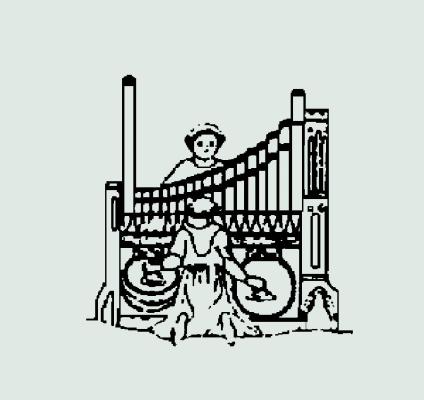
Connectivity
It does not seem that long ago that packing a briefcase for a business trip meant gathering file folders and notebooks. Today, all my files are digital, and my briefcase is full of chargers for iPhone and iPad and the power cord for my laptop. I admit to carrying an HDMI cord with adapters so I can plug into the television in a hotel room and watch movies or other good stuff using laptop, iPad, or phone, and I carry an extension cord to be sure I can set up camp comfortably. I add to all that a Bluetooth speaker so I can listen to music and NPR programs with rich sound. There are a lot of wires in my wireless life.
My desk at home similarly includes wires that make the essential connections of my life, and I had to add one more yesterday. The printer in a drawer under my desk, happily connected to Wi-Fi, suddenly went hermit on me and refused to perform. I ascertained that the Wi-Fi connection had failed and spent most of an hour mucking around with passwords, straightened paper clips, and reset buttons . . . to no avail. If this had happened at our home in Maine, I would have jumped into the car (it was snowing) and driven forty-five minutes to Staples to buy a cord. Luckily, I was in New York, where Staples is immediately across the street from us. The only door I have to pass is an ATM. Even though it was snowing, I did not bother with a jacket and ran across to get the cord. I fished it through the hole I had made for the printer’s power cord, and I was back in business.
I suppose I will want to renew the Wi-Fi connection sooner or later, but as I only paid $125 for the printer, I may just buy another one rather than spending more time trouble-shooting. Wendy’s printer is working fine, as is all of our other wireless gear, so I feel safe assuming that the printer is the culprit. It is not all that long ago that I put paper directly into a typewriter, and there was no question about the need for connectivity.
§
Toward the end of the nineteenth century, scientists and engineers were racing against each other to perfect the harnessing and application of electricity for everyday life. J. P. Morgan’s mansion at Madison Avenue and East 36th Street in New York City was illuminated by Thomas Edison in 1882. There was a fire that spoiled Mr. Morgan’s expensively appointed study that necessitated replacing a lot of wiring, but he was very proud to be on the forefront of that revolution and invited hundreds of people to parties at his home, encouraging them to marvel at the new equipment.
Three years earlier, E. & G. G. Hook & Hastings had completed a 101-rank masterpiece of an organ for the Cathedral of the Holy Cross in Boston, Massachusetts. I have not done the research, but I feel safe guessing that it was the largest organ in the United States at that time. (https://pipeorgandatabase.org/OrganDetails.php?OrganID=7254) Just look at that Great Chorus! Though the organ now has electric action opening the pallets, it was built without electricity, with mechanical key and stop action and a human-powered wind system.
Within ten years of the completion of the organ at Holy Cross, organbuilders were experimenting with electric power in pipe organs. Builders like George Hutchings and Ernest M. Skinner were developing the electro-pneumatic actions with which we are familiar today. In 1906, Mr. Skinner completed his massive instrument (Opus 150) for the newly unfinished Cathedral of St. John the Divine in New York City. With four manuals and eighty-four ranks, it was among the first really large fully electro-pneumatic organs in the world, completed just twenty-four years after the Holy Cross organ. (http://aeolianskinner.organhistoricalsociety.net/Specs/Op00150.html) And by the way, it had electric blowers.
That was quite a revolution. It took barely a generation to move from tracker action, proven to be reliable for over five hundred years, to electro-pneumatic action—that new-fangled, up-and-coming creation that provided organists with combination actions, comfortable ergonomic consoles (decades before the invention of the word ergonomic), myriad gadgets to aid registrations, and, perhaps most important, unlimited wind supplies. Many organists were skeptical of the new actions, thinking that because they were not direct they could not be musical.
In spite of the skepticism, electro-pneumatic organs sold like fried dough at the state fair. Before the end of 1915, the Ernest M. Skinner Company produced more than 140 organs (more than ten per year), forty-six of which had four manuals. (Who would like to go on a tour of forty-six pre-World War I four-manual Skinner organs? Raise your hand!) The negative side of this is the number of wonderful nineteenth-century tracker organs that were discarded in the name of progress, but it is hard to judge whether the preservation of those instruments would have been advantageous over the miracles of the innovation of electro-pneumatic action.
