Parsons Pipe Organ Builders, Canandaigua, New York, 100th Anniversary
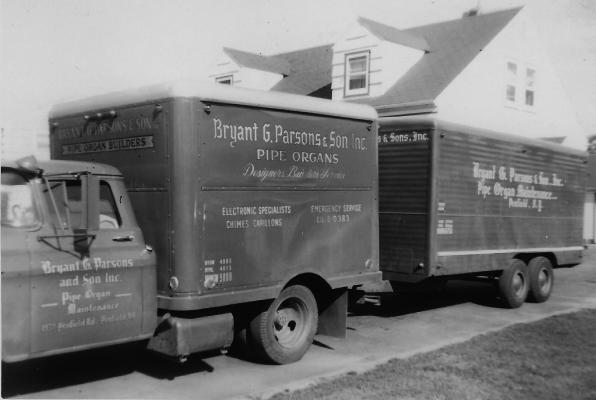
This year, Parsons Pipe Organ Builders celebrates the 100th anniversary of its founding and five generations of Parsons family members who have made pipe organs their vocation. Although the manufacturing workshop was established later, the family has been involved in the trade since the late nineteenth century.
Gideon Levi Parsons apprenticed as a flue voicer with noted organbuilder John Wesley Steere and later married Steere’s niece, May Estelle Steere. Gideon continued his voicing career with John’s son, Frank, and later with Ernest M. Skinner, who purchased the Steere firm in 1921. The couple had two sons, Bryant Gideon (b. 1896) and Richard Levi (b. 1905). Both of Gideon’s sons apprenticed with the Steere firm, but only Bryant continued in organbuilding. Following in his father’s footsteps as a voicer was not an option for Bryant as tradesmen commonly held their skills closely for job security. Bryant worked in every department—from stacking lumber, shoveling sawdust, holding keys, and even began setting up organs on his own. However, when he returned to the factory, he was known as “the kid.”
For a brief period prior to World War I, 16-year-old Bryant was hired by Professor Harry Jepson, head of the organ department at Yale University, to be curator of the renowned Newberry Memorial Organ, which he helped install. Originally built by the Hutchings-Votey firm in 1902, the organ was enlarged by J. W. Steere & Son in 1915. Bryant recalled that there was a secret button beneath the keys to activate the 32-foot reed so that only Professor Jepson could show the organ at its fullest.
Following time in the Navy during World War I, Bryant worked for the Bosch-Magneto Company in Springfield, Massachusetts, learning much about electricity (a concept quite new to organbuilding at the time). He then joined the Skinner firm, which by that time had purchased J. W. Steere & Son. Shortly afterward the factory burned, and Bryant moved with the firm to Westfield, where it took up shop in an old whip factory. Bryant was sent to Rochester, New York, to install the large organ at Kilbourn Hall at the Eastman School of Music along with the instrument in Professor Harold Gleason’s studio. While working in Rochester, Bryant met and married Ruth C. Blood, and they decided to settle there because he recognized the musical and cultural opportunities this community had to offer. Bryant’s Rochester career began with organbuilder Charles Topliff (himself a Steere alumnus), working with another Steere alumnus, Arthur Kohl. Bryant formed his own company in 1921 and continued to focus on service and restorations. To support his family during the Great Depression, Bryant sold vacuum cleaners door-to-door, among other things, while waiting for church work to revive.
While in Rochester, Bryant was curator of the four-manual, 129-rank Aeolian organ in George Eastman’s home—the largest residence organ ever built. Even those familiar with the founder of the Eastman Kodak Company are often unaware of Mr. Eastman’s fondness for organ music. His instrument had a Concertola Solo Music Roll Mechanism. Each Monday (even on Christmas Day), Bryant would arrive to check tuning and to set up the ten rolls for the week so that Mr. Eastman would be assured of music accompanying his breakfast. Each weekday, Mr. Gleason, who Mr. Eastman hired to head the organ department at the Eastman School of Music, would walk more than one mile down East Avenue from the school to play for Mr. Eastman’s breakfast promptly at 7:30 a.m. in the winter and 7:00 a.m. in the summer.
Bryant and Ruth had two children, Bryant Gideon, Jr., and Bina Ruth. Bryant, Jr., apprenticed with his father from an early age and later with the M. P. Möller Organ Company of Hagerstown, Maryland, installing many organs in the New York City area. Bryant returned to his father’s firm in Rochester following World War II where, in 1954, they incorporated as Bryant G. Parsons & Son, Inc. Bryant, Sr., retired in the early 1960s. The company grew and relocated to Penfield, New York, continuing with service and restoration work.
During the years in which father and son worked together in Western New York, Bryant, Jr.’s wife Esther Bills gave birth to five children. The two sons, Richard Bryant and Calvin Glenn, worked with their father from a very early age to learn the trade. Eventually, having been raised and trained as organbuilders, both sons were anxious to join the family firm in an official capacity and to establish their own credentials. Ric and Cal, as they prefer to be known, purchased the company from their father in 1979. In tandem with maintaining the company’s service responsibilities, the two set their sights on establishing a reputation for fine craftsmanship both through the restoration and rebuilding of existing organs and in the design and building of new organs bearing the Parsons name. Since that time, the company has completed a full portfolio of projects. As president and artistic director, Ric oversees the tonal and technical design departments. Ric has served on the board of the American Institute of Organbuilders in several capacities and as president of the Associated Pipe Organ Builders of America. As vice-president, Cal is responsible for managing the service department and for coordinating activities related to installations. In reality, Ric and Cal work as equal partners to ensure the company’s success.
