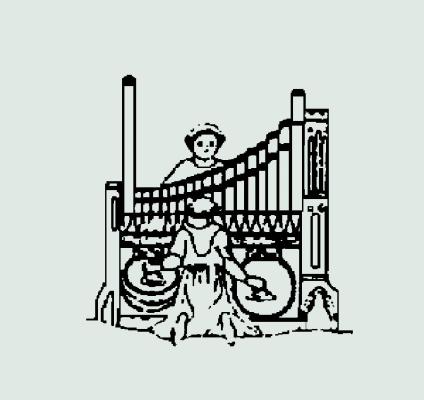
Noack Organ Co., Inc.,
Georgetown, Massachusetts
Shrine of Our Lady of Guadalupe, La Crosse, Wisconsin
From the director of music
The Shrine of Our Lady of Guadalupe consists of several buildings and various outdoor devotional areas and religious sculptures located on 100 scenic acres just outside the city of La Crosse, Wisconsin. It is the vision of its founder, the Most Reverend Raymond L. Burke, who was the Bishop of La Crosse at the time the shrine complex was begun, then became Archbishop of St. Louis, and who recently was appointed Prefect for the Apostolic Signatura in Rome, but who has continued his leadership role at the shrine. Although the shrine facilities are still a work in progress, the heart of the shrine, the Shrine Church, was recently completed and was dedicated on July 31.
This magnificent church is built in a richly decorated traditional style, cruciform in shape with a large dome above the crossing. The architecture is the result of a collaboration of Michael Swinghamer of River Architects in La Crosse and Duncan G. Stroik, professor of architecture at the University of Notre Dame in South Bend, Indiana. The church seats approximately 450 persons and is a wonderfully reverberant space. It is a building of national significance.
A suitable instrument was needed for this inspired space, and we were very fortunate in securing the Noack Organ Company of Georgetown, Massachusetts as the builder. In addition to my duties at the shrine, my primary position is that of music director and organist at the Cathedral of St. Joseph the Workman in La Crosse. We had already arranged for Fritz Noack to build two new organs for the cathedral (to be completed in August of 2010) when it became apparent that the Shrine Church had progressed faster than anticipated and would need an organ by summer 2008. The Noack firm was selected to build a very substantial three-manual instrument for the shrine.
The organ is located in a high choir loft at the rear of the nave. It is first and foremost an organ for liturgical use, but it is also a fine recital instrument, and in fact our liturgical practice includes the performance of substantial solo organ repertoire, so these purposes are not clearly distinguished. The liturgical aspect demands that the organ also serve effectively as an accompanying instrument both for the great choral/organ literature and for congregational singing. This organ has already demonstrated that it does all of these things very well.
The beautiful organ case, based on a design by Duncan Stroik, is thoroughly integrated into the room, both visually and aurally. The placement of the Swell division at the lower level of the main case is ideal for working with the choir. The Great is at the top for optimal projection down the nave, the Pedal is in side towers, and the Chair organ is located in the traditional location on the rail of the loft. The instrument speaks with perfect clarity in the room. The well-designed stoplist provides a versatile assortment of beautiful timbres which, while lovely individually, work together to form a coherent and balanced ensemble. The console is detached to make working with choir and orchestra practical. The key action is mechanical and the stop action is electric, with an extensive combination action and multiple channels of memory, providing excellent control over the touch and easy management of registration.
This outstanding Noack organ, optimally designed and placed, will provide many years of exciting and profoundly spiritual music for the Church at the Shrine of Our Lady of Guadalupe.
—Brian Luckner, DMA
Director of Music and Organist
Shrine of Our Lady of Guadalupe
From the organbuilder
We had already planned a large new organ for the Roman Catholic Cathedral in La Crosse, Wisconsin, with Dr. Brian Luckner, who directs a superb program of sacred music there. While funding for that instrument was still under way, I received a phone call from him asking simply if we would be interested in building first a three-manual organ for the new church under construction at the Shrine of Our Lady of Guadalupe near La Crosse. He would trust me completely with the tonal design, as we had already done much mutually beneficial brainstorming “inventing” the cathedral organ(s) and we knew quite well what sort of organ would be best for the Shrine Church. The case, however, was to be built according to the design by architect Duncan G. Stroik, of South Bend, Indiana, who was in charge of the interior design of the church.
We organ builders may have a reputation of dislike for cooperation with architects, a reputation that has its root in an outdated scenario where architects act as if they know everything about designing any visually important aspect of a building, including organ cases, and where organ builders consider themselves great architects.