And a generation later, what went around came around when the new interest in tracker-action organs surged, and scores of distinguished electro-pneumatic organs were discarded in favor of new organs with low wind pressure and lots of stops of high pitch.
§
Early electro-pneumatic organs relied on elaborate electro-pneumatic-mechanical switching systems for their operation. Keyboard contacts operated matrix relays to control keyboard and stop actions. Consoles were packed full of coupling and combination machines, inspired along with the development of the vast multiplication of switching systems that supported the spread of the telephone. The wiring diagram of a Skinner organ is remarkably similar to the old telephone switchboards where operators inserted quarter-inch plugs into sockets to connect calls.
Along with “traditional” organs for churches and concert halls, the advance of electric actions fostered the theatre organ, a vehicle that allowed a musician to rollick through the countryside along with the antics and passions of the actors on the screen. The invention of double-touch keyboards expanded the scope of organ switching, as did the ubiquitous “toy counters” that duplicated the sounds of cow bells, train whistles, sleigh bells, thunder and lightning, car horns, and dozens of other sound effects that might have a use during a movie. Those novelty sounds were not synthesized, but produced by the actual instrument being manipulated, struck, shaken, or stirred by an electro-pneumatic device. Push the button marked “Castanets,” and a half-dozen sets of castanets sound across the Sea of Galilee. Ole!
The original switching system of a big electro-pneumatic organ is a thing to behold—electric relays in rows of sixty-one, seventy-three, or eighty-five (depending on the number of octaves in a rank, a windchest, or a keyboard). Each relay has a contact for each function a given key can perform. In a big four-manual organ with sub, unison, and super couplers every which way, multiple windchests for each division, and unified stops around the edges, one note of the Great keyboard might have as many as twenty contacts in various forms. Sometimes you see that many contacts physically mounted on each key, with miniscule spacing, and tiny dots of solder holding the connections fast. Spill a cup of coffee into that keyboard, and your organ technician will spend scores of billable hours cleaning up after you.
One organ I worked on for years was in fact two. The organ(s) at Trinity Church in Boston included a three-manual instrument in the chancel and a four-manual job in the rear gallery. Of course, both had pedal divisions. The console functioned as a remote-control device, its keyboards, stopknobs, pistons, and expression pedals operated a complex relay in a basement room directly below. The outputs for seven keyboards and two pedalboards (491), 175 stop knobs, 45 coupler tabs, 7 pistons, and 4 expression pedals (48 for shutters, 60 for crescendo) were in the cable going to the basement, a total of 826 conductors. But wait, there’s more. Since the combination action was also in the basement, the conductors from the combination action that operated the drawknobs and couplers were in the same conduit, bringing signals up from the basement. Drawknobs and couplers totaled 220, and each needed three wires (on coil, off coil, and sense contact)—660. All together, the console cable comprised 1,486 conductors.
When my company was engaged to install the new solid-state switching and combinations in that organ, we wired all the equipment to the existing relays in the basement and chambers, bought an orphaned console for temporary use and equipped it with new stop jambs with knob layout identical to the original, and set everything up with plug-in connectors. After the evening service one Sunday, we cut the console cable, dragged the original console out of the way, placed the temporary console, and started plugging things in. With just a little smoke escaping, we had the organ up and running in time for the Friday noon recital. One glitch turned up. One of my employees consistently reversed the violet/blue pair of conductors in our new color-coded cable so throughout the complex organ, #41 and #42 (soprano E and F) were mixed up!
When something goes wrong like a dead note or a cipher, physical electric contacts are fairly easy to trouble-shoot. Once you have acclimated yourself to the correct location, you are likely to be able to see the problem. It might be a bit of schmutz keeping contacts from moving or touching, it might be a contact wire bent by a passing mouse. Organ relays are often located in dirty basements where spiders catch prey, stonewalls weep with moisture, and careless custodians toss detritus into mysterious dark rooms. Many is the time I have seen the like of signs from a 1963 rummage sale heaped on top of delicate switching equipment.
Oxidation is another enemy of organ contacts that are typically made of phosphorous bronze wire that reacts with oxygen to form a non-conductive coating, inhibiting the operation of the contacts. Also, in a simple circuit that includes a power supply (organ rectifier), switch (keyboard contact), and appliance (chest magnet), a “fly-back” spark jumps across the space between contacts as a note is released. Each spark burns away a teeny bit of metal until after millions of repetitions the contact breaks causing a dead note. You can see this sparking clearly when you sit with a switch-stack with the lights off while the organ is being played.
