Russell Meyer & Associates Organ Builders, Bridgeton, New Jersey
The Catholic Community of St. Charles Borromeo, Skillman, New Jersey
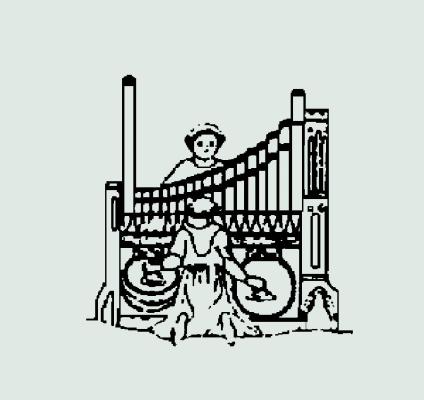
Russell Meyer & Associates
Organ Builders,
Bridgeton, New Jersey
The Catholic Community
of St. Charles Borromeo,
Skillman, New Jersey
The Catholic Community of St. Charles Borromeo is a large parish located in Skillman, New Jersey, seven miles north of Princeton, New Jersey. The building complex, which relies heavily on both modern and ancient stone and wood elements, was conceived by Monsignor Gregory E. S. Malovetz and designed by the architect Martin DeSapio. The 51,000-square-foot complex includes a sanctuary space, which houses the new organ, a daily prayer chapel, ministerial office space, meeting rooms, a library, a large youth ministry complex, two large gathering spaces, and a great room, St. Francis Hall. The entire structure is modeled after a monastery design, where the entire complex surrounds a courtyard prayer garden.
The music ministry of St. Charles Borromeo, under the direction of Tim Keyes, is an active part of the parish community, providing music for the large variety of weekly liturgical and paraliturgical celebrations. The entirely volunteer ministry includes a 35-member parish orchestra, two parish choirs, a high school youth choir, and a large cantor staff. There are also numerous musical groups that support the family catechesis program GIFT, women’s ministries, and the Children’s Liturgy of the Word.
The Salvator Mundi (Latin for “Savior of the world”) Pipe Organ takes its name from the painting by 19th-century British artist Sir Edward Coley Burne-Jones that is featured in the center of the organ’s swell box. The original conte crayon and pencil on board, 2′ x 4′ painting is owned by the Brooklyn Museum in New York. Special permission was obtained by designer Meg Poltorak Keyes to reproduce the painting and use it as part of the instrument design. The 4′ x 8′ reproduction is printed on archival linen, mounted to perforated quarter-inch sintra to allow for sound penetration, and hangs by custom-designed, hand-forged iron brackets from the Swell case top.
The organ was constructed by the now retired Russell Meyer & Associates of Bridgeton, New Jersey. It comprises 27 ranks, totaling 1,735 pipes, of which 904 are new and 831 recycled, repaired, and revoiced from older instruments. Except for two wind regulators in the Swell division, which were rebuilt by Meyer & Associates, the entire mechanism and structure is new.
The organ casework is constructed of red oak, finish stained by Meg Poltorak Keyes to match the interior woodwork of the sanctuary space. The detail in the organ case mirrors the design elements found throughout the entire building complex. The exposed façade is made of aluminum, with the largest pipes on the left and right of the instrument and the remaining pipework sloping to the center. This design reflects the action of the cantor’s arms when inviting the congregation to sing. As viewed from the front: the Great division is located on the right, the Positiv division is located on the left, and the Swell division, which is under expression, is located in the center.
The action is electro-mechanical. The state-of-the-art “Opus-Two” control system is manufactured by Essential Technology of Kanata, Ontario, Canada. The new moveable console was built by Steven Van Name—a terrace design constructed of mahogany, with rosewood drawknobs set in bird’s-eye maple terraces.
The new pipes were manufactured to Russell Meyer’s specifications and include 48 new aluminum façade pipes made by Matters, Inc. of Hermosa, South Dakota, and 856 pipes (14 ranks) imported from the Rieger-Kloss Company in the Czech Republic.
The recycled pipes come from a variety of sources: 427 pipes (7½ ranks) come from an organ (circa 1960) removed from the chapel/theatre of Sussex Community College (formerly an Oblate Friars Seminary) in Newton, New Jersey. Of these, two ranks were new when installed in that organ: the Rohrflöte and the Trompette. The rest were recycled ranks when installed in that organ and range in age from 80 to 100 years old, and include Geigen Diapason, Viole de Gambe, Nasongedeckt, Dolce, Dolce Celeste, and Lieblich Gedeckt. (The Lieblich Gedeckt is identified as originally having been made in 1927 for St. Peter’s Episcopal Church in Mountain Lakes, New Jersey.)
