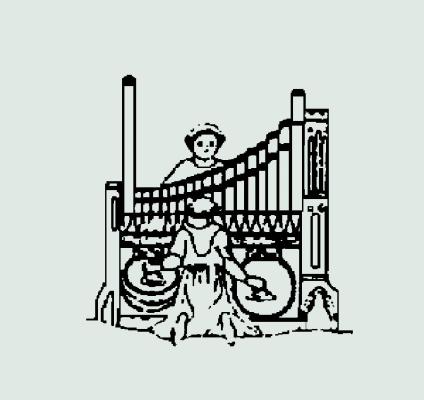
Who you gonna call?
When I was an organ major at Oberlin in the mid-1970s, I had a part-time job working for Jan Leek, a first-generation Hollander who came to the United States to work for Walter Holtkamp and wound up as Oberlin’s organ and harpsichord technician. Traveling around the Ohio and Pennsylvania countryside with Jan making organ service calls, I learned to tune and learned the strengths and weaknesses of action systems of many different organbuilders. I moved back to Boston in 1984 with my wife and two young sons to join the workshop of Angerstein & Associates, where along with larger projects including the construction of new organs, I made hundreds of service calls. That workshop closed in 1987 when Daniel Angerstein was appointed tonal director for M. P. Möller, and I entered a decade during which I cared for as many as 125 organs each year as the Bishop Organ Company.
I’ve always been an advocate for diligent organ maintenance, but ironically, I’ve noticed in my work with the Organ Clearing House that century-old instruments that have never been maintained are sometimes the most valuable. The pipes are straight and true, the original voicing is intact, and there’s not a trace of duct tape anywhere. You remove a dense layer of grime (mostly carried out of the organ on your clothes) to reveal a pristine instrument. You might take that as an argument not to maintain an organ, but the truth is that I’ve found most of those organs in remote humble churches, where in many cases they haven’t been played for decades.
The challenge for the conscientious organ technician is not to leave a mark. If your tuning techniques damage pipes, you’re not doing it right. You should not leave scrape marks on the resonators with your tuning tools, and you shouldn’t tear open the slots of reed pipes. Cone-tuned pipes should stay cylindrical with their solder seams unviolated. Wiring harnesses should be neat and orderly, with no loopy add-ons. Floors and walkboards should be vacuumed and blower rooms should be kept clean.
There are legitimate excuses for fast-and-dirty repairs during service calls, especially if you’re correcting a nasty problem just before an important musical event. But if you do that, you owe it to the client to make it nice when you return.1 And, when you do make a fast-and-dirty repair, you should adjust your toolkit to accommodate the next one. Did you use a scrap from a Sunday bulletin to refit the stopper of a Gedeckt pipe? Put some leather in your toolbox when you get home.
Many of the churches where I’ve maintained organs are now closed. Many others have diminished their programs and aren’t “doing music” anymore. Some tell me that they can’t find an organist, which is often because they’re not offering a proper salary, and some have “gone clappy.” In this climate, I think it’s increasingly important for organ technicians to be ready to help churches care properly and economically for their pipe organs.
Some churches charge their organists with curatorial responsibilities, purposely placing the care of the organ in the musician’s job description. Others do not, and it’s often a struggle to get boards and committees to grasp the concept of responsible care of their organs. It’s also important to note that while most churches once had full-time sextons or custodians, that position is often eliminated as budgets are cut. Lots of church buildings, especially larger ones, have sophisticated engineering plants that include HVAC, elevators, alarm systems, and sump pumps. The old-time church sexton knew to keep an eye on all that, and to be sure they were serviced and evaluated regularly. Hiring an outside vendor to clean the building does not replace the custodian. I think it makes sense for such a church to engage a mechanical engineer as consultant to visit the building a few times each year checking on machinery, and have volunteers clean the building.
A pipe organ is a machine like none other, a combination of liturgical art and industrial product. A layman might look inside an organ chamber and see a machine, but the musician sits on the bench facing a musical instrument. If you think that the governing bodies of your church don’t fully appreciate the value of their organ, I offer a few thoughts you might use to raise awareness.
“Cleanliness is next to Godliness”
It’s an old saw, but besides your personal hygiene, there’s likely nowhere in your life where it rings truer than in your pipe organ. After fire, flood, and vandalism, dirt is the worst enemy of the pipe organ. An organ technician knows that a fleck of dust getting trapped on the armature of a chest magnet or the surface of a pallet is enough to cause a cipher. The leg of a spider will wreck the speech of a trumpet pipe, most likely one of the first five notes of the D-major scale, ready to spoil almost every wedding voluntary.
