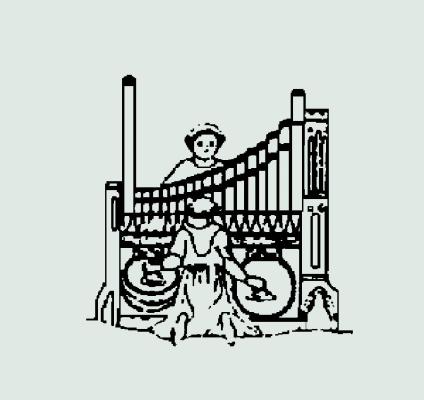
J.H. & C.S. Odell, East Hampton, Connecticut, Opus 644
St. Ann’s Episcopal Church, Bridgehampton, New York
From the Rector of St. Ann’s
The committee all agreed--something had to be done. For
years the church organ had been in irreversible decline, and the time had come
to act. I regarded this to be a daunting and confusing challenge in which we
needed professional counsel. Dr. Mark Andersen guided us through the various
options and needs of the decision-making process, and by July 2004 it was
agreed that J.H. and C.S. Odell of East Hampton, Connecticut be engaged to
restore the organ. It was a decision that we would never regret.
In September 2004, Edward and Holly Odell arrived to remove
the existing organ. Pipes were carefully laid out in special boxes. Frames and
blowers were removed--and those were only the things that I could
identify! It all happened remarkably quickly, and before long the truck was
driven away leaving a large space where the console had once stood, and a
spotlessly clean church where the disassembly had taken place.
The novelty of using just piano and occasional other
instruments wore off after Christmas, and we waited anxiously for the organ to
return. Our patience was not helped by tantalizing photographs and reports sent
regularly from the Odell factory showing the new instrument taking shape!
It was March 2005 (the day I was flying off on vacation)
that the Odell team returned. It was time to put the whole thing together, but
it was only two weeks before Holy Week, and three to Easter. Could it really be
done?
Eight days later I returned to find the church in wonderful
disarray with parts and pipes everywhere, and Edward Odell looking and sounding
confident, if a little tired. Yes, of course it could be done. The project was
running according to schedule. The organ would be partly voiced by Palm Sunday
and ready for Easter.
Every part was in place and every promise fulfilled. A
magnificent new console was carefully maneuvered into position. Pipes were
ready and being expertly voiced by Holly Odell. Cables and wires were
connected. The organ had life--and was indeed ready for Easter morning. It
was resurrection in a different form!
We have not looked back since then. Not only has this
instrument enhanced our Sunday worship, it has enabled us to host a season of
superb organ recitals over the summer, and earned for St. Ann’s Church a
reputation for being a place where good music can be found.
style="mso-spacerun: yes">
Working with the Odell Organ Company has been not only a
proven right decision but also a joy. From the outset we not only admired the
professionalism of Edward and Holly Odell, but also came to share in their love
of organs and sheer depth of knowledge in their field. All these things,
coupled with their warmth and sense of humor, have made the whole process one
which we can reflect on with immense satisfaction. It is never an easy task for
a small parish church to embark on such a large project and investment, but we
know that we have learned and benefited so much from choosing the right organ
and the right builder.
The Reverend Tim Lewis, Rector
St. Ann’s Episcopal Church
Bridgehampton, New York
From the Consultant
As an organ consultant for nearly 35 years, I have had the
opportunity to design a large range of instruments from the smallest two-manual
to several five-manual instruments throughout the United States, England, and
Australia.
St. Ann’s parish is that wonderful combination of
sophistication in a relaxed atmosphere. It is many New Yorkers’ church away
from home, and the organ would have to meet the discriminating tastes of
parishioners who worship in some of the largest churches in the metropolitan
area.
There was not much with which to start--an old hybrid
Möller from the ’20’s that was on its very last legs after having several ranks
replaced over the years. I designed an organ specification capable of
accompanying a proper Anglican service, but in a size and fit that matched St.
Ann’s. After requesting bids from many organbuilders, it was clear that J.H.
& C.S. Odell had the talent to see the task through with outstanding
results. Tonally the organ now fits the space perfectly and is complete enough
in specification to satisfy even the most discriminating organists. The
craftsmanship is superb, and the voicing is clear and clean, leaning beautifully
toward the English tradition. The project has surpassed my expectations.
Mark Andersen, PhD
New Berlin, New York
From the Organbuilder
Our Opus 644 began life as what could be termed a “Heinz 57”
instrument, which is to say it featured a combination of pipes and parts from a
combination of organbuilders and suppliers. The console case and most of the
wooden pipes in the organ date from a five-stop 1927 M.P. Möller instrument,
which was then rebuilt and altered in the early 1970s. It was during this 1970s
rebuild that much of the original pipework was replaced.
As we found it, the organ was a unified instrument of modest
resources, most of them well made if not terribly well looked after. It was
unrefined, but met the basic requirements. In the 1980s a German supply house
Trumpet 8’ and Mixture III (inexplicably, a Zimbel based on 2?3’ pitch) were
added, along with a polished tin Gemshorn that was used to form a façade. The
entire organ was in a single expression chamber to the right of the chancel. The
existing electro-pneumatic unit chests, made from solid mahogany, were in good
physical condition, though the installation made maintenance access difficult
in certain areas.
In July of 2004, Dr. Mark Andersen (organ consultant to St.
Ann’s) approached us with a prospectus that included a rebuild and enlargement
of the organ. In addition to new pipes and new chest work, a new 3-manual
terrace-jamb console was part of this plan.
