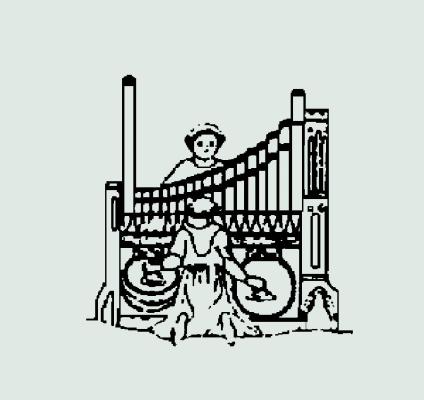
M. L. Bigelow & Co., Inc.,
American Fork, Utah
St. Paul Lutheran Church (ELCA), Davenport, Iowa
“What’s the largest organ you guys have built?” It’s a question organ builders hear often, and there are different ways to answer it. This time, the fact that two 53-foot semi-trailers were required to transport it allowed us to answer honestly, “This one,” even though it has fewer ranks than our magnum opus. In any case (no pun intended), 42 ranks is a large number for any two-manual organ.
The 36-foot-tall freestanding case takes a commanding position at the front of the new sanctuary, but ingenious architecture by the Groth Design Group (Cedarburg and Madison, Wisconsin) preserves a focus on the altar and other religious elements. Robert Mahoney was the acoustical consultant, and the results are excellent for music and more than adequate for speech.
A quick look at the stoplist reveals complete principal choruses with sub-octave foundations for all three divisions, and a good selection of voices at unison pitch. The Open Bass, utilizing pre-existing pipes and chests, and the Chamade successfully extend the dynamic range into territory previously unexplored by Bigelow.
The swell box is located at impost level, where it speaks directly to the choir, which stands on risers immediately in front of the organ. The Great division occupies the upper portion of the case. Pedal flues and reeds reside on separate chests on either side of the swell box. Carbon fiber rods, 18 feet long, make up the majority of the tracker runs to the Great. All other trackers are cedar, except for the long horizontal pedal trackers made of basswood. Electro-pneumatic action is employed for the Open Bass, the eleven largest pipes of the Subbass, Præstant and Principal pipes at the lower façade level, and the Chamade; electric pull-downs are used for notes 25–32 of the Præstant 16′ and for the two Pedal duplexes in the Swell; otherwise all key action, including couplers, is mechanical. Stop action is electric and connected to a Laukhuff 60-level memory and piston sequencer. Two retractable flat screen video monitors give the organist a good view of the choir director and the altar area.
Artisans of Bigelow & Co. who participated in the project were Michael Bigelow, Katherine Bigelow (daughter), Amy Carruth, David Chamberlin, Dustin Cottongim, Felipe Dominguez, Robert Munson, Melanie Smith, and Shayne Ward. Metal pipes were made by the firms of Stinkens, Giesecke, and Schopp. Tonal finishing was conducted by David Chamberlin and Michael Bigelow, assisted by Katherine Bigelow. Logistics of the installation, which spanned over five months, were wonderfully managed by Melanie Sigafoose and other members of the organ committee, and by parishioner and construction overseer Dan Iossi. Senior pastor Peter Marty and the entire staff of St. Paul were always very supportive and helpful.
Mark Sedio served as consultant on the project. On May 15, 2009, St. Paul’s director of music, Dr. Melanie Moll Sigafoose, played the inaugural recital to an enthusiastic full house.
—David Chamberlin