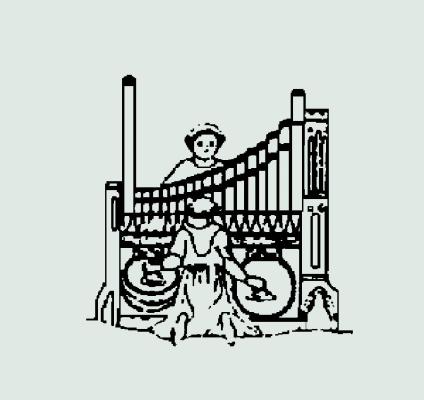
M. P. Rathke, Inc., Indianapolis, Indiana, Opus 8
Newtown United Methodist Church, Cincinnati, Ohio
From the director of music
II Corinthians 5:17 reminds us that “[t]he old becomes new again.” Organbuilder Michael Rathke’s Opus 8 at Newtown United Methodist Church (NUMC) in Cincinnati, Ohio, tangibly exemplifies just that. Rathke repurposed four ranks of century-old pipework— unanticipated gifts to NUMC from a neighboring church—juxtaposed them with a fresh principal chorus, Stopped Diapason, and Trumpet, and housed the result within a sleek, hand-crafted, solid walnut case to make the old new again.
In 2011, members and friends of NUMC began the process of selecting a new organ for their historic church. At first blush, artistic and practical considerations elicited from the modest membership of 106 people two responses: exhilaration and trepidation. Inspiration came from organbuilder Michael Rathke, organ consultants Thom Miles and Roberta Gary, and administrative council chair Larry White. White significantly reframed an increasingly nagging question, “How can we?” to an affirmative new mantra: “How can we not?” The decision to pursue the purchase of a pipe organ—a first in the church’s history—thus held stewardship on an equal footing with artistic goals. Larry White, Reverend Howard D. Preston, and Craig Correll (facilities manager and chair of the organ committee) led church members and friends in the purchase of an instrument that would prove an investment in the future of NUMC and a commitment to the values and history that had long been integral to the church.
All recognized the need for an eclectic instrument rooted in historical principles: sufficiently versatile to accompany solo, choral, and instrumental music; sufficiently rich to satisfy a wide range of liturgical requirements; and sufficiently responsive to evoke artistry in the performance of the organ repertoire. Paramount was an unwavering commitment to good stewardship and to honoring the architectural integrity of the worship space. Rathke Opus 8, a mechanical key- and stop-action organ modeled on centuries-old organ building practices, far exceeded our initial expectations. This instrument inspires us to become new again.
—Dr. Kristy Swift
Director of Music
From the organbuilder
Nothing lasts forever. This cheerless reality surely haunted the earliest artists and builders who, observing decay in the natural world, would have foreseen the eventual deterioration of even their most careful work. Yet they designed, labored, and built all the same. Perhaps they were encouraged that, although nothing endures indefinitely, some things do last for a very long time. And pipe organs happen to be among the longest-lived of all human creations; this is especially true of their component wood and metal pipes, whose life spans are often measured in centuries.
Newtown United Methodist Church is located in a historic village on the near southeast side of Cincinnati, Ohio. The 1867 building was apparently constructed without a pipe organ, nor does one seem to have been installed during its first century and a half. Then in 2012 came a confluence of several related factors: quality vintage pipework offered for essentially the price of retrieving it, the creative vision of music director Kristy Swift, and the strong support of Pastor Howard Preston.
The deteriorating state of Newtown’s aged electronic organ had given church leadership pause for thought. A generous and welcome bequest from a parishioner in years past, it had reached the end of its anticipated life span and was no longer able to be repaired. In response to Pastor Preston’s directive, the church formed a committee led by Kristy Swift, which in turn retained consultants Thom Miles and Roberta Gary. That a modest pipe organ would be the preferred solution soon emerged, but then there was the small matter of funding. Although the congregation was healthy and, in fact, led the local Conference in per-capita giving, it was far from being rich, and the decision to procure a new instrument of any sort would be approached thoughtfully and prayerfully.
Then this remarkable church, which had given so much to others, received a surprise gift of its own in the form of several ranks of excellent vintage pipework from a neighboring church. This tipped the scales, so to speak; the Newtown congregation was able to raise the balance of funds for a modest two-manual, seven-stop pipe organ, a contract for which was signed in 2012 with M. P. Rathke, Inc., of Indianapolis.
Once the project was approved and local interest grew, several donors stepped forward and asked if they might contribute toward making the organ larger and more flexible. Dr. Swift subsequently met with the organbuilder and consultants; together they settled on an enlarged ten-stop specification, including an independent 8′ Open Diapason in the Pedal, as well as a full-length German Trumpet of hammered lead.
Placement
Where the organ would be situated and how it would relate to the worship space were twin issues that first had to be resolved. It is axiomatic that pipe organs generally sound their best when placed high in a room and speaking down its long axis; yet here we had limited ceiling height (16′) and a space that was nearly as wide as it was long, offering no obvious long axis. The choir’s historic location in the acoustically advantageous right-hand front corner of the room—visible to the congregation yet by no means the center of attention—ended up being a critical consideration. We thus decided to place the instrument near the choir in a compact, freestanding walnut case, against a side wall near the front of the building, and centered between two windows—a solution that, happily, did not require appreciably more usable floor space than the previous electronic organ console.
