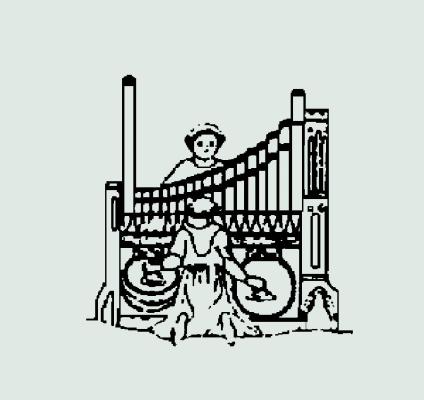
Berghaus Pipe Organ Builders, Inc., Bellwood, Illinois
La Casa de Cristo Lutheran Church, Scottsdale, Arizona
Opus 224 (2008)
From the organbuilder
Overview
Berghaus opus 224 at La Casa de Cristo Lutheran Church contains 91 ranks, 94 stops, and 5,067 pipes over four manuals and pedal. The instrument takes its place as one of the largest pipe organs in the state of Arizona. The majority of the instrument (Pedal, Great and Positiv) is located on the mezzanine level at the front of the sanctuary, on a concrete platform measuring 42 feet across. The enclosed Swell is located above the musician’s gallery in a resonant chamber measuring 14 by 18 feet, and the Antiphonal is divided and elevated on two sides of the rear gallery, flanking the large rear window.
The casework is constructed from light-golden, rift-cut oak. The design emulates contemporary shapes found elsewhere in the sanctuary. The visually striking façade, including polished tin Principals from the Pedal, Great, and Positiv divisions, takes its inspiration from the McDowell mountain range, located in the northeast corner of the Phoenix valley. A sense of depth is created with the mountain-like arrangement of flamed-copper 16′ Principal pipes from the Great and Pedal divisions. The façade also contains twelve non-speaking wood pipes, painted sage green, in homage to the majestic Saguaro cactus found in the region. Adding to the visual display is the asymmetrical layout of the Trompette en Chamade, constructed with flamed-copper resonators. The twin Antiphonal façades echo the details found in the main organ.
Tonal Approach
We designed an eclectic instrument, taking cues from the American Classic and Romantic traditions, that would be able to handle a comprehensive repertoire, including a wide range of expression, both dynamic and tonal. To that end, there are no less than five manual 8′ principals, ten different 8′ and 4′ flutes, strings and hybrid (tapered) stops of varying tone and construction. The versatility of this instrument results from our ability to treat each of these stops as a beautifully unique voice when used alone, as well as having the ability to blend well, thus creating new and desirable tones when used in combination. This is evident in the Great, which contains the standard French-Romantic foundation of Principal, String, Open Flute, and Stopped Flute.
Given the challenge of creating a large organ with only one expressive division, it was clear from the onset of the project that great care would have to be taken in the tonal finishing process to ensure a seamless crescendo and to create an organ with equally balanced manual divisions. The ranks of the unenclosed Positiv are designed and voiced to provide a remarkable degree of expressiveness, and to serve as a tonal bridge between the Swell and the Great. The overall effect in the crescendo is that of a seamless transition from ppp to fff without experiencing staggering dynamic or color steps.
Tonal Analysis
The Great division consists of 19 stops, 22 ranks, and is mostly divided between two large slider chests, one containing the principal chorus through mixture, the other containing the flute and string stops. The 8′ First Principal is of generous scale, and is constructed of 75% tin throughout. This creates a timbre that is simultaneously bright and full, and gives it a singing quality that provides a strong foundation upon which the subsequent ranks are built. The 16′ Sub Principal is scaled proportionally (smaller) to the First Principal and is extended to be available as an 8′ stop (Second Principal). This gives an alternative diapason tone that is more subdued than its larger neighbor, yet is large enough to be a lighter 8′ texture for the entire plenum. The principal chorus is completed with narrowly scaled mutations, and is crowned by two mixtures: a full 2′ V-rank Fourniture, and a sparkling 1⁄2′ III-rank Cymbale. The Flûte Harmonique is large scale, with harmonic pipes starting at no. 30, and is voiced with a very strong increase in the treble. Other flute stops include a metal 8′ Bourdon, a harmonic 4′ Flûte Octaviante, and a II-rank Gross Kornet, constructed of large-scale open flutes at 51⁄3′ and 31⁄5′ pitches to enhance the 16′ harmonic series. The 8′ Gamba is of slender scale and is gently voiced to be a blending stop. The 16′ and 8′ unit Kontra Posaune is a blending chorus reed of German construction. The 16′ and 8′ Trompette en Chamade contains schiffchen-style shallots, producing a sound reminiscent of older Spanish trumpets, yet it can be used as a crown for full organ. The Great provides a myriad of combinations suited for a range of demands from the liturgical service to the solo organ repertoire.
