John Bishop is executive director of the Organ Clearing House.
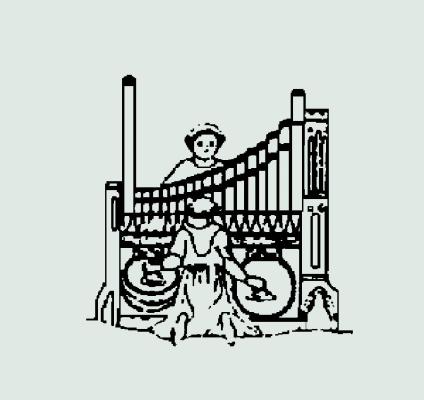
Special delivery
The Bath Iron Works (a General Dynamics Company) is about fifteen miles from where we live. Located on the shore of the Kennebec River in Bath, Maine, more than ten miles up from the ocean, they build Aegis and Zumwalt class destroyers for the United States Navy. The shipyard is unique because of its immense lifting capacity—you can see their mammoth cranes from miles in each direction. This allows them to mass-produce ships in large sections because they can lift as much as a third of a ship at once. In the company’s heyday during World War II, they launched a completed destroyer every twenty-two days. Think of the supply chain. That’s a lot of steel—tens of thousands of tons. That’s a lot of wire, windows, pipes, engines, tanks, valves, and gauges. It took about 275,000 person hours to build a ship. Twenty-two days—that’s 12,500 hours a day, or 1250 workers working ten-hour days. To stay efficient, each worker had to have the right tools and the right materials at the right time. Any organbuilder’s head would spin to think of such a management challenge. It’s hard enough to organize 200 person hours per week in a five-person workshop.
In the 1870s and 1880s, E. & G. G. Hook & Hastings was building new organs at the rate of something like one a week. We know that materials were delivered at night to that workshop in Boston by horse-drawn rail cars using the same tracks that the passenger trolleys used by day. Think of the mountains of American black walnut going into the maw of that place, all to be unloaded by hand. I suppose they had a night crew of men who did nothing but unload rail cars and make sure the materials were stored in the right place. And I suppose once the lumber was stored they loaded bales of sawdust to be carted off to line chicken coops.
While we think about the work involved in organizing a flow of materials into a nineteenth-century organ shop, what about the actual work of building the organs? When I started working in organ shops, we had screwdrivers that we turned by hand—analog screwdrivers. For a while we used electric screwdrivers that had wires hanging out of the handles—wires that could flop across the pipes of the Mixture while you were taking down a bottom board of an upper chest to repair a dead note. Now we have rechargeable cordless tools. And to top that, I have a battery charger that runs on the twelve-volt power in my car so I can recharge my power tools between service calls.
I’ve joked with the hypothetical question, “if Bach had a Swell box would he have used it?” I bet Mr. Skinner would have delighted in an eighteen-volt rechargeable DeWalt screw-gun. It’s even got an adjustable clutch to keep you from stripping the threads.
Supply and demand
We live at the end of a half-mile dirt road. I have a swell little workshop at the house where I tackle portions of our projects. I’m especially fond of working on organ consoles and I have a beauty in the shop right now, built by Casavant in 1916. We are renovating the organ for a church in Manhattan and I’m spending the summer plugging away at the console. Our house is at the end of the UPS route. A couple times a week at around 5:30 in the afternoon, the big brown truck hurtles down the driveway and careens into the dooryard. Nuthatches, chickadees, mourning doves, and goldfinches scatter in terror, groundhogs and chipmunks dash into the stone walls—only the sassy and pugnacious little red squirrels seem ready for the challenge.
With diesel engine roaring and spewing, the driver (there are two regulars) turns the truck around so it’s heading home before he’ll even look at me. He tosses a couple boxes at me and blasts off in a cloud of fumes, dust, and pebbles. (If he had to take care of a long dirt road the way I do he’d never drive like that—each time he comes to the house, five shovels of my gravel goes into the woods.) Measuring sound in decibels-per-hour, the UPS guy makes more noise in two-and-a-half minutes than I do in a week.