Engineering
Once the organ’s placement and footprint had been established, we faced a familiar conundrum of fitting the proverbial ten pounds into a five-pound bag. In so doing, we were challenged to design a playing mechanism that was reliable, durable, and responsive; to ensure ready tuning and maintenance access; and to provide all pipework with sufficient speaking room. This last consideration was especially vexing because, unusually for a small instrument, fully five of its ten stops are at 8′ pitch; four of those five stops comprise full-length, open pipes.
The organ utilizes mechanical stop action and suspended mechanical key action, the latter playing through splayed tracker runs to keep the action simple and vertical space requirements to an absolute minimum. Manual I and Manual II share a common windchest with alternating divisional key channels in the chest grid, a space-saving expedient that has the knock-on effect of housing most manual pipework on the same level for optimal tuning stability. Two registers—the 4′ Open Flute and the 8′ Stopped Diapason—are tubed from the main windchest up to a so-called flying toeboard, much in the manner of a mounted Cornet. This configuration, while economizing on windchest depth, also lends a spatial aspect to Manual II, whose pipes are located higher in the case than Manual I and thus provide an interesting “stereo” effect when the two divisions are played in dialogue, and a special richness when coupled. But because the vertical distance is minimal (36 inches) there is essentially no negative effect on tuning stability or the two divisions’ tendency to hang together with regard to cohesion and blend.
All Pedal pipework is similarly tubed off from its own windchest, which sits immediately behind the pedalboard. This somewhat unusual arrangement was chosen for several reasons. First, had we placed the Pedal chest deeper into the instrument, beneath the pipework it controls—the most common solution, and appropriate to most situations—it would have simplified our design work considerably, but it would have introduced a potential maintenance nightmare: a bit of dirt on a pallet could necessitate a half-day’s disassembly. Now one needs only to remove the pedalboard for full access to the division’s pallet box. Being entirely tubed off, pipework may be placed for maximum space efficiency. An added bonus is further enjoyed by the largest bass pipes, which typically speak their best when fed via wind conveyances of reasonable length.
Tonal design
Here the roles of consultants Roberta Gary and Thom Miles cannot be overstated. In a small instrument, especially, every stop must be something of a chameleon, functioning effectively not only on its own but also in a variety of combinations. The late addition of the 8′ Trumpet to the organ’s specification in particular required some serious discussions among church staff, consultants, and organbuilder. How much space, already at a premium, would it add to case depth? What would its tonal character be? And from which division would it play?
The first question was the easiest, answered by conventional drafting and geometry and mitigated by careful chest layout. The second question received more spirited discussion, but a Trumpet of North German character (this one based on Tobias Brunner’s fine example at Tellingstedt) soon emerged as the unanimous choice, largely on account of its rich, dark, and blending sonority, which one listener colorfully described as “German chocolate.”
The third question—in which division would this German Trumpet live?—occupied somewhat more time than anticipated. The celebrated historic instruments of North Germany and Holland, important points of departure for the Newtown organ’s design, would almost always have placed the Trumpet in the primary manual division. Secondary manual divisions would either have had no reed, or else a lighter reed register, often half- or quarter-length.
It was Dr. Gary who first suggested departing from tradition and placing the Trumpet on Manual II for the following reasons: 1) it could be played in dialogue with the Manual I Principal chorus; 2) it could be accompanied by any number of 8′ + 8′ or 8′ + 4′ combinations on Manual I; and 3) it could be coupled directly to the Pedal, thus lending substance and independence to this two-stop division.
Final Thoughts
At this point, many organbuilders will conclude by writing about the fine sound and appearance of their instrument, the excellent quality of pipe construction and voicing, the sensitive and responsive action, and the like. And we certainly hope others will write similar things about our work for Newtown Methodist in due course. For now, we will refrain from saying much ourselves because, as builders, we can’t pretend anything close to objectivity. We think we’ve built a beautiful and estimable instrument; but in the end, our thoughts aren’t the really important ones. We are encouraged that feedback thus far has been positive, we are proud of the work we have done for this remarkable congregation, and we hope our efforts will stand the test of time and inspire the worship of generations to come. And we unhesitatingly invite interested readers to visit, see, play, listen, and decide for themselves.
Nothing in this world lasts forever. It is nonetheless our sincere hope that our Opus 8 will last for a very long time, indeed, and that it may speak to future generations of those things which are truly eternal. Ad majorem Dei gloriam.
—Michael Rathke
Builders of the organ
Ana Carlson
Christopher Church
Timothy McEwen
Michael Rathke
Paul Rathke +
Lindsey Redder
Luke Redder
Caleb Ringwald
Nicholas Ringwald
Christopher Sedlak
Specialist Artisans
Linda Cook: calligraphy for stop labels, coupler labels, and builder plate
Louise Pezzi: design and fabrication of wrought-iron drawknobs
Morgan Faulds Pike: design and carving of walnut pipe shades
MANUAL I
8′ Principal (façade to middle C, polished
25% tin; rest hammered 50%)
8′ Gemshorn* (ex Kimball 1–25, zinc &
50% tin; rest new, 50% tin)
4′ Octave (hammered 40% tin)
22⁄3′ Twelfth (hammered lead)
2′ Fifteenth (hammered lead)
MANUAL II
8′ Stopped Diapason (poplar)
4′ Open Flute* (1–18 poplar,
19–58 50% tin)
8′ Trumpet (hammered lead)
PEDAL
16′ Bourdon* (white pine)
8′ Open Diapason* (zinc & 30% tin)
*ex 1908 Kimball, wholly or in part
Couplers (toe, hitchdown)
I–P
II–P
II–I
Tremulant (general)
Pedalboard: flat and non-radiating
Temperament: Kellner, A-441 @ 72° F