Dr. Andersen’s proposed stoplist would add a total of nine
ranks to the organ. The scheme had an immediate appeal, as it would expand the
resources of the organ to include a full principal chorus in the Great, as well
as a new 8’ Rohrflute to contrast the existing Chimney Flute in the Swell.
“Fleshing out” the Great with six new ranks allowed us to recast the remaining
resources to work as a mostly independent Swell division. The new scheme would
also extend the existing Trumpet to 16’ pitch to play from the Pedal and add a
small Cornet (a tenor C, 2-rank 12/17 combination, scaled and voiced to match
the new Great flute).
The challenge, of course, was to now somehow fit 19 ranks in
a space that before barely contained eight. Early in the design process it became
evident that much of the precious real estate in the organ chamber could be
reclaimed if the many offset chests for various ranks could be consolidated
onto a new single offset chest that would also provide for the new Trumpet 16’.
We also wanted to ensure the new chamber layout would permit adequate access
for service and, most importantly, tuning. Rebuilding the existing expression
shades and fitting them with new expression controllers made available space
that had been previously occupied by a pneumatic motor with an unwieldy linkage
system.
We developed a new 7’4? diatonic chest scale to accommodate
the new stops and the relocated Gemshorn. The existing Principal 8’ was
carefully revoiced to give it more moderate power, and the new principal ranks
were scaled and voiced to build from this new foundation. The new Great Bourdon
8’ was voiced using a special arch cutup schedule, which lent the pipes a color
that allows the stop to work superbly as both a solo and ensemble voice. The
Swell was given its own new 3-rank mixture based on 2’ pitch, and the existing
Zimbel mixture was recomposed into a more appropriate chorus mixture based on
11?3’ pitch for the Great.
Though the action for the new chestwork was specified to be
electro-mechanical, we milled all windchest toeboards to be no less than one
and one-half inches in thickness. This, along with proper attention to voicing,
successfully offset any pipe speech problems normally anticipated with this
type of action. Our windchests were made from solid poplar, with the exception
of the toeboard for the new Swell Mixture, which was milled from sugar pine.
The new console and case, both entirely of our own design
and manufacture, were milled in
our East Hampton shop from solid quarter-sawn white oak, and stained and
finished to match existing fixtures in the sanctuary. The console interior
(stop jambs and key cheeks) was milled from solid walnut and finished with
hand-rubbed Danish oil. The façade pipes are polished tin, made to custom
specifications we developed and submitted to our friends at Giesecke. The new
flue pipes were built to our scales by Luc Ladurantaye Tuyatier of Lac Saguay,
Quebec.
Along with the standard complement of accessories, the
console features an integrated control system with multiple memory levels,
programmable crescendo and sforzando, 12-step transposer and MIDI interface for
record and playback ability. The digital Antiphonal division was contracted and
installed separately by Artisan Instruments.
Edward Odell
J.H. & C.S. Odell
Glück New York,
New York, New York
The Church of Our Lady of Loretto, Cold Spring, New York
This historic church, known for its remarkable collection of
stained glass windows, was recently restored, with a new instrument and a
marble chancel floor included in the renewal plans. Under the direction of Fr.
Brian McSweeney, Pastor; Frances Pergamo, Director of Music; and Fr. Richard D.
Baker of the New York Archdiocese, three organbuilders were each invited to
present their vision of an appropriate musical instrument. The smallest and
most stylistically focused proposal submitted, the new Glück organ occupies a
traditional position in the rear gallery to great acoustical advantage. While
the organ looks toward the French orgue d’accompagnement of the 1860s for both
its concept and tonal palette, it is certainly not intended to be a stylistic
copy.
The manual soundboards are placed side-by-side at impost
level, with the Swell to the right, its vertical shutters operated by direct
mechanical linkage. The two large wooden pedal stops stand on their own
windchests behind the organ. The Great organ incorporates some pipework from a
mid-1870s Levi Underwood Stuart organ of undetermined provenance. Interior
metal pipes are of 70% lead alloy, except for the Swell strings, which are of
50% tin. Wooden pipework is of pine and fir. The façade pipes are built with
English bay leaf mouths arrayed in a swag pattern after Gottfried Silbermann’s
façades of the 1740s.
The walnut keydesk en fenêtre sports beveled figured maple
jambs and pao ferro drawknobs. Both pedal and manual accidentals are Brazilian
rosewood. Compasses are 56/30; there is no combination action, but the three
unison couplers are reversible by toe paddles. The case is painted in various
shades of olive, with details in sapphire, ruby, and faux marbre. Architectural
design was by Sebastian M. Glück, who executed the Neapolitan-style angel,
tower finials, and buttress niches, which are suitably polychromed and gilded.
Color photographs may be viewed at the firm’s web site at
<www.glucknewyork.com>.
The structural design and layout are the work of Albert
Jensen-Moulton, general manager of the firm, who was assisted in the
construction of the organ by Dominic Inferrera, foreman. Voicing and tonal
finishing were accomplished on site by Sebastian M. Glück, tonal director. The
organ was formally dedicated in a series of three recitals by Lana Kollath, Dr.
Jennifer Pascual, and the builder.
--Benito Orso
GREAT
8’ Open
Diapason
8’ Open
Wood Flute
4’ Principal
2’ Doublet
8’ Hautboy
(from Swell)
Swell
to Great
Swell
to Great Octaves
SWELL
8’ Salicional
8’ Voix
Céleste
8’ Stopped
Diapason
4’ Harmonic
Flute
8’ Hautboy
Tremulant
Swell
to Swell Octaves
PEDAL
16’ Open
Wood Bass
16’ Stopped
Bass
8’ Octave
style="mso-spacerun: yes"> from Great
8’ Hautboy
from Swell
Great
to Pedal
Swell to Pedal
Swell
to Pedal Octaves