Leaning to the left
I suppose that if we were at the beginning of the route, the UPS driver would have a little more time to chat, but I remember reading an article that allowed a glimpse into the company’s efficiency. As traffic increases on America’s roads, we are all aware that you can wait a long time for a chance to make a left-hand turn on a busy road. Years ago I fell into the habit of planning errands to avoid left-hand turns. If I go to the hardware store first, grocery store second, bank third, the only left turn is when I leave the grocery store. I got teased about that some, but on December 9, 2007 the New York Times published an article that I believe excused my apparent eccentricity. Titled “Left-Hand-Turn Elimination,” the story told that that UPS has a “package flow” software program that maps out routes for the drivers limiting the number of left-hand turns as much as is practical. UPS operates 95,000 big brown trucks. By limiting left-hand turns they were able to reduce their routes by 28,500,000 miles, save 3,000,000 gallons of fuel, and reduce carbon dioxide emissions by 31,000 thousand metric tons. (Now you know what kind of mileage a UPS truck gets.) You can read the story at <A HREF="http://www.ny times.com/2007/12/09/magazine/09left-handturn.html">www.ny times.com/2007/12/09/magazine/09left-handturn.html</A>. Makes my five shovels of gravel seem a little less important!
After the big brown truck barrels up the driveway and turns right onto the road, I go back into the shop and open the boxes. What goodies I find: silver wire for key-contacts, woven felt for keyboard bushings, snazzy little control panels for solid-state relays and combination actions, specialty wood finishes from a one-of-a-kind supplier, useful tools that you can’t find at Home Depot. It’s like a little birthday party at the end of the day.
I need a huge variety of parts and materials to complete a project like this, and I spend a lot of time on the phone, leafing through catalogues (the big industrial-supply catalogues have more than 3,500 pages) and searching online. I rely on Internet access, next-day delivery, and specialty supply houses. And I can buy just about anything. Let’s say I need some red woven felt (bushing cloth) to replace the bushings in a mechanical part. I can use an X-Acto knife to get the old cloth out of the hole, but it’s really hard to measure the thickness of a piece of felt that was made ninety years ago. So what thickness should I get? Easy. If I search carefully online I can find it in thicknesses graduated by 64ths of an inch. I order a few square feet of four different thicknesses and experiment.
Close enough?
We talk about the importance of duplicating original materials when restoring an instrument. “If Mr. Skinner used 9/64″ red bushing cloth, I’m going to use 9/64″ red bushing cloth.” But I bet Mr. Skinner wasn’t choosing between eight different thicknesses listed on a catalogue page. I think he bought the stuff that was available and made it work.
The expression shutters of this Casavant organ we’re working on turn in bearings of woven felt. There’s a quarter-inch steel pin in each end of each shutter that serves as an axle. The pins turn in holes in wood blocks—those holes are bushed with green woven felt. After seventy years of regular use and twenty years of neglect, that felt is hard and worn. Over the years, organ technicians fixed squeaks and squeals in those shutters by glopping grease, oil, candle wax, mutton tallow, and more recently silicone and WD-40 from spray cans on those bearings.
I could buy Teflon tubing of quarter-inch interior diameter (1/4″ ID) from McMaster-Carr, an industrial supply company in New Jersey. I found it on page 91 of their 3,528-page catalog. It costs $1.28 a foot and comes in five-foot lengths. I could cut it into half-inch lengths (less than five-and-a-half cents each), and drill them into the shade frames to make perfect bearings for the quarter-inch steel axles. I bet it would be a long time before they squeal or squeak. It’s not historic, it’s not good restoration practice, but I bet those shutters would work beautifully for decades. I think I’ll go ahead and make that change. I’m confident that the organists who will play on this organ will never know we did, and I trust that Claver and Samuel Casavant will forgive me. My intentions are good and my conscience is clear.
