John Bishop is executive director of the Organ Clearing House.
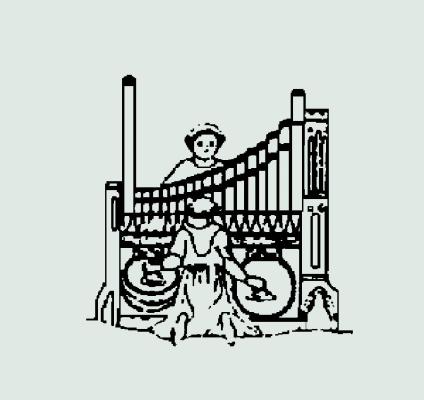
Semantic antics and a few rhetorical questions
What does it mean to restore an organ?
If you start with a simple ordinary pipe organ in poor condition, releather windchests, add a few stops, revoice a few more, and install a fancy solid-state combination action, have you restored the organ? Many practitioners would say no. A strict literal interpretation of the word implies that you would use nothing that had not been part of the original organ. This interpretation implies that while you might be exactly faithful to the work of the original builder, you almost certainly leave behind an organ that cannot be played. You didn’t replace any worn leather, any broken trackers, or any missing ivories.
When a museum conservator prepares a newly acquired chair for exhibition, it’s possible and logical to use the literal approach. No one expects to be able to sit in a chair from Marie Antoinette’s boudoir so there’s no need for strengthening the frame or replacing the upholstery. It’s safely placed behind velvet ropes and as long as it can hold itself up, it’s fine. But, except in the rarest situations, when we restore an organ we certainly do intend to play it as if it were a new instrument.
It’s common therefore for organbuilders to take the word restore with a grain of salt. We restore the instrument to its original playable condition, replacing leather and other parts and materials. We make concessions so the bench won’t collapse and so we don’t have to hand-pump the organ every time it’s played. But again, we have a literal translation. If the original builder used sheepskin, we don’t use goatskin. We match the colors and composition of the felt, the hand-made metal hardware, the chemistry of the wood finish.
When you finish a true restoration, you’ve left nothing in the organ that came from a hardware store or a supply catalogue. Instead of paying thirty dollars for a gallon of stain, you’ve paid a chemist $250; instead of buying threaded wires from a catalogue for twenty dollars per hundred, you’ve paid a machine shop seventy-five plus a $200 set-up fee. And for each of those transactions you’ve spent fifteen hours researching who could do the work for you and making the necessary arrangements. You’re perilously close to the legends of military purchasing—the land of the $10,000 toilet seat. Or the cost of the fish you catch from a new boat—the first fish costs $10,000 or $20,000 a pound and it takes a long time and a lot of fish before it averages into anything reasonable! The cost of the authentic restoration is greater than the price of the comparable new organ.
Another loaded word in the conservator’s lexicon is preservation. In a project completed last year, Old Salem (the wonderful museum village at Winston-Salem, North Carolina) oversaw the restoration of a marvelous organ built by David Tannenberg in 1800. The organ had been dismantled a century earlier and stored in the attic of a church building. Taylor & Boody Organbuilders of Staunton, Virginia accomplished this exacting important work. The project was celebrated and discussed in great detail at a symposium held at Old Salem in March 2004. Historians, preservationists, and restorers gave papers discussing the theories of restoration from different points of view. One concept mentioned was that the purest way to handle the preservation of this important artifact of American heritage would be to catalogue the parts and preserve them intact—façade pipes left flat, keyboards missing, parts and pipes in a shambles.
That concept of preservation was compromised as Taylor & Boody, guided by officials at Old Salem (notably Paula Locklair), appropriately restored the organ to playable condition. They built new keyboards according to models from other surviving Tannenberg organs, they rounded out the façade pipes, they lengthened other pipes to make the pitch established by those façade pipes, and they used the tuning system described by Tannenberg. That description was in itself a masterpiece of preservation. Several years after the organ was built, the church asked Tannenberg to return to tune it. He refused, but instead sent a letter that described in careful detail how to set the temperament and tune the organ. The Moravian Archives at Old Salem has preserved the letter and it was on display during the symposium. What a treasure.
By restoring the organ to playable condition, Taylor & Boody and Old Salem have provided an unparalleled opportunity for us to understand the work of David Tannenberg. Without the handling and working of those precious organ parts, we would not know the sound, the essence of the instrument. In the interest of preservation, taking advantage of technology available to us, the artisans at Taylor & Boody documented everything by photograph and measurement.
Here’s a hypothetical twist: An organbuilder is engaged to restore an important organ. During the initial study of the instrument, the organbuilder comes across original parts of the organ that failed over time because they were not designed and built to take the mechanical strain they were subjected to. The restorer (in all humility) realizes the reason for the failure and can easily see how to redesign the offending part so it will not fail in the restored organ. But is that restoration? Technically no. It’s a modification to the intent and product of the original builder. In this case, you could say that a literal restoration would be a recipe for failure. Does that justify making the change, ensuring that the “restored” organ will last longer than the original?
