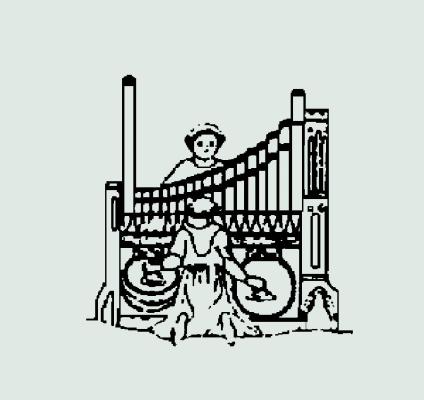
The sum of the parts
Spring comes late where we live. Business travel this year has treated me to springtime in California and Virginia, but here in Maine it’s about thirty degrees this morning. The ground freezes pretty deep here, so when it starts to thaw in spring the moisture cannot seep into the ground. It sits above the freeze level and produces what we affectionately call mud season. The driveway feels like taffy under the wheels of the car, and there are places in the yard where you go in up to your ankles.
Chilly nights continue for another month, so we don’t get the gardens started until mid-May, when we can sneak in the first peas and lettuce. Sounds grim to those of you who live south of us, but the trade-off is that our high summer is glorious with ocean breezes and brilliant sunshine. And by then the garden is filling the kitchen with glory.
Today is the Ides of April, that most taxing day of the year, and although the thermometer warns, it’s sunny and clear and I started the day in the garden cutting back the remains of last year’s perennial growth and raking and turning over the raised beds where we start the early vegetables. One of those beds is devoted to chives and mint, both of which grow abundantly and add much to summer meals. As I cut back the woody sticks of last summer’s mint plants, I got a good whiff of that real minty smell, and my mind went directly to a summer evening cookout, of tzatziki, that cool refreshing dressing made of yoghurt, garlic, olive oil, cucumber, and mint that goes so beautifully with grilled lamb, and of course Mojitos and Gin and Tonics. Or is it Gins and Tonic?
Those mental pictures and virtual smells brought real pleasure to the chore of turning over the soil, reminding me of why we do this work.
Start with the basics
Having my hands in the dirt early this morning reminds me of a sense I like to keep alive in our workshop. There might be a Swell engine on someone’s workbench—a complicated, even goofy-looking contraption with puffers and pullers that was seemingly and improbably inspired by the gear used to hitch up horses. The person at the bench can scrape off old leather and glue on new, lubricate the mechanical parts, clean up the finish and get it ready for new wiring and installation without ever really knowing what the thing is for. I like to be sure that our crew gets to hear organs often enough that they can have some idea of how a machine is used—what it’s for. If while you’re scraping off the leather you can hear in your mind’s ear a processional hymn with swell shutters opening in front of the reeds as the choir reaches the chancel steps, perhaps the machine you’re working on will work a little better when you’re done. It’s the same as smelling that mint on a frosty morning—the tzatziki you make in August will be that much better because you had it in your mind in mid-April.
By the way, The New Heritage Dictionary (Houghton Mifflin 2000) defines “whiffletree” as “The pivoted horizontal crossbar to which the harness traces of a draft animal are attached and which is in turn attached to a vehicle or an implement.” The horse-and-cart whiffletree was the inspiration for Ernest Skinner’s famous Whiffletree Swell Engine. It’s a good thing Ernest was working in the days when you still might see horses hitched to a carriage or we might have Swell motors that incorporate trailer balls.
It’s all in the ingredients
I love to cook. I love thinking about what we’ll have for dinner, being sure that we have everything we need, and firing up the kitchen at quitting time. It’s fun to clean, scrape, chop and combine those ingredients and apply heat to them in just the right way. Will we grill or broil the meat? Will we steam or sauté the vegetables? Should it be dill or tarragon? And the meal is made or broken by the quality of the ingredients you start with. Forty years ago, Julia Child told us not to use that cheap jug wine in your cooking—if you wouldn’t choose to drink it, why would you want to eat it? Since Julia encouraged Americans to feel free to cook well, we’ve lived in a revolution of understanding how important it is to start with the right ingredients. It’s okay to put leftover vegetables in a stock pot, but not rotten ones.
The organbuilder chooses his materials with the same care a chef might use squeezing tomatoes in the market. The chef doesn’t decide on the menu until he’s been to the market. With all the talk about combining flavors to create a finished dish, one of the best tasting things I’ve ever eaten is the hot-in-the-sun cherry tomato snagged off the vine while driving by on a lawnmower. Think of the salad inspired by that flavor. It’s a better salad than the one that’s made because you know there should be lettuce, onion, tomato, and dressing. Make the salad by how each ingredient tastes, not by a standard list.
It’s a little like the organist who automatically draws eight-four-two-mixture without listening, or without thinking of trying it with a soft flute added, a gentle sixteen-foot reed, or leaving out the two-foot to make the sound a little more transparent. Registrations chosen by listening will always sound better than those chosen by list.
The organbuilder comes across a special piece of wood—beautiful grain pattern, unusual colors—sees what it should be made into, and sets it aside for the perfect music rack, name board, bench top, or pipe shade. Fifty years later, the organist sits through the thousandth sermon admiring that beautiful grain pattern. (When I left my last church position to join the Organ Clearing House, I calculated that in seventeen years I had listened to something close to 800 sermons and led close to 2300 hymns. Makes my fingers hurt.)
Remember Michelangelo choosing his piece of marble and removing everything that didn’t look like a saint? The chef starts with a carrot and takes away everything that doesn’t belong in the soup. We chose not to eat the bitter skin or the tough top raw, so why would cooking it make it better?
