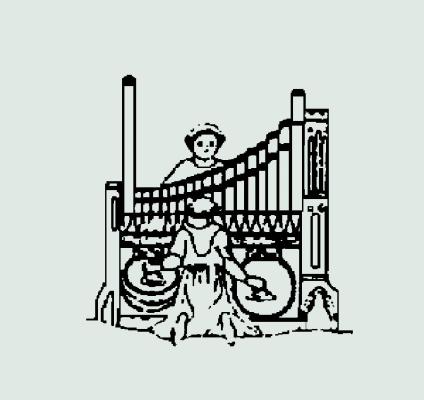
Frank Hastings, of the Weston Hastings
For the past 25 years or so, I’ve been caring for a lovely little organ in a Lutheran church in Waltham, Massachusetts. It was built by the Hook & Hastings Company in 1927, their Opus 2542. Originally, there were three stops on the Great (Diapason, Dulciana, Trumpet), five on the Swell (Stopped Diapason, Salicional, Voix Celeste, 4′ Orchestral Flute, Oboe), and a Pedal 16′ Bourdon. The Bourdon has a dual-pressure stop action and two drawknobs. When you draw 16′ Bourdon you get the same 4-inch pressure as the Swell and Great; when you draw 16′ Lieblich Gedeckt, you get 3-inch pressure, and the pipes speak more softly. If you don’t know any better and draw them both, the organ is smart enough to simply use the standard pressure.
Three ranks were added to the Great in the 1950s—a 4′ Octave, and a Quint and Super Octave that draw on one knob as Mixture II. A set of chimes was added at the same time. The additions were not made with particular historic sensitivity: they’re a little brighter than the rest of the organ. It’s fun to play using just the original stops to understand best what the builder had in mind. There’s a Tremolo for the Swell, plenty of couplers and combination settings, and a handsome little drawknob console. The entire organ is enclosed in a single expression chamber.
Such a simple little organ, so why all the fuss?
A grand tradition
Elias and George Greenleaf Hook founded their famous organbuilding firm in 1827 in Salem, Massachusetts. The first organ they built is preserved in the Peabody-Essex Museum in Salem. The company moved to Boston in 1831, occupying a site near the present North Station. It took about 18 years for the Hook brothers to produce their first 100 organs. In 1854, the firm moved again to Tremont Street to the neighborhood now occupied by Northeastern University. By that time, E. & G. G. Hook employed more than 200 workers and built 20 organs the year they moved.
Francis (Frank) Hastings was born in 1836, apprenticed with a toolmaker, and joined the firm of E. & G. G. Hook as a draftsman at the age of 19. He quickly proved himself a valuable employee and gained experience in all departments of the factory.
In 1870, E. & G. G. Hook produced 54 organs. Nine of those were three-manual instruments, including the 45-rank organ built for the First Unitarian Church of Woburn, Massachusetts, now located in the Church of the Holy Cross in Berlin, Germany. In 1870, George Hook was 63, Elias was 65, and the brothers were planning their retirement. They took Frank Hastings into partnership and changed the name of the company to E. & G. G. Hook & Hastings. George and Elias Hook died in 1880 and 1881, respectively. Frank Hastings purchased their shares in the company, and the name was changed to Hook & Hastings.
Frank Hastings had grown up in Weston, Massachusetts, now an affluent suburb to the west of Boston. But in the 1830s and 40s, Weston was rolling farmland with few trees and no hint of proximity to the city, excepting the Fitchburg (later Boston & Maine) Railroad that passed through town. Frank’s grandfather, Jonas, worked as a boot-maker and farmer; his father, Francis, had continued that work. Frank was born in the house Jonas had built on North Avenue in 1823. Frank may have loved living in the country, but he hated making boots and farming as much as he hated school, so he dropped out at the age of 14 and found work in Boston. Although he had worked in the city most of his life, he dreamed of moving the Hook & Hastings factory to Weston.
This was more than a bucolic or nostalgic urge. The 1880s were the dawn of labor unrest, and many American companies were struggling to control their work forces. This led to the founding of the American Federation of Labor (AFL) in 1886, the same year that an anarchist exploded a bomb in Chicago’s Haymarket. In 1892, there was a highly publicized violent strike at Andrew Carnegie’s Homestead steel mill near Pittsburgh, Pennsylvania. And in 1895, striking workers at the Pullman railcar factory in Chicago were confronted by the Illinois National Guard—30 people were killed and 57 injured.
Frank Hastings conceived that he might avoid such unrest within his company if he went out of his way to provide comfortable living and working conditions for his employees and their families. So in 1884, three years after the deaths of the Hook brothers, he purchased five acres of land from the family homestead, and built a gabled, Shingle-style house, directly across the road from his parents. In 1886, he purchased the remaining 45 acres of the family property, along with the 150-acre Warren farm on nearby Lexington Street. The new factory was completed in 1889, and the company was moved.
