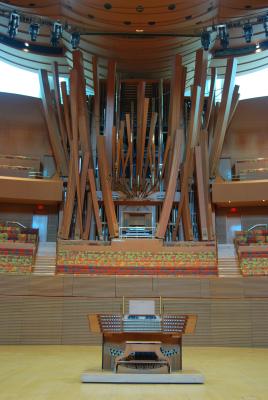
The life of π
If you have maintained bird feeders, you know what squirrels can do. They are powerful, lithe acrobats, and they can outsmart almost any attempt to deter them. I recognize several individual male gray squirrels in our yard that are strong and agile enough to leap three or four feet from the ground on to the cone-shaped baffles. They shinny up the steel poles, over the tops of the feeders, hang upside down, and gorge themselves.
Some days I think it is okay to feed the squirrels as well as the birds, letting them take turns, but one day last week as I watched them dominate, it occurred to me that I could make a new baffle of different design, a two- or three-foot disc of plywood with flashing around the edge. If they jumped on it, it would surely flip and dump them off. I took a quick measurement and set off to the lumber yard for a sheet of half-inch exterior plywood and some flashing. How much flashing? It comes in ten-, twenty-, and thirty-foot rolls. I told the kid behind the sales desk (he’s younger than my kids) that I planned either a twenty-four- or thirty-inch circle. Let’s see. Twenty-four inches is two feet. Two times π is about six-and-a-quarter feet. Thirty inches times π is a little less than eight feet. Easy. Ten feet will do it.
The kid asked, “What’s π?” I told him it is a number discovered by a Greek mathematician named Archimedes who lived around 250 B.C. that defines all the properties of a circle. Π = roughly 3.14. Multiply π by the diameter of a circle and you get the circumference (c = πd), or multiply π by the radius squared to calculate the area of the circle (a = πr2). I added that Archimedes came up with other really useful ideas like the continuous inclined plane (the thread of a screw), and the properties of levers. “So a carpenter can use math,” he observed. I told him he could also use π to figure out the difference between a twelve- and sixteen-inch pizza. 3.14 x 12 = 37.68 square inches. 3.14 x 16 = 50.24 square inches. (I used the calculator in my iPhone.) Adding four inches to the diameter makes the pizza a lot bigger. If a bite of pizza is two square inches, the bigger pie has twenty-five more bites.
I took the ten-foot roll of flashing, drove into Building 3 to pick up the plywood, and went home to cut my circle. I decided on thirty inches and tied a Sharpie and an awl to a piece of string fifteen inches apart to make a rough compass. I marked and cut the circle, used little screws to attach the flashing to the sombrero-like gizmo, and mounted it on the pole under the bird feeder. It took the squirrels less than two days to get to the feeder.
Simple Simon met a π-man . . .
Carpenters work automatically with increments of sixteen inches, the standard distance between studs, joists, and rafters. To make things easy, most metal tape measures have clear markings every sixteen inches. A good carpenter knows sixteen inches perfectly. A baker makes a twenty- or thirty-pound batch of bread dough and cuts it into one-pound pieces. Maybe he checks each one with a scale, but he develops a knack for the heft of a pound. Our butcher does the same. I ask for a pound of ground beef, he grabs at the bowl, and puts 15.77 ounces on the scale. “You’ve done this before.” Experienced organ tuners develop a similar knack for the length of a pipe relative to the pitch. You hear the pitch and reach for the pipe of the correct length.
I worked in an organ shop that used twenty millimeters as the standard thickness for milling lumber for organ cases. We bought 4/4 (one-inch thick) rough-sawn wood from a lumber yard. Planing it flat and then to thickness, we could reliably get twenty millimeters from it. I had twenty-millimeter wood in my hands so much that I could tell if a stick was nineteen or twenty-one millimeters. Likewise, we set the “key-dip” on a keyboard, the distance of travel for the natural keys. It is usually something like ten or twelve millimeters. If you have spent three or four days leveling keyboards and adjusting key-dip, you can tell a millimeter difference in a heartbeat.