The Swell division contains 21 stops, 23 ranks, and is “double-stacked,” with the complete principal chorus, mutations, and reeds occupying the lower level. Flutes, strings, and celestes are mounted above. The principal chorus is based on an 8′ Diapason of spotted metal, crowned with a 2′ IV-rank Plein Jeu. The relatively low pitch of this mixture, combined with a narrow scale, allows the pipes to be blown full, which helps to produce a clear principal tone. Furthermore, the mixture is voiced softly enough to give the entire plenum a gentler quality suitable for choral accompaniment. The III-rank Cymbale is designed as a tierce mixture and voiced to its full potential to reinforce harmonics present in the fiery chorus reeds. It also blends well and can be used as a higher-pitched mixture with the principal chorus.
The Viole de Gambe is made of 75% tin and slotted for optimum harmonic development. The combination of this stop with its 61-note Voix Celeste is intended to produce true string tone, and not tone associated with narrow principals or stringy hybrid stops. This approach allows us to keep each of the tonal categories of the instrument separate and distinct. The Swell is also home to the softest rank of the organ, the 8′ Flûte Conique, which when paired with its celeste elicits a most haunting timbre. Other flutes in this division include the 8′ Flûte à Cheminée, which is wood in the bass and is extended to 16′ pitch, and a 2′ Octavin, which goes harmonic at no. 13. This 2′ flute is not intended to be used with the mixture, but rather with the 8′ and or 4′ flutes. However, it works equally well with the principals, as the scale is moderate and the voicing is light. The battery of reeds consists of a full-length 16′ Basson, an 8′ Trompette and 4′ Clairon of French construction, and an 8′ Hautbois featuring coned-in bells and parallel French shallots. When combined with foundation stops, the 8′ Hautbois becomes a most useful solo voice, especially for music from the French symphonic school. The Voix Humaine is of American Romantic construction.
The Positiv division is located adjacent to the Swell, which allows this division, along with the Swell, to accompany the choir. Totaling 19 stops and 19 ranks, the Positiv is based on an 8′ Prinzipal constructed of 75% tin and is complete through a 1′ IV-rank Scharf. The ranks of the plenum are narrower in scale than in the other divisions and provide a good secondary chorus to the Great, especially in Baroque music. The 8′ Gemshorn has a very wide mouth with a low cut-up and a 1/3 taper, giving it a string-like tone. A complete Cornet decomposée including Septième comprises pipes of various construction, from the 8′ Holzgedackt made of poplar to the 22⁄3′ chimneyed Rohrquinte. There are three solo reeds in the Positiv division, including an imitative 16′ English Horn, an 8′ Cromorne, and an 8′ Trumpet with English shallots.
The Antiphonal division comprises 9 stops and 10 ranks, and provides additional support for congregational singing as well as interesting echo effects to the main instrument. Placed on opposing sides of the gallery, the Antiphonal is higher in elevation in comparison to the main organ. The Antiphonal principals are voiced in a mild fashion, to give a sense of surrounding the listener while providing a supplemental role to the main instrument. This approach was preferred to bombarding the listener with sound from the gallery and purposely announcing the Antiphonal’s presence. Of note are the two solo flutes: the 8′ Doppelflöte and the 4′ Flauto Traverso (harmonic), both made of poplar. The organ’s heroic reed, the 8′ Trompette de Fête, is located in the Antiphonal division as well. The Trompette de Fête features hooded resonators and is voiced on 18 inches of wind.
The Pedal division comprises 26 stops and 17 ranks. The division is thoroughly complete to provide ample foundation tone in a variety of timbres and volumes. Fortunately, few of the pedal stops are borrowed, which gives tremendous flexibility to the division as a whole. The principal chorus is based on an open metal 16′ Principal, scaled according to classical principles (relative to the Great 8′ First Principal). The entire chorus provides a solid contrast to the Great and gives excellent support without being woofy. When a more penetrating foundation is desired, the generously scaled 16′ Open Wood is useful for larger combinations. Of particular note is the 31⁄5′ V-rank Pedal Mixture. The first rank of this stop is a tierce (16′ series), constructed of 2/3 tapered pipes. Voiced gently, this rank dramatically enhances the 16′ fundamental tone, while giving the overall plenum a pleasantly reedy tone. This helps to further clarify the Pedal line in contrapuntal textures. As with many of our larger instruments, an 8′ Spitzflöte is included to give a more pointed emphasis to the Pedal line in softer combinations. The reed chorus consists of a 32′ and 16′ Bombarde constructed with pine resonators, and a large-scale 8′ Trompette with English shallots. A 4′ Rohrschalmei is a very characteristic reed useful for cantus firmus solos.