The Voix Celeste rank came from an organ in the Chapel of First United Methodist Church of Millville, New Jersey. The Hautbois (Oboe) was from an organ in Holy Trinity German Lutheran Church, Camden, New Jersey. The Spitz-octave rank is from an organ that was in Logan Memorial Presbyterian Church in Audubon, New Jersey. The Chimes were previously installed in St. Andrew’s Episcopal Church in Trenton.
Three ranks come from farther away. The large wood pipes of the Subbass were made by the Estey Organ Company in 1925 for Patterson Memorial Presbyterian Church in Dayton, Ohio. The Bombarde and Trompette Harmonique were manufactured in 1956 by the Reuter Organ Company for St. Mark’s United Methodist Church, Baytown, Texas.
And, finally, the copper pipes of the Cromorne were manufactured in Germany in 1972 by the Laukhuff Company for one of the last organs of the Aeolian-Skinner Company and installed in Hughes Hall Auditorium of Ohio State University in Columbus. The recycled pipework was completely cleaned and revoiced to blend with the new pipework. All the reed pipes were restored and revoiced by Trivo, Co., Inc. of Hagerstown, Maryland.
Members of Russell Meyer & Associates involved in the construction of the Salvator Mundi Organ include Russell Meyer, Adam Bojaciuk, Eric Nyman, Steven Van Name, James Murray, Joseph Ritter, and James Holland, with installation assistance from Dave Milton, George Grover, Stephen McCarthy, and Richard Sawicki. Assisting in the tonal finishing were Brantley A. Duddy, Dennis Cook, and John Thomas.
Several members of St. Charles Borromeo Church assisted in the installation, most notably music director Tim Keyes, Meg Poltorak Keyes, Dr. Harvey Smires, and Nick Pavia. Also involved were numerous members of the youth ministry, St. Charles staff, and parish volunteers. Special thanks are due to Kenneth
Knieser for his efforts toward the donation of the Sussex pipe organ, the continued support of Monsignor Gregory E. S. Malovetz, and all of the many generous financial donations that made this project possible.
—Tim Keyes
Russell Meyer & Associates, Opus 12, 2009 St. Charles Borromeo Church, Skillman, New Jersey
GREAT (unenclosed)
16′ Gedeckt Bass (common bass, Pos)
8′ Open Diapason 61 pipes
8′ Spillgedeckt* 12 pipes
8′ Dolce (Pos)
4′ Octave 61 pipes
4′ Spillflöte 61 pipes
22⁄3′ Twelfth 61 pipes
2′ Fifteenth 61 pipes
11⁄3′ Mixture III 183 pipes
8′ Trompette (Sw)
4′ Clairon (Sw)
Chimes* 25 tubes
16′ Swell to Great
8′ Swell to Great
4′ Swell to Great
8′ Positiv to Great
SWELL (enclosed)
8′ Geigen Diapason* 61 pipes
8′ Rohrgedeckt* 61 pipes
8′ Viole de Gambe* 73 pipes
8′ Voix Celeste CC* 73 pipes
4′ Geigen Octave* 12 pipes
4′ Rohrflöte 12 pipes
22⁄3′ Nazard 7 pipes
2′ Kleinflöte 5 pipes
13⁄5′ Tierce TC 39 pipes
2′ Plein Jeu III 183 pipes
16′ Contre Trompette* 12 pipes
8′ Trompette* 61 pipes
8′ Hautbois* 61 pipes
4′ Clairon 12 pipes
Tremulant
16′ Swell to Swell
4′ Swell to Swell
POSITIV (unenclosed)
8′ Spitzprincipal 12 pipes
8′ Nasongedeckt* 61 pipes
8′ Dolce* 61 pipes
8′ Dolce Celeste TC* 49 pipes
4′ Spitzoctave* 61 pipes
4′ Blockflöte 61 pipes
2′ Blockflöte 12 pipes
11⁄3′ Larigot
1′ Sifflöte
8′ Cromorne* 61 pipes
8′ Trompette Harmonique** 61 pipes
Tremulant
16′ Swell to Positiv
8′ Swell to Positiv
4′ Swell to Positiv
Zimbelstern (prepared for)
PEDAL (unenclosed)
32′ Untersatz (resultant)
16′ Open Diapason 12 pipes
16′ Subbass* 32 pipes
16′ Lieblich Gedeckt* 12 pipes
8′ Octave 32 pipes
8′ Bourdon* 12 pipes
4′ Choral Bass 12 pipes
4′ Blockflöte (Pos)
22⁄3′ Rauschquint II (Gt)
32′ Grand Cornet VII (derived)
16′ Bombarde* 12 pipes
16′ Contre Trompette (Sw)
8′ Trompette (Sw)
4′ Cromorne (Pos)
8′ Great to Pedal
8′ Swell to Pedal
4′ Swell to Pedal
8′ Positiv to Pedal
* indicates recycled ranks
** includes 17 new pipes