∏ is special. It is approximately 3.14, more accurately 3.14159265359 . . . . There is apparently no limit to the number of digits—as of now, it has been calculated to 31.4 trillion digits and counting. I have no concept of how those digits are calculated, so I accept 3.14. That is a lot fussier than sixteen-inch studs, and it is a great example of a concept that is all around us that we do not necessarily think about. When I was a kid on school field trips, I was interested in an exhibit at the Museum of Science in Boston that showed a perfect sphere and a perfect cone on a scale. Each shape had the same radius, and radius and height were equal. They balanced. My old-guy memory of my young-guy thinking had me wondering, “Who figured that out?” You can prove it by using π to calculate the volume of each shape.
The simple circle equations, a = πr2 and c = πd, are pretty familiar. I will take it a step further. The volume of a cylinder is πr2 (the area of the circle) times the height (v = πr2h). The volume of a cone is v = πr2h/3. The volume of a cone is one-third the volume of a cylinder of the same dimensions. The volume of a sphere is v = 4/3πr3. I suppose you can guess I was pleased with myself for the little math lesson I gave the kid in the lumber yard. But what do bird feeders have to do with pipe organs?
The organ pipe maker is the π-man. People who make organ pipes live and breathe π. To make an organ pipe, you cut out three pieces of metal, a pie-shape (no relation to π) for the foot, a rectangle for the resonator, and a little circle for the languid (the horizontal piece at the joint between the foot and the resonator). The width of the rectangle and the length of the curved top of the cone both equal the circumference of the pipe. The circumference of the languid equals the width of the rectangle.
I wish that every organist could witness the making of organ pipes, the soul of our instrument. The metal is blended in a melting pot (just the right amount of lead, tin, eye of newt, and toe of frog) and cast into sheets on a long table. A few seconds after the sheet is cast, there is a magic moment when the liquid metal becomes solid. You can see it happen. The metal is planed to exact thickness, and some organ builders hammer softer metals (those with higher lead content) to make the metal denser.
Thick and strong metal sheets are cast for larger pipes. Low C of an 8′ Diapason is typically about ten feet long, including the foot and sometimes some extra length for tuning. (The speaking length of any organ pipe is measured from the lower lip of the mouth to the tuning point.) The highest note of that Diapason is a couple inches long from mouth to tuner, but take a look at some little mixture pipes, or the top octave of 1-1⁄3′ or 1-3⁄5′ ranks. The speaking length is a half inch or quarter inch and the diameter is a quarter inch or less. I will play with π a little to estimate that the rectangle of metal is 78/100 by 25/100 (1⁄4) of an inch, smaller than a chiclet. That’s a fussy little piece of metal to cut, much different from the carpenters’ sixteen-inch centers. The pipe maker forms that chiclet into a cylinder around a steel mandril, then solders the seams. Careful not to burn your fingers.
The pipe maker cuts sixty-one pieces of pie (toes), sixty-one rectangles (resonators), and sixty-one circles (languids), one of each for every note on the keyboard. Each is a different size. While the length of the pipes halve at every octave, the diameters of the pipes halve every seventeen notes or so. It is that halving that keeps scales (diameters) of the treble pipes large enough to speak, and it is that halving at seventeen that forms the beautiful parabola of the tops of the pipes as they sit on a windchest. When all those pieces are laid out in order on a table, they show the image of a rank of pipes. As I can tell the difference between eighteen and twenty millimeters in my fingers, so the pipe maker can pick up one of those rectangles and know what the diameter of the pipe will be.
I wonder how Archimedes came across π. What induced him to think so intently about a circle? Did the formula appear to him in a dream? Did he use trial and error? How did he check himself? Did he draw a grid on a circle and count the squares?
Radical radii
I spent a couple weeks in Germany in September of 2019. I wrote about organs I visited on that trip in the December 2019 issue of The Diapason, pages 14–15. I spent about a week in Überlingen, on the shore of the Bodensee, visiting my friend and colleague Stefan Stürzer, director of the respected organ building firm Glatter-Götz in nearby Pfullendorf, perhaps best known in the United States as builders, with Manuel Rosales, of the iconic “Disney Organ.” I sat one afternoon with Heinz Kremnitzer, the designer and engineer for the company, who told me about the process of designing and making the huge, curved pipes that have given the organ the sobriquet, “A Large Order of Fries.” Frank Gehry, architect of Walt Disney Concert Hall and creator of the organ’s visual design, called for the curves.
