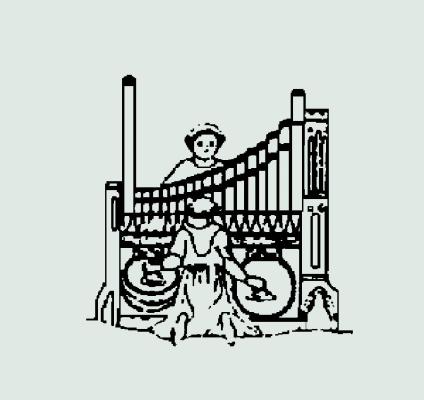
Lewtak Pipe Organ Builders, Inc., Camillus, New York
First Presbyterian Church,
Greenville, North Carolina
A note from the organist/choirmaster
When I arrived at FPC Greenville in 1998, the 1971 two-manual W. Zimmer and Sons organ of about 20 ranks stood in the rear gallery. A gift of the Guy V. Smith, Max R. Joyner, and James Gibson families, it had served the congregation, community, and East Carolina University music department well for almost 40 years. When it was determined that the congregation and music program needed a larger instrument with placement in the chancel, we began exploring moving and expanding the organ.
The Zimmer’s copper façade pipes of the 8′ Pedal Principal were spread across the rear wall, directly behind the choir, in the shallow but wide gallery. With the Rückpositif division directly behind the organ bench and cantilevered over the balcony wall, the choir singers were literally in the middle of the organ pipes. The organ was of German neo-Baroque style, with no Swell or other enclosed division. It did have some nice pipework, a strong principal chorus, and a relatively independent pedal division for an organ of this size.
Originally the plan was to move the organ to the front chancel area with a few additions. The project evolved, and due to the generous gift from the estate of Mary Potts Goodman Sorenson, it was to become essentially a new organ—utilizing most of the pipes from the original instrument, along with new ranks, to make it over twice the original size.
We wanted the following qualities in a new instrument: well-rounded sound that would support and enhance congregational singing; an organ that would speak evenly through the worship space, filling but not overwhelming it; one that would play repertoire of all periods and be a worthy recital instrument. We also wanted to build upon the German nature of the original. I had wished for full-length 16′ pedal ranks, string ranks, a Swell division with reeds and mixtures, colorful mutations, and additional flutes and 8′ ranks—a lot to ask on a limited budget.
Upon the first visit of Tom Lewtak, his enthusiasm and vision of the possibilities for the space were inspiring to everyone. There were no problems or limitations that were not dealt with in a positive way and solved. When we got the first drawings, everyone was impressed by the boldness and artistry of the design, which was dramatic, yet still looked like it belonged in the space. It complements the contemporary design of the church building and its best feature, the beautiful stained glass windows.
Before renovations, which started in 2009, the focal point of the sanctuary was the prominent high pulpit with a large overhanging tester, which fanned out toward the congregation. Looking further and behind this, one would see the empty space behind the pulpit forming a kind of alcove, which rose to over 40 feet. What was this space designed for if not for organ pipes? So it is now filled with a beautiful arrangement of pipes, casework, and tower façades.
First Presbyterian Greenville is located on the edge of the campus of East Carolina University and enjoys a close relationship with the ECU music department. The Zimmer organ, at one time the premier instrument in Greenville, had been used as a teaching and practice tool for students. Many recitals, organ and other, have been held in our space. The church has been host to many AGO meetings and events.
Even when the organ was a little over half done and heard at the Eastern Carolina AGO chapter meeting last fall, participants were overwhelmingly positive about the sound, observing its sweetness of tone as well as power. This is even more the case now, and we are fortunate to have an instrument with character and color, warmth in the ensembles and choruses, with brilliance as well as depth.
William M. Wood, organist/choirmaster, is originally from Graham, North Carolina. He did undergraduate work at the University of North Carolina, Chapel Hill, and Elon University, and holds the Master of Sacred Music in organ from East Carolina University. His organ teachers have included Robert B. King, William J.N. Stokes, and Janette Fishell. A frequent recitalist, he has served churches in Richmond, Virginia, and in North Carolina.
From the organbuilder
Building a straight tracker organ in a space that requires 30-foot-long tracker runs is always a challenge. I feel very strongly that mechanical action is superior, so I had no doubts that this is what was needed at First Presbyterian Church in Greenville, North Carolina—that is, if the church wanted to remain a leading center for cultural events in town. The acoustics of the sanctuary are more like those found in concert halls than in churches. There is sufficient reverberation to fill the room with lively sound, and the bass response is excellent, thanks to brick walls all around. The conditions for a new instrument were very favorable; this allowed us to design an instrument that, despite having just two manuals, has a comprehensive specification throughout, giving the organist a wealth of possibilities.