Actually, I was delighted to accept this promising challenge. Several of my closest family are professional architects, and I have always respected and enjoyed close cooperation with members of that profession. Just to avoid discord, my firm’s contracts always state that we are ultimately responsible for the entire design of our organs, including the case. Duncan’s plan proved to be elegant, and respectful of the finest classical traditions, and we were happy to retain all of its décor and overall flair. We merely modified the shape to reflect the actual layout of divisions and the precise dimensions of the speaking front ranks (Diapason 16' on the main case and Dulciana 8' on the Chair). We were fortunate to engage James Lohmann, who has carved most of the beautiful pipe screens on our organs to date, for the pipe shades, tower consoles, and angel heads to float below the Chair case. Partially because of the relatively short time between contract and planned dedication of the church, we engaged the woodworking firm of Hawkes & Huberdeau (both partners having learned their trade in our shop!) of Amesbury, Massachusetts, to make the solid mahogany case. This unusually festive-looking organ bears testimony to a successful cooperation between all designers and craftspeople who poured the essence of their skill into this challenging project.
The technical design of the instrument, including the intricacies of balancing the Chair organ beyond the edge of the organ loft, and the electrical stop and combination action, were competently detailed by our Ted Brinduse. I myself enjoyed doing all the pre-voicing at the shop, while the on-site finishing was beautifully achieved by our David Rooney. Our team also included Aaron Tellers, Alan Meyers and Frank Thompson, with Eric Kenney (as he has for over thirty years) supervising. In moving the organ to La Crosse and the on-site erecting of the large parts on the instrument, we again had the capable help of the “A-Team” from the Organ Clearing House. Considering that at the time of the installation, the church was still a bustling construction site on a hillside surrounded first by several feet of frozen snow and later foot-deep mud (and no access for the big truck), their job was particularly appreciated.
I often have been asked what style we normally follow in the design of our instruments, and I usually try to avoid formulating a reply. The only honest answer would be: our own contemporary style, which, I might hasten to add, respects and is inspired by many historic styles that have given us a rich gift of organ music. The tonal architecture of North German Baroque organs is, of course, part of this gift. We also find that reeds that could have been made in France in 1800 actually work rather well in this context. I have made New England my home for almost half a century now, and so it may come as no surprise that stops such as our Bell Gamba (one of our favorites) and Oboe do not stray too far from those of the Hook brothers. To me the greatest achievement is to turn what could easily be a faceless collection of unrelated parts into one cohesive, musically attractive instrument. Our focus is on touching the listener’s heart, rather than to be completely governed by the goal of providing accurate media for the performance of a specific literature. If that appears as though we are avoiding an important task and opportunity for the organ, fear not. It often comes as a surprise that so much of idiomatic literature sounds, at least to our ears, so “right” on this instrument. Perhaps therein lies the secret: a truly beautiful sound will take precedence over a mediocre, but “correct” sound. As I noted above, I probably should avoid trying to define our style.
A few details may be of interest. Most of the Diapason chorus and strings are made of 70% tin, except for the Great Diapason 8', which is of almost pure hammered lead. Most flute chorus pipes, including the 5-rank mounted Cornet (after Dom Bedos, but all ranks open) are from “common metal,” an alloy of 70% lead and 30% tin. The wood pipes are from select, standing-grain pine. All stopped metal pipes are soldered shut after having been tonally finished in the church; the smaller open metal pipes are cone-tuned. Zinc is used only to provide strength on the lowest part of the Trombone resonators. All reed boots are made as solid wooden units, but the reed blocks are the conventional hard lead type. The lowest seven pipes of the Double Diapason are shared by Great and Pedal; all other ranks are independent.
The temperament is after Vallotti—a slightly unequal system in which the thirds over C, G, and F are rather pure and get coarser with more sharps and flats, and all fifths are either pure or twice as tempered as in equal temperament (which is still quite “nice”). Wind pressure is 80mm (31'8'), provided by a blower in a separate room with a small static reservoir and large parallel-opening bellows and solid wood ducts in the organ—to provide a complete noise- and turbulence-free, calmly “breathing,” quite stable wind system.
The organ has slider windchests and a self-adjusting mechanical key action without any assist devices, except for the largest front pipes, which are on pneumatic offset chests. Trackers are wooden, running in wooden guides. Rollerboards are solid aluminum (tubular often being unpleasantly audible). The sliders are moved by solenoids; there is an eight-level combination system from SSOS. The freestanding keydesk has bone-covered natural keys. The fancy stop knobs are moved by Harris propulsion magnets and are set in fiddleback maple stop terraces. The swell action is mechanical.