The first question was whether such an organ pipe would speak, so Glatter-Götz built low DDDD of the 32′ Violon as a prototype. The curves were marked on the huge boards that would be the sides of the pipes and cut using a hand-held circular saw. Big deal. We all have “Skilsaws” in our shops. But remember, that pipe was almost twenty-eight feet long, the length of an average living room. To assemble the pipe, the flat board that would be the back of the pipe was placed on sawhorses spaced far enough apart that the board sagged to approximate the correct curve. Glue was applied, the pipe assembled, and as anyone who has heard the Disney organ knows, the pipe spoke. Stefan told me that they borrowed dozens of extra clamps from neighboring organ companies to accomplish that complex job.
Each curve is a segment of a circle with a huge radius. Twenty-seven pipes of the 32′ Violon and ten pipes of the 32′ Basson are curved. Four different radii were used: 51.545 meters, 32.102 meters, 20.586 meters, and 13.027 meters. How much is 51.454 meters in feet? 169.11 feet. Double the radius to picture a 338.22-foot circle. That is more than the length of a football field, including both end zones. The length of the segments of those circles would be the speaking length of each pipe. With today’s sophisticated Computer Aided Design (CAD), that would be simple enough to draw. But turning that digital arc into a pencil line on a board is quite a process.
But wait, there is more. Remember there are ten curved reed pipes, the longest of which is over thirty-one feet and remember that reed pipes are tapered. How do you curve a tapered pipe? Easy, there are two different radii for each pipe.
Heinz spent weeks in the Los Angeles offices of Gehry Partners, LLP, designing the complicated supports for the curved pipes. The supports would have universal joints on each end to achieve the multiplicity of angles, and each pipe would have two supports to achieve rigidity. Heinz drew the supports into the CAD drawings, weaving each between the complex shapes and layout of the pipes. Take a look at a photo of the organ and imagine the task. Heinz’s last word on those big, curved pipes, “It was a challenge I really enjoyed.” Great thanks to Stefan Stürzer and Heinz Kremnitzer of Glatter-Götz for giving me permission to publish this fascinating information. I am not going to ask how Gehry arrived at a radius of 51.545 meters as the perfect curve.
A penny for your thoughts?
Our system of telling time has been derived from the movements of celestial bodies. The earth rotates in twenty-four hours. The moon orbits the earth in twenty-seven days. The earth orbits the sun in 365 days. There are anomalies in the way those cycles have been divided. Our months have different numbers of days, and there is a corrective “leap day” every four years allowing us to catch up. The exact measurement of time is a complex science, one that I do not have to worry about because my iPhone is the most accurate clock I have ever had. When I cross into a different time zone (which I will do “full-vax” in two weeks for the first time in almost fifteen months), Steve Jobs gives me a nudge with the exact local time.
Mechanical clocks are marvelous machines, and it takes meticulous attention to achieve really accurate timekeeping. Ian Westworth, the clock mechanic for the Houses of Parliament in Great Britain, is leading a team in the restoration of the Great Clock built in 1859 and installed in the Elizabeth Tower of the Palace of Westminster. While many people think “Big Ben” is the name of the clock, in fact, “Big Ben” is the name of the largest of the five bells, the solemn boom that tolls the hour.
On Tuesday, April 13, 2021, The New York Times published a story by Susanne Fowler under the headline, “What Does It Take to Hear Big Ben Again? 500 Workers and a Hiding Place.” The hiding place is the secret and secure location of the workshop where the clock is being restored. Many of the 500 workers are involved in the restoration of the tower and the four twenty-three-foot glass faces of the clock. An amazing 1,296 pieces of mouth-blown pot opal glass have been made, and the fourteen- and nine-foot hands of the clock are being restored to their original condition.
Mr. Westworth explained how they regulate the speed of the clock to keep accurate time. When the clock is operational, its speed varies by plus or minus two seconds in twenty-four hours. The weight of the pendulum controls the speed of the clock. They have calculated that adding or subtracting the weight of a penny (3.56 grams) changes the speed of the five-ton clock by two-fifths of a second over twenty-four hours. The clock is wound each Monday, Wednesday, and Friday. The clock mechanics keep careful track of the time of striking and adjust the speed at each winding by adding or subtracting a penny or two. That might be the only way you can actually buy time.