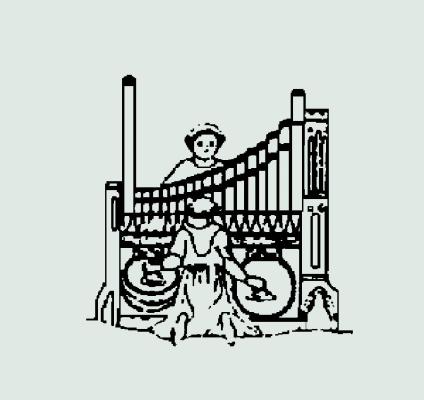
Alaska officials ponder
only road to Juneau
Juneau, Alaska, is currently accessible only by airplane or boat. The city of 31,000 is the capital of the state, but many Alaskans have never been there because of its remoteness. That could change a little if the state government’s plans for a 65-mile, $281 million highway survives in the federal transportation bill, The New York Times reported.
The highway would connect Juneau to the rest of the state’s highway system through Canada, but some residents vehemently oppose the idea. They like Juneau’s remoteness. If Alaskans wanted a more accessible capital, they could move it to Anchorage or another city, but several attempts over the past 40 years to do just that have failed. Even with the highway, the trip from Juneau to Anchorage would be 800 miles.
The planned highway is a proposal of Gov. Frank Murkowski and U.S. Rep. Don Young, who is influential in transportation policy as chairman of the House Transportation and Infrastructure Committee.
Critics say the road would cost too much and possibly take funding away from other needed infrastructure projects. They also say the proposed alignment would threaten bears and other animals in the Tongass National Forest and would be dangerous in winter because of avalanches.
A draft environmental study is scheduled to be released this month. If the highway is not built, Juneau will remain the only state capital that cannot be reached by car.
ARTBA grassroots program
wins Telly Award
The American Road & Transportation Builders Association (ARTBA) has won the 2004 Telly Award for the multimedia training program it produced this year to help construction-industry workers across the nation get involved in federal legislative advocacy in support of increasing federal transportation investment.
The prestigious award, founded in 1979, annually showcases the best work of the most respected advertising agencies, production companies, television stations, cable operators and corporate video departments in the world.
More than 10,000 entries from all 50 states and five continents are submitted annually. On average, only about 7% of those entries are selected as winners. The Telly Awards are affiliated with the Center for Creativity, an organization that was founded in 1963 to research and study advertising, design, production and journalism.
ARTBA developed “Mobilize! A Grassroots Legislative Action Program for Transportation Construction Firms,” which includes a 10-minute DVD, CD-ROM, PowerPoint presentation and instructional booklet. It is believed to be the first multimedia package developed by a national transportation association to facilitate grassroots training.
The program provides information about how decisions made by Congress and the White House affect the transportation construction market. It also offers employees tips on how to get involved in helping shape federal policies that will benefit their future livelihoods.
ARTBA engaged Washington, D.C.-based LAI Creative Media for the production work, and the DVD features innovative grassroots techniques that have been used successfully by Harrisburg, Pa.-headquartered Stabler Cos./PSI and by Oldcastle Materials Inc., which is located in Washington, D.C.
The association distributed nearly 1,500 kits to companies throughout the country with the goal of bolstering activities in support of a significant increase in federal transportation investment as part of the TEA-21 reauthorization.
Cement demand up in 1st quarter
Portland cement demand increased 14.8% in February, followed by a 23.8% increase in March, according to The Monitor, published monthly by the Portland Cement Association (PCA). On a seasonally adjusted annualized basis, March’s reading of 125.9 mmt is a single-month record. Year-to-date consumption is tracking 12% above last year.
Blended cement was rather flat in March at -0.3%. Year-to-date consumption is down 12.3%.
Masonry cement consumption increased 28.3%, following significant gains in January and February. Year-to-date consumption is 21.3% above 2003 levels.
Cement and clinker imports continued to grow at 7.9% in February and 11.5% in March. Year-to-date, imports are up 13.7% from the first three months of last year.
PCA’s statistics reflect the latest data from several government-issued reports.
Environmental streamlining
a success in marshland highway
Involving all the interested agencies early allowed the Federal Highway Administration and the Louisiana Department of Transportation and Development (LADOTD) to finish the environmental study of a replacement highway through a sensitive marsh area in just 44 months, according to a “Success Story” on the website of the American Association of State Highway & Transportation Officials.
The new Louisiana Rte. 1 will provide enhanced access to the vital oil, gas and fishing industries in the gulf area. It also will provide a more reliable evacuation route in case of a severe storm such as a hurricane while preserving the marshes that buffer the area from those gulf storms.
The new four-lane highway will replace an old two-lane structure. Instead of a lift bridge over Bayou Lafourche at Leeville, there will be a new fixed, high-rise bridge. The road will stretch 16 miles from Fourchon to Golden Meadow.
Ronald Ventola, chief of the Regulatory Branch of the New Orleans District of the U.S. Army Corps of Engineers, credited the FHWA and the LADOTD for understanding the sensitivity of the habitat and being willing to adjust the construction plan. He also gave the resource agencies credit for understanding the need for the highway and the lack of good alternatives.
One accommodation to the habitat was the decision to use “end-on” construction except for the high-rise bridge near Leeville. According to the end-on construction method, the heavy equipment working on Rte. 1 will sit on a platform on concrete piles instead of in the marsh. A crane on the platform will drive piles and place segments of the viaduct bridge then move to the next platform and repeat the process.
