Joseph E. Robinson received his B.A. from California State University at Long Beach and his M.A. from Occidental College in Los Angeles. He studied piano with Charles Shepherd and organ with Clarence Mader, Paul Stroud and Robert Prichard. During 1970–1971 he was an organbuilding apprentice with the Schlicker Organ Co. under the direction of Herman L. Schlicker. He was organist at the University United Methodist Church in Buffalo, New York, and later at St. James’ United Methodist Church in Pasadena, California.
Now a retired business systems analyst, he is currently organist for the Aliso Creek Ward, Church of Jesus Christ of Latter Day Saints, and a member of the Orange County California chapter of the American Guild of Organists. He is very grateful to his wife Pat, without whose support a large residence pipe organ would not have been possible. His interest in pipe organs and their music was sparked years ago when, as a sixth grade student, his class was taken on a field trip to a recital on the Mormon Tabernacle organ.
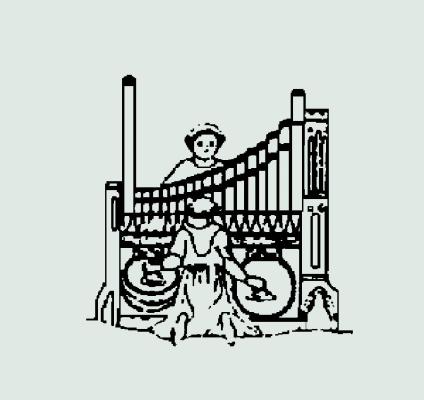
Graduate school was a joy, offering full-time study of music and the use of three fine instruments (two 4-manual Aeolian-Skinners, one 3-manual Schlicker). But that happy situation was not to last, the real world providing a career in information technology with employers adamantly against a church job. With payroll usually due Friday morning, any complications that occurred on Thursday had to be solved. “Sorry, I have to go to choir practice” was unacceptable.
Missing the superb organs of graduate school, I thought that my need for an instrument might be fulfilled by a fine residence instrument. With great optimism, in 1980, I bought a large 4-manual Casavant console. It would take, I figured, about 27 ranks to do what I “needed” done. But even at that, I would only use a small portion of the console, unless I resorted to horrendous unification. Perhaps the resources could be expanded with analog electronic generators. No, that sound simply was not good enough.
Within the last decade, the major digital organ companies (Allen, Rodgers, Ahlborn-Galanti, Johannus, etc.) have produced reasonably priced MIDI modules with digital sampling that have a lot to offer. The lessons learned in adding four of these units to my residence pipe organ provide the material for this article. I now have 20 ranks of pipes playing and four MIDI modules. Equipment The four modules are an Ahlborn Classic Archive module, an Allen MDS Expander II, the Rodgers MX-200, and a custom Cavaillé-Coll sampled module installed on an Ahlborn chassis. Syndyne LS6401 stop controllers control the two Ahlborn-based modules. All the modules are controlled by normal stops and pistons.
Speaker placement
I connected the first module purchased to my high-quality stereo system. The loudspeakers were on the opposite side of the room from the pipe ranks. Such placement only served to accent the differences between the digital stops and the real pipes. The best place for the speakers turned out to be behind the pipe chests with the speakers pointing at the wall rather than the listeners. Sound now bounces off the wall and travels through the pipe ranks before arriving at the listener. Now there is cohesion of pipe and digital sound that is light years ahead of the original placement. Proper speaker placement can be the difference between success and mediocrity.
Experience has shown that for my residence, I did not need special “organ speakers,” but high-quality stereo speakers do the job splendidly. Since these modules have 32' stops, there are four powered subwoofers that are rated flat (+ or – 3 db) down to 20 Hz. These 32' stops require this kind of support if they are not going to just fizzle out as you approach low C.
Level balance
Each of the modules includes a big reed of some sort (i.e., Festival Trumpet, Trompette en Chamade, Spanish Trumpet, and Royal Trumpet). These and other stops can be set to appropriate high volume levels. That approach results in your organ becoming a “digital organ with pipes.”
My dominant manual pipe reed is a Trompette Musette. So I set the volume level of all the digital big reeds to be slightly less than that. Next in power in the pipes is a Dulzian. All digital trumpets are set to be slightly less than it is. Third in the reed pipe ranks is a Krummhorn. The digital Hautbois, Clarinette and so forth are set in level slightly below that. A similar pattern is used for all the flue stops. In this manner the full ensemble is a pipe-dominated ensemble. It is very tempting to do otherwise, but the cost of doing otherwise is to turn your pipe organ into an electronic.
