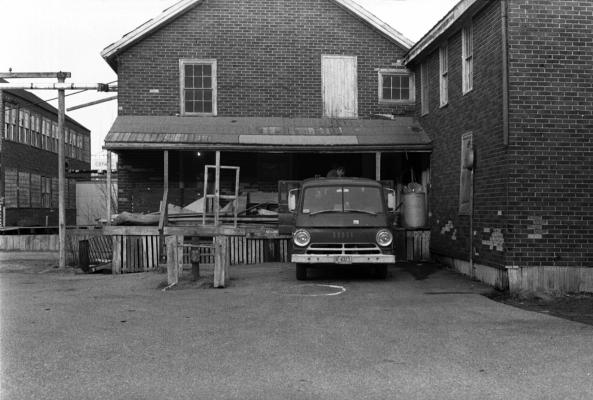
Making things
Before we moved to New York City, Wendy and I lived in the Charlestown Navy Yard in Boston. Our building had been an electrical warehouse for the Navy Yard, which actively built ships from 1801 until 1975. It is a building that once had forklifts racing around inside, so the ceilings were nice and high. Our living room windows looked across Boston Harbor to the Coast Guard base, the Custom House, and into the heart of Boston, and we had “cocktail chairs” in front of the sixth-floor windows where for ten years of evenings we watched the Wednesday night sailboat races, foolish non-seamen in overpowered speed boats, and the constant flow of commercial shipping including the mammoth Liquid Natural Gas tankers whose captains looked us in the eye from their towering bridges.
The Navy Yard still functions formally as a military base as it is home to the USS Constitution, the Navy’s oldest commissioned warship. One of the oldest buildings in the Charlestown Navy Yard is the Ropewalk, built of heavy granite blocks and completed in 1838, where most of the rope used by the United States Navy was made until it closed in 1970. Imagine the floor plan of a building designed expressly for making rope, over 1,300 feet long and 45 feet wide. That is more than twice the length of the Cathedral of Saint John the Divine in New York City. One of my walking routes included the length of the building that is almost exactly a quarter mile, and I wondered what sort of machinery was used for all that twisting and winding. Take a look at this video to see an antique ropewalk in operation: https://www.youtube.com/watch?v=2M5mo2I2c0Q.
The Maine Maritime Museum is on the site of the Percy & Small Shipyard in Phippsburg, Maine, where dozens of wooden sailing ships as long as 444 feet were built through the nineteenth century. The museum is adjacent to the Bath Iron Works, famous for having launched a new destroyer every twenty-five days during World War II with Rosie the Riveter riveting a river of rivets. Now, the Bath Iron Works is known for producing new Zumwalt Class destroyers.1 The museum includes a diorama of the J. T. Donnell Ropewalk in Bath, Maine, which adjoined Percy & Small and provided the shipyard with rope. When you are building six-masted schooners you need lots of rope, and the ropewalk was a wooden structure some 1,200 feet long with a stationary steam engine at one end to power the equipment. A legend by the diorama shares a quote from The Bath Times in 1883:
John D. Smith of this city, a ropemaker at the J. T. Donnell ropemaking factory, has done a large amount of walking in his life. He is sixty-four years old and has worked at ropemaking for forty-five years working as a handspinner, in which time he has spun 69,940,666 fathoms [six feet] of thread, walking ten miles a day to do this, which in the forty-five years of spinning would aggregate the enormous distance of 140,400 miles [six day weeks for forty-five years]. Of this, one-half the distance has been accomplished walking backwards . . ., the equivalent of backing a distance nearly equal to around the world three times.
Reminds me of the quip about Ginger Rogers, who did everything Fred Astaire did, but backwards in high heels. (Mr. Smith probably didn’t wear high heels.)
Color my world with a spring in my step.
Children have grown up watching Sesame Street since 1969. I was thirteen, and I had just landed my first paying job as a church organist, so I was above “strings and sealing wax,” but fifteen years later the show was a staple for my sons. As a lifelong machine geek, I loved the segments about how things are made, all of which are easy to find online. There is a humdinger about making crayons accompanied by a brilliant musical tone poem. My favorite is “Peanut Butter,” the jazzy flapper-style song written and performed by Joe Raposo that accompanies a tour through a peanut butter factory featuring smiling workers in what look like Krispy Kreme hats pushing the important looking buttons to run the machines. I especially like the shot of a broad stream of peanut butter oozing out of a press and into the pipes that lead to the jars as Raposo sings, “he keeps it pumpin’ through the pipeline like a peanut-butter-pumper should.” What great teaching.
