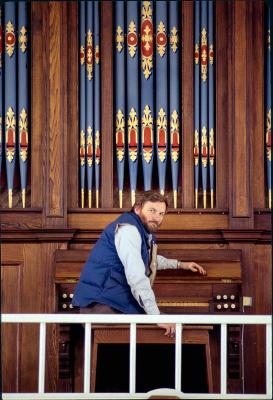
In memory of Alan Laufman: the birth of the Organ Clearing House
I have written often about the dynamic renaissance that dominated the history of the pipe organ in the United States in the second half of the twentieth century. In the 1950s and 1960s, E. Power Biggs toured Europe, bringing home recordings of distinguished historic instruments, catching the ears of the listening public. A large, four-manual tracker organ by Rudolf von Beckerath was installed at Trinity Lutheran Church in Cleveland, Ohio, in 1957, the same year that Biggs arranged for the installation of the iconic Flentrop organ in the museum formerly known as the Busch-Reisinger at Harvard University in Cambridge, Massachusetts. American organbuilders and organists developed a renewed interest in organs with mechanical key actions and low wind pressures because of the clarity of tone and sensitivity of touch. Many new firms devoted to building tracker-action instruments were established, and with that came renewed interest in nineteenth-century American organs with their mechanical action and low-pressure voicing.
The change of direction affected electro-pneumatic instruments as well. In June 1956, G. Donald Harrison was hurrying to finish the new Aeolian-Skinner organ at Saint Thomas Church on Fifth Avenue in New York City, a substantial “American Classic” rebuild of the original Skinner organ built in 1912. The national convention of the American Guild of Organists would be held in the city later that month, and Pierre Cochereau, organist of the Cathedral of Notre Dame in Paris, France, was scheduled to play the new organ for the convention. There was both a heat wave and a taxi strike in New York, and after working into the evening on June 14, Harrison had to walk home to his apartment on Third Avenue. After dinner, while watching Victor Borge on television, G. Donald Harrison died of a massive heart attack. He was sixty-seven years old.
By coincidence, John Scott, the brilliant British organist whose tenure as organist at Saint Thomas ended with his untimely death in 2015, was born on June 18, 1956, four days after the death of G. Donald Harrison.
On June 27, less than two weeks after Harrison’s death, with the AGO convention in full swing, a group of ten people interested in historic American organs gathered in the choir room of Saint Bartholomew’s Church on Park Avenue to discuss the possibility of forming an organization for like-minded people. Present were Horace Douglas, Dorothy Ballinger, Robert Clawson, Albert F. Robinson, Barbara J. Owen, Donald Paterson, Kenneth F. Simmons, Charlene E. Simmons, Homer D. Blanchard, and Randall E. Wagner. They discussed the possibility of maintaining a list of endangered instruments and publishing a newsletter for the exchange of information of interest to members, and the Organ Historical Society was born. Barbara Owen and Randy Wagner are the two survivors of that group.*
One of the many reasons why historic organs were being threatened came from an act of Congress. The Federal Aid Highway Act passed in 1956 led to the creation of the Dwight D. Eisenhower National System of Interstate and Defense Highways (the Interstate Highway System). As commander of Allied Forces in Europe during World War II, Eisenhower had been impressed by the importance of the German autobahn system in the mobilization of the military, and building highways was a priority of his presidency. It is difficult to imagine the United States without interstate highways, but their construction caused significant collateral damage as rights of way were carved through American cities causing the destruction of countless buildings, including churches and their pipe organs.
Barbara Owen was the first keeper of the endangered organ list. She solicited information from colleagues around the country and published the list in the mimeographed (remember that smell?) newsletter of the foundling OHS. Within a couple years, the newsletter was replaced by the society’s professionally printed journal, The Tracker, and Alan Laufman became interested in the movement to preserve historic organs. Around 1960, Alan assumed responsibility for the list of endangered organs; in 1961, he petitioned the board of the OHS to allow him to spin “The List” into an independent company, and by 1962, Alan Laufman was listed as director of the Organ Clearing House on the masthead of The Tracker.*
Alan Miller Laufman (1935–2000)
Alan was born in Arlington, Massachusetts. He taught English at Saint Thomas Choir School and later at the Thomas More School in Harrisville, New Hampshire. He was interested in the organ as a child, an interest that was surely nurtured during his time at Saint Thomas. In the early days of the Organ Clearing House, Alan was able to turn the list into action, finding homes for organs slated for destruction. He organized deals between churches that would cover moving costs and solicited thousands of hours of volunteer labor from organbuilders, organists, and enthusiasts. Parishioners provided lodging and meals, and organs were moved by the dozen at low cost.