Wind System and Chests
The vast majority of flue stops in this organ are placed on slider and pallet chests, which we believe speak to the heart (and origins) of good organ building. Principals and flutes in each division (sans Antiphonal), are placed on separate chests. This helps to solidify each respective chorus. We have insured absolutely steady wind by incorporating a large number of bellows and schwimmers. By contrast, reeds are placed on electro-pneumatic chests, allowing wind pressures to vary to suit the tonality of each reed. Furthermore, wood wind conductors are used throughout the organ, which helps to eliminate turbulence and the resulting wind noise. Pneumatic pedal and offset chests are supplied with their own regulators and concussion bellows.
Console
Design elements of the four-manual console were taken from architectural themes found in the church. The contemporary English-style drawknob console is low profile, and contains state of the art controls for the combination action and record/playback systems. Controls were placed inside a drawer to the organist’s right in order that the console be visually free of electronic clutter. The shell is made of light-golden, rift-cut oak to match casework. Drawknob jambs are made of burled walnut. Keyboard coverings are bone and feature top-resistant tracker touch.
Construction Timeline
The creative journey to construct opus 224 began late fall 2007, with final voicing completed spring 2009. The organ was dedicated in a festival service organized by Dr. Jennaya Robison, director of music, and played by Dr. Homer Ashton Ferguson III. Dr. Weston Noble conducted the combined choirs. The organ was also featured at the 2009 Region IX AGO convention.
Berghaus Pipe Organ Builders wishes to thank the members of La Casa de Cristo Lutheran Church, Scottsdale, Arizona, and the following individuals: Pastor Andrew Garman, senior pastor; Dr. Jennaya Robison, director of music; Dr. Homer Ashton Ferguson III, organist; and Dr. William Barnett, prior organist.
Berghaus Pipe Organ Builders also wishes to thank members of its staff for their countless hours and dedication to this instrument:
President: Brian Berghaus
Director of sales and marketing: David McCleary
Tonal design: Jonathan Oblander, Kelly Monette
Head tonal finisher: Kelly Monette
Reed specialist: Steven Hoover
Structural and visual design: Steven Protzman
Shop foreman: Jeff Hubbard
Logistics: Jean O’Brien
Construction / assembly / installation: Mark Ber, Mitch Blum, Stan Bujak, Kevin Chunko, Chris Czopek, Steve Drexler, Trevor Kahlbaugh, Kurt Linstead, David Mueller, Joe Poland, Daniel Roberts, Tim Roney, Paul Serresseque, Ron Skibbe, Jordon Smoots, Paul Szymkowski, Randy Watkins.
—Kelly Monette, David McCleary, and Jonathan Oblander
Photo credit: David McCleary
Berghaus Pipe Organ Builders, Inc., Bellwood, Illinois
La Casa de Cristo Lutheran Church, Scottsdale, Arizona
Opus 224 (2008)
GREAT – Manual II (unenclosed, 90 mm wind pressure)
16′ Sub Principal (façade) 61 pipes flamed copper and 75% tin
8′ First Principal (façade) 61 pipes 75% tin
8′ Second Principal (façade) 12 pipes (extension of 16′ Sub Principal)
8′ Flûte Harmonique 49 pipes 1–12 from Bourdon, harmonic @ f30
8′ Bourdon 61 pipes 52% tin
8′ Gamba 61 pipes 1–12 zinc, 13–61 52% tin
4′ Octave 61 pipes 52% tin
4′ Flûte Octaviante 61 pipes 52% tin; harmonic @ c25
22⁄3′ Twelfth 61 pipes 52% tin
2′ Fifteenth 61 pipes 52% tin
13⁄5′ Tierce 61 pipes 52% tin
51⁄3′ Gross Kornet II 88 pipes 51⁄3′ and 31⁄5′, 52% tin; c13 to g56