Among the many factories I have toured are a potato chip factory (no free samples but a gift shop at the end), a major brewery (free samples), and an auto assembly plant (no free samples). When I was working for John Leek in Oberlin in the early 1980s, we were building an organ for Saint Alban’s Episcopal Church in Annandale, Virginia, and we planned to make the sliders in the style of Flentrop, double sliders of Masonite, the holes connected with little leather tubes, with hundreds of springs between them to press the two sliders against chest table and toeboard.
No hardware store could have supplied the thousands of identical fine coil compression springs we would need, and we found the Timms Spring Company in Elyria, Ohio, perfectly situated to supply the several large car makers in the area. The company had around twenty employees, most of whom were tool-and-die makers, and the factory was full of machines. Timms would receive an order from a car maker for a million specialized springs, and a machine would be set up to make them that would then run on its own for a week or two gobbling up coils of wire and filling bins with springs.
We brought a sample (probably borrowed from a Flentrop organ we serviced) and met Bill Timms, the third generation of the spring-making family. Bill gave us a fascinating tour around the factory explaining the purpose of each spring being made and gave us lots of free samples. We watched as a toolmaker set up a simple jig to copy our spring by hand and returned a week later to pick up our order.
Organ shops
Visiting a pipe organ workshop is a special treat, educational and eye-popping for both the layperson and the organbuilder. I have visited dozens of shops across the United States, in Great Britain, and in Europe, and while I like to think I know a lot about the building and history of organs, I always learn something fresh. It is fun to compare how different workshops approach common tasks like building windchests and reservoirs, racking pipes, or making wind connections. Different firms have particular products or processes they have developed of which they are particularly proud, different firms have thoughtfully designed console layouts that distinguish them from others, and different firms specialize in different types of windchest actions.
The organbuilding firm of Harrison & Harrison in Durham in Great Britain moved into a new well-equipped building in 1996, where one can pass from one department to another witnessing the deep skills of a venerable firm at work. Immediately upon entering the building, one sees displayed in an elegant frame a cast gold medallion and a letter from Queen Elizabeth II dated November 20, 1997:
Prince Philip and I are delighted and deeply impressed with the marvelous work of restoration of the fire damaged area of Windsor Castle. Being anxious to show our appreciation of the skill and dedication, which you and others have devoted to it, we have this special medallion struck to mark the completion of the restoration and it comes with our grateful thanks. [Signed] Elizabeth R
The organ involved in the Windsor Castle restoration is a new instrument of seven ranks in the “Private Chapel” built in 1997. Harrison & Harrison has produced a vast list of important and well-known organs including those at King’s College, Cambridge, Durham, Ely, and Exeter cathedrals, Royal Festival Hall, Westminster Abbey, Winchester Cathedral, and Saint George’s Chapel at Windsor Castle. We have all seen several of those organs on television. I especially like the thought that the marvelous organ in Westminster Abbey was built for the coronation of George VI in 1936—imagine the feelings of nervousness, expectation, and pride those organbuilders must have felt. When I visited that workshop in 2016, the organ from King’s College was in the shop for renovation. I got a kick out of noticing the pipe crate labeled “Solo Tuba,” the stentorian tenor melody under a certain verse-six descant ringing in my ears. My visit to Durham included a tour of the H&H cathedral organ with operations manager Jeremy Maritz, setting the standard that one Double Open Wood Diapason is not enough. There’s one on each side of the choir, one of which goes to 32′.
The workshop of Taylor & Boody in Staunton, Virginia, is housed in an old public school building with huge windows and high ceilings, a spacious, airy, and well-lighted place to work. Since the firm was founded in 1979, they have built nearly ninety mechanical-action organs, developing a great reputation for excellent workmanship. Most of their instruments show the influence of the North European Baroque, with tonal schemes that allow lots of versatility. They ensure their own supply of high-quality wood by harvesting carefully chosen trees, cutting them into lumber in their sawmill, and drying them in the adjacent kiln. It is a kick to walk around the yard among stacks of lumber designated for particular opus numbers. When Wendy and I visited there in 2009, we stayed in the apartment above the sawmill and saw the huge oak logs destined to become the wonderful innovative organ for Grace Church in New York City. We have a fond memory of John Boody showing us his “free-ranging” moveable chicken coop and giving us fresh eggs for our breakfast.
Taylor & Boody is one of a number of firms that casts pipe metal to their own specifications. Watching the casting box being pushed down the long table leaving a shining pool of molten metal behind is something special to watch, especially the magic moment a few seconds later when the elixir turns into solid metal. The transformation from liquid to solid is instantly apparent. It seems like alchemy. The idea that freshly cast metal and those huge oak logs would soon be a pipe organ epitomizes the craft we celebrate.