You can retro fit a switching system by installing diodes in each circuit (which means rows of sixty-one) that arrest the sparks. You can replace phosphorous bronze with silver wire that does not oxidize, but you still have to keep the whole thing clean and protected from physical harm.
§
Just as the telephone companies have converted to solid-state switching, so has the pipe organ industry. Solid-state equipment is no longer new; in fact, it has been around as long as electro-pneumatic organs were before the revival of tracker organs. But perhaps some of you don’t actually know what “solid-state” means. A solid-state device controls electricity without any physical motion. Circuits are built using semi-conductors. What is a semi-conductor? A device that conducts electricity under certain circumstances or in particular ways, less fully than a standard conductor. A piece of wire is a conductor. Electricity travels freely over a piece of wire in any direction.
A great example of a semi-conductor is the diode I mentioned earlier that contains “fly-back” sparks when a circuit is broken. The diode can do this because it conducts electricity in only one direction. It has a wire on each end to connect to a circuit, and power can flow from the switch through the diode to the magnet (if you have installed it facing the right way!). When the contact is released, the power cannot come back through the diode from the magnet to the switch. Semi-conductor.
Some semi-conductors are in fact switches (transistors) with three legs. Apply power to one leg, and power flows through the other two. Integrated circuits are simply little gadgets that contain many transistors. Resistors are gadgets that reduce the flow of power by resisting it. The advance of electronics has been enabled by the reduction of size of these components. I have transistors in my toolbox that are replacements for common organ controls that are each the size of my pinkie fingernail. Huge! I have no idea how many circuits there are in my iPhone, but it must be millions.
I first worked with solid-state organ actions in the late 1970s. One job was in a rickety Anglican church on East 55th Street in Cleveland where we were installing one of the earliest Peterson combination actions in an old Holtkamp organ. The church had a dirt crawl space instead of a basement, and as the apprentice, it was my job to crawl on my belly with the rats (yup, lots of them), trailing cables from chamber to console. We followed the directions meticulously, made all the connections carefully, crossed our fingers, and turned it on. Some smoke came out. It took us a couple hours to sort out the problem, and we had to wait a few days for replacement parts, but the second time it worked perfectly. I do not believe we were very sure of what we had done, but we sure were pleased.
In around 1987, I became curator of the marvelous Aeolian-Skinner organ (Opus 1202, 1951) at the First Church of Christ, Scientist (The Mother Church) in Boston. With over 230 ranks and 13,000 pipes, the instrument had heaps of electro-pneumatic-mechanical relays. As I came onboard, wire contacts had started to break at a rapid rate, and as the switches were mounted vertically, when a contact broke, it would fall and lodge across its neighbors causing cluster ciphers. Ronald Paul of Salt Lake City, Utah, had been contracted to install a new solid-state switching system, and I was on hand to help him with many details. I was assuming the care of the organ from Jason McKown who had worked personally with Ernest Skinner at the Skinner Organ Company and cared for the Mother Church organ since it was installed. Jason was in his eighties and still climbed the hundreds of rungs and steps involved in reaching the far reaches of that massive organ.
Jason looked over all the shiny gear, bristling with rows of pins and filled with those fiberglass cards covered with mysterious bugs, shook his head, and said, “this is for you young fellows.”
Swing wide the gates.
Over the past fifty years, most of us have gotten used to solid-state pipe organ actions. In that time, we have seen the medium of connections go from regular old organ cable to “Cat5” to optical fiber. I know that some of the firms that supply this equipment are experimenting with wireless connections. I suppose I may be asked to install such a system someday, but while I am committed to solid-state switching and all its benefits, I am skeptical about wireless.
Forty years ago, I was organist at a church in Cleveland that had a small and ancient electronic organ in the chapel. I was happy enough that I almost never had to play it, but there was one Thanksgiving Day when the pastor chose to lead an early morning worship service in the chapel. Halfway through that service, human voices blared out of the organ, decidedly irreverent human voices. The organ was picking up citizens band radio transmissions from Euclid Avenue in front of the church. I dove for the power cord. “Roger that, good buddy. Over and out!”
We have wireless remote controls for televisions, receivers, radios, even electric fans, and it is often necessary to punch a button repeatedly to get the desired function to work. And there was that printer yesterday, choosing idly to skip the bounds of our Wi-Fi router and booster, requiring the introduction of a new wire.
When I think of a wireless connection between the console and chambers of a large pipe organ, I imagine sweeping onto the bench, robes a-flutter, turning on the organ, pushing a piston, and garage doors throughout the neighborhood randomly opening and closing. Swing wide the gates, I’m coming home.