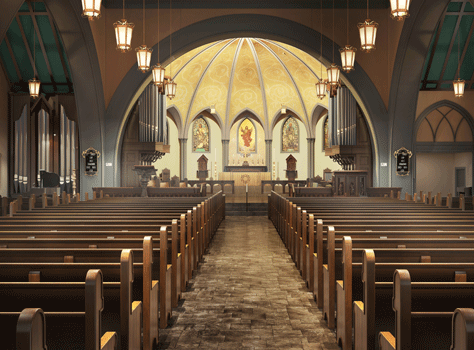
Goulding & Wood hosts an open house January 3, from 3 to 8 p.m., featuring their Opus 52 for St. John's Episcopal Church, Knoxville, Tennessee.
The new organ comprises 70 ranks across three manuals and pedal.
The open house takes place at their shop, 823 Massachusetts Avenue, in Indianapolis, Indiana.
For information: 317/637-5222; https://www.gouldingandwood.com/
See their new company video at: https://www.gouldingandwood.com/company.html