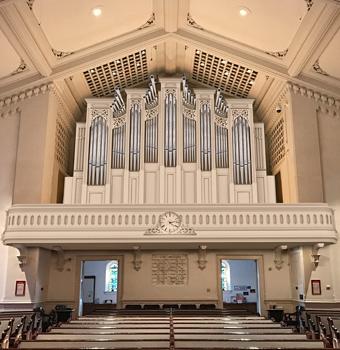
Létourneau Pipe Organs has signed a contract with Market Square Presbyterian Church, Harrisburg, Pennsylvania, to rebuild the church’s pipe organ. The project will begin with the removal of the entire instrument, including the Positiv division currently on the gallery rail, to allow for reconstruction of the church’s two organ chambers. The existing electro-pneumatic windchests will be fully reconfigured to suit the new tonal plan while a new four-manual console will be built. Similar to the present, part of the rebuilt organ will be displayed within a new case across the back of the church’s gallery.
Nearly three-quarters of the rebuilt instrument’s pipework will be restored from the church’s previous organs by Aeolian-Skinner Organ Co. (Opus 1048, 1947) and M. P. Möller (Opus 11805, 1991). When complete during the third quarter of 2020, this pipe organ will be the firm’s Opus 136.
For information: http://letourneauorgans.com.