The new factory was located adjacent to Fitchburg Railroad tracks, and Mr. Hastings arranged for a whistle stop and later the small Hastings station, making it possible for his workers to commute easily from Boston. The Hastings stop is still active as a whistle stop in Boston’s commuter rail system. The proximity of the railroad allowed for efficient delivery of materials to the factory and shipment of completed organs to customers.
To accommodate his work force, Frank Hastings built cottages on his properties for workers to rent. He made inexpensive mortgages available so workers could build their own houses, stipulating that the houses must be worth at least $1,000, because if a house was too cheap, the owner wouldn’t maintain it faithfully. Hastings Hall was constructed to serve as a community center, theater, and recreation hall. Across from his house he built a caretaker’s cottage for the employee who oversaw the maintenance of gardens, lawns, and all the buildings.
In 1890, the population of Weston was around 1,600, and Hook & Hastings was by far its largest employer and industry. The Weston Historical Society has records of company parties that included dinners “under the tent,” “games and rambles,” badminton tournaments, speeches, and contests. Newspapers reported that a community of self-respecting mechanics sprang up around the factory. In 1890, the Boston Herald reported that “every man feels he has a friend in his employer. If there is any trouble coming, if there is sickness in the family, the one to whom they turn for help, for sympathy, for comfort, is the head of the concern. He knows personally every man in his employ.” Settled in the new factory, the company built 26 organs in 1890.
We know little about Frank Hastings’ first wife. Their son, Francis Warren Hastings, was an officer in the company; but his health deteriorated, and he moved to Bermuda in 1895. In 1897, Hastings hired Arthur Leslie Coburn (brother of the schoolteacher Anna Coburn, who taught at the nearby District School #4) as factory superintendent and secretary of the corporation. Frank’s first wife died during this period, and in 1899 Frank married Arthur’s sister, Anna. How’s that for a harmonious working situation?
Warren Hastings died of consumption in Bermuda in 1903, and Arthur Coburn became the president of the company. In 1904, the first full year of Coburn’s presidency, the Hook & Hastings Company built 39 organs.
Frank Hastings died in 1916 at the age of 80, 61 years after he joined E. &
G. G. Hook, and 27 years after moving the company to Weston. Arthur Coburn had assimilated enough of Frank Hastings’ philosophy that the company continued to produce organs with exceptional artistic content for about fifteen more years. But the pace was diminishing. In 1916, the year of Frank’s death, the 89-year-old company produced only 19 organs. That same year, the 10-year-old Ernest M. Skinner Company built 23 instruments.
Ernest Skinner brought formidable competition to the marketplace. At the turn of the 20th century he was young, ambitious, and a brilliant mechanic and inventor with deep musical intuition. He had a knack for providing his organs with snazzy new mechanical accessories and innovative tonal resources. In the first years of the century, his fledgling company produced instruments that were admired by the best musicians, and he quickly developed an impressive roster of clients. The meteoric rise of the Skinner firm coincided with the decline of Hook & Hastings.
After Arthur Coburn’s death in 1931, the company continued for a few years, but the quality of the instruments declined dramatically, and the output dwindled to four instruments in 1934, and four more in 1935. Anna Hastings had retained ownership of the company after Frank’s death, and as she watched the decline, she said that her husband had always put quality before price, and when organbuilders started talking about price first, it was time to stop. A contract was signed with the Mystic Building Wrecking Company of Chelsea, Massachusetts, the company’s buildings were demolished, and the corporation was dissolved in April of 1937.
Under the names of E. & G. G. Hook, E. & G. G. Hook & Hastings, Hook & Hastings, and The Hook and Hastings Company, 2,614 pipe organs were built over a span of 110 years. They were located in 47 states and as far away as Quebec, London, Dresden, and Chihuahua, Mexico. Organs were installed in two churches in Honolulu, one in 1875, and another in 1893. Often, when I’m sitting at my desk talking on the phone, my correspondent and I exchange photos and documents by e-mail or text. It’s surreal to be talking with someone in Australia, and having a message arrive in a few seconds. In 1876, a railroad train crossed the continental United States in 83 hours, setting a new record. Those Honolulu organs must have left Weston by rail, traveling to San Francisco where they were transferred to ships for the 2,100-mile voyage to Hawaii. It would have taken weeks to send proposals and drawings back and forth, to exchange signed copies of contracts and receive funds. Did Hook & Hastings send a crew to install an organ, or were there locals available on the island?
Why the fuss?