Parsons’ reputation as a builder of fine liturgical pipe organs began to grow under Ric and Cal’s stewardship and with the addition of key staff members. Duane A. Prill, a gifted musician from Van Wert, Ohio, joined the firm in January 1991. Duane had just received a master’s degree in organ performance from the Eastman School of Music where he studied with Russell Saunders. Duane’s postgraduate studies at Eastman were under the direction of David Craighead. After joining Parsons, Duane worked with head voicer Gordon Dibble and quickly developed his own notable style of voicing and went on to become the company’s tonal director. Duane’s collaborative work with Manuel Rosales and Jonathan Ambrosino, combined with his ongoing commitment to study and visit organs throughout the United States and Europe, has helped raise the tonal designs of Parsons instruments to new heights. In addition, his service as principal organist at Asbury First United Methodist Church in Rochester has driven Parsons to build instruments that strive for high-quality execution of church repertoire.
Peter H. Geise, also a gifted musician, joined the firm in 2004. He received a master’s degree in organ performance from the Eastman School of Music where he studied with Hans Davidsson. After receiving his master’s, Peter embarked on a one-year training period at the Göteborg Organ Art Center in Sweden. Now Parsons’ technical design director, Peter is responsible for the design processes related to the mechanism and casework for each project. By necessity, Peter works in a hands-on fashion with Parsons construction and installation crews to ensure that what appears on the computer screen translates precisely to what is being built. In addition to his work at Parsons, Peter serves as the minister of music at Lima Presbyterian Church, Lima, New York, also home to Geise Opus 2, a two-manual, 25-rank electric-slider instrument built with church volunteers under Peter’s direction.
Ric’s two sons, Matthew and Timothy, have committed their efforts and skills to the company as well. Both Matt and Tim have accumulated years of experience and work closely with Ric and Cal to manage the company’s day-to-day operations. Matt currently serves as the dean of the Rochester chapter of the American Guild of Organists and vice president of the American Institute of Organbuilders. He is also responsible for the firm’s affiliation with the Eastman School of Music where Parsons serves as curator of organs. Tim has been heavily involved in Parsons’ recent entry into CNC technology, which has greatly enhanced the firm’s capabilities in terms of both process and production schedule. Tim is also involved in the firm’s manufacturing and installation processes and is responsible for the company’s graphics department.
Parsons Pipe Organ Builders strives to help clients find solutions that are tailored to their specific needs rather than limiting clients’ options to a particular style of building. Known for achieving superb results, Parsons maintains its own tonal goals. However, the company believes strongly in taking a collaborative approach with its clients to ensure that discussions cover a broad range of possibilities.
The Parsons project list is diverse with new organs of both tracker and electric actions, historic restorations, and even an unusual commission for an artist in Soho, New York City. Particularly challenging and interesting was Parsons’ participation in the research project for Cornell University, Ithaca, New York, working with the Göteborg Organ Art Center (GOArt), in Sweden. This two-manual, 40-rank, mechanical-action instrument is an historic copy based on the tonal design of the 1706 Arp Schnitger organ that was located in the Charlottenburg Castle Chapel in Berlin.
Parsons is currently under contract to build new organs for First Lutheran Church, Cedar Rapids, Iowa (three manuals, 52 ranks, mechanical action, Scott R. Riedel, consultant); St. James by-the-Sea Episcopal Church, La Jolla, California (four manuals, 79 ranks, electric-slider action, in collaboration with Manuel Rosales; Thomas Sheehan, consultant); and St. Benedict Catholic Cathedral, Evansville, Indiana (three manuals, 57 ranks, electric-slider action). Parsons was also recently chosen to complete the research, documentation, and restoration of the circa 1841 Jacob Hilbus organ for the Organ Historical Society (Bynum Petty, archivist and consultant; S. L. Huntington & Co., collaborating).
Much has transpired since the firm built the first two organs in the 1,400-square-foot workshop in Penfield, New York. In 1986, the firm relocated to the current workshop in Canandaigua, New York, which was expanded to 21,000 square feet in 2005. The introduction of 3D CAD arrived at the firm in 1986 when it was one of the first to provide computer generated images of a proposed organ design in the context of a client’s architectural setting. The year 2019 brought the addition of a CNC machine and with it a new level of efficiency and accuracy in construction.
Of course, the value of any business that relies on craftsmanship and personal commitment to achieve the highest quality work lies with every member of the Parsons organization. That number has grown over the years from four to eighteen, and we are grateful to acknowledge the work of Derek Bommelje, Joseph Borrelli, Brian Ebert, Aaron Feidner, Aaron Grabowski, Eric Kesler, David McCleary, Jay Slover, Chad Snyder, Dwight Symonds, Bernard Talty, and Travis Tones. Ric’s wife Ellen and Tim’s wife Kate currently manage the office. Ric often mentions that the company’s success has as much to do with divine intervention as it does with having a sound business plan! Parsons continues to be optimistic about its future contributions to the fine art of organbuilding for generations to come.
Photo: Bryant G. Parsons & Son, Inc. truck fleet, circa late 1950s
Cover photos:
2010 (top left): St. George’s Episcopal Church, Fredericksburg, VA, III/55 tracker
2020 (top center): First Lutheran Church, Cedar Rapids, IA, III/51 tracker
2005 (top right): St. Stephen’s Lutheran Church, Monona, WI, II/30 tracker (Rosales/Parsons)
1985 (left center): Westminster Presbyterian Church, Houston, TX, II/9 tracker
1989 (right center): Evangelical Lutheran Church of the Atonement, Rochester, NY, II/26 tracker
2019 (bottom left): Hope Lutheran Church, St. Louis, MO, II/27 electric slider
2015 (bottom right): United Church, Canandaigua, NY, III/40 electric slider