Decades before the introduction of cell phones, Alan would commandeer the phone of the church where he was working, calling all over the country to arrange the next deal. Gradually, the operation became professional. Organs were delivered to organbuilders’ workshops for restoration. A permanent, paid crew was established, many of whom joined the company because they happened to live near where a project was underway. Alan would approach a group of kids, asking if they wanted to “earn some money over the weekend.” Amory Atkins, who first worked with Alan in 1978, and Joshua Wood, who joined in 1986, became Alan’s business partners and are officers in the company today.
Dozens, then hundreds of wonderful organs of all sizes by such builders as Hook, Hook & Hastings, Hutchings, Stevens, Erben, Jardine, Barckhoff, and Appleton were given “second wind” through Alan’s efforts. Organs facing demolition typically were moved without purchase price; so, from the beginning, the OCH charged a finder’s fee to the recipient of an instrument rather than receiving a sales commission.
Alan maintained the list of available organs in large, three-ring binders, typically one page per organ. He called the binders “The Family Album.” There would be a snapshot, a stoplist, and a brief description of the organ, its location, and situation. In the late 1980s and through the 1990s, I was running the Bishop Organ Company in the Boston area, and I was able to sell several organs to my clients through OCH with Alan’s help. I recall the lengthy phone calls as I described the buildings where an organ might be installed. Alan was often casually munching on something as he rifled through those binders. I would hear the click as he snapped the rings open and the creak of his desk chair as he swiveled toward the fax machine. Through the miracle of then-modern technology, I would receive pages describing a few organs Alan thought might be good candidates. The snapshots were taped to the three-hole page and showed up on the faxes as black blobs. “Laufman and his black blobs” was a common snicker between organbuilders. Looking back, it seems primitive, but it sure was effective, and I know many other organ guys listened to the munching and creaking as they received their black blobs.
A few examples
In 1981, the Metropolitan Museum of Art in New York City acquired an organ built in 1830 by Thomas Appleton through the Organ Clearing House. Sacred Heart Catholic Church in Plains, Pennsylvania (near Wilkes-Barre), was closing, and the OCH removed the organ and delivered it to the workshop of Mann & Trupiano for restoration. It was installed in the balcony in the grand acoustic of the marble Equestrian Gallery of the Pierpont Morgan Wing where it joined the museum’s iconic collection of musical instruments. The organ has more recently been removed for cleaning and renovation and returned to its lofty location concurrent with the renovation of the gallery. The oldest organ in the United States was built by Snetzler of London in 1762—it is located in the Congregational Church of South Dennis, Massachusetts. There are a few British-built instruments in the Boston area dating from around 1800, and there is a two-manual organ built in 1800 by David Tannenberg at Old Salem, North Carolina. With those, the Appleton organ at the “Met” is one of the earliest extant American-built organs and perhaps the second oldest with two manuals.
One of the grandest OCH relocation projects involved the 1871 organ with three manuals and fifty-four stops built by E. & G. G. Hook of Boston for Saint Alphonsus Catholic Church on West Broadway in New York City, near the entrance to the Holland Tunnel. The church was to be demolished to make space for a parking garage. There is a luxury apartment complex at that address today. This massive organ is over fifty feet tall, including the seven-foot-tall angels perched high atop the pedal towers. Ithaca, New York, area organbuilder Culver “Cullie” Mowers told of transporting those angels from New York to New Haven in his “Beech Wagon.” Driving through a toll booth on Interstate 95, the toll-taker took a look and asked, “Where are you taking them?” Alan gathered a large crew to remove the organ from its original home and created a consortium of organbuilders to renovate the instrument and install it at Saint Mary’s Catholic Church in New Haven, Connecticut. The project started in 1981, the same year as the relocation of the Appleton organ, and was completed in 1982.
Transitions
In July 2000, the Organ Historical Society held its convention in Boston at the Park Plaza Hotel. Though he was suffering from cancer, Alan addressed the convention, traveling across town from the hospital to speak about the history of the Organ Clearing House. During that lecture, he estimated that in nearly forty years he had been involved directly or indirectly in the relocation of more than two thousand pipe organs. Later that week, Amory, Joshua, and I met with Alan in his hospital room to discuss my succeeding Alan as director of the OCH, allowing the company to continue supporting their families and to continue the work that Alan had started and nurtured. We all shook hands, and Amory made the quip that has defined my life since, “Okay John, you kill ’em, and we’ll skin ’em.”
As Alan’s condition worsened, hospice care was set up for him in the front room of Amory’s house in Cambridge, Massachusetts, where friends and family, colleagues and associates traveled from far afield to visit Alan. The number of people who passed through that house during the fall of 2000 is tribute to Alan’s influence on the world of the pipe organ and the wide reach of his professionalism and friendships. Amory, his wife Virginia, and children Ty and Sydney gave Alan a profound gift by making the farewell procession possible. He passed away during the evening of November 30, 2000.