The FHWA and the LADOTD also undertook a study of the effect on the marsh grasses of the shade from the new structure.
The marshes are already threatened. In the past 50 years, 1,500 square miles of Louisiana’s gulf wetlands have disappeared through erosion and subsidence. In 2000, while FHWA and LADOTD were preparing the Environmental Impact Statement for Rte. 1, another 164 square miles of the salt marsh suffered a severe dieback of marsh grass. With the continuing erosion of the coastal marshes, the existing highway has become increasingly susceptible to flooding during storms.
The agencies that participated in the planning included the U.S. Coast Guard, the U.S. Army Corps of Engineers, the National Marine Fisheries Service, the U.S. Environmental Protection Agency, the U.S. Fish and Wildlife Service and others.
Those involved in the process said the cooperation and mutual respect among the agencies proved the U.S. DOT could streamline the environmental review process with the least effect on the environment.
The new La. Rte. 1 will become part of the National Highway System in view of its intermodal link to the U.S. energy supply.
Protection Tip of the Month
Many eye injuries on construction sites result from flying wood dust and other debris like paint chips, dirt and concrete particles. Solvents, paints and adhesives used in construction can be toxic to the eyes and skin. Eyewashes and drench showers should be in place to mitigate such hazards at heavy construction sites. Equipment ranging from bottle eyewashes through portable stations to plumbed fixtures is available to meet the unique needs of your work site. And an updated American National Standard for emergency eyewash and shower equipment includes minimum performance requirements and installation, maintenance and training specifications. ANSI Z358.1-2004 may be ordered by contacting ISEA, 1901 N. Moore St., Suite 808, Arlington, VA 22209 or 703/525-1695 or visit www.safetyequipment.org.
HIGHWAY NAMES
IN THE NEWS
Association news >>>>
JCB Inc., Savannah, Ga., has restructured its North American sales and marketing: Bob Wright will head dealer development, remarketing, governmental sales and business planning; Bruce Narveson has been named vice president of sales for the Northeast region; Jan Nielsen is now general manager for the Central region; David Hahn has been named general manager of the Western region; Ron Fulmer is now general manager for Canada; and Gordon Henderson will continue as vice president of sales for the Southeast region.
Meris Gebhardt has joined the sales staff at Tracker Software Corp., Snowmass Village, Colo.
PBM Concrete, Rochelle, Ill., has merged into J.W. Peters, Burlington, Wis.
JLG Industries Inc., McConnellsburg, Pa., has made a binding offer to purchase Delta Manlift, a Tonneins, France, subsidiary of the Manitowoc Co. Inc. JLG also will acquire certain intellectual property and related assets that will allow it to relaunch selected models of Manitowoc’s recently discontinued Liftlux aerial work platforms at a later date. Scott Brower has been named vice president of marketing and market development at JLG.
Anthony E. Fiorato, president and CEO of Construction Technology Laboratories, Skokie, Ill., has been elected president of the American Concrete Institute, Farmington Hills, Mich.
The American Society of Safety Engineers, Des Plaines, Ill., has been named secretariat of the American National Standards Institute’s A10 Accredited Standards Committee on Safety Requirements for Construction and Demolition Operations, which aims at protecting workers and the public.
Vernon Wehrung, president of Modern Precast Concrete, Ottsville, Pa., has been elected chairman of the board of the National Precast Concrete Association, Indianapolis.
Tim Gillespie of Sika Corp., Lyndhurst, N.J., has been voted a fellow of the International Concrete Repair Institute.
Engineering news >>>>
C. Diane Matt has joined Women in Engineering Programs & Advocates Network as the first executive director.
Arthelius “Trip” Phaup, P.E., is relocating to Ralph Whitehead Associates’ Atlanta office to assume the duties of Transportation Group leader.
James Rowan has been named area manager for the Philadelphia office of Parsons Brinckerhoff Quade & Douglas Inc. Parsons Brinckerhoff has appointed Mary Clayton North Carolina area manager.
HNTB Corp., Kansas City, Mo., has appointed Mary Axetell senior vice president. The firm also has appointed four vice presidents: Uri Avin, Rhett Leary, Jim Riley and Mark Urban.
Ben Berra of Skelly and Loy Inc., Harrisburg, Pa., has been designated by the U.S. Fish and Wildlife Service and the Pennsylvania Fish and Boat Commission as a qualified bog turtle surveyor in Pennsylvania.
Raymond F. Messer, P.E., has been named by Texas A&M University’s Department of Civil Engineering as the recipient of the Friend of the Department 2004 Award. Messer is president and chairman of the board of Walter P. Moore.
Horner & Shifrin Inc., St. Louis, Mo., has named Jamie McVicker, P.E., transportation/civil project manager, as an associate of the firm. Lisa E. Fennewald, P.E., also has been named associate and promoted to assistant project manager.
KS Engineers, Newark, N.J., has added Eugene W. Little and Eileen Della Volle as vice president of business development.
URS Corp., Seattle, has named Dave Alford manager of the company’s Pacific Northwest region.
Michael D. Spitz, P.E., has joined McMahon Associates Inc. as a senior project engineer in the firm’s Cape Coral, Fla., office.
At Carter & Burgess Inc., Kenneth Carper, P.E., CPSWQ, has joined as a vice president and unit manager of the Raleigh, N.C., Transportation Programs Unit, and James “Woody” Woodruff, P.E., has joined as a senior project manager in the Salt Lake City office.