Gene Bedient founded the Bedient Organ Company in 1969 and was the director until his retirement in 2010. Since retirement, he has traveled with his spouse, Gwen, who is an employee of the United States Department of State. They have lived in Algeria, Paris, Zimbabwe, Morocco, and currently, Brussels. He has carried out occasional tuning, service, and repair work on organs at these various locations. He spends his retirement time traveling, cooking, practicing the harpsichord, studying French, reading, and fixing things that are not in working order. When Gwen retires in 2021, they will be living in their California home in the Sacramento area.
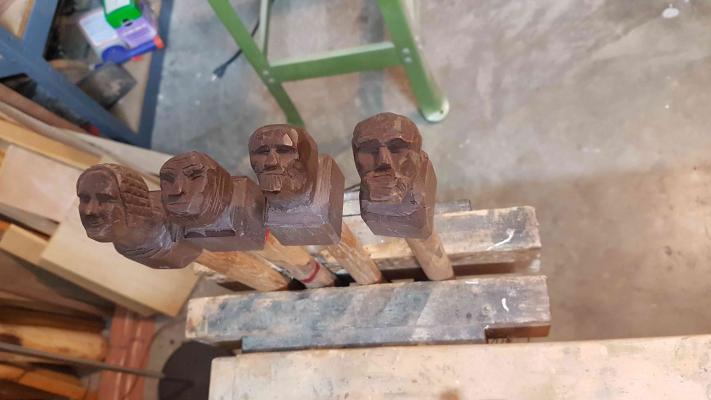
My foray into organbuilding was the result of a series of accidental discoveries and explorations. Entering the University of Nebraska, fall semester, 1962, I was an electrical engineering student, also taking a one-hour piano class lesson at the School of Music. Subsequently, I became a piano major with a minor in industrial arts.
During my sophomore year, I was introduced to the first pipe organ of my life—a 1960 Reuter organ at Holy Trinity Episcopal Church, Lincoln, Nebraska. Having always loved machines, technical things, and music, it captivated my imagination in ways I would not have imagined!
I subsequently explored organbuilding as much as I could by way of the university library music section, which had a rather extensive organ collection thanks to professor of organ, Myron Roberts. Concurrently, I learned about the American Guild of Organists and The Diapason magazine. I was able to study organ performance as my instrumental minor.
The next major event was attending the 1965 AGO Region VI convention in Boulder, Colorado. A three-stop, mechanical-action organ had been brought to the convention by Charles McManis, organbuilder from Kansas City. I learned that actual persons made these captivating instruments! Charles was encouraging and based on my described woodworking skills and seeing a couple of wooden pipes I made, months later he wrote a letter offering a job for the following summer.
Arriving in Kansas City, I worked in the shop for some weeks before we left on a trip to Florida, where we were to install a sizable instrument in Sarasota, at Church of the Redeemer. Enroute, we made an unforgettable stop at the 1966 AGO national convention in Atlanta. There, I heard both Virgil Fox and
E. Power Biggs give performances. Fox played on a Möller organ in a Baptist church, probably selected because the console was on a raised platform in the front, and the platform had the essential open spiral staircase to mount and descend! It was stiflingly hot and humid in the church. The sanctuary became hotter and even less pleasant when Fox asked the ushers to shut all of the windows mid-performance so we could “fully enjoy” the quietest sounds of the organ without distraction of outside street noise! At the end, those attending staggered out into the evening for breaths of fresh air!
Biggs played at Saint Anne’s Episcopal Church on a new Flentrop organ. He was well aged by then, and the program was not particularly engaging. For me, the excitement occurred when, right after the recital, a young John Weaver sat down to try the organ and played a dazzling Prelude and Fugue in A Minor, BWV 543, by Bach, from memory. As part of the trip, we visited the one-manual Tannenburg organ at the Single Brothers’ House in Winston-Salem, North Carolina.
The organ installation was informative and educational, and I did my best to be as useful as possible. At the end of the summer, back at the shop in Kansas City, and I was determined to build my Opus 1, and Charles good-naturedly gave me from his salvage inventory an Aeolian-Skinner 4′ Harmonic Flute and a tenor C 8′ Dulciana by Möller. The latter I cut in half and made into a 2′ quasi-Principal.
Armed with information from Die Kleine Orgel by Walter Supper, with assistance from an art department professor, and some #2 pine from the local lumber yard, I had already been engaged in making an 8′ Gedackt stop in the industrial arts shop at the university. Thus, Opus 1 had begun before I realized it had begun.
At the time I attended the regional convention in Boulder, I met Norman Lane of Meunier organ works in Denver and had a tour of their shop before returning to my western Nebraska home. The Meunier people had given me a keyboard from an old tracker organ. Thus, full of ideas, pipes, a keyboard, and a few completed Gedackt pipes, my Opus 1 began to take shape. It would have the disposition of 8′ Gedackt, 4′ Harmonic Flute, 2′ Principal (49 notes), one-manual.
I was very lucky to have many interested professors in various disciplines of the university, and I was able to do then what one probably could not do today—build an organ in a department of the university! As an industrial arts student, I was required to complete a project that would make use of the various disciplines that I had learned over the coursework of the program. For this project, I would receive one credit hour, and my project was to build a three-stop, mechanical-action pipe organ! I could not have accomplished this task without the support and encouragement of one professor in particular: Neil Munson, professor of industrial arts. As an old-world gentleman interested in all of the creative arts, he was not only fascinated that I would want to do this project, but was forever helpful.
As the project neared completion, I was in need of a wind supply. A small horizontal bellows with rubber cloth gussets had been constructed, but I needed a blower. I went to the local Sears, Roebuck and Company store downtown, bought a ½-horsepower motor, and made a blower! The impeller was contained in a plywood/sheet metal housing with the motor standing vertically on top. It produced plenty of wind and also the equivalent amount of noise of a 20-horsepower Spencer blower!
With the organ complete prior to the end of my fifth undergraduate year, Neil Munson wanted to have an organ recital in the industrial arts shop, which he arranged and invited professors and friends from across campus for my performance of Bach, Froberger, Sweelinck, etc. He was so excited to see this event accomplished; I think it was one of the high points of his career! There were many small visits to the organ and demonstrations that followed as curiosity got the better of people.
What to do with the completed instrument? I was fortunate that C. Richard Morris—organist, mentor, and dear friend, the person who had introduced me to the Reuter organ years previously—arranged for my Opus 1 to be used at the chapel of First Plymouth Church in Lincoln, preceding the arrival of a Schlicker organ. The instrument was eventually disassembled, moved several times, and on the occasion of leaving my 18th and “L” shop in Lincoln after eleven years occupancy, most of the organ was discarded. The only parts that remain are the four stopknobs. Enamored by the photo in The Organ in Church Design by Joseph Blanton of the nineteenth-century keydesk at the Jakobikirche, Hamburg, with its impressive carved head stopknobs, my Opus 1 had to have them! One for each of the three stops and one for wind. They are what remain of my Opus 1!
Photo: carved head stopknobs