Tuning
Pipes vary in pitch with change in weather. MIDI modules do not. The modules need to be tuned to the pipes if they are to blend in. That is easily accomplished. Finding what works and what does not Each of these modules from these competing manufacturers has different strengths and weaknesses. Furthermore, even within the same product, the quality of digital sampling can vary greatly. For example, the Rodgers MX-200 contains a 32' pedal Bazuin that is almost good enough to justify the cost of the unit by itself. On the other hand there is an ensemble Principal chorus 8', 4', 2' that to my ear sounds like a 1940s electronic with Leslie speaker on slow with spring-loaded reverb. That sound may be desirable in some quarters, but not for my pipe organ. So in working with these units, you find things that work very well, and other things that you will not use.
Mutations. In general, these work extremely well. For example, on the Positiv, my 8¢ pipe Holz Gedeckt combined with the Allen Sesquialtera is every bit as good as the real deal on the Swell. Mixtures. On my Swell I am using an Ahlborn-Galanti Plein Jeu and on the Great a Rodgers Fourniture. These are working out so well that I have decided I can forgo the real mixture I originally planned and thus save space.
Flue Doubles. Sometimes a 16' flue is nice to have on the manuals. The real estate such stops take up makes them impractical for a residence organ. The Allen 16¢ Gedeckt, for example, works very well when used in conjunction with real manual flutes.
On the Pedal I have a real 16' Subbass. On some small pipe organs, a single pipe rank is used for a Lieblich Gedeckt and a more powerful Subbass by varying the wind pressure supplied the pipes. That practice is often unsatisfactory. The digital units fill the Lieblich function well. In a Rodgers workshop, Hector Olivera mentioned that he was a bit tired of the overdone ca-chunk attack of 16' pedal stops on many “organ reform” instruments. So, if I use the Allen Bourdon on the Pedal, I get a tasteful ca-chunk. If I use the Rodgers, there is no ca-chunk. You move to the real Subbass when more is happening.
Celestes. I purchased a real Gemshorn and its corresponding Celeste. The Gemshorn is the most recently installed rank on my organ. Until I could get the Celeste installed, I decided to assign one of the Rodgers Celeste stops to that function. Even though by itself this Rodgers Celeste does not sound realistic in all areas of the compass, when combined with the real Gemshorn, the result is fabulous. The effect is sufficiently successful that I have decided to forgo the real Celeste, since I don’t have room for all the remaining ranks I want.
Observation. In the above paragraphs I have listed the functions in which the digital stops work very well. In these functions, the digital stops have the following things in common:
1. Real pipe ranks are combined with them giving the “breath of life.”
2. The digital stops have a pitch relationship to those pipes as well as a timbre relationship.
Generally when you are looking for a certain timbre from a digital stop and that stop is to be used alone, the result is often not as good. The same is often true when only digital stops are combined. Reeds. Today’s digital reeds are better than ever before. But that is not to say that they equal pipes. Nevertheless, they can be quite useful.
My organ contains four real reed ranks (Rankette, Dulzian, Krummhorn, and Trompette Musette). Note that they are all short-length resonator types. Suppose the middle section of Franck’s Pastorale is to be played. With the Cavaillé-Coll unit, the Trompette can be used. Not bad, but it sounds digital. Using the real Krummhorn gives a sound that is too “Baroqueish.” But when using the Trompette and Krummhorn together something wonderful happens. The Trompette seems to give the Krummhorn a full-length resonator sound, while the Krummhorn gives the Trompette the attack and other missing characteristics of a real reed stop.
In the Pedal I use two 32' digital reeds. These are the 32' Bombarde from the Ahlborn-Galanti and the 32' Bazuin from the Rodgers unit. As good as they are, they could be better. From the lesson learned above, I ordered a 32' octave for my Rankette from Germany. This short-length 32' stop gives the digital stops the real slap of the reed tongue that they were missing. The digital stops in turn give the effect of a full-length resonator.
Principals. The older analog electronic organs provided some sort of generic sound called Diapason. With these digital modules, the principals have character. The Ahlborn-Galanti Principal has a southern European flavor. The Cavaillé-Coll Montre gives something of the sound of slotted pipes. The Allen Principal has a northern European influence. The Ahlborn-Galanti Principal is used on my Positiv division whose pipe 8' flue is the Holz Gedeckt. This Principal adds some interesting foundation tone when added to the Positiv ensemble.
That said, however, the following also needs to be noted. Suppose the final measures of Bach’s “St. Anne” triple fugue in E-flat major are played. Combining the Great pipe stops of Principals 8', 4', and 2' with the Allen 16' Principal, the Rodgers IV Fourniture, and the Ahlborn-Galanti III Cymbale gives a very good sound. What happens though if digital 8', 4', and 2' Principals are substituted for the real ones? Then you move instantly from the real organ sound to a pale imitation. If at all possible, you want at least your 8' and 4' principals to be real!