The tonal design called for a mid-German-style organ, with full principal chorus in the Great and rich complement of flutes in the Swell, along with strings and a well-developed reed section throughout the instrument. Both manuals are based on 16′ stops—Bourdon 16′ in the Great, and Fagott 16′ in the Swell—which provides the necessary gravitas of sound. The Great offers Principals 8′, 4′, 22⁄3′, 2′, and Mixture. This, along with a warm Trumpet 8′ and a bright Clarion 4′,
guarantees a strong plenum. There are also two flutes in the Great, to enable soft registrations and good blend for accompaniments. Lastly, there is a lively Cornet III, which serves as a versatile transition stop, good for both solo as well as plenum, with or without the Mixture.
The Swell has a substantial selection of colorful ranks. At the 8′ level we have included a wide-scale Hohlflöte, Quintadena, and Gambe, along with complementing Celeste. The Prestant 4′ has a slightly stringy quality to it, and the metal Gedackt 4′ perfectly complements the 8′ flute. Going up, we added a 2′ Piccolo and 11⁄3′ Larigot—this gives lightness and a “sparkle” to this division. The Mixture III–IV in the Swell is a bit unusual in that it includes a Tierce. The Tierce is voiced very mildly, not to be too present, and yet changes the character of the Mixture toward the “wider” sound, rather than the typical high-pitched shrill. This allows the Mixture to be used more frequently even in smaller ensembles with no danger of overpowering the singers. The Swell offers a generous choice of reeds as well; aside from the already mentioned Fagott 16′, we have included Oboe 8′ and Rohrschalmei 4′.
The Pedal division features a Posaune 16′ with full-length metal resonators, which along with a metal Principal 16′ makes for a solid bass foundation, even at the loudest dynamic level. The Pedal is independent enough to support the manuals without coupling, but of course we installed traditional couplers I–P and II–P for additional flexibility.
Since flexibility was one of the main goals in the design of this organ, it is worth mentioning the inclusion of an additional II–I Sub coupler. It is a fully mechanical coupler and yes, it does make you work a bit harder than normal, but it is worth it. The usefulness of this coupler is unquestionable, both for solo combinations as well as full-organ playing. Just consider this—when you sub-couple the 16′ Fagott to the Great, you end up playing a 32′ pitch on the main manual!
One peculiarity of this organ is the fact that the Quintadena 8′ of the Swell division happens to be placed entirely outside of the expression box. This is because we inherited the façade pipes from the old Zimmer organ, and among them was this Quintadena, which had 20 of the lowest pipes in the façade. We did not want to have 20 pipes out in the open and the remaining 36 under expression, so the logical solution was to offset the top of this rank completely outside the Swell. It seems to be working quite well, giving the Quintadena a distinct solo capability.
The design of the façade went through several stages. We first submitted three different proposals from which one was chosen and then modified to fit the space, the needs, and the taste of the congregation. The cabinetry is made from solid cherry, real mahogany, sapele, and wenge (the last two species are native to African tropical forests). Milder wood tones were needed to complement the church interior, and yet we did not want to make a completely dark façade, as the light in the building is rather subdued. The façade consists of eight towers—five in the lower tier and three in the upper—with rather daring angles and lines. As one can see on the drawing, the windchests and all playing components sit on the loft, twelve feet above the floor level, but the console is placed on the main floor. In designing the façade, we strove to make the organ look as “one”, with no detectable division between the upstairs and the downstairs. The towers are visually supported by the console cabinet, making the design very cohesive. In reality, the presence of the “loft” is hardly noticeable. The highest tower peak is 41.5 feet (12.6 meters) above the floor of the sanctuary, and the façade is 17.4 feet (5.3 meters) wide. Needless to say, the rigging was difficult and risky. We were able to use 90% of the Zimmer façade pipes: 29 made from copper and 27 made out of tin. All pipes were totally renovated so that they would look like new.
The console boasts our trademark features: drawknobs turned in Norway from real mahogany wood and then inlayed with Baltic amber stones set in sterling silver. The jewelry work was hand-crafted in Poland. The keyboards were produced in Germany, with key coverings provided by us. The naturals are covered with Madagascar rosewood called Bois de Rose, the sharps covered with bone. Bois de Rose was also used throughout the keydesk, key cheeks, and the music stand for inlays. All thumb pistons that control the electronics were capped with this wood as well. Stop nameplates are made of sugar maple and laser-engraved. The music rack is made of solid wenge wood and has all lighting fixtures concealed within it. It is easily detachable, to provide access to action regulation right behind it.
