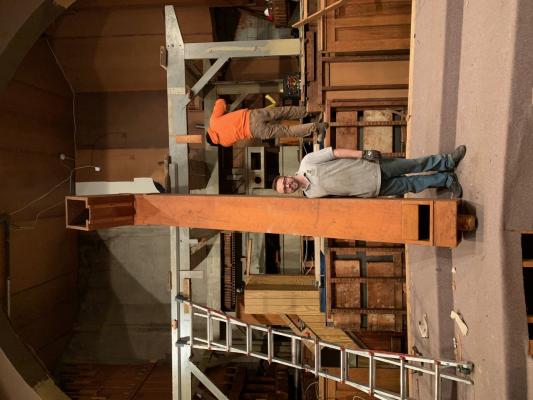
Music as community . . .
When I was offered the opportunity of joining the Organ Clearing House during the summer of 2000, I faced a critical choice. In addition to working independently as an organbuilder and technician, renovating and maintaining a gaggle of organs in the Boston area, I was also director of music at a large suburban Congregational church. I knew that the Organ Clearing House would sweep me into a busy travel schedule, and that I would have to make a choice.
That was a difficult decision on many levels. I had developed many friendships over my nearly twenty-year tenure at the church. For the first sixteen years, it was a privilege to work with the senior pastor, a kind and wise man and fellow sailor who preached beautifully and supported the music program vigorously. The privilege diminished after his retirement with a string of short-term successors who ranged from silly to terrible, but I valued my relationship with the choir enormously. We were fortunate to have a superb professional quartet joining the twenty or so volunteers, and we had a blast preparing and presenting all sorts of music from simple unaccompanied hymns to great oratorios with orchestra.
Each Thursday night, we opened our home after rehearsal, and at least half, sometimes all of the choir would show up. BYOB was the order of the day (though we made sure to have extra on hand, just in case), and we would order pizza or some appropriate substitute and spend a couple hours discussing the music we had worked on that evening, projects that various members were involved in outside the church, and simply nourishing our friendships. I have no doubt that the camaraderie of those many evenings enhanced our music-making by building special levels of trust and respect among that cheerful group of musicians.
Almost twenty years have passed since I faced and made the decision to leave all that and join the Organ Clearing House. I do not regret the choice, but I miss the fun and richness of working with that choir. Of all the aspects of playing the organ for worship, I miss most the pageantry of processional and recessional hymns—the movement of the sound of the choir through the building, the relationship between the choir and congregation, the ebb and flow of the poetry, and the wonderful feeling of producing all that acoustic sound to surround, lead, encourage, and inspire the congregation. As the choir mounted the chancel steps and split into the rows of center-facing choir stalls, I loved having eye contact with them as I played and they sang. Sometimes an exchanged wink would remind us of a joke, sometimes we simply reveled in the joy of it.
The living organ
Charles Brenton Fisk (1925–1983) was an innovative and inquisitive organbuilder and founder of the venerable firm C. B. Fisk, Inc. Charlie was revered by his coworkers for his Socratic teaching, inspiring creative thought by posing questions. He famously said, “The organ is a machine, whose machine-made sounds will always be without interest unless they can appear to be coming from a living organism. The organ has to appear to be alive.” I have often written that it is the challenge, even the responsibility of the organbuilder to remove the mechanics from the equation. Practically, it is impossible. Every organ has some elusive click, buzz, or hiss. But careful attention to fabricating techniques and quality control, especially being sure that moving parts are identical in form and function can tame the wild beast within.
Some organs, especially undistinguished organs with electro-pneumatic action, can seem like industrial products with lifeless tone, but when I am working inside an instrument, there is a big difference in the sensations I feel whether the blower is running or not. When the blower is not running, the organ is static and lifeless. When the blower is turned on, I hear and feel the air surging through the windlines, filling the reservoirs and pressurizing windchests. There may be a few creaks and groans as wind vessels fill. The organ gains breath and comes alive.
Organs that are conceived, intended, and built to seem alive are those that can become part of a community of music making in a church. They join the choir in air-driven acoustic musical leadership, that unique type of tone that carries and blends so well.