Orchestral sounds. The Allen and Rodgers modules offer orchestral sounds in addition to organ stops. While in general I do not see great art served by a one-man imitation orchestra, a number of these sounds are very useful. The Allen orchestral flute, for example, with tremolo, combined with a real 8' Koppelfloete produces a most lovely flute solo. In addition to its many orchestral sounds, the Rodgers can alter the attack by way of “velocity sensing” keyboards. That feature I can’t comment on: with my 1927 Casavant console the note is either on or off.
I just ran out of notes! While the advertisements and user manuals don’t mention it, when you own the modules, you may soon discover that you run out of notes. One reason is explained in more detail in Jerome Markowitz’s book Triumphs & Trials of an Organ Builder. In brief, as the digital organ was being developed, it was “financially questionable.” A Rockwell engineer by the name of Watson reasoned that people have ten fingers and two feet. Hence there would only have to be 12 notes available for playing at any time, not 61. That reduction resulted in a great cost saving.
If you have played an Allen or Rodgers organ that supports these MIDI modules, you will notice that the MIDI stops do not couple. On my console, it all couples. To couple is the equivalent of playing more notes. On a three- or four-manual console, if a MIDI stop is selected on each manual and pedal, and all manuals are coupled to Great and Pedal, and we come to the end of a composition such as Vierne’s Carillon de Westminster, the MIDI modules are going to run out of notes. The first notes lost in overplaying are the lowest notes, so that 32' reed is lost precisely when needed most. So you use good organ sense and reduce the number of MIDI stops requested of a module until it can supply all the notes.
Perhaps because the Ahlborn-Galanti uses a MIDI channel per division rather than per stop, you can use all its stops coupled and still have eight simultaneous notes available before overplaying. A nice design feature is that notes are lost from the second note up when over played. So on this module that important bass note is always there.
Distinctive features
Allen went to some effort to make their module organist-friendly. On the LCD you see organ divisions (SW, GT, etc.), not MIDI channel numbers. You also see the name of the stop that is going to play when you activate the MIDI tab or knob. This intuitiveness is a good feature of the Allen for those of us who want organ terms and not MIDI terms. The Allen provides more organ stop samples than any other module. [Note: Allen has replaced the MDS Expander II with a newer model. These features apply to both.]
The Rodgers MX-200 provides almost as many organ samples as the Allen. With 170 orchestral samples it excels in this area. This unit is also most like MIDI sound modules obtainable outside the organ world. On a Rodgers organ, a sound may be assigned to a MIDI channel by a “Quick Key.” Set much like a capture combination action, for example, when middle C is pressed, the selected MIDI “stop” becomes a 16' Pommer. For a non-Rodgers organ, move the part knob to the MIDI channel to be changed, set the selector switch to “flue” and turn the value knob until the number “3” appears on the display. That gives the same 16' Pommer. Since only a number appears and not a stop name, I keep my owner’s manual at the organ at all times.
Using a very different approach, Ahlborn-Galanti gives you only 20 sampled organ stops. However, the Ahlborn-Galanti is like a 20-stop organ in a box. These stops may be combined and coupled in any way. Great flexibility is provided in adjusting the relative levels and scales of each of these stops. By using a MIDI channel per division rather than per stop, only three MIDI channels are used for the 20 stops, in contrast with the one stop to one MIDI channel of the others.
If an organ needs more stops, the Ahlborn-Galanti unit is a good choice to provide 20 more stops. On the other hand, if the basic specification is sufficient, and you occasionally want to augment with a more exotic stop (i.e., French Horn or Harp and Chimes, or a 11⁄7' Septieme, etc.), then an Allen or Rodgers unit is a good choice. And of course, you can do both and more as finances permit.
Conclusion
If I had it to do all over again, I would still do the same mix to get the advantages of each brand. One does have to use a little organ common sense to get the best effects. In the Principal section I mentioned for the closing of a big Bach fugue, I used the pipe Principals of 8', 4', and 2' along with the Allen 16' Principal, the Rodgers IV Fourniture, and the Ahlborn-Galanti III Cymbale. By spreading the load across the several modules, you gain the advantages of using more loudspeakers and amplified channels, giving a more realistic ensemble effect. These modules have given me the flexibility to play effectively the same music I used to play on the large pipe organs in graduate school. When properly adjusted to complement rather than blot out or compete with the pipes, these modules offer a lot of resources at a very reasonable price.