But where did that dirt come from? When building windchests, windlines, bellows, and wind regulators, the organbuilder tries hard to ensure that there’s no sawdust left inside. I have an air compressor and powerful vacuum cleaner permanently mounted by my workbench so I hardly have to take a step to clean the interior of a project I’m finishing.
Assuming that the organbuilder delivered a clean organ, the first obvious place for an organ to pick up dirt is in the blower room. Many organ blowers are located in remote basement rooms, and in many cases, there’s no one changing the light bulbs in basement corridors, and there’s no one in the building who knows what that thing is. We routinely find blower rooms chock full of detritus—remnants of Christmas pageants, church fairs, flea markets, and youth group car washes. Organ blowers can have electric motors of five horsepower or more, and I often see 90 or 100-year-old motors that throw impressive displays of sparks when they start up. If the ventilation is obstructed, a fire hazard is created. That sign from the 1972 church fair isn’t that important. Throw it away.
To illustrate the importance of cleanliness, I share our protocol for cleaning a blower room:
• Seal the blower intake with plastic and tape.
• Close the circuit breaker that provides power to the blower so it can’t be started accidentally.
• Vacuum, sweep, wash walls, ceiling, floor, blower housing, wind regulators, and ductwork.
• Leave the room undisturbed for 48 hours to allow dust to settle before opening and starting the blower.
Likewise, if a church fails to cover and protect their organ while the floor of the nave is sanded and refinished, they can expect serious trouble in the future.
Identification
As organist, you might be the only person in the church who can identify the areas occupied by the organ. Designate organ areas as “off limits,” with access limited to the organ technician. Nothing good will happen if the organ chamber is used for storage of old hymnals or folding chairs. Nothing good will happen if teenagers find their way inside to create a secret hidey-hole.2 Nothing good will happen if the altar guild puts a vase full of water on the organ console, and, by the way, nothing good will happen if you put your coffee cup there.
The organ’s tuning will almost certainly be disrupted if someone goes into the chamber out of curiosity. Most things inside pipe organs that are not steps lack the “no step” marking, like the touchy areas on an aircraft wing have.
Insurance
Maybe that 1927 Skinner organ in your church (lucky you) cost $9,500 to build. In the early 1970s, a new two-manual Fisk organ cost less than $40,000. I’m frequently called as consultant when a church is making a claim for damage to their organ, working either for the church or the insurance company, and I’ve been in plenty of meetings where bad news about the difference between loss and coverage is announced. It’s both possible and wise to have the replacement value of an organ assessed every five or ten years, with that value named on the church’s insurance policy.
If the organ at your church sustains $250,000 of damage because of a roof leak, and the replacement value of the organ is not specifically listed on the church’s insurance policy, a lot of discussion is likely to lead to a disappointment.
What makes good maintenance?
It’s not realistic to make a sweeping statement about how much it should cost to maintain an organ. Some instruments require weekly, even daily attention, especially if they’re large and complex, in deteriorating condition, and in use in sophisticated music programs. Some instruments require almost no maintenance. A newer organ of modest size with cone-tuning could go five years or more without needing attention.
I suggest that every organ should be visited by a professional organ technician at least once a year, even if no tuning is needed, even if every note plays perfectly, even if all the indicators and accessories are working. The lubrication of the blower should be checked, and the interior of the instrument should be inspected to guard against that one pipe in the Pedal Trombone that has started to keel over. If it’s not caught before it falls, it will take the pedal flue pipes with it. A four-hour annual visit would prevent that.
It’s usual for an organ to be serviced twice a year. While it’s traditional for those service visits to be before Easter and Christmas, at least where I live in the temperate Northeast, Christmas and Easter can both be winter holidays, so it makes more sense to tune for cold weather and hot weather, or for heat on, heat off.
Most organs do not need to be thoroughly tuned during every visit. In fact, starting over with a new “A” and fresh temperament every time can be counterproductive, unless it’s a very small organ. While the stability of tuning varies from organ to organ, most instruments hold their basic tuning well. I generally start a tuning by checking the pitch stops in octaves from the console, writing down a few that need tuning, and check the organ stop-by-stop for inaccuracies. I list a couple dozen notes that need tuning and a half-dozen stops that don’t need anything, and I list which reed notes (or stops) need to be tuned. In that way, I can build on the stability of tuning established over years, keeping the broad picture of tuning clear and concise.
Regular organ maintenance should include cleaning keyboards, vacuuming under pedalboards (the tuner keeps the pencils), checking blower lubrication, and noting larger things that will need attention in the future. Tuners, if you see cracks in a leather gusset on a wind regulator, make a note with your invoice that it will need to be releathered within several years. Your client doesn’t want to hear bad news, but they don’t want a sudden failure and emergency expense either.
