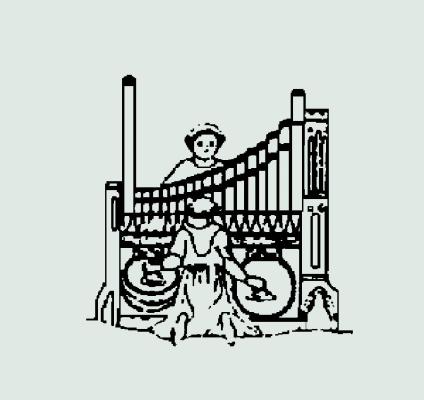
I didn’t know there were any of you left.
Frequently I am invited to speak about the pipe organ to community gatherings, AGO meetings, and the congregations of churches with which we work. Those who have heard me give such a talk have likely heard the description of a hypothetical scenario: You’re meeting people in a social situation—a cocktail party for example—standing in a little circle going through predictable small-talk. Someone asks what you do for a living. One replies, “I’m a college English professor.” “I’m an investment banker.” “I’m a pipe organ builder.” “A pipe organ builder, I didn’t know there were any of you left.” This happens to me often enough to be comical. Yesterday I heard a new sarcastic twist: “That’s funny, you must be the sixth organbuilder I’ve met this week!”
Those conversations typically continue as nice opportunities to talk about our trade, and when I say that there are professional trade organizations with conventions and monthly journals, my interlocutors are again amazed.
Last month I attended the convention of the American Institute of Organbuilders (AIO) in Seattle. The Pacific Northwest is a great region for the pipe organ. There are a number of outstanding builders located there, and a fleet of terrific organs. The scenery is spectacular. Mt. Rainier (14,410 feet) pokes its snowy head through the clouds, the Seattle waterfront is a blend of busy international port and picturesque marketplace. The Olympic Mountains loom to the west across Puget Sound serving as host to grand sunsets. And the city itself nestles between the waterfront and dramatic hillsides. Ferryboats and seaplanes are important parts of Seattle’s transportation system. Public cultural events such as concerts and theater are scheduled to work with the ferry schedule lest a concert be disrupted by the departure of hundreds of audience members determined to catch the last boat.
An AIO convention includes plenty of visits to churches and concert halls for demonstrations and concerts on a variety of organs. The rollicking bus rides are a mainstay just as they are at conventions of the AGO or the OHS. There were lectures on a variety of subjects at the convention hotel, and many suppliers to the trade were exhibiting their wares and services in the exhibit hall, which also served as center of much of the socializing. (I treated myself to a long-coveted set of wood-handled brass tuning cones at the Laukhuff booth.)
The AIO convention was the last week of three on the road for me. The Organ Clearing House had just completed the delivery of M.P. Möller’s Opus 5819 to the University of Oklahoma. (You can read about this exciting project elsewhere in this issue of The Diapason, and I will write about it in detail next month.) Originally housed in the Philadelphia Civic Center, and given to Oklahoma by the University of Pennsylvania, the organ will be the centerpiece of the American Organ Institute directed by Professor John Schwandt.
It’s all the same to me.
My trip included a week each in Philadelphia, Norman, Oklahoma, and Seattle. I changed planes in Atlanta and Denver. Starting and ending in Boston, that made seven flights and six airports, and the common thread was sameness. The vendors in all the airports were virtually identical. I started the trip with a book of crossword puzzles that was less than I hoped, but couldn’t find a replacement because Hudson News was carrying the same book in all its stores across the country. The culinary experience in our airports is barely worth mentioning. The sameness of the airports makes it easy to find your way around—signage, numbering systems, even layout is very similar from place to place. But a little exposure to local color would be nice. Having changed planes in Denver, one cannot say one has been to Denver.
From the air you see interchangeable real estate developments, shopping malls, industrial parks. And although the landscapes are different (to someone from the Northeast, Oklahoma sure is flat), once you get away from the airports there is much sameness. We are trained to recognize corporate logos enough to leave no doubt that you are passing Home Depot, Applebee’s, or Sears even if you are too far away to read the text on the sign. I did some shopping in Norman and, although the names of the department stores were different, the floor plans were sure familiar (you can’t get anywhere without having to walk through the cosmetics department!). A striking and unsettling example of sameness is found in the national chains of bookstores. You would think that the interests of readers would vary between regions, but the front tables in Barnes & Noble stores are identical in Boston and Oklahoma City. All of that chain’s buying is done in an office in New York by people who must know best what all Americans should be reading.
National chains of restaurants allow us to buy a predictable meal in any city. I’ve heard people say that this eliminates the risk of having a bad meal. I suggest it’s more like choosing a bad meal instead of risking a good one. Leave a hotel looking for a family-owned restaurant and you’re likely to be disappointed.
While spending time chatting with the good folks in the exhibition booths at the AIO convention, I reflected that there is a significant vein of sameness in the American organ industry. A couple generations ago, if an organbuilder wanted to include a combination action in an organ’s console, they had to build it themselves. Those were the days when many organbuilders had hundreds of employees, and we marvel at the long lists of monumental organs built by the big firms in the early 20th century (the Skinner opus list shows that Ernest Skinner built 39 four-manual organs before the end of 1915), forgetting perhaps that those shops employed hundreds of workers. Many of today’s small organbuilding firms would be hard pressed to build their own combination actions. The fact that organs built by a dozen different companies might have identical combination actions is actually an advantage. The elegant and reliable products offered by such firms as Peterson, Solid State Organ Systems, Laukhuff, Heuss, Artisan Instruments, and Classic Organ Works (among others) make it possible for the independent organbuilder to focus on the artistic content of their instruments.