An expressive conundrum
We have some tree work going on in our yard and one of the crew is a skillful equipment operator. He’s using a light-duty excavator that’s known as a backhoe because the bucket (or shovel) comes back toward the operator as it digs. The machine’s boom has three joints, roughly analogous to the human shoulder, elbow, and wrist, and the bucket compares to the hand, as it can curl under to scoop the earth. Each of the joints is operated by a hydraulic piston—that ingenious machine that uses the pressure of oil to extend or contract. It seems counterintuitive, but the engine of this machine drives no gears at all—its sole purpose is to drive a pump that creates the oil pressure. Even the wheels that drive the tracks are turned by hydraulics. The machine’s controls are valves operated by handles—those valves conduct the pressurized oil to the appropriate pistons.
The operator, a young guy named Todd who’s anticipating the birth of his second child as he digs in our yard, has his feet on the pedals that drive the machine forward and back. He has each hand on a four-function joystick. Each push of a control operates only one function, but Todd moves his hands and wrists in quiet little circles combining the machine’s basic movements into circular, almost human motions. His understanding of his controls is intuitive. He doesn’t have to stop to think, let me see . . . if I pull this handle this way, the bucket will curl under . . . He effortlessly combines the motions to extend the boom and the bucket, sets the teeth in the dirt, and brings the boom toward him as the bucket curls under filling with dirt. He whirls around to empty the bucket on a pile, and as he turns back to the hole, the boom and bucket are extending to be ready for the next scoop, which starts without a pause, a jerk, or a wiggle. He’s operating six or seven functions simultaneously. The power that operates the machine and the nature of the motion are both fluid.
I’ve read that some revered orchestral conductors eschew the pipe organ as an inexpressive instrument because it’s not possible for an organist to alter the volume of a single organ pipe. You press a key, the pipe plays. You pull a handle in a backhoe and the bucket moves in one direction. I can hear my colleague organists gasp as I compare Todd’s backhoe with an elegant musical instrument, but isn’t there a similarity between the two machines? After all, we don’t hesitate to call the pipe organ the most mechanical of musical instruments. And when we press that key, we’re opening a valve to let pressure through to do work. (I have to admit I’m glad we’re not messing around with hydraulic oil near a chancel carpet.)
The organist intuitively manipulates the controls—playing keys, changing stops, pushing pistons, operating expression pedals—and the result is fluid crescendos, accents, beguiling delays, great oceans of sound billowing through the air. Literally, organ music is the result of thousands of switches or levers moving at the will of the organist. That organist has practiced for thousands of hours, mastering the limitations of his or her body, teaching the body to perform countless little motions with ease and grace so the music flows free, denying both the physicality of the player and that of the instrument. Because the machine and player are both well-tempered, the music is infinitely expressive.
And of course we separate the organ from the backhoe. It’s nice to be able to move a ton of dirt in a few minutes without breaking a sweat, and we admire the skill of the guy who can make that machine come alive. But I couldn’t help notice that one of the joints on Todd’s machine has an important squeak to it, enough that when I was back in my workshop or office and couldn’t see the machine, I knew when he was extending or retracting the boom. Not my swell shutters!
A pipe organ is magic when all the squeaks and squeals are gone, when each function of the machine responds effortlessly to the intuitive motions of the player. In the workshop we make thousands of little choices about what material to use, how to adjust it, how to glue it down, so the machine will not stand in the way of the music. In the practice room we hone our skills so no knuckle cracks, no muscle binds, no fingernail hangs, and nothing about our bodies will stand in the way of the music. We dress in clothes that allow us to move freely, and we make sure our shoes are less than two notes wide. Our bodies and our instruments are conduits between the composer’s ideals and the ears of the audience.
Thanks to the UPS guy for bringing all those goodies, and yes—I’m certain that Bach would have used the expression pedal, but only if the shutters didn’t squeak.