Remember that neat little organ in Waltham I mentioned earlier? It’s The Hook & Hastings Company Opus 2542, and it’s located about two miles from the site of the Hook & Hastings factory in Weston. It was built in 1927, four years before Arthur Coburn passed away, one of 11 instruments built that year. That organ would have been delivered on a small truck, taking less than half an hour to travel from factory to church. Maybe Anna Hastings and her brother Arthur went to hear it since it was so close to home.
The factory building is long gone, but Frank Hastings’ house is still there. The homestead across the street where Frank was born is still there, as are about a dozen of the houses built by the factory workers using mortgages provided by the company. After tuning in Waltham, it’s fun to take a spin past all that. Just after you pass Frank’s house at 190 North Street, turn left onto Viles Street. The first right off Viles is Hastings Road. The railroad tracks that passed the factory are a few hundred feet further down Viles Street.
What a heritage. Today, Hastings is a leafy, upscale neighborhood, where the heaviest traffic is landscapers’ trucks. I pull off to the side of the road and imagine the bustle of a 280-foot-long wood factory with scores of skilled workers creating hundreds of beautiful pipe organs. In the early days of the factory, there would have been plenty of horse-and-dray traffic delivering materials, and hauling finished organs for local delivery. The company opus list shows nearly 600 organs delivered to churches in Massachusetts, more than 90 in Boston alone! In the 1890s, the factory shipped around 50 organs each year. Roughly once a week, an instrument would be loaded onto wagons or railroad cars. Thousands of ranks of pipes, millions of action parts, and tons and tons of windchests, reservoirs, blowers, consoles, casework, and building frames left Weston each year.
Hook & Hastings to the land of the lemurs
In 1915, one year before Frank Hastings died, the company built a one-manual organ (Opus 2369) with six ranks for the Church of the Sacred Heart in Greenville, New Hampshire. It was moved by the Organ Clearing House to St. John’s Episcopal Church in Charlestown, Massachusetts, in 1995, where it was installed for temporary use while George Bozeman & Company were preparing the installation of a larger organ. When that organ was installed in 1996, the Hook & Hastings was moved to an upstairs parish hall, where it sat, little used.
In March of 2008, I received a phone call from Zina Andrianarivelo, Madagascar’s ambassador to the United Nations. I thought, of course you’re the ambassador from Madagascar. What ensued was a lifetime adventure. The Protestant (Presbyterian) churches in the capital city, Antananarivo, were preparing for the 140th anniversary of three acts of martyrdom, when an evil pagan Malagash queen ordered the murder of Christian missionaries. Three church buildings were established on those sites. One of those churches, located on the edge of a dramatic cliff was named Ampamarinana, which translates as “the Church of the Hurling Cliff.”
The nation’s president, Marc Ravalomanana, was also the vice-president of the National Church. He had charged the ambassador with “going back to the United States and finding a pipe organ for this church.” Skepticism satisfied, I went to New York (I lived in Boston at the time) and met with Mr. Andrianarivelo—I figured that I was the only organbuilder working at the United Nations that day.
Zina (we were on first-name terms right away) told me a little about the history of the churches, and the president’s desire to import organs to several churches. The priority would be the main central church, Faravohitra, where the anniversary service was planned for early November. Could we start with that one? It’s a pretty tall order to move and install an organ internationally in five months, but I thought of the one-manual Hook & Hastings in Charlestown, and suggested that we could relocate it quickly for temporary installation. We could bring a larger organ later, and move Opus 2369 to another smaller church.
Zina arranged for my visa, I followed the advice of the State Department concerning vaccinations (they warned me to be sure of the source of water I drank, including ice cubes), and received my airline ticket—my one-way airline ticket. Madagascar was formerly a French colony, so it’s serviced by Air France. They schedule weekly flights from Paris to Antananarivo (which is colloquially shortened to Tanariv, or simply, Tana), but they don’t schedule return flights until there are enough passengers on a list to fill a plane. I’m a stickler about travel arrangements, always being sure I have reservation numbers, flight information, accommodations, and addresses. Zina assured me there would be nothing to worry about.
I flew from New York to Paris, and then to Tana on a flight that would arrive there after midnight. I didn’t know who would meet me. I didn’t know how I would get from the airport to the city, 20 kilometers away. I didn’t know where I’d be staying, or how I would get around the city. And I didn’t know when I’d be going home. But I got on the plane for the 12-hour flight. Zina said it would be OK.
In next month’s column, I’ll tell my Malagash tales.
I offer thanks to Pamela Fox of the Weston Historical Society for providing photographs and facts, and for reading an early draft of this essay. Her command of this history and cheerful contributions have added much to my telling of this tale.