At one with the machine
In his book, Violin Dreams (Houghton Mifflin, 2006), Arnold Steinhardt, the now retired first violinist of the Guarneri String Quartet, wrote sensually about his relationship with his violin: “When I hold the violin, my left arm stretches lovingly around its neck, my right hand draws the bow across the strings like a caress, and the violin itself is tucked under my chin, a place halfway between my brain and my beating heart.” (page 5)
I have shared this quote in these pages several times over the years. When I first read it, I was touched by his eloquence about the intimacy of his relationship with his instrument, and I wondered further, what about the clarinetist or bassoonist who puts the business end of his instrument in his mouth. It does not get much more personal than that.
Compare that to the organist sitting on the bench at one end of a large room. She draws a simple stop, perhaps the most beautiful Diapason voice on the instrument, and plays a single note. If the organ has tracker action, the motion of her finger has moved a few levers to open a valve, releasing stored pressurized air to move into the pipe and produce tone.
If it is an electro-pneumatic organ, her finger has closed an electric contact (switch) sending current through a wire to an electro-magnet. The energized magnet moves a metal armature (valve), which opens one end of a pressurized channel to the atmosphere. The other end of that channel is closed by a leather pouch with a valve glued to it. When the pressure is released from the channel, the pouch collapses, pulling open the valve. It takes a lot more words to describe simply the motions of an electro-pneumatic action, and if it is a large instrument, there can be many more steps between key and valve including intermediate relays and switching. But in a well-built and well-regulated action, it all happens instantaneously.
That one motion of the organist’s finger sends a single tone across the vast space. It is similar to flipping a switch to turn on a light. But the lively thrill of playing the organ comes in the clever and seamless operation of the machine. Touch a button with your thumb and that single note releases a roar. Hold the note and flex your ankle, and the note gets softer. And to think you have done all this with a single note. Multiply those gestures exponentially, and you create a musical whole with an expressive range greater than that of a symphony orchestra, deftly skipping from one family of instruments to another, combining them, giving them solos, filling the room with complex tones.
Mr. Steinhardt is one of our greatest violinists. He can produce magic from that pound of spruce, producing a kaleidoscope of colors. He can shift from stentorian majesty to nimble coloratura. But Steinhardt’s kaleidoscope is miniscule when compared to the organist shifting from a mighty chorus of Tubas to a distant Aeoline. And the organist’s ability to superimpose a variety of tone colors simultaneously is unique in the world of music. The contrast between a Diapason and a Trumpet is the perfect example. The two voices may have the same volume level, but they are significantly different in harmonic structure. They can be compared one after the other, they can be contrasted, each being given an independent line of music, or they can be combined and played together. And that is just two stops. Multiply that by dozens or even hundreds, and the organist has a seemingly limitless variety of tone available at the touch of a finger. Or thousands of touches of fingers.
And that is where the seamless machine comes in. Recently, a colleague mentioned that he was using a sequence of forty-five pistons for a single decrescendo. What does that statement mean to a knowledgeable organist? First, it must be a huge organ to have that many pistons and enough stops to make that many meaningful changes in a single passage. Second, the organist is seeking a very grand, sweeping effect. Third, the organist is putting in a lot of work to prepare. Does it take an hour, two hours, or more of practice time to create such a sequence? Did he need to have a friend present to share in the listening as he made decisions? And we can assume (or hope) that this monumental organ is in a huge acoustic space. And that is one of the singular aspects of playing the organ—creating vast tonal structures in vast acoustic spaces. (I was right on all counts. It was David Briggs working on registrations for his new transcription of Bruckner’s Seventh Symphony at the Cathedral of Saint John the Divine in New York City on February 26.)
§
A violin typically weighs less than a pound—400 grams is usual. The luthier labors for months with a half dozen pieces of wood, each of which weighs a few ounces. We weigh pipe organs by the ton, and the process of building an organ involves thousands of hours of managing hundreds of components, some of which weigh as much as a ton. You see that big tower crown with moldings and carvings, sitting on top of a forty-foot organ case? And how did it get there? That’s right. People put it there. Notice how it is just a foot or two from the ceiling arch? And what does that mean? Right. There could be no hoisting point above it. People put it there without mechanical assistance.
How do we build a ten-ton machine whose mechanical presence can vanish under the fingers of an artist? Here are a few of the myriad issues to be considered by the organbuilder.