2′ Fourniture V 305 pipes 75% tin (15-19-22-26-29)
1⁄2′ Cymbale III 183 pipes 75% tin (29-33-36)
16′ Kontra Posaune 61 pipes 1–12 L/2, resonators zinc and 52% tin
8′ Trompete 12 pipes (extension of 16′ Kontra Posaune)
Tremulant
Zimbelstern 5 bells with adjustable delay, speed, and volume
16′ Trompette en Chamade 61 pipes 1–12 L/2, flamed copper resonators
8′ Trompette en Chamade 12 pipes (extension of 16′)
8′ Trompette de Fête (Antiphonal)
SWELL – Manual III (enclosed, 80 mm wind pressure)
16′ Bourdon 24 pipes poplar (extension of 8′ Flûte à Cheminée)
8′ Diapason 61 pipes 1–12 zinc, 13–61 52% tin
8′ Viole de Gambe 61 pipes 1–12 zinc, 13–61 75% tin; slotted
8′ Voix Celeste CC 61 pipes 1–12 zinc, 13–61 75% tin; slotted
8′ Flûte à Cheminée 49 pipes 40% tin, 1–12 from Bourdon
8′ Flûte Conique 61 pipes 75% tin
8′ Flûte Celeste TC 49 pipes 75% tin
4′ Prestant 61 pipes 52% tin
4′ Flûte Ouverte 61 pipes 40% tin
22⁄3′ Nasard 61 pipes 52% tin
2′ Octavin 61 pipes 75% tin; harmonic @ c13
13⁄5′ Tierce 61 pipes 52% tin
2′ Plein Jeu IV 244 pipes 75% tin (15-19-22-26)
1′ Cymbale III 183 pipes 75% tin (22-24-26)
16′ Basson 61 pipes L/1, resonators of zinc and 52% tin
8′ Trompette 61 pipes resonators of 75% tin
8′ Hautbois 61 pipes resonators of 52% tin
8′ Voix Humaine 61 pipes 52% tin
4′ Clairon 61 pipes resonators of 75% tin
Tremulant
8′ Trompette de Fête (Antiphonal)
16′ Trompette en Chamade (Great)
8′ Trompette en Chamade (Great)
POSITIV – Manual I (unenclosed, 70 mm wind pressure)
16′ Quintaton 61 pipes 1–12 zinc, 13–61 75% tin
8′ Prinzipal (façade) 61 pipes 75% tin
8′ Gemshorn 61 pipes 1–12 zinc, 13–61 52% tin; 1/3 taper
8′ Holzgedackt 61 pipes poplar
4′ Oktav 61 pipes 75% tin
4′ Koppelflöte 61 pipes 52% tin
22⁄3′ Rohrquinte 61 pipes 52% tin
2′ Oktav 61 pipes 75% tin
2′ Blockflöte 61 pipes 40% tin
13⁄5′ Terz 61 pipes 52% tin
11⁄3′ Larigot 61 pipes 52% tin
11⁄7′ Septième 61 pipes 52% tin
1′ Scharf IV 244 pipes 75% tin (22-26-29-33)
16′ English Horn 61 pipes resonators of zinc and 52% tin
8′ Trumpet 61 pipes 52% tin
8′ Cromorne 61 pipes 52% tin
Tremulant
8′ Trompette de Fête (Antiphonal)
16′ Trompette en Chamade (Great)
8′ Trompette en Chamade (Great)
ANTIPHONAL – Manual IV (unenclosed, 75 mm wind pressure)
8′ Principal (façade) 61 pipes 1–12 flamed copper, 13–61 75% tin
8′ Doppelflöte (façade) 61 pipes poplar
4′ Octave (façade) 61 pipes 75% tin
4′ Flauto Traverso 61 pipes poplar; harmonic @ c25
2′ Fifteenth 61 pipes 75% tin
11⁄3′ Fourniture IV 244 pipes 75% tin (19-22-26-29)
Tremulant
16′ Trompette de Fête 61 pipes hooded resonators, 18 inches wind pressure
16′ Trompette en Chamade (Great)
8′ Trompette en Chamade (Great)
PEDAL (unenclosed, 90 mm wind pressure)
32′ Untersatz 7 pipes poplar
16′ Open Wood 32 pipes poplar
16′ Principal (façade) 32 pipes flamed copper and 75% tin
16′ Sub Principal (Great)
16′ Subbass 32 pipes poplar
16′ Quintaton (Positiv)
16′ Bourdon (Swell)
8′ Octave (façade) 32 pipes 75% tin
8′ Principal (Great)
8′ Spitzflöte 32 pipes 75% tin, 4/5 taper
8′ Metallgedackt 32 pipes 52% tin
8′ Bourdon (Swell)
4′ Octave 32 pipes 75% tin
4′ Spillflöte 32 pipes 52% tin
2′ Nachthorn 32 pipes 52% tin
31⁄5′ Mixture V 160 pipes 52% tin (10-12-15-19-22)
32′ Contre Bombarde 12 pipes (extension of 16′ Bombarde)
16′ Bombarde 32 pipes resonators of pine
16′ Posaune (Great)
16′ Basson (Swell)
8′ Trompette 32 pipes 52% tin
8′ Posaune (Great)
4′ Rohrschalmei 32 pipes 52% tin
Tremulant (slider chest stops only)
8′ Trompette de Fête (Antiphonal)
16′ Trompette en Chamade (Great)
8′ Trompette en Chamade (Great)