And here’s another twist: Five years ago the Organ Clearing House “rescued” a beautiful organ built by William A. Johnson of Westfield, Massachusetts in 1883. It has two manuals and twenty-seven stops, a beautiful Victorian case, and its historic value is high because it had never been altered. It was in a church building in the Williamsburg neighborhood of Brooklyn, New York that was scheduled to be razed. With the financial assistance of many members of the Organ Historical Society, we dismantled and packed the organ, and shipped it to our warehouse in New Hampshire. There it sits.
Many potential purchasers have expressed interest in the organ, but each described plans to add an electric stop action and combination action to the organ. I’d hate to see that organ altered. After all, much of the reason we put so much effort into the organ was that it is such a rich, unaltered example of an important era of American organbuilding. But what’s the point of preserving an organ if it’s going to languish in storage? We can walk around it in the warehouse, admiring it in pieces, and patting ourselves on the back for what a wonderful job we did (and pay another month’s rent on the space). And, as I did recently, we can drive past the site in Brooklyn and see that the organ’s original home is gone. But we can’t hear the organ.
This raises a question much discussed among organbuilders who restore, renovate, refurbish, rebuild, or otherwise rehash pipe organs—a question that is relevant when discussing organs of some historic importance and especially when discussing relocating an instrument when there is need to adapt it to fit the space: Are “reversible” modifications appropriate? Maybe the original specification does not include a pedal reed, or maybe there is a lack of upperwork on the secondary manual. It’s technically possible to add a pedal reed to an organ in such a way that it could be removed later leaving little or no trace for the sake of historic purity. Would that compromise the integrity of the instrument? Is it presumptuous of us to imply that we know better than the original builder?
Returning to my example of the stored Johnson organ, suppose we found a way to add electric slider-motors to the organ, to replace the keyslips with new ones equipped with piston buttons (of course, preserving the originals with all their hardware), and to install a solid-state combination action, all in such a way that the whole thing could be reversed, returning the organ to its original condition. We would have necessarily made some screw holes, and there would surely be holes in the frame of the keyboards to accommodate the pistons. But if that meant that the organ was taken from storage and put back into use, are the changes so bad?
In 1870, E. & G. G. Hook built a large three-manual organ for the First Unitarian Church of Woburn, Massachusetts. When the parish disbanded, the organ was sold to a church in what had been East Berlin, Germany. The organbuilding firm of Hermann Eule in Bautzen, Germany was selected to “restore” the organ and install it in the Church of the Holy Cross (Kirche zum heiligen Kreuz) in Berlin. By the way, Bautzen is a lovely picturesque town, about two hours’ drive east of Dresden, near the border of Czechoslovakia. In Woburn, the organ was installed in a chamber behind a proscenium arch. The opening of the arch was much smaller than the organ so the organ’s sound was confined. In Berlin, the organ was installed free-standing in a spacious balcony—the case was expanded and the façade redesigned.
In one sense, this organ was restored. Its stoplist and tonal personality are unchanged. But the organ is fundamentally different. In Woburn, the organ was hidden, and the acoustics of the room were terrible. In Berlin, the organ is in the open, and the acoustics are spectacular. In that sense, it couldn’t be more different. I have seen and played the organ in both locations and I much prefer it in Berlin. Some colleagues grumbled about the way the façade had been altered, but what was so special about the original façade? Sitting in the church in Berlin listening to the organ, a colleague leaned over to me and said, “now they have one of our organs, it’s our turn to import some of their churches!”
If we’re doing a large-scale project on an instrument, how much can we change it and still call it a restoration?
Can we justify changes in the interest of making an instrument more useful?
How do we choose which instruments should be truly restored? Does an organ have to be beautiful to be considered for restoration? And who decides what’s beautiful?
Can we justify making changes to an instrument to correct what we perceive to be defects in the original? Who are we to decide what is defective?
Some historic instruments have short pedal compasses and secondary manuals with many “treble-only” stops. Many modern players will see these as constraints, limiting the usefulness of the instrument. Is it good stewardship for the owner of the instrument to commit to an expensive restoration?
These are questions for the restorers and the owners of the instruments alike. It’s common for the owner to feel that the instrument is worthy of special attention while the organbuilder thinks it has little merit. And of course, the opposite is true—it’s just as common for an organbuilder to work hard to convince the owner of an instrument to commit to an expensive restorative or preservative project when the owner finds the expense hard to justify or the explanation hard to understand.
I’ve had conversations like this with many organbuilders and curators. I’m not offering answers, just framing questions. I welcome your comments at