The key action is purely mechanical, with suspended action. It only has two square rails per manual to change the direction of the tracker run. One of the square rails for each manual is free-floating, providing the necessary self-adjustment of the action for climatic changes. The trackers are made from bass wood (linden tree) and all tracker parts (squares, arms, etc.) are made of hornbeam. Because of the significant distance between the windchests and the keyboards, we opted for a “double pallet” construction—imagine a normal pallet being sliced horizontally into two parts; the lower part opens first (breaking very minimal pluck force) and then the upper part falls down, letting a sufficient amount of wind into the tone channel. It is a simple and bulletproof solution for long tracker runs, allowing the key action to be light and crisp even with many stops drawn.
For the stop action, we utilized a German-made solid-state system with 3,999 levels of memory. Stops are controlled by drawknobs connected through this electronic system to slider solenoids opening and closing the stops. The console layout is European in its character, with only a minimal amount of buttons and gadgets. There is a clear numeric indicator for the swell shutters and for the crescendo. The thumb pistons are placed above the second manual, not under or between the keyboards. An average American organist will find it very user friendly, although different from our typical AGO standard. We also included one special feature for the drawknobs—the nameplates become gently illuminated from the back when the stops are turned on. It makes one’s eyes immediately aware of which stop is on and which is off.
Voicing—always the most important part of any organ—took a good half-year to complete. All pipes from the old Zimmer organ were treated as virgin pipework and revoiced from scratch, just like new pipes. The neo-Baroque flavor was removed in favor of a more rounded but full-bodied sound. There is no hint of shrillness and yet the sound is vibrant and bright. The instrument has plenty of power to impress the listener, with the might so typical for the King of Instruments; however, it is not senseless noise, which annoys our ears so often these days. For those who really want to experience the sound of this instrument, I cannot offer words of description. You need to come to Greenville and listen. The dedication of this organ will take place this month, on March 27, presented by Christopher Marks, assistant professor of organ at the University of Nebraska-Lincoln.
I wish to offer my heartfelt thanks to the people and staff of First Presbyterian Church of Greenville, North Carolina. Their incredible kindness, patience, and enthusiasm made this project the most gratifying experience one can ask for. This project would not have been possible without the support of Dr. William Neely, pastor.
Tomasz Lewtak was educated as an organist, having two master’s degrees in organ performance. His inspiration to become an organbuilder came at the age of 16, when he viewed the building process of the monumental organ at St. Mary’s Cathedral in Gdansk (Danzig), Poland, by the German firm of Hillebrand. Later, he studied organbuilding and design during his five years at the Academy of Music in Katowice, Poland. The following years took him to Denmark and Norway, where he apprenticed with Carsten Lund Organ Builders of Copenhagen. He acquired his voicing skills from Mogens Pedersen, chief voicer of Frobenius Organ Builders. Tomasz Lewtak is responsible for tonal design, pipe scaling, voicing, windchest and action design.
The following people worked on this project: Tomasz Lewtak, Pawel Lewtak, Craig Regan, Elliott Regan, Peter Clouser, Vanessa McCrea, Tony Pernisi, Michael McCrea, Kevin Reedy, and Joe Stillwell. Special thanks to Dick Marks for his volunteer service.
Photo credit: Tomasz Lewtak, unless indicated otherwise.
For more information about Lewtak Pipe Organ Builders: <A HREF="http://www.lewtak.com">www.lewtak.com</A>.
First Presbyterian Church
Greenville, North Carolina
2 manuals, 30 stops, 40 ranks
GREAT
16′ Bourdon
8′ Principal
8′ Rohrflöte
4′ Octave
4′ Spillflöte
22⁄3′ Quinte
2′ Principal
Cornet III
Mixture IV–V
8′ Trumpet
4′ Clarion
SWELL (under expression)
8′ Quintadena (outside of Swell)
8′ Hohlflöte
8′ Gambe
8′ Celeste
4′ Prestant
4′ Gedackt
2′ Blockflöte
11⁄3′ Larigot
Mixture III–IV
16′ Fagott
8′ Oboe
4′ Rohrschalmei
Tremolo
PEDAL
16′ Principal
16′ Subbass
8′ Octavbass
8′ Bassflöte
4′ Choralbass
Rauschquinte II
16′ Posaune
Couplers
II–I
II SUB–I
I–P
II–P
Manual keyboard compass: C–g′′′ (56 keys), naturals in black, sharps in white.
Pedal keyboard compass: C–g′ (32 keys), parallel keys, slightly concave.
Wind pressure: 90 mm water column for manuals, 99 mm for the pedal.
Mechanical key action (suspended), self-compensating for seasonal changes.
Electric stop action with 3,999 levels of electronic memory.