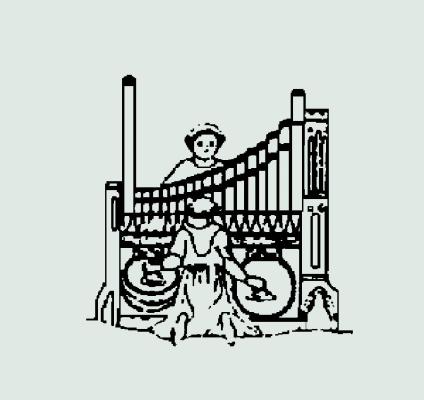
Berghaus Pipe Organ Builders, Bellwood, Illinois
1966 Aeolian-Skinner Organ Company Opus 1455
Church of the Holy Comforter, Kenilworth, Illinois
Organ renovation projects are as diverse as the instruments themselves. The decisions and processes that are undertaken by the owners and the curators of the pipe organs are varied, but the goal is always to breathe new life into the instrument. Sometimes the renovation is historically accurate, sometimes it completely changes the nature of the instrument. In the case of the 1966 Aeolian-Skinner Organ Company Opus 1455 at Church of the Holy Comforter, Kenilworth, Illinois, the organ was returned to its original glory as envisioned by George E. McClay, associate dean of the School of Music at Northwestern University, Evanston, Illinois, and organist-choirmaster at Trinity Episcopal Church, Highland Park, Illinois, who served as the consultant.
The Aeolian-Skinner replaced a two-manual, eight-rank Welte organ relocated in 1928 from the Wilmette Village Theatre (which had closed), which in turn had supplanted the 1907 Hook & Hastings Opus 2147 that was an identical replacement of the builder’s Opus 2106 that had been destroyed in a fire in October 1906. As the fourth organ at Holy Comforter, the instrument’s 50 years of faithful service and thousands of hours of beautiful music for Eucharists, baptisms, weddings, funerals, concerts, and special events made it an integral part of the life of the parish. It was finally decided in 2016 to raise the funds to undertake the complicated and sophisticated project of thoroughly renewing the instrument.
In June 2016, Berghaus Pipe Organ Builders began an extensive project to clean, rebuild, and refurbish the organ to as-new condition. All of the pipework except for some of the larger pipes from the Contra Bass in the Pedal were removed from the church and taken to the Berghaus shop for cleaning and repairs.
While in the organ shop, a couple of ranks that had been altered over time were restored to original specifications. The 4′ Flute Harmonique pipes were lengthened and the hole in the center section of each pipe that produces the harmonic sound was re-created. The Viole de Gamba and Viole Celeste pipework had mysteriously been replaced with pipes that did not properly blend with the rest of the instrument. Particular attention was paid to these two ranks during the revoicing process to duplicate vintage Aeolian-Skinner characteristics.
The reservoirs were also removed for releathering. The empty chamber was then thoroughly cleaned and water-damaged areas repaired and replastered. The console was stripped and refinished, updated with new lighting and combination action, and keyboards and pedalboard rebuilt. The tonal finishing process, which took two weeks, brought the instrument back to its original tone and timbre as the organ’s wind pressures were returned to their original measurements. This offered an opportunity to prepare for a 8′ Trompete on the Great that would be extended as a 16′ Posaune in the Pedal. The organ was finished in mid-September in time to go back into service for a prominent wedding.
The organ was rededicated on Sunday, April 23, 2017, by the Reverend Dr. Jason Parkin followed by a recital given by director of music, Derek E. Nickels. Dr. Nickels’s program, which included works by Mendelssohn, Bach, Howells, Lafford, Callahan, and Dupré, very likely put each of the more than 1,300 pipes to work, and was enthusiastically received by the near-capacity crowd.
—Jean A. O’Brien
Berghaus Pipe Organ Builders
Derek E. Nickels
Church of the Holy Comforter
GREAT (Manual I, Exposed, 3″ wind pressure)
16′ Bourdon1
8′ Principal 61 pipes
8′ Bordun 61 pipes
8′ Spitzflöte (Swell 8′ Spitzflöte)
4′ Octave 61 pipes
4′ Spindleflute 61 pipes
22⁄3′ Sesquialtera II 122 pipes
2′ Blockflöte 61 pipes
II Rauschquint 122 pipes
8′ Trompete (prepared)
Tremulant
Great 16
Great Unison Off
Great 4
SWELL (Manual II, Enclosed, 3″ wind pressure)
16′ Spitzflöte (2003, TC, fr 8′ Spitzflöte)
8′ Rohrflöte 61 pipes
8′ Viola da Gamba2 61 pipes
8′ Viola Celeste2 61 pipes
8′ Spitzflöte 61 pipes
8′ Flute Celeste (TC) 49 pipes
4′ Spitzprincipal 61 pipes
4′ Flûte Harmonique3 61 pipes
III–IV Plein Jeu 232 pipes
16′ Hautbois 73 pipes
8′ Trompette 61 pipes
8′ Hautbois (ext)
4′ Schalmei 61 pipes
Tremulant
Swell 16
Swell Unison Off
Swell 4
PEDAL (33⁄4″ wind pressure)
32′ Resultant (2003, from 16′ Bourdon)
16′ Contra Bass 56 pipes
16′ Bourdon 44 pipes
8′ Octave (ext 16′ Contra Bass)
8′ Bourdon (ext 16′ Bourdon)
8′ Rohrflöte (Swell)
4′ Choral Bass (ext 16′ Contra Bass)
16′ Posaune (ext Gt; prepared)
16′ Hautbois (Swell)
8′ Hautbois (Swell)
4′ Hautbois (Swell)
1. Added 1992, 1–12 Pedal 16′ Bourdon, 13–61 Swell 8′ Rohrflöte.
2. Original pipework replaced in 1992, revoiced in 2016.
3. Reconstructed to factory specifications in 2016.
COUPLERS
Great to Pedal 8
Great to Pedal 4
Swell to Pedal 8
Swell to Pedal 4
Swell to Great 16
Swell to Great 8
Swell to Great 4
ACCESSORIES
6 Great divisional thumb pistons
6 Swell divisional thumb pistons
6 Pedal divisional toe studs
5 General Pistons (thumb and toe)
Setter thumb piston
General Cancel thumb piston
Great to Pedal reversible (thumb and toe)
Swell to Pedal reversible (thumb and toe)
Swell to Great reversible (thumb piston)
Full Organ reversible (thumb and toe)
Memory Up thumb piston
Memory Down thumb piston
Swell Shoe
Crescendo Pedal
MIDI transposer, playback and record