John Bishop is executive director of the Organ Clearing House.
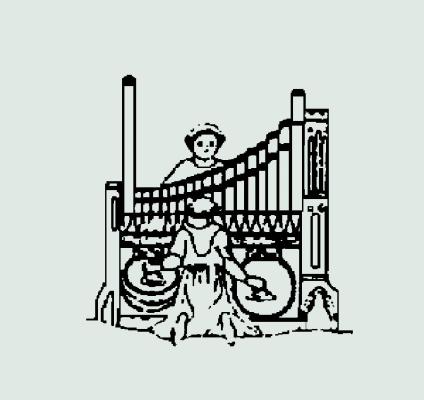
Shiny side up
The work of the Organ Clearing House involves trucks. Lots of trucks. We rent trucks when we are working on projects small enough to fit into a single truck body. And we have a trucking company in Nevada that we call when we need a semi-trailer or a little fleet of semi-trailers. After many years of jumping around from one company to another, it was a relief to begin working consistently with a single firm that could meet most of our needs.
When we are dismantling an organ, loading day is heavy work. A crew runs in and out of a church building all day long carrying heavy parts down stairs and fitting them into a truck like a giant Tetris® game. When the truck is full there’s often a moment when the crew and truck driver “shoot the breeze” for a few minutes before the load hits the road. We’ve heard a few doozies. One driver mentioned that it was a good thing we weren’t sending him to Canada because he had been convicted for smuggling firearms and wasn’t allowed to drive there anymore. We had just loaded an Aeolian-Skinner organ into his trailer.
Sometimes it’s pearls of wisdom: “You can drive down that hill too slow as many times as you want. You can only drive down it too fast once.”
And the friendly greeting as he puts it in gear and lets out the clutch, “keep the shiny side up!” Good advice, especially with my organ in the back!
Skootch
In 1979 I was part of a crew installing a new European organ in Cleveland. (You historians can route out which organ that was . . .) The church’s sexton, a fifty-ish German man, was involved in setting up the scaffolding, and I as “the young guy” was up there with him. As we were putting up the last scaffold frame we ran into the pitch of the ceiling. “Hold this,” he said, handing me the scaffold frame. I was standing on a plank. He pushed against the ceiling with his hands, gave the scaffold tower a kick with both feet, and the whole thing jumped a couple inches toward the center of the room. We were up high enough to be able to put a bridge from the top of the tower across the top of the organ to another tower. It was a three-manual free-standing organ in a classic organ loft with a spiral stairway. Must have been 50 feet. After his kick the tower didn’t stop making noise for several seconds, and because I was holding that frame I couldn’t steady myself. Nothing bad happened, but as I reflect on that moment, especially watching our crews set up massive towers of scaffolding today, I can hardly believe the risk that guy exposed me to without asking. I would have said no.
In another Cleveland church my boss and I witnessed a near disaster. We walked through the nave heading for the rear gallery where we were finishing renovation of the antiphonal organ. The pews were divided into three sections across the room, so there were in effect two center aisles and no side aisles. The walls featured unusually large stained-glass windows. A couple guys from the church’s maintenance staff were changing light bulbs in the chandeliers, using the kind of scaffolding that’s made of two-inch aluminum tubes and has a two-by-six-foot footprint. They were four sections high, and had the outriggers (stabilizers) pointing up the aisles the “long way,” rather than between the pews. From inside the organ chamber we heard “that” noise and ran down the stairs to find the tower at a 45-degree angle, the bottom of the tower still in the aisle, and Mr. Lightbulb on top with his foot on the wall next to a window. A couple inches to the right and he would have gone through the glass and fallen a long way to the lawn. Telling him to hang on, we yanked the tower straight again, and I had to go up to help the guy down.
What kind of maintenance supervisor would let that happen? Oh yeah, in the first story he was the guy on top of the tower with the big feet.
Those little voices
That Cleveland area organbuilder I was working with is Jan Leek of Oberlin, Ohio. I was privileged to work in his shop part time when I was a student, and then full-time for about five years after I graduated. He had learned the trade in Holland in what could best be described as an old-world apprenticeship, and as he taught me how to handle tools and operate machinery, he had a way of saying, “listen for those little voices.” If the little voice in your head says, “you’re going to cut your finger with that chisel if you do that once more,” the little voice is right. It’s a great image, and I am sure that his description taught me to conjure up those voices. I can still hear them. “The paint is going to drip on the carpet.” “The keyboard is going to fall on the floor.” “Your finger will touch that saw blade.”
The apprentice doesn’t hear the voices. The journeyman hears them and doesn’t listen. The master hears them and does listen.
An open quart can of contact cement is sitting on the chancel carpet next to the organ console. Of course it’s going to get knocked over when you stand up. The price of the glue, $4.79. The price of the carpet, $47,500.
A row of tin façade pipes is standing against the workshop wall. A worker is using a five-pound hammer to break up the crates that the pipes came in. The head flies off the hammer and dents one of the pipes, and they all fall over, one at a time in slow motion like 15-foot-tall tin dominos and there’s nothing anyone can do.
Cheery, isn’t it?
This subject is on my mind for several reasons. One is that I’ve spent the last couple days negotiating the rental of a huge amount of scaffolding and rigging equipment for a large project we will start next week, so I’ve been talking with salesmen about weight and height limits and what accessories are necessary to ensure safety. Another reason is that a locally owned small manufacturing company near us suffered a catastrophic fire last week. And as we work with scaffolding companies in New York we hear stories about the construction industry, especially relating to recent serious accidents involving cranes used in the construction of high-rise buildings.