Likewise, the organbuilder puts a skin of leather on a light table and marks the imperfections with a Sharpie® so he can avoid everything that shouldn’t be part of an organ. A little pinhole in the leather will leak a tiny bit of air and make that pouch move just a touch slower. Will the organist notice that when playing a quick scale or trill? He might not be able to put his finger on it, but there’s something not quite right. And by the way, that pinhole is a weakness in the leather—that pouch will be the first one to fail seventy-five years from now. Maybe it would be five more years before the next one failed. That little pinhole had a noticeable effect on the lifetime of the organ.
The sheep had a run-in with a barbed-wire fence and the resulting scar is a little tough spot in the skin. The pouch made of that piece of leather might open the valve a little cock-eyed. One time in ten thousand, that valve will catch on the edge of the toe-hole and cause a cipher. The same pipe is played three sixteenth-notes later and the cipher goes away, but the observant organist had a split second of wondering what was going on. And it happened so fast that she couldn’t keep track of it and couldn’t write it down after the service. It happens again the next Sunday. This time it doesn’t go away and the cipher interrupts the service, all because the scar stayed in the pouch. It’s like finding a little stone in a beautiful dish of risotto.
We drop a peach in boiling water for a minute or so, and the skin comes off easily. It’s an extra step, you might scald your fingers on the hot peach, but there’s no fuzzy mouthful of skin interrupting the experience of eating the tart. Ptooey!
Before the Swell motor goes back in the organ we clean the pins by scraping with a knife or rubbing with some emery cloth. This guarantees a good connection when the new wire is soldered on. It will never be that a stage of the motor fails to work because of a dirty solder joint. After all, what good is a fifteen-stage Swell motor? That choir mounting the chancel steps wouldn’t notice that stage number 7 didn’t work, but the effect was lessened just a tiny bit. (I get a funny picture in my mind of a couple of indignant choir members confronting the organist after the service complaining that the Swell box didn’t sound just right!) If it’s good enough for government work, is it good enough for God?
If it’s worth doing, it’s worth doing right
I’ve participated in dozens, maybe hundreds of meetings with church committees discussing the sale and purchase of pipe organs. Often enough there’s one guy (it’s always a guy!) who says, “We’ve got a roof that leaks, a parking lot with potholes, the city is making us install an elevator and ramps, and the organist says we need a new organ. What can we do to save some money on this unit?” (It’s the word “unit” that gets me.) I respond, “All those projects are important, but I don’t think that the organ is on the same list as parking lots and elevators. I think it’s on the list with communion silver and stained-glass windows. It’s liturgical art, not a ‘unit.’”
By far the vast percentage of money I’ve earned during my career has been donated money—those cherished funds, prayerfully raised by the faithful of the congregation. On one hand, it’s hard to say that you shouldn’t go with the lowest bidder when purchasing a pipe organ. But in fact, if the organ is liturgical art, doesn’t it somehow transcend money? I know that’s not a practical point of view, but without such thinking how did the great cathedrals get built? Certainly there was a cheaper way to build a huge church than festooning it with vaulted ceilings, and why do you need a three-hundred-foot tower if only to hold up a bell? Those buildings are expressions of faith. The twenty-million-dollar tower is a symbol of faith, forming a physical connection between heaven and earth as if a community were holding its hands to the heavens. You didn’t need that huge stone tower. You didn’t need the simple wooden steeples you see on country churches throughout New England. You didn’t need the expensive stained-glass windows, the carved saints, or the marble altar. And you didn’t need the magnificent pipe organ.
But we have those things, we care for those things, we respect those things because of how effectively they express our faith. The building committee of the First Baptist Church in Damariscotta, Maine didn’t pay for the steeple when the church was built in 1862 because it would look good on twenty-first century postcards, they built it because it would stand as a symbol expressing their faith to their community. It’s at the top of the Main Street hill. You can see it from a couple miles down the river, and you can see it from the highway that bypasses the town. That building committee got their money’s worth. Today the steeple is sitting somewhat forlornly on the lawn next to the church. It was leaning a little to the left and the town participated in a fund-raising drive to rebuild it. No one could imagine the town without it.
So we justify the cost of a pipe organ. As we discuss the specifications and the related costs, we are continually reminded of the need to economize. But can we also inspire that committee to think beyond the nuts and bolts of the price and think of the instrument as the fulfillment of a vision? It’s not a “unit,” it’s an expression of faith. It will be there seventy-five years later for the weddings of their grandchildren. It will be built by craftsmen who know how important it is to scrape those pins, mark those pin-holes, choose those boards. No fifteen-stage Swell engines here.
A carpenter building a house might grab the next two-by-four off the pile and nail it in. It takes a little more time for the organbuilder to set aside that special burl and turn it into a music rack.
The moment when the congregation really understands why the organ would cost so much is the moment it comes out of the truck and its parts are laid out across the backs of the pews. Thousands of parts, each beautifully made. The congregants walk around the room thinking in terms of what they’ve paid for a dining table or a credenza, and the whole thing starts to make sense. Shortly after the Organ Clearing House started installing an organ in Virginia last fall, there was an evening event to which the congregation was invited. More than a hundred people came to see the organ half assembled, to see the parts and pipes spread around the room, and to hear something about how the organ works, how parts are made, how we care for our craft. I like to think that they went home knowing they were getting their money’s worth. I recommend such an evening as part of every installation.
And afterwards, sit down to a meal beautifully prepared from the freshest and finest ingredients, no stones in the risotto, no cheap wine in the sauce, and no fuzz in the tart. If it’s worth doing, it’s worth doing well.
Now that I’ve finished writing, it’s time to go to the market.