Schoenstein & Company in Benicia, California (the gateway to Napa Valley), mirrors the dedication to quality at Taylor & Boody, building organs in a style worlds apart. They are widely respected for the sophisticated tonal structures with versatile orchestral voices, double expressions, and powerful solo voices, and their elegant consoles are superbly appointed with accessories unique to them. One look at an expression shoe and you know it is a Schoenstein organ. Schoenstein purchased their building in 2004, leaving the 1928 workshop in downtown San Francisco. They have since raised the ceiling of one room to forty-two feet, creating an erecting space, and added a wing for pipe shop, voicing room, and archives. The attention to detail is unparalleled—the company logo is stenciled on the propane tanks of the forklift. Jack Bethards and his skilled staff are working with a clear vision, strongly influenced by the fabled companies of the early twentieth century. The firm has just completed a grand organ with four manuals and seventy stops, including a 32′ metal façade, for the new Basilica of Mary, Queen of the Universe in Orlando, Florida.
Glatter-Götz in Pfullendorf, Germany, is housed in a new facility built for them shortly after the famous Walt Disney Concert Hall organ was completed. When I was there in the fall of 2019, vast fields of sunflowers were in bloom as I drove to the little village. There is a one-story façade facing the street, effectively concealing the two-and-a-half story rear of the building. There is a huge slanted roof covered with solar panels allowing second floor offices at one end of the building and lofty open areas with plenty of space for erecting organs and handling long lumber. You enter at the end of the building where the lunchroom is to the left, the voicing room to the right, a corridor ahead to the workshops, and a long stairway to the suite of offices. All the workspaces have lots of big windows, plenty of clean bench space, storage areas for lumber, and fasteners, leather, and organ parts are neatly organized. There were two organs being assembled when I visited, one for Marietta, Georgia, and another older instrument being renovated for a music school in rural Russia. The next-door neighbor is a farm implement dealer, so a parade of tractors runs back and forth outside.
Paul Fritts & Company occupies an attractive architect-designed (craftsman style?) building in Tacoma, Washington. I visited there in April 2019 with my colleague Amory Atkins (it was Amory’s birthday) while we were installing an organ at the University of Washington. Organs for the First Lutheran Church of Lorain, Ohio, and the Chapel of Hillsdale College in Hillsdale, Michigan, were standing in the shop when we visited. The Lorain organ was complete and ready for shipment. I was especially impressed by their CNC (computer numerical control) router. It is housed in a separate building to separate the considerable noise from the rest of the workshop. It is as big as a bus and capable of drilling entire windchest tables with dozens of different hole sizes, milling the many sizes of wood reed boots, and mitering wood windlines, all by programmed computer control. The machine chooses and inserts bits as necessary and calmly progresses from one task to another while the organbuilders work on other tasks in the workshop across the way. We had a birthday dinner with Paul and college pals Bruce and Shari Shull in Tacoma, then drove back to our hotel in Seattle in a wicked rain squall, crowned by a complete double rainbow. Happy Birthday!
C. B. Fisk, Inc., moved into a new purpose-built facility in 1979. That building has been expanded significantly since, with tall erecting space added, and a large wing containing several department workshops. The first organ to be built and assembled in the new shop was Opus 68, a three-manual, twenty-seven-stop instrument for the Southwick Music Complex of the University of Vermont. Close to ninety new organs have been built in that building, which, like others I have described, is superbly equipped and spacious enough for nearly thirty people to be at work with all the tools and supplies they need.
Charles Fisk founded the eponymous company in 1961 in an old ropewalk building in Gloucester, Massachusetts. C. B. Fisk “lifer” Bob Cornell, who has been with the firm for fifty years, remembers that the ropewalk was actually built for making nets for the city’s fleet of fishing trawlers. (Remember George Clooney and Mark Wahlberg in The Perfect Storm.) There was a twenty-foot-high room at one end where organs could be erected, and an attached structure over 120-feet long where the nets had been made and the various workspaces for the organ company were placed. Bob remembered poison ivy growing through openings in the walls, and that the long floor slanted away from the tall building as the land sank into the nearby bog causing window frames to become trapezoidal. About ten people worked in that shop. The landmark organs for Kings Chapel in Boston (1963) and Harvard Memorial Church (1967) were built in the ropewalk.
What groundbreaking work happened in that shop as the innovative and Socratic Charlie Fisk, with a loyal group of disciples, dug into the history of organbuilding and developed the signature style that has been so influential. The company has now built over 150 organs in distinguished venues all over the world. Those fledgling organbuilders may not have walked 140,000 miles, but they sure changed the content of the industry.
Each of these companies has a well-developed website with photo galleries, opus lists, and workshop tours. Happy visiting. And buy good organs.
Notes
1. Just to show that the Navy can have a sense of humor, the first launch of the futuristic evil-looking Zumwalt class ships was the USS Enterprise commanded by James Kirk.
Photo:
The Fisk Ropewalk, moving day to the new shop, Charles Fisk loading the van (photo credit: Robert Cornell)