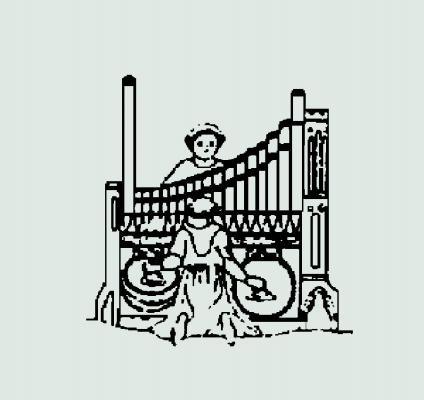
New England Organbuilders, LLC, Willimantic, Connecticut
Portative organ,
Joseph Flummerfelt residence
New England Organbuilders has built a positive organ for Dr. Joseph Flummerfelt. This instrument was presented during the Princeton, New Jersey Bach Festival on June 30, 2007, by the builder, Christopher Walton. It was given in grateful appreciation for the years of teaching and musicianship Dr. Flummerfelt shared with so many students at Westminster Choir College of Rider University.
This instrument was inspired by extant examples of such organs and by period artwork. The organ once belonging to Kaspar ab Yberg, housed in the Basel Historical Museum, Basel, Switzerland, was especially influential. The ab Yberg organ dates from ca. 1550, and as a consequence of restoration by Cecil Adkins, Ph.D., mechanical drawings of this organ are available. The key dimensions of Dr. Flummerfelt’s instrument were taken from the ab Yberg organ. The table positives of the sixteenth and seventeenth centuries typically had a short compass, and tended to possess many ranks for their size. For example, the Basel organ contains four ranks: Metal Gedeckt 4', Principal 2', Quinte 11'3' and Zimbel ½'. Tuning and speech difficulties can arise from this crowded arrangement.
Within this modest instrument of two ranks, there is ample space for good projection. Tuning access is by a hinged panel, situated well above the mouths of the pipes, or by a removable door for the larger pipes. By keeping the tuning access as distant from pipe mouths as possible, the pipes are less affected by the “shading” effects sometimes found in encased organs. The key compass is extended to 45 notes with a short octave in the bass (excluding C#, D#, F#, and G# in the low octave). This short octave is not only for space considerations but also for a pragmatic reason—in the tuning systems of the period that inspired this instrument, such notes were not often used, particularly in the lowest range of the keyboard. Extending the compass to 45 notes makes performance of Renaissance and early Baroque works more practical.
The scaling of the pipes was executed for sufficient breadth and power to accompany small choral or instrumental ensembles. The scaling of both ranks is variable, changing throughout the compass for tonal and practical reasons. The Gedeckt 4' of oak begins as a small scale, increasing rapidly throughout the short octave. This treatment enables the pipes ample room to speak in the bass, and allows for a comparatively larger overall scale for good tone projection. This rank is always on, with no stop action. The Principal 2' scale is similarly varied. It is controlled by a slider accessed on the right side of the case.
A challenging departure from church organs and our scaling practices, designing an organ that will work well in different acoustics is an exercise in compromise. Tonal finishing for an instrument intended to be moved proved especially difficult, for the stops would change character, even for the player. This difficulty was predictable, so we moved the organ to different rooms and churches to hear it in various acoustical conditions. Directly in front of the instrument, the Principal is bold, and seems perhaps too loud to blend with the Gedeckt. At a distance, however, and in a live room, it simply adds brilliance, the Gedeckt functioning as the foundation of the instrument. Our primary work being church organs, we do not normally hear one instrument in different spaces, and the experience was valuable. It was a great pleasure hearing the organ played by and accompanying such fine musicians at the Bach Festival. It was an honor to have it so well received.
“What a joy for me to receive this beautiful instrument from Chris Walton. That he spent several years and countless hours creating this amazing gift is quite overwhelming. The organ is a work of art, both visually and tonally, and, as an erstwhile organist myself, it will afford me many hours of music-making in the quiet of my own home.”
—Dr. Joseph Flummerfelt
The casework is of white oak, with keyboard naturals, mouldings and carvings of Imbuya, a richly colored hardwood. The accidentals are maple. The curved panel of the case was made with a bent lamination technique using a vacuum press, and then veneered with white oak utilizing the same process. All other elements of the case are of solid hardwoods. Although the metal for the Principal was supplied cut to our specifications, all aspects of the design, casework, wind-chest, keyboard and pipework were executed in our shop. Wind is provided by a blower that easily attaches to the back, and is removable for transport. Wind pressure is 63mm.
The instrument was exhibited at the Boston Early Music Festival, June 2007, and was played in the St. John Passion at the Princeton Bach Festival. This was the first instrument of this type produced by New England Organbuilders and proved an enjoyable task.
New England Organbuilders is based in northeastern Connecticut, building primarily mechanical action and electric slider pipe organs, as well as restoring, rebuilding, and maintaining pipe organs with any type of action. Information is obtainable on our web site at <www.newenglandorganbuilders.com>.
—Christopher Walton