Who’s driving?
It’s a well-understood fact that the organs of Aristide Cavaillé-Coll (1811–1899) were the driving force behind an entire school of organ composition. Composers such as Franck, Widor, Dupré, Tournemire, Vierne, Messiaen, and Mulet were inspired and challenged by those grand organs that featured countless mechanical and tonal innovations. It’s not as easy to tell who was in charge in other eras of organbuilding. J.S. Bach was knowledgeable about the organs of Gottfried Silbermann, but who was teaching whom? We know Bach worked as a consultant, hired by churches to review new organs when they were completed. His comments were sometimes negative—he was especially critical of inadequate wind systems—but one can say that his music was exploring the capabilities of the organs he played. The mid-20th-century American Organ Renaissance was to some extent a collaboration between organists and organbuilders. Organists helped raise awareness of the classic traditions while organbuilders worked hard to interpret them. But the fact that organists became divided (sometimes bitterly) over the issue of tracker vs. electric implies that the organbuilders were really running the show.
During the convention, I was impressed by the number of conversations among organbuilders that focused on playing. During the 1980s there was a disappointing drop in the number of young people studying organ, and several prominent schools have recently closed their organ departments. But AGO Pipe Organ Encounters have been enormously successful, and a number of important university organ departments are thriving. There is a clear upswing in the number and quality of young organists, and our brilliant young players are demanding much of their organbuilders. In my experience, players are increasingly aware of the quality, refinement, and versatility of their instruments. They have sophisticated understandings of organ sound and highly developed personal approaches to registration, not relying on accepted standards of registration but using their ears to blend colors. They are demanding much of their instruments and much of those who build and maintain them. This is a very good thing.
While organbuilders in general have often been inclined to talk about instruments as if they were separate from the music, I observe that players are increasingly the focus. I had several conversations at the convention with colleagues who wanted to share how moved they were by hearing what a particular player brought out of an instrument. More than one expressed that the experience “made it all worthwhile.” Aha—we are building instruments for the sake of music. A layperson might see a pipe organ as a mechanical marvel (of course that’s true!), but a well-conceived and beautifully built organ in the hands of a great player transcends the mechanical.
Nothing new under the sun?
The October issue of The American Organist features an article by Moo-Young Kim that presents a study of the programming of recent American organ recitals. Using pie charts and other graphic illustrations, the frequency of performance of pieces of organ literature is analyzed. The result of the study is easy enough to predict—if you took away the top 20 or so titles you’d have little left. This reflects a dilemma. We know that audiences lean toward the familiar. (How many times have you tried to steer a bride away from Jesu, Joy of Man’s Desiring or Canon in D?) But finding ways to balance the familiar with new music that will challenge, inspire, and thrill the public must be one of our principal goals. We all know that the pipe organ was integral to the musical life of a community 200 years ago. What about today? What about tomorrow?
In answer to this I share thoughts about what was for me the high point of my experience in Seattle. St. Mark’s Cathedral (Episcopal) is an unusual building in a dramatic location on one of the city’s hillsides. The building was planned in 1928 combining traditional Gothic lines with newly developed poured-concrete construction. The collapse of the stock market in 1929 caused the collapse of the funding of the project, and only the crossing was completed. The cathedral’s website
The stoplist comprises Dutch nomenclature, so familiar from my days as a student at Oberlin (a town of 8500 people that was home to more than 20 Flentrop organs in 1978), and implies a clear historically focused style of organbuilding. I’ve heard this organ on four different occasions, and each time I’ve been amazed at its versatility. The organ’s sound is brilliant and full. It’s expressive and sweet. It’s powerful enough to defy the low wind pressures. It’s simply thrilling to hear. It’s more than 40 years old and must be considered one of the monuments of 20th-century organbuilding.
Douglas Cleveland was the recitalist. Having just read the previously mentioned article in The American Organist, I noted quickly the predictability of the program: Bruhns G major, Vivaldi/Bach D minor, Schübler Chorales, St. Anne Prelude and Fugue. Nothing new under the sun—except for two important points: first, Mr. Cleveland is a stupendous player, and second, that was only the first half. His presentation of those standards of the repertory was fresh and inviting. The second half of the program included Ave Maris Stella by Pamela Decker, Pièces de Fantaisie (Deuxième Suite) by Louis Vierne, and the world premier of Four Concert Etudes by David Briggs. Perfect. In the first half, Mr. Cleveland’s playing and the Flentrop organ won me over with their classic beauty. In the second, I (and the friends around me) was dazzled by the grandeur, excitement, and the sheer sonic power of the marriage between the organ and this smashing new music. I hope that Briggs’s Four Concert Etudes will get many more readings. Mr. Briggs is himself a marvelous organist—his music reflects that deep understanding of his instrument—and Mr. Cleveland knew how to interpret it with his understanding of the terrific instrument given for his use that night, and the audience was the richer for it. More, please!