Before the shrine opened, I had the opportunity to bring a small group of attendees of the AGO national convention from Minneapolis for a preview visit to the shrine. When Brian Luckner played a multi-faceted program with elegant articulation and thoughtful registration for us, my style worries quickly evaporated. I was even more assured of this organ’s ability to fulfill its true role at the church’s four-hour dedication service with Brian, who also had composed a large amount of the music, again at the keydesk providing a wealth of wonderful music.
We owe much thanks to the founder and director of the shrine, the Most Reverend Raymond L. Burke, its music director Dr. Brian Luckner, the executive director of the shrine, Sister Christa Marie Halligan, and the architects Duncan G. Stroik, Michael Swinghamer, and Sherry Wall, all of whom supported us in the most sincere manner. Seldom have we undertaken a large job in which so much mutual trust and support carried us to a successful completion.
—Fritz Noack, FAIO
President, The Noack Organ Co., Inc.
AGO post-convention organ crawl
Fritz Noack led one of the most interesting organ crawls imaginable, following the Minneapolis AGO convention. The twenty of us, who were the lucky ones to take part in this, got to see and hear his latest opus in a church (a shrine, actually) that is not yet open to the public. A scenic two and a half hour bus ride alongside the Mississippi River took us to La Crosse, Wisconsin, where the new Shrine of Our Lady of Guadalupe was having the finishing touches applied to its extremely ornate Italian Renaissance structure, housing a three-manual, 40-stop mechanical action (electric stop action) Noack organ in the rear balcony. To say that this was a unique treat would be a gross understatement.
Brian Luckner ably demonstrated the organ, proving that it is comfortable in many styles of repertoire. Well winded, elegantly voiced, with comfortable action and beautiful casework (African mahogany, like the pews in the new building), the organ seemed to reveal an endless array of possible colors from old (Buxtehude) to Romantic (Vierne) to contemporary (Leighton). It handled it all with aplomb! The shrine was opened in July, and pilgrims can take the half-mile walk up the path to the church to witness a glorious building housing a spectacular organ. Our trip was capped with a lunch served at the Pilgrim Center and another scenic trip back to the Twin Cities, including seeing a bald eagle flying over the river!
—Jonathan Dimmock
San Francisco
<www.jonathandimmock.com>
GREAT — Manual II
16' Double Diapason 51 pipes 70% tin, front, C–F# = Ped Dbl Diap 16'
8' Diapason 58 pipes hammered lead
8' Chimney Flute 58 pipes 30% tin
8' Viola 58 pipes 70% tin
4' Octave 58 pipes 70% tin
4' Harmonic Flute 58 pipes 30% tin
22/3' Twelfth 58 pipes 70% tin
2' Fifteenth 58 pipes 70% tin
8' Cornet V c'–c''' 125 pipes 30% tin, mounted
11/3' Mixture IV–VI 318 pipes 70% tin
8' Trumpet 58 pipes 70% tin
SWELL (enclosed) — Manual III
8' Diapason 58 pipes 50% tin (C–F Haskells)
8' Gedackt 58 pipes 30% tin
8' Bell Gamba 52 pipes 70% tin (C–F = Diapason 8')
8' Celeste (from G) 51 pipes 70% tin
4' Octave 58 pipes 70% tin
4' Recorder 58 pipes 30% tin
2' Gemshorn 58 pipes 30% tin
2' Mixture IV 232 pipes 50% tin
8' Cornopean 58 pipes 30% tin
8' Oboe 58 pipes 70% tin
CHAIR — Manual I
8' Stopt Flute 58 pipes 30% tin
8' Dulciana 58 pipes 70% tin, front
4' Prestant 58 pipes 70% tin, front
4' Chimney Flute 58 pipes 30% tin
22/3' Nasard 58 pipes 30% tin
2' Octave 58 pipes 70% tin
13/5' Tierce 58 pipes 30% tin
1' Whistle 58 pipes 30% tin
1' Sharp III 174 pipes 70% tin
8' Cremona 58 pipes 30% tin
PEDAL (AGO pedalboard)
16' Double Diapason 32 pipes 70% tin, front
16' Stopt Bass 32 pipes wood
102/3' Quinte 32 pipes wood
8' Diapason 32 pipes 50% tin
8' Gedackt 32 pipes 30% tin
4' Octave 32 pipes 50% tin
16' Trombone 32 pipes zinc and 30% tin
8' Trumpet 32 pipes 30% tin
4' Clarion 32 pipes 30% tin