Architectural design
The excellent monumental organ should claim a commanding architectural presence in its surroundings. The organ relies on the building for the projection and blending of its tone, and the symbiotic relationship should include visual harmony. In that sense, the organ is the mouthpiece of the building.
Tonal structure
If an organ is intended for liturgical use in a large space, it must include:
• a wide dynamic range with individual voices carefully planned so as to allow subtle gradation between different levels of volume;
• enough variety of tone to satisfy the requirements of congregational leadership, expressive accompaniment of solo voices and choruses, festival outbursts, and the realm of solo organ literature;
• multiple keyboard divisions, each with a specific purpose and individual character, and each blending seamlessly with all the others.
Limitless lungs
A mentor and colleague once shared his mantra with me, “Air is the fuel we burn to produce organ tone.” If we are setting out to produce monumental tone in a monumental space, we are going to need a lot of fuel. It takes a hurricane of air to make one big bass pipe go. Once in a while, when servicing an organ, I have occasion to lift one of those big babies from its hole, and let me tell you, until you have experienced ten or fifteen inches of wind blasting through that six-inch hole, you cannot have full appreciation of the amount of energy involved in the speech of that pipe.
Add to that one toehole the hundreds involved in the last fortissimo chord of French toccata, and you might get a sense of what’s going on. A six-note chord with a hundred stops playing equals how many toeholes? A large organ blower might be able to move ten thousand cubic feet of air per minute at whatever pressure the organ is running on. How big is ten thousand cubic feet? It’s fifty by twenty by ten feet. A professional bowling lane is sixty feet long.
The machines and reservoirs that create and store the pressure are accurately regulated to provide pressure at a steady and constant rate. If the pressure varies, so does the pitch and intensity of the tone.
Sensitive mechanics
I have stressed several times the importance of silence of the organ’s mechanical systems. Once again, it is impossible, practically, to make such a complex and monstrous machine disappear. The listener may hear a “thump” from the console during a big registration change, a squeak from an expression shutter, a click from a distant primary valve. The organist and the organbuilder or maintenance technician cooperate to correct and repair those conditions as they arise. I know I have spent hundreds of hours crawling around in organs looking for extraneous mechanical noises. On more than one occasion, it has turned out not to be the organ at all, but a light fixture above the nave ceiling that rattles when low FFF# is played. The last time the bulb was changed, the custodian did not tighten all the screws.
The keyboards are regulated so that all feel alike, and the “strike point” of each is at precisely the same level. All the keys travel the same distance and have the same spring tension and weight.
Windchest actions are silent and consistent. Precision is essential in fabricating the mechanical parts of a pipe organ. Each must have exactly the dimensions, density, and weight in order to ensure that each note performs the same as the rest. The standard for the best pipe organ actions is the repetition rate. In both tracker and electro-pneumatic organs, the action must be free and capable of repeating faster than any human fingers can move. While many musicians assume that speed of attack is essential to rate of repetition, the offending issue is more often the (lack of) speed of release.
With all these factors faithfully executed and carefully balanced, the pipe organ becomes the perfect extension of the musician. It is an acoustic pantograph, expanding the scale of musical thought according to physical settings.
Community spirit
That organ, so beautifully balanced and scaled to its environment, is not only an extension of the thoughts and inspirations of the organist, but for the entire community of listeners and singers. While plant life takes in oxygen and produces carbon dioxide, a transformation that is essential to the balance of life, a pipe organ takes in air and exhausts air. The same air that runs through the works and the pipes of the organ is inhaled by the singers, soloists, choristers, and congregants alike, who in turn produce musical tone in harmony with the instrument. The inspiration and exchange of air enables the inspiration and exchange of musical ideas, emotional responses, worshipful experiences, and the range of human interaction. Those sensations are measured in goose bumps.
The organ in the church where I played last was not extraordinary, but it was a good, solid, pretty complete three-manual electro-pneumatic organ. It was in good condition and everything worked, and the independent voices blended nicely into choruses, with solo singers, the choir, and with the congregation. It was a familiar part of the family, and together we rode its broad back through countless adventures. It was a magic carpet ride with plenty of seats and cup holders. I loved it.