I love the image of the organbuilder at a wooden workbench, a window open next to him providing a gentle breeze, a sharp plane in his hands, and the sweet smell of fresh wood wafting off the workpiece as the shavings curl from the blade of the plane. Or that of the voicer sitting in seclusion with beautiful new pipes in front of him coming to life under his ministrations.
But think of that majestic organ case in the rear gallery with an ornate monumental crown on the top of the center tower, covered with moldings, carvings, and gilding, and pushed up against the ceiling. Uplifting, isn’t it? It might be eight feet long, six feet wide, and three feet tall. It might weigh 500 pounds, and someone had to put it there. Making it is one thing. Getting it 50 feet off the floor and placed on those 20-foot legs that hold it up is another thing altogether. Uplifting, all right.
Organbuilders have a variety of skills. We work with wood, metal, and leather. We work with electricity and solid-state circuitry. We have acute musical ears for discerning minute differences in pipe speech and for setting temperaments. And we must be material handlers—that specialization of moving heavy things around safely.
To put that tower crown in place you need scaffolding, hoisting equipment, and safety gear to keep you from falling. How high up do you need to be before you need that gear? Easy. Ask yourself how far you’re willing to fall. Twenty feet? Thirty feet? Four years ago the Organ Clearing House dismantled the huge Möller organ in the Philadelphia Civic Center. (That organ is now under renovation in the new workshop of the American Organ Institute at the University of Oklahoma.) The organ chamber was above the ceiling, 125 feet above the floor. The demolition company (the building was to be torn down) cut a hole in the floor of the blower room big enough for the organ parts to pass through. And we were left standing on the edge of an abyss. We used full-body harnesses and retractable life lines. If you fell you’d drop about six feet and the ratchet-action of the retractable would stop you, something like the seatbelts in your car. And there you are, hanging 120 feet up.
Away aloft
A sailor hollers “Away aloft” as the halyard hoists the sail up the mast. The rigger might do the same. He ties a line around the load, hooks it to the line from the winch, and up it goes. It’s important to choose the right type of line—you don’t want chanciness caused by a line that stretches, for example. But what really matters is the knots you use. Some knots are meant to slip. Some are meant to be permanent. A favorite is the bowline, which cannot untie, but also cannot pull so tight that it cannot be undone. It was developed by early sailors to tie a ship to a dock or mooring. Think of a large sailing vessel, bow tied to a mooring, bouncing on the waves and pulled by the wind for weeks. There’s a terrific amount of force on that knot. But you give the top of the knot a push sideways and it can be taken apart easily. Beginning sailors are taught how to tie the bowline both left- and right-handed, blindfolded. I once had to tie a bowline while diving under a boat in order to repair a centerboard control.
Different knots are intended for different purposes.
A half-hitch is a great knot for securing something temporarily, but it looks a lot like a slip knot. If you don’t know the difference you might tie a slip knot by mistake. How will that work when the weight of a windchest shifts while being hoisted into the organ?
If your skill set doesn’t include three or four good reliable knots, I recommend you learn them. There are neat books for this purpose, predictably available from boating-supply companies. Some come with little lengths of line so you can practice in the comfort of your home.
When hoisting heavy parts you can also use nylon webbing. It’s available in neat pre-cut lengths with loops on each end for easy tying. The webbing is easy on the corners of the piece you’re lifting, and it’s very strong. A one-inch wide web is rated for 2,000 pounds in vertical lift. But keep a good eye on its condition. Recently there was an eerie photo in the New York Times in the aftermath of the collapse of a construction crane. It showed a piece of torn webbing dangling from a hook. That photo prompted us to purchase new webbing for our next rigging job!
In the nineteenth century, the great Boston organbuilding firm of E. & G.G. Hook suffered two serious fires, both of which destroyed their workshops. I know of two North American organbuilders who have had bad fires in the last decade. Neither was caused by carelessness; in fact, one was caused by lightning. I thought about those two colleague firms working to rebuild their companies when we heard of a terrible fire at a boatyard near us. Washburn & Doughty is a family-owned company with about a hundred employees that builds heavy commercial vessels like tugboats, fireboats, and ferryboats. It’s quite a spectacle to see a hundred-foot tugboat under construction in a small village. And a mighty amount of steel goes into the building of such a boat. On Friday, July 11, sparks from a cutting torch ignited a fire that destroyed the building. It was routine work for a place like that, and newspaper stories told that the fire was officially accidental. They were able to save a hundred-foot tug that had been launched and was being completed at the dock—they cast it adrift! But two others that were still in the buildings were lost and 65 employees were laid off temporarily while the owners work out how to rebuild.
Ten years ago I was restoring an organ built by E. & G.G. Hook with lots of help from volunteers from the parish. We were refinishing the walnut case, and I mentioned the fire hazard of rags that were soaked with linseed oil. They must be spread out to dry. If they’re left in a heap they will spontaneously combust. One of the volunteers took a pile of the rags home and put them in a bucket in the middle of his backyard. He told us later that it had only taken about ten minutes before the bucket was full of fire!
This is a pretty gloomy subject. But I write encouraging my colleagues to look around their workplaces with a critical eye toward safety. Be sure you have the proper gear for lifting and moving the things you’re working on. Store your paints and finishes in a fire-proof cabinet. Eliminate the possibility of sparks finding a pile of sawdust and spread out those oily rags. Encourage your workers to use safety equipment. Safety glasses may look nerdy, but it’s not cool to lose an eye!
Get your hands on a good industrial supply catalogue—I have those from Grainger and McMaster-Carr on my desk. Go to the “safety” pages and leaf through. You’ll see lots of things that protect against stuff you haven’t imagined could happen! Organbuilders are precious. Let’s keep them all in good health.