Alan’s memorial service was held at the Church of the Immaculate Conception, the Jesuit Urban Center in Boston, home of the monumental four-manual 1902 Hook & Hastings organ, created by the rebuilding of E. & G. G. Hook’s Opus 322 (1863). Thomas Murray played the organ, and I’ll not forget the experience of singing ST. CLEMENT (“The day Thou gavest, Lord, is ended . . .”) with the vast, musically sophisticated congregation.
Alan lived in Harrisville, New Hampshire, for many years, a community he served as a selectman. He brought a one-manual Hook organ to Saint Denis Catholic Church, which he played for services when he was at home. His ashes were interred in Saint Denis Cemetery, enclosed in a box made by a colleague organbuilder from an old bass Bourdon pipe.
Among his many accomplishments, Alan was especially proud of the twenty-seven issues of The Organ Handbook he produced annually as editor from 1972 until 1999. Those publications were the program guides for conventions of the Organ Historical Society, and along with schedules and recital programs, they included organ specifications and historical essays about each instrument visited. Alan spent months in each convention city, visiting each instrument and researching the history of the organs and their buildings. Each volume was scholarly, comprehensive, and impeccably accurate. Complete sets of these vital books documenting hundreds of organs are to be seen in the offices of organists and organbuilders all across the country.*
Organbuilder David Wallace of Gorham, Maine, first met Alan at the 1963 OHS convention in Portland, Maine, and has been associated with the Kotzschmar Organ (Austin Organ Company, 1912, five manuals, ninety-six ranks) in Portland’s City Hall since he was a child. David tells of a conversation with Alan at the 1983 OHS/AGO convention in Worcester, Massachusetts, that has helped guide his career. Alan was asking David about the efforts to preserve the Kotzschmar Organ that was by then in poor condition having fallen victim to municipal budget cuts a few years earlier. A passerby cut in, “Why don’t they get rid of that piece of junk and get something decent in there.” After a stunned silence, Alan replied, “Because it is a noteworthy instrument on a global basis that significantly merits preservation.” Now David was stunned, “. . . here was the sacrosanct nineteenth-century organ hero Alan Laufman advocating for an over-the-hill twentieth-century orchestral organ.” Alan went on to say that each individual organ should be looked at with an eye for what it has to offer, not only its past but also what it can carry to the future. Recently, the organ has been thoroughly renovated and is in terrific condition well into its second century.
And the rest is history.
Since Alan’s death, the Organ Clearing House has continued the work of maintaining information about available organs, placing instruments in appropriate new homes. The pace has slowed to an average of about fifteen sales a year, and the emphasis has changed from the ubiquitous ten-stop Hook & Hastings organ to three and four-manual electro-pneumatic instruments. With organists’ renewed interest in orchestral transcriptions and complex Romantic music, the organs most likely to sell are those with lots of solo voices and fundamental tone, at least two expressive divisions (preferably more), and state-of-the-art consoles with the latest of whizbang solid-state gadgets allowing hundreds of registration changes at the speed of light.
The company has evolved to offer new services. With the experience of dismantling hundreds (thousands?) of pipe organs, we are specialists in hoisting and rigging delicate and heavy components inside ornate buildings chock full of precious artworks, and we are frequently engaged to assist organbuilders in the installation of new organs, erecting scaffold towers with hoisting equipment that rolls along I-beams on trolleys, and engaging truck transportation and overseas shipments. We have sent organs to Madagascar, Bolivia, New Zealand, China, Australia, Great Britain, and Germany. We cover organs for protection during building renovation, and we provide consultation services, advising owners of organs about their care, improvement, and replacement.
We prepare empty organ chambers for the installation of an organ, building level floors, repairing leaking gallery windows, plastering and painting, and working with HVAC, plumbing, electrical, and fire protection contractors to ensure a safe home for the organ. And we have enhanced, renovated, and installed organs under our own name. We are especially proud of the three-manual 1915 Casavant organ we moved from Maine to the Upper East Side of New York City, transforming it from a country organ to a city organ, and from a “downstairs church organ” to an “upstairs church organ.”
I have been director of the Organ Clearing House for twenty years, and I’m the new guy. Amory Atkins, Joshua Wood, Terence Atkin, and I all worked with and for Alan, and his influence is very much alive in our work. I was invited in 2008 to visit Madagascar by the country’s Federal President, Marc Ravalomanana, who was also an official of the national Protestant Church, to study the possibility of bringing American organs to Malagash churches. My “cold call” came from Madagascar’s Ambassador to the United Nations, Zina Andrianarivelo. Zina took me to the Presidential Palace in Antananarivo, the capitol city. Sitting in an upholstered chair waiting for my meeting with the president, I thought, “Alan would have loved this.”
* Thanks to the Organ Historical Society Library and Archives and archivist Bynum Petty for supplying and confirming this historical information.
Photo: Alan Laufman in 1979 at a Stevens organ, Blue Hill, Maine (photo credit: William T. Van Pelt)