Steve Riskind is an independent photographer based in Ridgewood, New Jersey. He is best known for his portraits of classical musicians. In recent years he has concentrated on artisans and fine artists at work—capturing the relationship between these skilled creators and their materials. As a long time lover of pipe organ music, photographing organbuilders has been a wonderful addition to this project. Riskind’s work combines the aesthetic of black and white film photography with his love for the capabilities of digital photography.
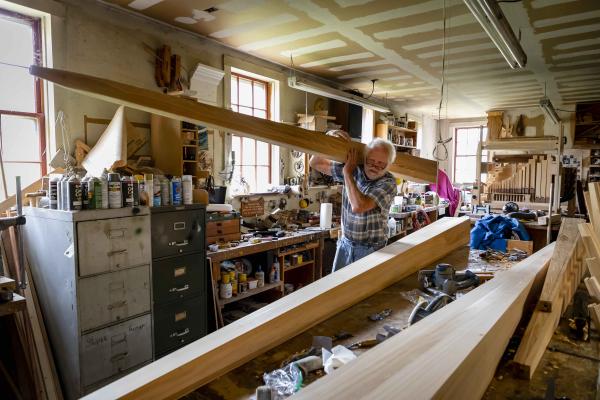
This photographic essay explores the work of two pipe organ builders. One is a business with over a dozen employees; the other is an owner/organbuilder who works with associates when large projects dictate additional help. One firm has embraced technology, electric action and stops, augmented with solid-state electronics; the other builds tracker-action instruments where, on smaller instruments, the blower motor is the only electrical part. Both have extremely well-equipped woodworking shops.
For the last eight years, I have been photographing small artisan businesses in northern New Jersey. After taking pictures at a specialty textile mill and a jewelry maker housed in a former silk mill, I was looking for another artisan business. The Diapason’s annual Resource Directory provided the lead I needed to continue the project. Peragallo Pipe Organ Company is located in Paterson, near the other firms in my project. I contacted the Peragallos, they were interested, and thus began my third photo essay of an artisan business.
Peragallo recently celebrated its one-hundredth anniversary. The company founder, John Peragallo, Sr., apprenticed with the Skinner Organ Company. The elder Peragallo’s experience with Skinner instruments gave the company a direction it follows to this day, though they freely make use of technologies that have come along since their founder’s time.
More recently, and again with the help of the staff of The Diapason, I reached out to a second builder, A. David Moore of North Pomfret, Vermont. David Moore builds and maintains pipe organs that are very different from those made by Peragallo.
A. David Moore’s career as an organbuilder began with the restoration of a circa-1850 George Stevens tracker instrument from the then-closed Woodstock (Vermont) Christian Church.1 After a three-year apprenticeship with C. B. Fisk, he started his own firm in 1973. He continues today to work out of a shop on his family farm in North Pomfret.
Over the years, I have learned much from The Diapason’s monthly feature in which an organbuilder discusses the process of creating a new or restored instrument. These articles deal with aesthetic, ecclesiastical, architectural, and a wide variety of human and financial issues. Peragallo Pipe Organ Company and A. David Moore, as successful organbuilders, deal with all of these. Underlying these kinds of meta-concerns, however, is a foundation of craftsmanship—how does the organbuilder create a physical instrument that will, for decades, meet the needs of a congregation?
These photographs show this craftsmanship as exhibited by two organbuilders. In the case of the Peragallo company, one sees their skill in designing and executing casework and consoles and their deep experience in digital and analog electronics. Peragallo’s heritage from Skinner is manifest in the wide range of tonal resources available in their instruments. A number of their organs employ a French tonal scheme and French-inspired curved terraced consoles.
A. David Moore, Inc., builds only tracker-action instruments. Moore and his associates cut lumber from trees, fabricate cases, consoles, and action, and they make wood and metal pipes for their instruments. (His largest instruments do include electric stop action alongside mechanical stop action, making it possible to have electronic combination action.) While Moore uses modern power woodworking tools, he describes his pipe organ aesthetic as mid-nineteenth century.
Different builders have different skill sets, but I would argue that, they all depend on skilled artisans. My photographs show the connection between these artisans and the materials with which they work—the foundation for creating a pipe organ.
Notes
1. See “Organ in a Pomfret hay barn!,” Vermont Life, 1965, Summer, Volume XIX, No. 4, p. 31, for an account of A. David Moore and a fellow high school student’s adventure restoring a nineteenth-century Stevens organ.
Photo:
A, David Moore carrying one of the 16′ Trombone pipes from wood shop to erecting room (photo credit: Steve Riskind). All photos may be viewed in the digital, PDF, or print editions.