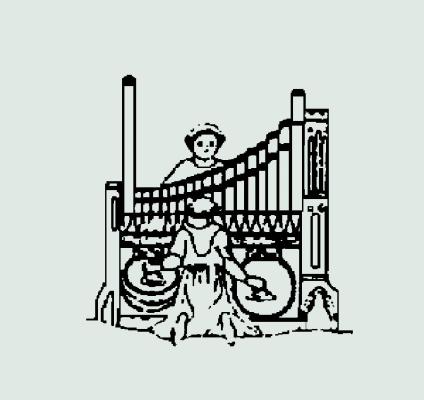
What happens when the pastor and organ committee in an active rural church challenge their congregation to support the purchase of a world-class pipe organ? Members at Zion Lutheran Church in Mascoutah, Illinois (adjacent to Scott Air Force Base and some thirty minutes outside St. Louis, Missouri) began by asking how the organ might enrich their worship experience, whether the organ would encourage member participation, and how the organ could be relied upon to expand the church’s reach into the community. In other words, how would investing in a pipe organ aid in the mission of the church? As a matter of faith, while concerns about costs and logistics were seen as important issues, Zion chose to assign a higher value to their conviction that the organ would significantly enhance their experience and provide a springboard for greater community involvement.
The history of this organ project really began in the late 1990s when the congregation decided to build a new sanctuary. The new building was finished in 2000, but funds for a new or improved organ were not available, so the congregation moved their mid-1950s two-manual, 14-rank Schlicker pipe organ from the much smaller, more reverberant space of the old church building into the new, larger sanctuary, which was plagued with relatively dry acoustics. Once in the new space, the sound produced by the organ was, at best, diminutive and lacked the attributes of foundation, expression, and color. Given its new surroundings and the fact that the congregation follows the Lutheran tradition of “Singing forth with great conviction,” the organ proved to be incapable of leading the congregation.
Rather than conclude that a more substantial pipe organ was outside the realm of possibility, the newly formed organ committee went to their list of preferred builders and asked that each devise options to provide the church with a workable proposal. Like many churches, Zion Lutheran considered that, while there are advantages to an entirely new organ, costs would be such that the resulting instrument would likely be inadequate and would not materially improve their current situation. The congregation also felt that it was important to respect the role played by the 1950s Schlicker and sought to preserve their musical heritage by incorporating resources from the Schlicker into the new organ.
While our firm is primarily involved with building new organs, we find that an increasing number of clients are coming to us with requests similar to that of Zion Lutheran. In these situations we are asked to commit our expertise to locate and adapt existing resources. Not surprisingly, whether with pipes or the organ infrastructure itself, re-tasking such materials to build an organ that is artistically credible and able to stand on its own merits (much less bear our name) is considerably more difficult than having the luxury of specifying every aspect of a new organ. Regardless, this process is becoming a part of the “new normal” and is something that many organ builders are embracing as they strive to meet the needs of their clients.
The question associated with these endeavors is always one of determining the extent to which the proposed organ represents the artistic signature of the original builder, or begins to reflect characteristics typically found in one’s own work. While every situation is different, much depends on whether the proposed resource is an intact instrument deemed worthy of restoration, or whether components from multiple organs are to be refurbished and combined with new construction. When restoring and relocating a noteworthy organ, unless there are significant tonal anomalies, we prefer that the organ continue to represent the intent of the original builder. On the other hand, when working with individual components (primarily pipework), we have the opportunity to elicit modifications that better reflect our own preferences.
Regarding Zion Lutheran, after selecting Parsons, a significant amount of time was spent outlining requirements and refining options. Having previously removed a large Schlicker from Grace Episcopal Church, New York City, Parsons suggested combining portions of the Grace gallery installation with the original Mascoutah Schlicker to form a cohesive three-manual and pedal organ. While the edifice at Grace bears no resemblance to Zion, Mascoutah (in terms of architecture or size), the organ at Grace was known to be underpowered. Wind pressures approaching three inches combined with relatively small-scale pipes proved to be inadequate at Grace. For Zion Lutheran, however, the opposite would be true.
After carefully selecting stops from both organs, ideas began to form that offered exciting possibilities. Further discussions regarding organ infrastructure solidified the concept of rebuilding Grace Episcopal’s Heissler electric-slider windchests and three-manual console, while stipulating the construction of a new wedge-bellows winding system. The resulting specification also called for incorporating a Peterson ICS-4000 solid-state switching system. As the engineering process unfolded, it was determined that volunteer contractors at the church had the credentials to build the Swell enclosure and develop a simple façade. While these are not aspects of the process that Parsons typically relinquishes to its clients, in this instance it was felt to be appropriate.