When you should call
The better you know your organ, the easier to judge. I once received a panicky call from an organist saying the entire organ had gone haywire. He was abusive over the phone, and demanded that I come right away. I dropped everything and made the 90-minute drive to the church. Haughtily, he demonstrated the cause of his concern. It took me just a few seconds to isolate one pipe in the Pedal Clarion. If he had bothered to look, he could have played without the Clarion for weeks, but I couldn’t tell him that, and I’ve carried the memory of that unpleasant encounter for more than 30 years.
You should call your tuner/technician when:
• You hear a big bang from inside the organ. (Once it was a raccoon tripping a Havahart trap!)
• You hear unusual wind noise. (In some organs, a big air leak like a blown reservoir can lead to the blower overheating.)
• You hear unusual mechanical noise, grinding, thumping, squeaking, etc.
• You find paint chips in organ areas. (Is the ceiling falling in?)
• The organ blower has been left on accidentally for a long time. It’s a long time for a blower to run between Sundays.
• And obviously, when something important doesn’t work.
When you should not call
Sudden changes in climate often cause trouble with the operation of a pipe organ. Several days of heavy rain will raise the humidity inside a building so Swell shutters squeak and stick, keyboards get clammy and gummy, and the console rolltop gets stuck. If you can manage, simply let the organ be for several days. When conditions return to normal, chances are that things will start working again. Likewise, excessive dryness can cause trouble.
A couple years ago, I was rear-ended in heavy traffic on the Hutchinson River Parkway in Westchester County, just north of New York City. I drive a full-size SUV and have a heavy-duty trailer hitch so while the Mercedes that hit me left a rainbow of fluids on the road under its crumpled radiator, the only damage to my car was that the back-up camera stopped working. As I’ve driven many hundreds of thousands of miles without one, I didn’t bother to get it fixed, and I’m still perfectly happy driving the car.
If there’s a dead note in the middle octave of the Swell to Great coupler, call me and I’ll fix it. It’s important to the normal use of the organ. If there’s a dead note in the top octave of the Swell to Choir 4′ coupler, and it’s spoiling a melody in a certain piece you’re playing, choose a different registration, or choose a different piece. One good way to head your church toward giving up on the pipe organ is to spend a lot of money on single repairs that don’t matter much to the music. Remember that your church pays me the same for mileage and travel time whether I’m doing a full service call with dozens of little repairs, or making a special trip for a single issue. A cipher is a bigger issue than a dead note.
It’s important to the long life of an organ not to “overtune.” Believe it or not, many churches in northern climes do not have air-conditioning, and it’s usual for temperatures to climb into the 90s inside the organ during the summer. If an organ was built, voiced, and tuned for A=440 at 70°, you’ll ruin the reeds—really ruin them—if you try to tune them to the Principals at 90°. It doesn’t make sense to wreck an organ’s reeds for one wedding, no matter who is the bride.
One of the most difficult tuning assignments I’ve had was at Trinity Church, Copley Square in Boston, in the early 1990s when Brian Jones, Ross Wood, and the Trinity Choir were making their spectacular and ever popular recording Candlelight Carols. It was surreal to sit in the pews in the wee hours of the morning, wearing shorts and a tee-shirt, sweltering in mid-July heat, listening to David Willcocks’s fanfare and descant for O come, all ye faithful. Everyone wanted the organ to be in perfect tune, but it was my job to be sure that the organ’s spectacular antique Skinner reeds would live to see another real Christmas. More than 200,000 copies of that recording have been sold, so lots of you have a record of that tuning!
§
Remember what I said about those dead notes that are a nuisance but not critical to the use of the instrument? The most important part of the organist’s role in organ maintenance is keeping a list. Maintain a notebook on the console, and write down what you notice. You might hear a cipher in the middle of a hymn that goes away. If you can pay attention enough to identify anything about it (what division, what stop, what pitch), write it down. If you think of a question, write it down. Maybe you noticed a tuning problem during a hymn. Write down the hymn number and what piston you were using. I’ll play the hymn and find the problem.
When I make repairs, I can check things off your list, write comments about the cause, make suggestions for future repairs or adjustments, and invite you for coffee the next time. The console notebook is the most important tool for maintaining an organ.
Notes
1. As I write, I’m thinking of the three clients where I owe follow-up. You know who you are.
2. I once found a little love nest inside an organ, complete with cushions, blankets, candles, and burnt matches. What could happen?