With the design of the organ taking shape, discussions shifted to acoustics and environmental concerns. Great care was taken during the planning of the new sanctuary to insure that the space was appropriate and welcoming. However, as a trade-off to what was seen as warm and welcoming, the acoustics of the room suffered and resulted in a drier acoustical environment. The wide shape of the room, combined with an unsealed, multi-faceted wood ceiling, single-layer drywall construction, and carpeted floors, created a lackluster acoustic. In addition, because the organ would occupy a large area at the rear of the choir loft, concerns were raised that temperature stratification would cause tuning problems. Noting the critical nature of these issues, the church wisely organized a group of highly skilled individuals to work with Parsons and manage whatever construction processes might be required. With regard to acoustics, it was determined that the walls of the surrounding organ chamber should be hardened, a protruding closet removed, and ceiling areas over the chamber and choir loft be thoroughly sealed. In addition, plans were made to modify choir risers and replace sound-absorbing carpet in the loft and chancel areas with hard-surface flooring. The church agreed to deal with temperature stratification by installing a micro-climate circulation system designed by Parsons to pull air from the bottom of the organ chamber and distribute it across the top of the organ. Following the installation, the various “fixes” proved to be successful. The organ projects nicely into the room, and tuning is extremely stable. The acoustics, while still not “live,” have improved noticeably. It is important to mention that work associated with acoustical remediation, installation of the micro-climate system, and general site preparation (electrical work, flooring, and painting) was carried out in a thoroughly professional manner by Zion volunteers.
Whereas the gallery installation at Grace Episcopal included 61 ranks distributed over Great, Swell, Positiv and Pedal divisions, the organ at Zion Lutheran comprises 36 ranks, distributed over the same divisional configuration. Given the abundant resources from Grace, and the original pipework from Mascoutah, Duane Prill, tonal director at Parsons, was able to recast the organ so that while it remains classically oriented, it possesses a broader, more cohesive sound, with well-developed bass and tenor registers, and improved blending capabilities. As with most projects that incorporate recycled pipes, this project involved a labor-intensive process that included major pipe repairs, initiating and reversing miters, rescaling, and a substantial amount of revoicing, regulation, and tonal finishing. In addition, because Schlicker reeds are characteristically unstable, each rank was completely rebuilt to insure optimal performance. From the perspective of the pipe department, when compared with the process of working with new pipes, achieving excellent results with recycled pipes requires as much, if not more effort. Yet, the result of this effort speaks for itself. The new organ features a warm, rich tone with ample power to lead a congregation in vigorous singing, yet also has the delicate nuance to lead choirs or soloists or to shine in solo work. As the congregation at Zion has become accustomed to the new organ, they have responded enthusiastically, with congregational singing increasing noticeably in the months since the organ was installed. The organ is now fulfilling its role of leading the congregation in song.
It must be said that the successful outcome at Zion Lutheran is truly the result of a collaborative process involving a full range of participants. Pastor Kirk Clayton, with his great passion for liturgy and music, served as an advisor on the project along with members of the organ committee, including Lisa Segelhorst (committee chair and organist), Nancy Peterson (principal organist), Pinky Ahner (organist), David Abuya (choir member), and Karl Bretz (interested layman), with great support and advice provided to the committee by Norbert Krausz. The physical work done in Zion’s building was coordinated by the sanctuary remodeling and acoustics committee, consisting of Mark Krausz (chair), Alan Kneschke, Jennifer Lara, Josh Peterson (choir director), Andy Sax, and Donna Wiesen. Buzz Kandler served as a point of contact between the congregation and Parsons to make sure communication was clear and smooth.
The committees at Zion and the willing volunteers who put in countless hours of study, consideration, and physical labor joined their efforts with the skilled staff at Parsons Pipe Organ Builders, who devoted their skills wholeheartedly to the height of the organ building art to bring this project to fulfillment. All worked together as partners to create an exceptional pipe organ that has already shown itself to be a great blessing to the congregation’s worship life and is becoming a significant part of the arts and music community in Southern Illinois. And yet, despite the work of many people on the project, perhaps the words ascribed to J. S. Bach summarize the process best: Soli Deo Gloria.